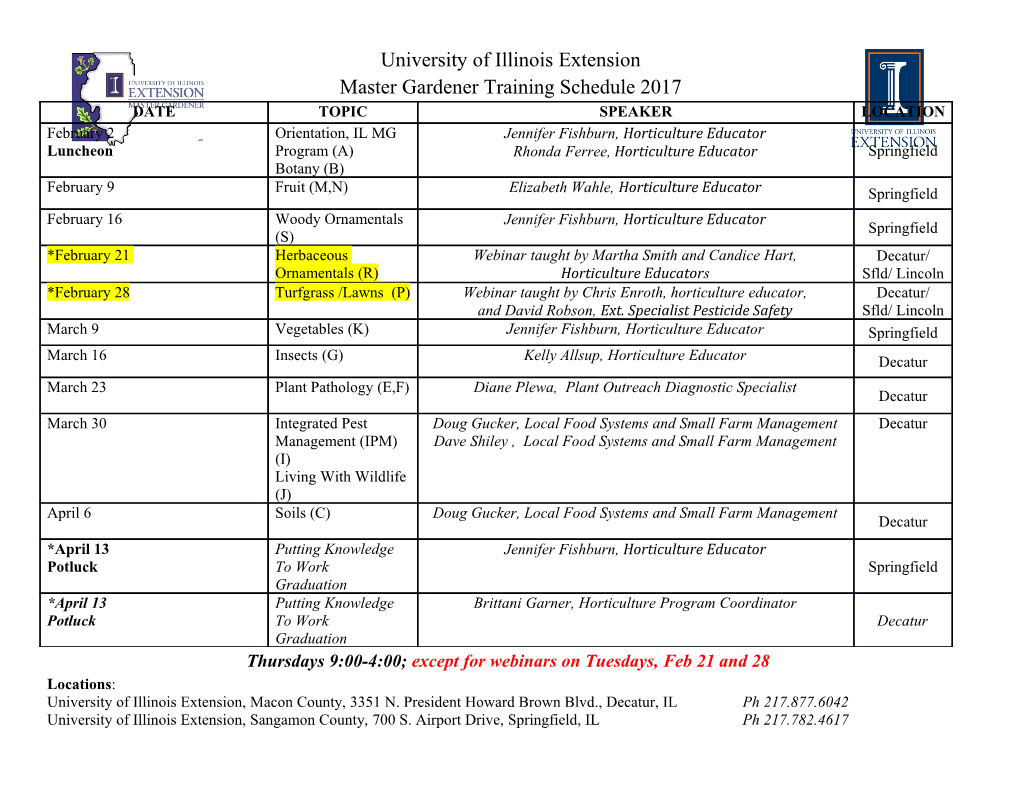
energies Article Hybrid Excited Synchronous Machine with Wireless Supply Control System Marcin Wardach * , Michal Bonislawski , Ryszard Palka, Piotr Paplicki and Pawel Prajzendanc Faculty of Electrical Engineering, West Pomeranian University of Technology, Szczecin, Sikorskiego 37, 70-313 Szczecin, Poland * Correspondence: [email protected]; Tel.: +48-91-449-42-17 Received: 27 June 2019; Accepted: 13 August 2019; Published: 16 August 2019 Abstract: The paper presents an unconventional approach to control the hybrid excited synchronous machine (HESM), which can be used for drives of pure electric vehicles. The hybrid excitation of the additional control coil placed on the rotor of the machine has been realized by the wireless energy transfer system connected with the rotor shaft. Experimental results of back-EMF characteristics obtained on a prototype of HESM were compared with 3-dimentional finite elements analysis (3D-FEA) predictions. This design, despite some additional complications in the power supply system of the machine, simplifies the mechanical construction and reduces the control coil’s losses compared to the construction with the coil placed on the stator. Keywords: permanent magnet machines; wireless power transmission; electric vehicles; finite element methods; variable speed drives 1. Introduction Generally, the air gap flux controlling in a permanent magnet machine can be realized in two ways: By the appropriate control system or by the relevant changes of the machine design. Conventional permanent magnet (PM) machines have a constant, non-adjustable excitation flux, which limits the power, thus becoming an important limitation. In the case of U/f = const. control strategy implementation, due to the limited power of the supply voltage and limited dielectric strength of winding insulation, to achieve higher speeds it is required to weaken the excitation flux, in order to reduce the back-EMF value. A very popular method of field weakening is realized by adjusting the current in the d-axis of the machine. This strategy, however, generates increased losses in the supply system and creates the risk of permanent magnets demagnetization, and consequently decreases the resultant torque of the machine. Conventional permanent magnet excited synchronous machines (PMSM), used as a drive in modern electric vehicles, suffer from the limited battery voltage in high-speed regions because of high back-EMF values. The field weakening (which is obligatory) requires design of machines with lower power conversion characteristics. This caused the development of hybrid excited synchronous machines [1–16]. These machines have PM excitation and an additional toroidal excitation coil fixed on the stator or mounted in the rotor in the machine axial center. By the proper powering of this coil, the amplitude of the induced voltage can be effectively controlled in the range from zero to values above those of classical permanent magnet machines. The hybrid excited synchronous machines have already been designed, optimized and measured very intensively [6–9]. For the reason mentioned above, in this paper an unconventional approach to control the hybrid excited synchronous machine (HESM), which can be used for the drives of electric vehicles, has been proposed. This solution consists of the hybrid excitation, which is characterized by the fact that the Energies 2019, 12, 3153; doi:10.3390/en12163153 www.mdpi.com/journal/energies Energies 2019,, 12,, xx FORFOR PEERPEER REVIEWREVIEW 2 of 12 2. Review of PM Machines with Adjustable Flux Excitation To realize the controlling of the excitation field (back-EMF) of the machine with PMs, different methods that require structural changes have been used. Regarding to reluctance machines the Energiesmethods2019 that, 12, 3153require structural changes have been used. Regarding to reluctance machines2 ofthe 12 construction with two parts of salient permanent magnets (double salient permanent magnet— DSPM) was proposed. DSPM machines are realized with internal (Figure 1) and external rotor additionalstructures control[10,11], coil wherein is placed the onsolu thetiontion machine ofof thethe rotorouterouter and rotor,rotor, the asas power shownshown supply inin FigureFigure is implemented 2,2, hashas nono additionaladditional using the wirelesscontrol coil. energy The transfer advantage system of these connected machines with is the a lower rotor production shaft. cost caused by small amounts of permanent magnets. 