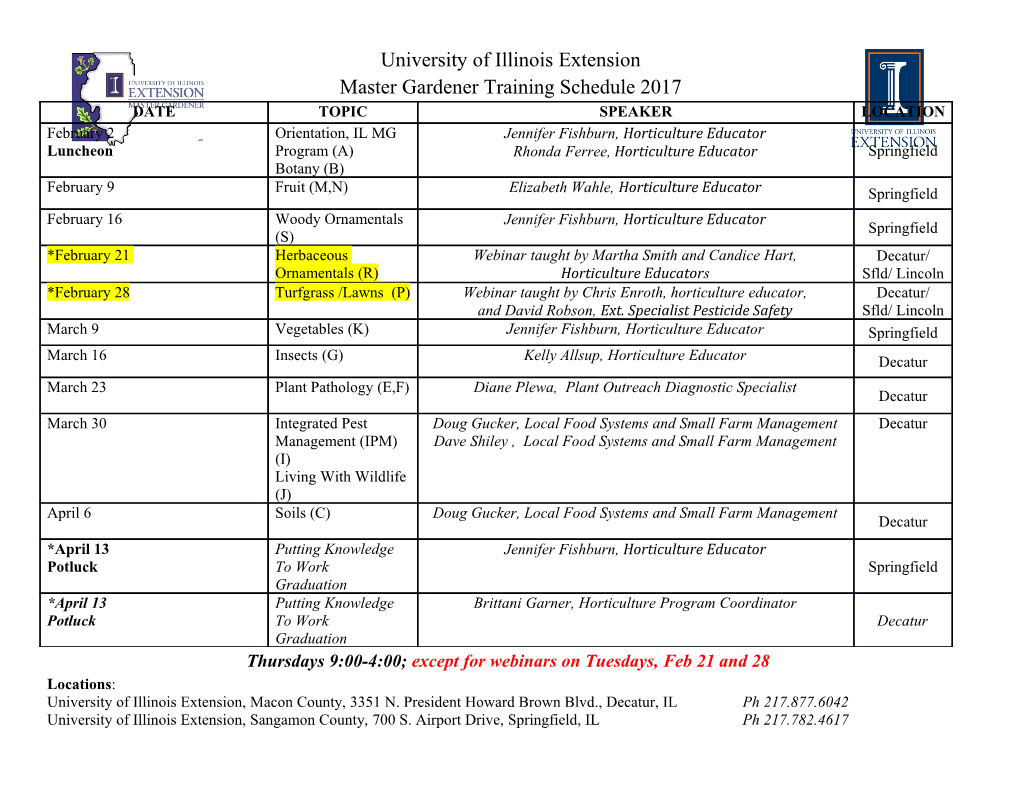
IZAWA, T., KATAYAMA, H., and SAND, N. Smelting reduction of chromite ore in an oxygen converter. INFACON 6. Proceedings ofthe 1st lIuematiOllal Chromium Steel alld Alloys Congress, Cape Towll. Volume 2. Johannesburg, SALMM, 1992. pp. 245-252. Smelting Reduction of Chromite Ore in an Oxygen Converter T. IZAWA*, H. KATAYAMAt, and N. SANO* * Research Association/or New Smelting Technologies, Tokyo, Japall tTechnical Development Bureau, Nippon Steel Corp., Tokyo, Japan tUniversity ofTokyo, Tokyo, Japan As electrical energy is more expensive in Japan than in other countries, technologies for decreasing the consumption of electrical energy in the processing of chromite ore to stainless steel have been developed. This paper describes the smelting reduction of chromite ore in the production of high-carbon ferrochromium, or the production of crude stainless steel in an advanced oxygen converter without the use of electrical energy as a heat source. Problems in the smelting reduction of chromite ore (i.e. slag foaming, reduction rate, post-combustion, lining erosion, and so on) can be solved simultaneously by a combination of the following conditions: (1) separation of the metal bath from the oxygen jet by a thick layer of slag and by an adequate blowing operation, and (2) control of the composition of slag as (MgO) + (AJ 20 3) = 45 to 46 per cent. Based on these principles, a pilot-plant test for the production of high-carbon ferrochrontium on a 5 1 scale (30 tid) was conducted successfully by lhe Research Association for New Smelting Technologics. Crudc stainless stcel is produced from dephosphorized pig iron and partially reduced chromite pellets by the smelting reduction process in a commercial top- and bottom-blowing converter. Introduction is decarburized by an oxygen jet, Figure I(a); that is, Conventionally, high-carbon ferrochrornium produced in an oxidizing reactions occur. On the other hand, if the metal electric furnace is used as a raw material in the production bath is separated from the oxygen jet by a thick layer of slag of chromium steel. In Japan, electrical energy is more containing a large amount of carbonaceous materials, it is expensive than in most other countries; therefore, the possible to proceed with reduction within the slag and to technology for the prereduction of chromite ore has been suppress the re-oxidation of the metal, Figure I(b). developed with the purpose of reducing the consumption of electrical energyl.2. In this decade, various research activities have been devoted to the production of high­ carbon ferrochromium or crude stainless steel by the smelting reduction of chromite ore in an advanced oxygen converter. Likewise, various technologies have been developed for the reduction of chromite ore without the use of electrical energy as a heat source. This paper describes these research activities and developmental work. The symbols used are defined at the end of the paper. Principle of the Process Recently, the top- and bottom-blowing converter has been used for steelmaking (Figure 1). In this furnace, the stirring (a) Steelmaking (b) Smelting reW::tion