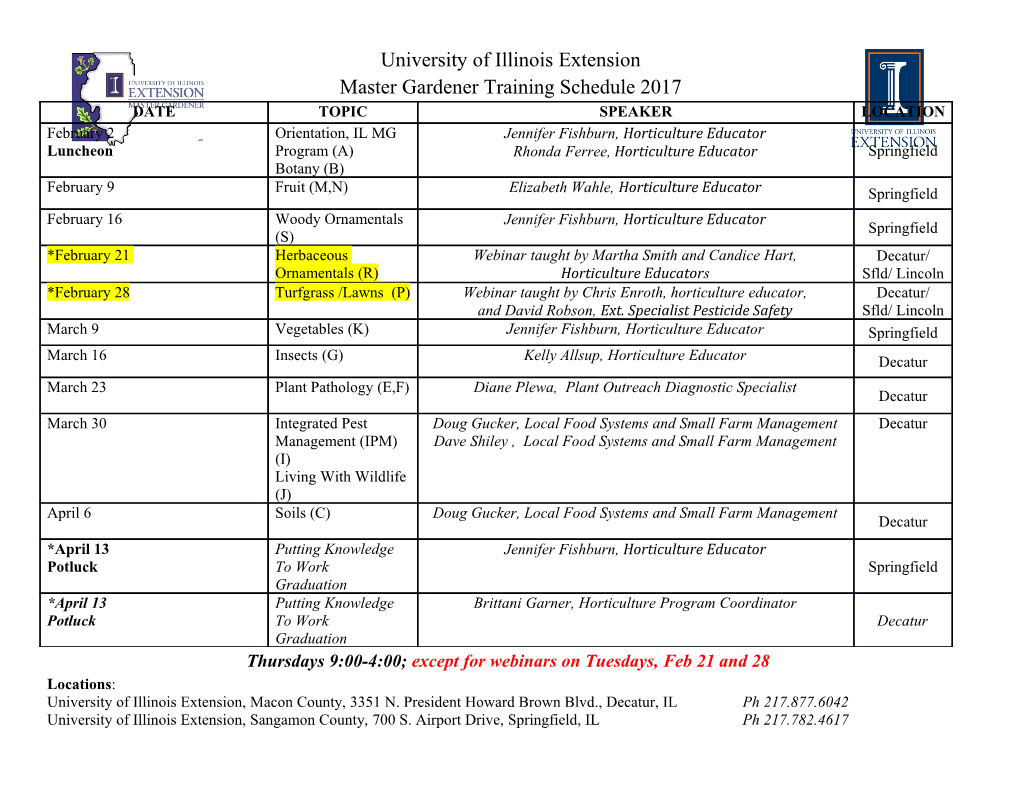
FORGING PROCESS DESIGN FOR RISK REDUCTION DISSERTATION Presented in Partial Fulfillment of the Requirements for the Degree Doctor of Philosophy in the Graduate School of The Ohio State University By Yongning Mao, M.S. * * * * * The Ohio State University 2009 Dissertation Committee: Approved by Professor Rajiv Shivpuri, Adviser Professor Jose M. Castro __________________________ Professor Allen Yi Adviser Industrial and Systems Engineering Graduate Program ABSTRACT In this dissertation, forging process design has been investigated with the primary concern on risk reduction. Different forged components have been studied, especially those ones that could cause catastrophic loss if failure occurs. As an effective modeling methodology, finite element analysis is applied extensively in this work. Three examples, titanium compressor disk, superalloy turbine disk, and titanium hip prosthesis, have been discussed to demonstrate this approach. Discrete defects such as hard alpha anomalies are known to cause disastrous failure if they are present in those stress critical components. In this research, hard-alpha inclusion movement during forging of titanium compressor disk is studied by finite element analysis. By combining the results from Finite Element Method (FEM), regression modeling and Monte Carlo simulation, it is shown that changing the forging path is able to mitigate the failure risk of the components during the service. The second example goes with a turbine disk made of superalloy IN 718. The effect of forging on microstructure is the main consideration in this study. Microstructure defines ii the as-forged disk properties. Considering specific forging conditions, preform has its own effect on the microstructure. Through a sensitivity study it is found that forging temperature and speed have significant influence on the microstructure. In order to choose the processing parameters to optimize the microstructure, the dependence of microstructure on die speed and temperature is thoroughly studied using design of numerical experiments. For various desired goals, optimal solutions are determined. The narrow processing window of titanium alloy makes the isothermal forging a preferred way to produce forged parts without forging defects. However, the cost of isothermal forging (dies at the same temperature as the workpiece) limits its wide application. In this research, it has been demonstrated that with proper process design, the die temperature can be reduced greatly without violating process window constrictions. Moreover, the computation cost is also reduced by replacing the complex 3-dimensional (3D) shape with its corresponding 2-dimensional (2D) representative cross sections, and a well balanced load distribution has been achieved by proper design of die flashland. iii Dedicated to my family iv ACKNOWLEDGMENTS This dissertation could not have been written without Dr. Rajiv Shivpuri, who not only served as my advisor and provided me financial support, but also encouraged and challenged me throughout my academic program. It is Dr. Shivpuri who guided me to learn knowledge and the methodology to obtain it. The research experience working with Dr. Shivpuri has helped me to become more professional and be prepared to make more contributions to the future. I would like to express my sincere appreciation to members of my dissertation committee Dr. Jose M. Castro and Dr. Allen Yi for their scientific inputs and advices. I would also like to thank members of my candidacy committee, Dr. Gary Kinzel, Dr. Henry Busby, and Dr. Theodore Allen for their valuable comments and suggestions. Thank also goes to my group members, Dr. Francesco Gagliardi, Dr. Chun Liu, Dr. Yuanjie Wu, Dr. Xiaomin Cheng, Dr. Meixing Ji, Dr. Wenfeng Zhang, Dr. Jiang Hua, Dr. Satish Kini, Dr. Sailesh Babu, Dr. Zhiqiang Sheng, Yijun Zhu and Kuldeep Agarwal for their helpful discussions and friendship during my graduate program. v I wish to thank my parents for their unconditional love and endless support throughout my doctoral study. Finally, I would like to express my sincere gratitude to my wife Dr. Ruomiao Wang for her continuous encouragement, love and never-ending patience. vi VITA May, 1978 Born – Shenyang, China 2000 B.S., Plasticity Engineering, Shanghai Jiao Tong University, Shanghai, China 2000 – 2003 M.S., Mechanical Engineering, Shanghai Jiao Tong University, Shanghai, China 2003 – 2009 Graduate Research Associate, Department of Industrial, Welding, and Systems Engineering, The Ohio State University PUBLICATIONS Rajiv Shivpuri, Xiaomin Cheng, Yongning Mao. Elasto-plastic pseudo-dynamic numerical model for the design of shot peening process parameters. Materials and Design, in press. FIELDS OF STUDY Major Field: Industrial and Systems Engineering Minor Fields: Operations Research and Design