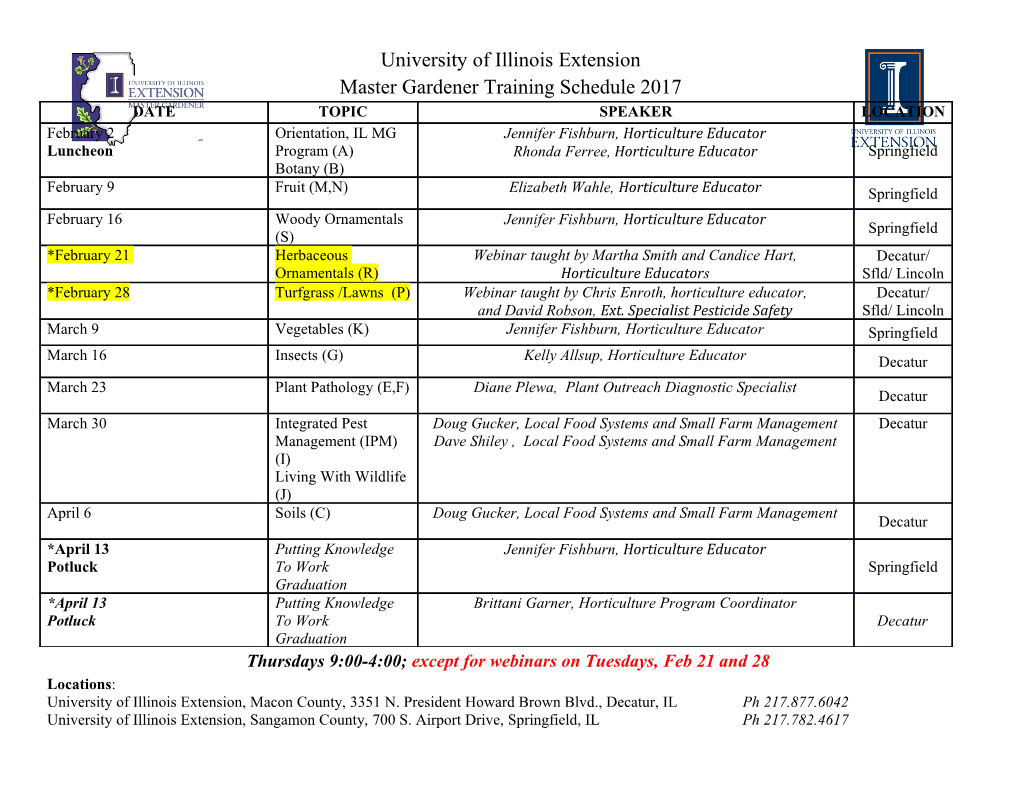
A continuum mechanics approach to modeling and simulating engineering materials undergoing phase transformation using the Evolving Micro-Structural Model of Inelasticity By Adetokunbo Adelana Adedoyin A Dissertation Submitted to the Faculty of Mississippi State University in Partial Fulfllment of the Requirements for the Degree of Doctor of Philosophy in Computational Engineering in the Department of Computational Engineering Mississippi State, Mississippi May 2014 Copyright by Adetokunbo Adelana Adedoyin 2014 A continuum mechanics approach to modeling and simulating engineering materials undergoing phase transformation using the Evolving Micro-Structural Model of Inelasticity By Adetokunbo Adelana Adedoyin Approved: Douglas J. Bammann Youssef Hammi (Major Professor) (Dissertation Co-advisor) Thomas E. Lacy (Committee Member) Seongjai Kim (Committee Member) Edward A. Luke (Committee Member) Roger L. King (Graduate Coordinator) Achille Messac Dean Bagley College of Engineering Name: Adetokunbo Adelana Adedoyin Date of Degree: May 16, 2014 Institution: Mississippi State University Major Field: Computational Engineering Major Professor: Dr. Douglas J. Bammann Title of Study: A continuum mechanics approach to modeling and simulating engi- neering materials undergoing phase transformation using the Evolving Micro-Structural Model of Inelasticity Pages of Study: 82 Candidate for Degree of Doctor of Philosophy Heat treatment for the purpose of material strengthening is accompanied by residual stresses and distortion. During these processing steps, steel alloys experience a phase change that in turn modify their overall mechanical response. To properly account for the cumulative composite behavior, the mechanical response, transformation kinetics and subsequent interaction of each phase have to be properly accounted for. Of interest to material designers and fabricators is modeling and simulating the evolutionary process a part undergoes for the sake of capturing the observable residual stress states and geometric distortion accumulated after processing. In an attempt to capture the aforementioned physical phenomena, this investigation is premised upon a consistent thermodynamic framework. Following this, the single phase Evolving Microstructural Model of Inelasticity state variable model is extended to accom- modate the occurrence of multiphases, affrming that the interaction between coexisting phases is through an interfacial stress. Since the effcacy of a multiphase model is de- pendent on its ability to capture the behavior of constituents phases and their subsequent interaction, we introduce a physically based self-consistent strain partitioning algorithm. With synthesis of the aforementioned ideas, the additional transformation induced plas- ticity is numerically accounted for by modifying each phase’s fowrule to accommodate an interfacial stress. In addition, for simulating the cohabitation of two phases, the mechan- ical multiphase model equations is coupled with a previously developed non-diffusional phase transformation kinetics model. A qualitative assessment of the material response based on a Taylor, Sachs and self-consistent polycrystalline approximation