2. Review of PM Machines with Adjustable Flux Excitation The other design of cylindrical machines with permanent magnets is one with a movable rotor, which—atTo realize higher the speeds—moves controlling of the in the excitation axial direction, field (back-EMF) leaving its of part the outside machine of with the stator PMs, [12]. different Such methodsa solution that leads require very effectively structural to changes the reduction have been of back-EMF, used. Regarding but its disadvantage to reluctance is machinesa complicated the constructionstructure and with the two lack parts of possibility of salient permanentto increase magnets the excitation (double flux, salient useful permanent atat lowlow magnet—DSPM)speedspeed operationoperation wasrange. proposed. DSPM machines are realized with internal (Figure1) and external rotor structures [ 10,11], whereinInIn thethe the literatureliterature solution cancan of alsoalso the bebe outer foundfound rotor, designsdesigns asshown withwith aa dodo inuble Figure rotor.2, hasIn this no solution additional there control is one shaft, coil. Thewhich advantage is common of theseto two machines different isrotor a lower topologies: production A conventional cost caused PM by rotor small and amounts laminated of permanentreluctance rotor magnets. without magnets. This conception allows to obtain a machine which has a high ratio Ld/Lq of inductances Ld/Lq [13].[13]. FigureFigure 1.1. DSPMDSPM machinemachine withwith internalinternal rotor.rotor. FigureFigure 2.2. DSPMDSPM machinemachine withwith externalexternal rotor.rotor. TheMany other designs design are of described cylindrical in paper machines [14], with where permanent thethe authorsauthors magnets presentpresent is solutionssolutions one with ofof a movable hybridhybrid excitedexcited rotor, which—atmachines higherfor both speeds—moves cylindrical and in disk-type the axial direction, machines. leaving Similar its characteristics part outside of can the statorbe obtained [12]. Such with a solutionsuitably leadslocated very magnetic effectively barriers to the [15]. reduction In the literature of back-EMF, are also but known its disadvantage designs of isclaw a complicated pole [16,17] structure(Figure(Figure 3)3) and andand the disc-typedisc-type lack of possibility machinesmachines withwith to increase adjustableadjustable the excitation excitationexcitation flux, fluxflux useful [18].[18]. at low speed operation range. In the literature can also be found designs with a double rotor. In this solution there is one shaft, which is common to two different rotor topologies: A conventional PM rotor and laminated reluctance rotor without magnets. This conception allows to obtain a machine which has a high ratio of inductances Ld/Lq [13]. Many designs are described in paper [14], where the authors present solutions of hybrid excited machines for both cylindrical and disk-type machines. Similar characteristics can be obtained with suitably located magnetic barriers [15]. In the literature are also known designs of claw pole [16,17] (Figure3) and disc-type machines with adjustable excitation flux [18]. Hybrid excited Vernier machines are a large group of machines with adjustable excitation flux. In a previous paper [19], structures with magnets mounted on the surface and using magnetic concentrators were presented. Whereas, [20] presents a Vernier permanent magnet machine that uses homopolar topology. The authors of [21] presented research of the machine, whose rotor consists of two parts: One has permanent magnets, and the other electromagnets analogous to that of the wound field synchronous machines. Energies 2019, 12, x FOR PEER REVIEW 2 of 12 2. Review of PM Machines with Adjustable Flux Excitation To realize the controlling of the excitation field (back-EMF) of the machine with PMs, different methods that require structural changes have been used. Regarding to reluctance machines the construction with two parts of salient permanent magnets (double salient permanent magnet— DSPM) was proposed. DSPM machines are realized with internal (Figure 1) and external rotor structures [10,11], wherein the solution of the outer rotor, as shown in Figure 2, has no additional control coil. The advantage of these machines is a lower production cost caused by small amounts of permanent magnets. The other design of cylindrical machines with permanent magnets is one with a movable rotor, which—at higher speeds—moves in the axial direction, leaving its part outside of the stator [12]. Such a solution leads very effectively to the reduction of back-EMF, but its disadvantage is a complicated structure and the lack of possibility to increase the excitation flux, useful at low speed operation range. In the literature can also be found designs with a double rotor. In this solution there is one shaft, which is common to two different rotor topologies: A conventional PM rotor and laminated reluctance rotor without magnets. This conception allows to obtain a machine which has a high ratio of inductances Ld/Lq [13]. Figure 1. DSPM
Details
-
File Typepdf
-
Upload Time-
-
Content LanguagesEnglish
-
Upload UserAnonymous/Not logged-in
-
File Pages12 Page
-
File Size-