Optimization vii TABLE OF CONTENTS ABSTRACT........................................................................................................................ ii ACKNOWLEDGMENTS .................................................................................................. v VITA ................................................................................................................................. vii LIST OF FIGURES .......................................................................................................... xii LIST OF TABLES ........................................................................................................... xvi CHAPTER 1 INTRODUCTION ........................................................................................ 1 1.1 Forging processes......................................................................................... 1 1.1.1 Applications of forged parts.................................................................... 2 1.1.2 Classification of forging processes ......................................................... 3 1.2 Tooling and process design issues................................................................ 5 1.3 Risk and forging ........................................................................................... 8 1.4 Objective and outline ................................................................................. 14 CHAPTER 2 BACKGROUND AND LITERATURE REVIEW..................................... 17 2.1 Preform design in forging process.............................................................. 18 2.1.1 Backward finite element simulation ..................................................... 18 2.1.2 Sensitivity analysis approach................................................................ 23 2.1.3 Other approaches .................................................................................. 27 2.2 Property control in titanium forging........................................................... 29 2.2.1 Metallurgy of conventional titanium alloys.......................................... 30 2.2.2 Hot working of titanium alloys............................................................. 32 2.2.3 Related work on forging of titanium alloys .......................................... 38 2.3 Property control in superalloys forging...................................................... 46 2.3.1 Metallurgy of superalloys ..................................................................... 47 2.3.2 Melt-related defects in superalloys ....................................................... 48 viii 2.3.3 Forging of superalloys .......................................................................... 53 CHAPTER 3 APPROACH AND METHODOLOGY...................................................... 58 3.1 Finite element method................................................................................ 58 3.1.1 Rigid-plastic FEM................................................................................. 60 3.1.2 Metal forming modeling using viscoplastic approach.......................... 62 3.1.3 Applications in forging ......................................................................... 63 3.2 Design of experiments and response surface methods............................... 65 3.3 Monte Carlo simulation.............................................................................. 70 CHAPTER 4 EFFECT OF FORGING PATH ON MICROFEATURE LOCATION IN COMPRESSOR DISK FORGING................................................................................... 72 4.1 Introduction to hard alpha inclusion........................................................... 72 4.2 Multi-body simulation modeling................................................................ 75 4.2.1 Constitutive equations and friction ....................................................... 75 4.2.2 Spatial and time discretization.............................................................. 77 4.2.3 Discrete contact treatment..................................................................... 78 4.2.4 Finite element formulation.................................................................... 79 4.3 Titanium forging modeling with hard alpha inclusion............................... 80 4.3.1 3D modeling of hard alpha in forging................................................... 81 4.3.2 Simplification of 3D modeling to 2D modeling ................................... 94 4.4 Risk mitigation by changing forging paths ................................................ 95 4.4.1 Forging path selection and constraints.................................................. 97 4.4.2 Numerical simulations to build regression
Details
-
File Typepdf
-
Upload Time-
-
Content LanguagesEnglish
-
Upload UserAnonymous/Not logged-in
-
File Pages221 Page
-
File Size-