intensity of the molten metal and slag can be controlled by the blowing of gas through the bottom. In steelmaking with FIGURE I. Operation of the oxygen converter for steelmaking and relatively little slag (50 to 150 kglt of metal), the metal bath smelting reduction SMELTING REDUCTION OF CHROMlTE ORE IN AN OXYGEN CONVERTER 245 Before smelting reduction can proceed at high as fluoride or sodium compounds3 to the slag, by the productivity, il is imperative that those conditions which injection of fine chromium ore into a hot spot4.S• or by will stabilize a stirred bath be studied and quantified. For controlling the composition of the main components of the this purpose, the following problems have to be solved: slag (MgO, Si02, and CaO). Figure 3 shows an example of (I) how to suppress slag foaming the influence of slag composition on the reduction of (2) how to accelerate the reduction rate of chromite ore chromium oxide. In tl1is case, the addition of silica to the (3) how to increase the post-combustion ratio, slag accelerates the reduction of chromium oxide by allowing it to dissolve in the slag. The rate of the reduction %CO, depends on the composition of lhe metal, the viscosity of ( %CO + OkCO, x 100). the slag, the amount of carbonaceous materials, the to achieve the generation of sufficient heat temperature, and the stirring intensity. (4) how to suppress the erosion of the lining. Results of Fundamental Investigations In order to solve the problems outlined above, various 101 types of research studies have been conducted. 0 0 0 0 0 Suppression of Slag Foaming 0 ;;: In a conventional oxygen converter thal is used for the II making of steel, molten slag foams extensively, the apparent U .0. to ... density of the slag layer being less than 0,2 g/em'. If the ... .0. amount of slag increases under these conditions, stable O(SiO, )~301 operation of the converter is disturbed by an overflow or 6 ~351 0.11 0 ~401 'slopping' of the slag. The extent of slag foaming depends ... ~451 on the rale of CO generation and on the composition of the slag. However. il has been found that the presence of an 0 20 40 60 BO adequate amount of carbonaceous materials controls lhe timo (min) apparent density of the slag layer to a level of about 1,0 g/cm~, independent of the slag composition, as shown in FIGURE 3. Inl1uence of slag composition on the reduction of sIng Figure 2. This increase in density is due to the fact that containing chromium oxide by carbon in rocking furnace carbonaceous materials accelerate the release of CO gas by The rate formula can be expressed as follows: the coalescence of small bubbles generated by the reduction reactions. for (T. Cr) ;0, about 3 per cent, 1.2- d(T.Cr)_ k . 0' [I] .P"'---~-~'" d/ 1.0 '"ro P' ...a-Q. _ Vi , " for (T. Cr) < about 3 per cent. _"0.8- " o § I, ;:: " 0. 6 Co I 0, d(T. Cr) - k I {(T. Cr) - (T. Cr)r! . CIl 01 /, [2] t: - /0 kJ dt ~ 0.4 rr 1 0 1 The relationship between k I and the composition of the 0. 