is carried out. Further analysis of the multiphase model and its interaction with transformation kinetics is evaluated. Key words: Plasticity, Phase Transformation, Multiphase, Rate Kinetics, Polycrystalline Approximation DEDICATION To all involved in the advancement of knowledge in continuum mechanics and its ap- plication to metal inelasticity. ii ACKNOWLEDGEMENTS This work was supported by the Center for Advanced Vehicular Systems at Mississippi State University. I am grateful to Dr. Douglas J. Bammann for directing this research. Most importantly, I appreciate his relentless effort towards mentoring and providing a surplus of keen insight into problem solving; irrespective of the diffculty level. I have also learnt from Dr. Bammann that every problem has an anchor and as a Scientist and Engineer it is your responsibility to search for it. He has also thought me to press-on in attempting to solve a problem and refning the solution as i move along in acquiring knowledge. I choose my committee members with the criterion being courses that were known to require some rigor on both the part of the student and Instructor. Most importantly, I was in search for mentors that were excellent in their respective felds. I appreciate the effort of Dr. Thomas E. Lacy Jr. for his patient in teaching me Continuum Mechanics, Dr. Seongjai Kim for his shrewdness in communicating a numerical view on Partial Differential Equations and Dr. Edward A. Luke for his theoretical rigor in teaching parallel computing. I pray that their effort towards mentoring students not go in vain. I am also grateful for their comments on this dissertation. Special thanks to Dr. Esteban Marin, Dr. Youssef Hammi, Dr. Kof Enakoutsa and Dr. Sule Dogan for their relentless support both educational and emotional during this effort. iii Lastly, I am grateful to God for my parents, Mr. Simeon Shina and Mrs. Henrietta Kikelomo Adedoyin, and my immediate siblings for their continuous support in my past, present and future endeavor. iv TABLE OF CONTENTS DEDICATION .................................... ii ACKNOWLEDGEMENTS .............................. iii LIST OF TABLES .................................. vii LIST OF FIGURES .................................. viii MODEL NOMENCLATURE ............................. x CHAPTER 1. INTRODUCTION .............................. 1 1.1 Literature Review .......................... 1 2. APPLICATION OF PHYSICALLY BASED PLASTICITY MODEL TO MATERIALS UNDERGOING PHASE TRANSFORMATION ...... 9 2.1 Abstract ............................... 9 2.2 Introduction ............................. 10 2.3 Methodology ............................ 13 2.3.1 Multiphase EMMI Constitutive Equations ......... 13 2.3.2 Additional Considerations: Polycrystalline Approximation 20 2.4 Results ............................... 23 2.5 Summary .............................. 29 3. A QUALITATIVE ASSESSMENT OF THE MULTIPHASE EMMI PLAS- TICITY MODEL COUPLED WITH PHASE TRANSFORMATION KI- NETICS ................................... 32 3.1 Abstract ............................... 32 3.2 Introduction ............................. 33 3.3 Methodology ............................ 39 3.3.1 On the Thermodynamics for Coexisting Phases ...... 