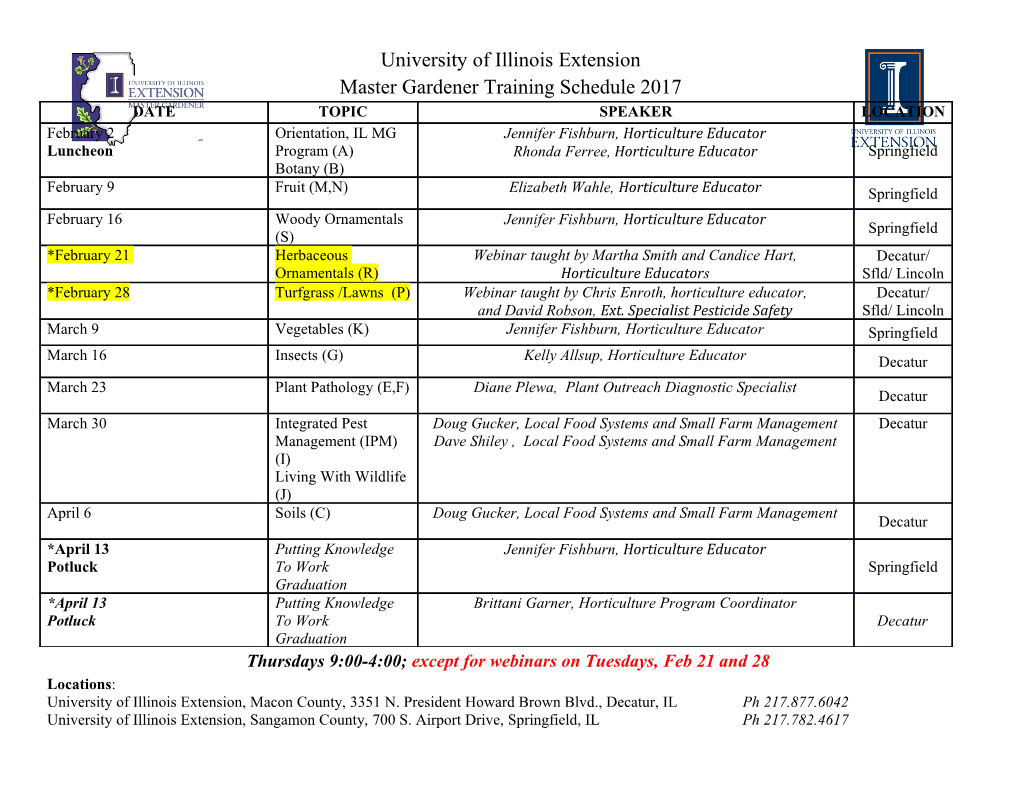
BASF Corporation JOINING OF NYLON BASED PLASTIC COMPONENTS -- VIBRATION AND HOT PLATE WELDING TECHNOLOGIES Abstract mechanical properties. Molded nylon parts are more resistant to creep, fatigue, repeated impact, Previously we reported to SPE’96 the and so on compared to the parts made of many optimized mechanical performance of linear less rigid thermoplastics. vibration welded nylon 6 and 66 butt joints. Under the optimized vibration welding There are more than a dozen classes of conditions (amplitude, pressure, meltdown, nylon resins, including nylon 6, nylon 66, nylon thickness of interface), the tensile strength at the 46, nylon 12, etc.). Welded nylons are used in nylon butt joints was equal to or 14% higher than many industrial products, the largest being the the tensile strength of the base polymer (matrix). automotive. In recent years, demands to use non-filled, fiber-glass reinforced and filled nylon H. Potente and A. Brubel presented to products to replace metals and thermosets in SPE’94 and SPE’98 an analysis of the welding power tools, lawn / garden equipment (leaf performance in a family of amorphous and semi- blowers, chain-saws, gas-tanks), and the crystalline thermoplastics including nylon 6 automotive (air induction, power train systems, using hot-plate welding technologies. For hot- fluids reservoirs, and other uses), have increased plate welded nylon 6 with a range of glass-fiber (1, 2). reinforcement from 0 to 40% (by weight), the tensile strength at the weld was 40–60% less On average a car uses 18 kg of nylon compared to the tensile strength of the base based plastics. With the annual vehicle polymer. production at nearly 15 million, the needed amount of nylons is more than 200 million We performed a comparative study of kilograms -- more than 45 million kilograms for mechanical performance of welded nylon’s butt under-the-hood applications alone, and another joints. In this study we analyzed the efficiency 11 million kilograms for welded air intake of both widely used joining technologies: manifolds (AIM) and resonators. The design of vibration welding and hot plate welding. Under these critically stressed welded components the optimized hot plate welding conditions, requires advanced analysis of structure, noise tensile strength of both nylon 6 and 66 joints is vibration & harshness (NVH), and welded joints close to or slightly higher than the tensile using short-term and long-term strength and life strength of the base polymers. criteria. Reinforced nylon plastics (with 30-35% of glass-fiber by weight) are typically used in Presented results will help plastic parts design of AIM’s. designers, material developers and manufacturers, by giving them alternatives when The AIMs, resonators, fluid reservoirs, choosing types of nylon (6, 66, 66/6, 46, etc.) and many others are hollow parts that may be and welding technologies for a wide range of produced by either “lost core”, plastic welding, applications. or welding plus fastening / overmolding technologies. Worldwide (1), nearly 80% of Introduction AIMs are produced by either a lost-core injection (46%) molding process or injection molding Nylons (polyamides) are high followed by linear vibration welding (32%). The performance semi-crystalline thermoplastics with lost core process is more capital intensive a number of attractive chemical, physical and compared to plastics welding processes because it involves additional forming, melting and metallic core removing. It is also possible (3) to Welding temperature in interface during use the hot plate (H-P) welding technology for the LVW process is not directly controlled and plastic AIM’s. guided parameter in the standard LVW Linear vibration welding (LVW) and H- equipment available from leading manufacturers P welding equipment and welding tools and of welding machines (Branson Ultrasonics nests are not very expensive, and the welding Corporation, Bielomatik, Inc., Forward process itself is not that time consuming. The Technology Industries, Inc., etc.). For LVW and H-P welding processes are PC optimizing LVW processing conditions controlled with sensors scanning the positions (including temperature in interface) we used and automatic reporting the key process advanced thermal imaging infrared method and parameters critical for both welding computerized system (4). technologies. Orbital vibration welding (OVW) Similarities and Differences of Linear technology allows motion to be programmed in Vibration (LVW) and Hot-Plate (H-P) many ways, and it also provides more freedom in designing the weld areas. OVW avoids some of Welding Technologies the hindrances of LVW, which has problem with unsupported walls perpendicular to oscillation / Different welding methods were used vibration direction. The OVW method is also for joining and assembling