2 I- metal is shown in Figure 4. The rate constant k I decreases , with [%Cr], but levels off at chromium contents greater 0.1 0.2 than 20 per cent. This is so because, at lower chromium ° Coke/Slag (wt. ratio) levels, carbon in the metal contributes to the reduction of the chromium oxide but, with chromium contents higher than FIGURE 2. Effect of coke-to-slag ratio (by weight) on slag foaming 20 per cent, almost all the reduction occurs on the surface of the carbonaceous materials present in the molten slag. Acceleration of Chromite Ore Reduction Figure 5 shows the influence of the slag composition on Chromitc orc added to molten slag dissolves aL first, and the the overall rate constant in all experimenl in which argon chromium oxide in the slag is then reduced by carbon. The was inlroduced by bottom blowing without any top blowing dissolution of chromite ore is checked by the fonnalion of of oxygen, and the slag composition was conLrolled by the an insoluble spinel layer (MgO.AI20 3) around the ore addition of lime. The temperature of the metal bath was particles. The dissolution of the chromite ore can 1600 ±20°C and the slag was 0 to 100°C lower in consequently be accelerated by the addition of fluxes such temperature. The rate constant changes abruptly when the 246 INCSAC I c: 0.8 I 16000 e ..,0 u 12 :l "0 0.6 ..~ " 10 c: 0°,0" '" 'E .<: ~ 0.4 ~ 'c 8 \). ;;: ~ ';; 6 \'---0---- ~ 0.2 ::.e. '" a 0 0 r.,. ~ -.:-'" 4 - ...---ce__°-2.... u ~ a 20 40 60 80 100 2 (% C02) (%CO) + (%C0 )X 100 (%) oI:---'-_~':--'--:':_'----l'_-:';,-'--' 2 o 20 40 60 FIGURE 6. Effect of post-combustion on the chromium content of the ler] (%) slag in an oxygen converter with a thick layer of slag FIGURE 4. Effect of the chromium conteDl in the metal bath on the Increase in Post-combustion Ratio apparent rale constant, k1 To decrease the phosphorus input, the consumption of carbonaceous material should be decreased by an increase in the post-combustion ratio in the converter. The post­ 12 combustion ratio in a conventional oxygen converter for 16oo"C steelmaking is lower than 15 per cent. Nevertheless, 10 separation of the metal bath from the oxygen jet by a thick layer of slag is effective in increasing the post-combustion C B ratio while at the same time decreasing the formation of ! dust. This is shown in Figure 7. N 6 0 x x 4 2 0 30 60 (MgO) + IA',O,) (%) I, == 2 .... 4 kW!t 100 100 '"'E FIGURE 5. Effect of (MgO)) + (A120 3) content on the apparent rate ~ constant, k] i !!! ; c ~ 0 .E (MgO) + (Al 0,) content reaches 45 per cent. Ahove that ~ t: 2 ~ , critical value, the dissolution of chrornite is supposed to be 50 50 ." -g '0 suppressed. 0 C, ~ 0 On the other hand, in an experiment where top blowing of ~ 0 E oxygen was used, the temperature of the slag was almost CL 0 '" equal to that of the metal bath. Then the critical value of 0 0.7 1 2 3 Ls/Lso (-1 (MgO) + (A1 20,) was about 46 per cent at 1600°C. Therefore, the dissolution of chromite ore and the reduction FIGURE 7. Relationship between post-combustion and Ls/Lso in an of chromium oxide can be accelerated if (MgO) + (AI 20,) is oxygen converter less than the critical value, and this can be achieved by the addition of lime to the slag.
Details
-
File Typepdf
-
Upload Time-
-
Content LanguagesEnglish
-
Upload UserAnonymous/Not logged-in
-
File Pages8 Page
-
File Size-