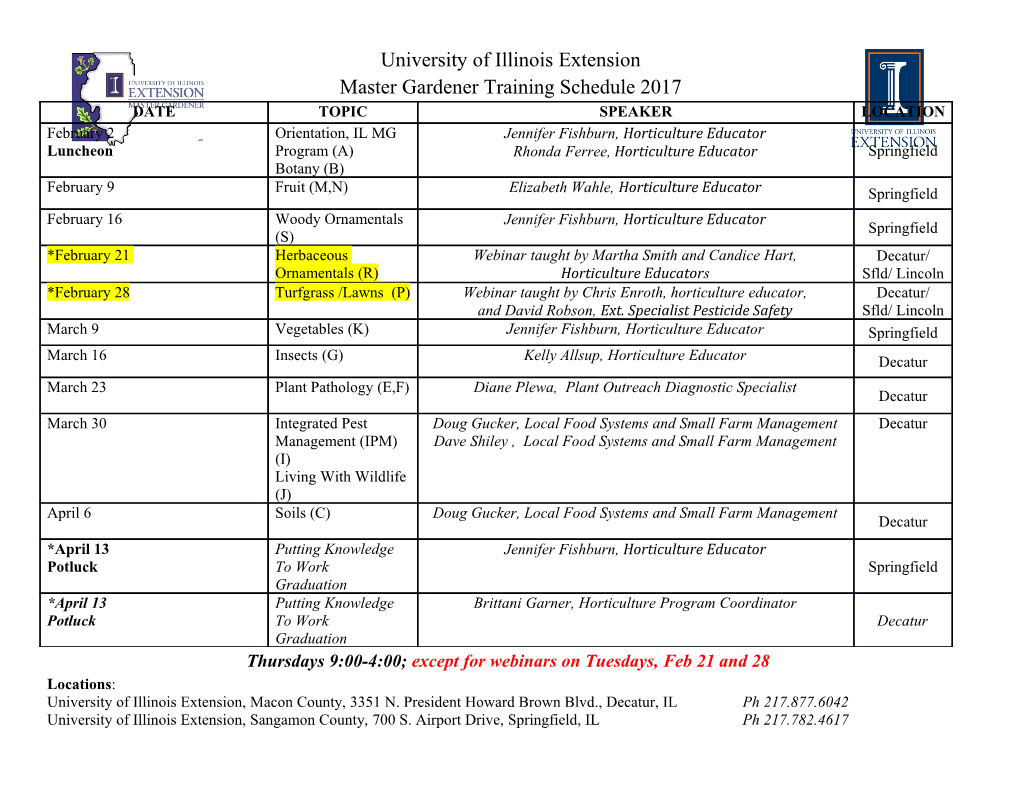
Electromagnetic Solutions Magnet Retention in Permanent Magnet DC Motors – Part I Introduction and Overview For more than 50 years, Windings has provided engineered electromagnetic solutions for critical applications in Aerospace, Defense, Automotive and Oil & Gas industries. As a full-service provider, Windings is a leader in the design, test, manufacture and support of custom electric motors, generators and related components including rotors, stators, lamination stacks and insulation systems. From Induction to Permanent motors feature permanent magnets mounted to Magnets the rotor and electromagnetic windings fixed to the For decades, alternating current induction motors inside of the motor housing. Locating the permanent (ACIM) have provided the driving force for magnets on the rotor significantly reduces rotor commercial and industrial applications. These inertia, enabling higher acceleration. The downside asynchronous motors feature simple and robust to this approach is the need for a rotor position designs, require little maintenance, function feedback device and complex external electronics reliably in a range of uses, require very simple to track rotor position and manipulate current in electric starters/contactors to operate, and are the stator windings to produce the desired motion inexpensive to manufacture. Asynchronous rotors output. Higher performance came with higher are cast; the magnetic field necessary to oppose the overall system cost and complexity, and concern electromagnetic field generated in the stator winding over magnet retention—especially at high rotational is induced in the rotor. No permanent magnets are speeds. used. But ACIM have limitations: Single phase ACIM have low starting torque, are relatively inefficient Properties of Magnetic Materials under lighter loads, and are acceleration-limited due Permanent magnet material selection significantly to inherently high rotor inertia. affects the overall performance of a BLDC motor; it is one of the most critical decisions an engineer As demand increased for higher motor acceleration, makes during the design process. Magnetite, power density, and overall efficiency, motor a naturally occurring iron ore, has the highest manufacturers have turned to synchronous motor magnetism of any mineral, but has limited magnetic designs. Permanent magnet synchronous motors strength. Ceramic ferrites—alloys of iron oxide (PMSM) incorporate permanent magnets to supply with barium, manganese, nickel, or zinc—can be the necessary opposing magnetic field. This magnetized; and aluminum, nickel, and cobalt significantly increases torque density and efficiency, (alnico) alloys have even stronger magnetic particularly during acceleration, by eliminating the properties. extra current required to induce the magnetic field. In the 1960s, scientists at the US Air Force Initially, PMSMs were configured with permanent Materials Laboratory alloyed yttrium and cobalt magnets adhered to the inside of the motor housing to create the first rare earth magnets, stronger and electromagnetic windings fixed to the rotor. than even alnico. Further research resulted in This configuration, commonly referred to as a combinations of neodymium and samarium–cobalt. brushed DC motor, uses carbon brushes and a These component minerals are called rare earth copper commutator to feed electrical current to not because they are scarce, but because they are the rotor windings. Brushed DC motors share diffuse and difficult to mine in quantity. the ACIM benefits of simple and robust designs, simple electric starters/contactors for operation, In addition to cost, rare earth magnets have two and low manufacturing costs. They also share the serious drawbacks: They are brittle and vulnerable drawback of limited acceleration due to high rotor to corrosion. To reduce the risk of damage or inertia and have higher maintenance requirements disintegration, these magnets are often plated due to constant wear on the carbon brushes during or coated with more durable materials such as operation. nickel-copper-nickel. Also, at extremely high temperatures, even rare earth magnets can become Continuing customer demand for higher demagnetized. acceleration, as well as for point-to-point positioning and more accurate position control, spawned the Despite these limitations, rare earth magnets are development of brushless DC (BLDC) motors. An the key to high power density and efficiency in inversion of the brushed DC configuration, BLDC electric motors. No other material helps generate 2 as much output with the same energy inputs. So about a resurgence in the use of permanent holding those magnets in place becomes a critical magnets to provide the field excitation for consideration for design engineers. To optimize electric machines. The rare-earth