39 v 3.3.2 On the Transformation Kinetics Model ........... 46 3.3.3 Integration of the Multiphase EMMI Constitutive Equations 50 3.4 Results ............................... 55 3.5 Summary .............................. 62 4. SUMMARY ................................. 65 4.1 Summary .............................. 65 REFERENCES .................................... 68 APPENDIX A. EXPERIMENTAL AND NUMERICAL DATA FOR AUSTENITE .... 77 B. EXPERIMENTAL AND NUMERICAL DATA FOR MARTENSITE ... 79 C. FORMS OF MATERIAL PARAMETERS ................. 81 C.1 Form of EMMI Model Parameter ................. 82 vi LIST OF TABLES 2.1 Material parameters for 5120 austenite and martensite steel......... 25 2.2 Material properties for stainless steel 304L (SS304L)............ 26 3.1 Direct Integration Algorithm for Single Phase EMMI Model ........ 56 0 3.2 Direct Integration Algorithm for Multiphase EMMI Model atθ < Mstart . 57 vii LIST OF FIGURES 2.1 Strain rate partitioning for Sachs, Taylor and a self-consistent (SCi) poly- crystalline approximation at_ = 1/s. ..................... 23 2.2 EMMI model response ftted to experimental data of 5120 martensite steel. 26 2.3 EMMI model response ftted to experimental data of 5120 austenite steel.. 27 2.4 σ´ 1 for Taylor, Sachs and self-consistent approximation at 90%A + 10%M. 27 2.5 σ´ 1 for Taylor, Sachs and self-consistent approximation at 50%A + 50%M. 28 2.6 σ´ 1 for Taylor, Sachs and self-consistent approximation at 10%A + 90%M. 30 3.1 Kinetics rate using Lusk and KM model at carbon content %C = 0.1,...,0.4. 47 3.2 Lusk model at a fxed cooling rate evaluated at %C = 0.1,0.2,0.3,0.4..... 49 3.3 Functional vs. an incremental approach for SS304L at _ = 0:1=s ...... 52 3.4 EMMI model for 5120 austenite steel at uniaxial tension........... 58 3.5 EMMI model for 5120 martensite steel at uniaxial tension.......... 59 3.6 Multiphase EMMI model with Lusk model at 100C/s, 200C/s and 300C/s and 0.2%C. .................................. 59 3.7 Multiphase EMMI model with Lusk model showing σ´ for austenite at 100C/s, 200C/s and 300C/s and 0.2%C. ....................... 60 3.8 Multiphase EMMI with Lusk model showing σ´ for martensite at 100C/s, 200C/s and 300C/s and 0.2%C. ....................... 60 3.9 Interfacial for multiphase EMMI model with Lusk model at 100C/s, 200C/s and 300C/s and 0.2%C. ............................ 61 viii 3.10 Multiphase EMMI with Lusk kinetics showing 1 − φ at 100C/s for %C = 0.05, 0.1 and 0.2. ............................... 62 3.11 Multiphase EMMI with Lusk model showing σ´ for austenite at 100C/s and %C = 0.05, 0.1 and 0.2 ............................ 63 3.12 Multiphase EMMI with Lusk model showing σ´ for martensite at 100C/s and %C = 0.05, 0.1 and 0.2. ............................ 63 3.13 Multiphase EMMI with Lusk model showing TRIP strain at 100C/s for %C = 0.05, 0.1 and 0.2. .............................. 64 A.1 EMMI model response to uniaxial tension data for 5120 austenite steel at various strain rates and temperatures ..................... 78 B.1 EMMI model response to uniaxial tension data for 5120 martensite steel at various strain rates and
Details
-
File Typepdf
-
Upload Time-
-
Content LanguagesEnglish
-
Upload UserAnonymous/Not logged-in
-
File Pages96 Page
-
File Size-