hollow plastic parts, based on friction, which uses an electromagnetic such as ultrasonic (U/S), linear vibration LVW), drive to create relative motion between two orbital (OVW), spin, extrusion, hot plate / tool plastic components. The orbital motion ensures (H-P), implant resistance, infrared (IR), etc. that each point surface of the driven plastic part LVW and H-P welding methods were utilized in orbits a different point on the butt joint surface assembling various plastic components made of the stationary part. This orbit of motion is from two, three, or more pieces, molded, continuous and identical for all points on the extruded, thermally formed from the similar or joint surface. OVW operates at low vibration dissimilar thermoplastics. These joining amplitudes. Even the sensitive electronic technologies all share the following typically components are not damaged mechanically or welding phases: thermally, contrary to other plastic joining • joined plastic parts placement / nesting and methods. gripping in specially designed tools; • materials heated in areas where the joints are The following key processing and weld to be formed; interface parameters are important for the • local melting in jointed surfaces areas; performance of H-P welded butt joints: • surfaces contacting / pressing together for • temperature at the heating element / plate; in joining; local areas of materials or interface at • cooling in the joint interface and other areas; joining; in material(s) diffusion phase; start • welded part removal from welding tool / and final temperatures at hold / sealing nest and machine. (local cooling) phase; • time: pre-melt, during melting, and during The type of heat generation and heat hold / sealing (cooling); transfer distinguishes these technologies. The H- • clamp pressure (variable in process): pre- P welding method presents an external heating melt and during hold / sealing (cooling); process. The LVW is an alternative internal • thickness of interface / distance: of pre- heating process using friction. For H-P welding heated layer(s); melt collapse (at joint technology, the joined surfaces of thermoplastic sealing phase); final thickness of the parts are plasticized or melted prior to welding. It interface (in local areas). permits direct control of the pre-heating and welding temperature during the heating and For H-P welding, it is critically fusion phases. For LVW, the temperature in the important to achieve a sufficient and consistent interface is a function of processing parameters through-thickness and local material heating such as time, clamp-pressure, amplitude, during the pre-melt phase. For the semi- frequency, and meltdown, and it depends also on crystalline materials the requirements are (5): the physical characteristics of the polymers. • melt layer thickness (meltdown) of about • vibration frequency (typically in range 30% of the wall thickness (for a wall from 120 to 240 Hz). thickness < 4 mm); • sealing distance / joining displacement of Typically the LVW machines combine approximately 60 to 80% of above all the advantages of vertical or horizontal & mentioned melt thickness; vertical design for joining of components made • hot-plate / tool temperature (for semi- from the similar or de-similar plastics. The sizes crystalline plastics application) should be of the joined parts vary from small (valves, fluid equal to the melting peak, + 70°C. reservoirs, etc.) to very large (cars crossbeams, etc.). The H-P welding technology is a reliable joining method for injection molded, When applying LVW and OVW technologies, blow molded, and extruded hollow components. we need to be aware of the following info: Typically, H-P welding machines have all the • weight (of the upper fixture + nested part) advantages of horizontal or vertical design (see and design limitations: in the sizes of the Figure 1). These include welds of small and big part placed in upper nest / fixture; components (i.e. gas tanks), long / large diameter • limitations on the weld plane configuration gas pipes made from the similar plastics. and maximum value of out-of-welded plane angle; When applying the H-P welding • difficulties (to achieve optimized method, we need to be aware of the following mechanical strength / life performance of disadvantages: joint) in using dissimilar plastics with the • design limitations: plane configuration of different melt temperatures (of 50°C); the joint surfaces; position tolerance • dimensional limitations (in non-isometric (centering capability for non-stiff melt distribution in local areas of possible applications – flexible walls, etc.); gaps) in reinforced plastics and for non- • dimensional limitations (in non-isometric optimized
Details
-
File Typepdf
-
Upload Time-
-
Content LanguagesEnglish
-
Upload UserAnonymous/Not logged-in
-
File Pages11 Page
-
File Size-