permanent performance, the designer must keep the magnets magnet materials allow machines of very high as close as possible to the stator windings; efficiency and energy densities to be built. minimizing the air gap between the rotor and stator The use of permanent magnets to provide the will maximize torque. The drawback is that as the air field excitation in an AC generator reduces gap decreases, manufacturing difficulty increases in the size and complexity of the generator. The a non-linear fashion. slip rings and field excitation no longer have to be provided, and the high energy density of Surface and Interior Mounting the permanent magnets allows the size and Stricter government standards for electric motor weight of the alternator to be reduced. One efficiency have put tremendous pressure on ACIM of the most important issues in the design manufacturers. Initial efforts to increase efficiency and manufacturing of any permanent magnet were focused on magnet wire material and rotor machine is the method used to hold the magnets designs, followed by the use of external variable in place and to prevent them from flying off frequency drive electronics to control acceleration during operation due to centrifugal forces.” and minimize inrush current during startup. More recently, ACIM designers have incorporated The authors clearly describe the options design permanent magnets in rotor designs to further engineers had at the time: boost electrical efficiency. These modern ACIM configurations embed the permanent magnets into “Gluing or banding the magnets in place a stack of magnetic steel laminations bonded to increases the cost and complexity of the the rotor. This configuration is called an interior manufacturing process, whereas, burying the permanent magnet rotor. Because the magnets are magnets increases the magnet leakage flux captured within the rotor lamination stack, there is and the complexity of the magnetic design and little concern over magnet retention. model.” Unlike the ACIM configuration, permanent magnets At higher performance levels, adhesive alone was in a BLDC motor are bonded to the outside of the not enough to retain the position and integrity of rotor, a configuration called a surface permanent surface mounted magnets for the expected life of magnet rotor. Surface mounted magnets need to the motor. Motor designers gradually took a “belt be held in place with a very strong and reliable and suspenders” approach to magnet retention adhesive to prevent movement or breakage of the and started wrapping the rotor assemblies, known magnets during operation, complicating design as “roving,” with various materials to secure requirements and adding to manufacturing costs— the magnets in place should the glue bond fail. but surface magnet rotors offer higher performance Common materials used for banding or roving characteristics than interior magnet rotors. included fiberglass, Kevlar, and Inconel. These materials provided added protection and in many Evolution of Design cases extended the life of the motor, but they were In the publication IEEE Transactions on Industry still vulnerable to failure in demanding applications Applications in 1996, authors Michael W. Degner, involving high speeds or high temperatures. The Richard Van Maaren, Azza Fahim, Donald W. authors went on to recommend the latter method, a Novotny, Robert D. Lorenz, and Charles D. buried magnet design: Syverson outlined the problems of magnet retention on high speed rotors: “A major problem in the design and manufacturing of surface mounted permanent “The advent of high-energy product, rare-earth magnet machines is reliably holding the permanent magnet materials has brought permanent magnets in place at high speeds. 3 This paper evaluates a unique rotor lamination was titled “Nonmagnetic magnet retention channel design for a high pole number, permanent arrangement for high speed rotors.” Apart from magnet alternator. This buried magnet design, the difference in magnetic properties of the which is capable of reliably holding the channel material, the two designs had very similar permanent magnets in place at high speeds, descriptions. offers both easier and cheaper assembly when compared with the methods currently used in In 2008, Hamilton Sundstrand (now part of Collins surface mounted permanent magnet machines. Aerospace) filed a patent for retention of permanent Finite element analysis is used to compare magnets in rotors. Titled “Magnet retention system the buried magnet design with equivalent for permanent magnet motors and generators,” it surface mounted designs and shows that the described a design with slots in the rotor that held performance of the alternator is not significantly the
Details
-
File Typepdf
-
Upload Time-
-
Content LanguagesEnglish
-
Upload UserAnonymous/Not logged-in
-
File Pages5 Page
-
File Size-