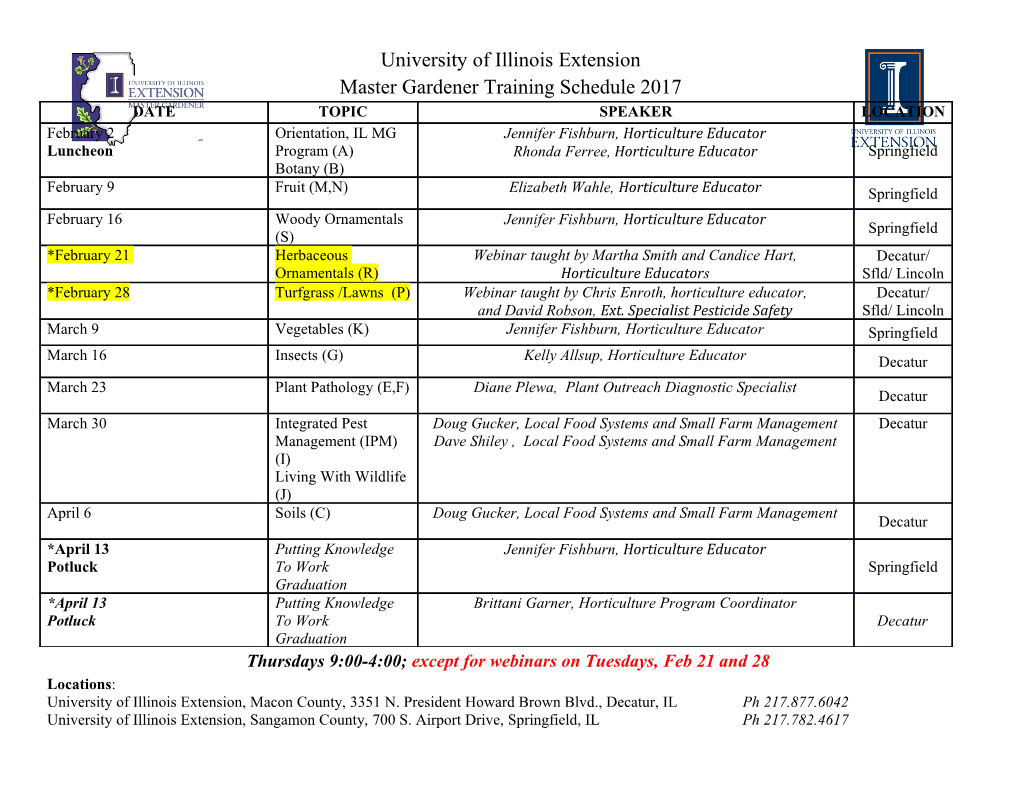
Polymer(Korea), Vol. 32, No. 2, pp 95-102, 2008 Versatic Acid/Vinyl Acetate의 비닐 에스테르를 가지는 α,ω-Diacrylate Poly(dimethylsiloxane)의 에멀션 공중합 연구 Hamid Javaherian Naghash7, Shadpour MallakpourF, Parivash Yavari Forushani, and Nurseli UyanikFF Department of Chemistry, Islamic Azad University, Shahreza Branch, P.O. Box 311-86145, Shahreza, Isfahan, I. R. Iran. *Organic Polymer Chemistry Research Laboratory, College of Chemistry, Isfahan University of Technology, Isfahan 84156, Iran **Department of Chemistry, Istanbul Technical University, 80626 Maslak, Istanbul, Turkey (2007년 8월 21일 접수, 2008년 1월 19일 채택) A Study on Emulsion Copolymerization of α,ω-Diacrylate Poly(dimethylsiloxane) Containing Vinyl Ester of Versatic Acid/Vinyl Acetate Hamid Javaherian Naghash7, Shadpour MallakpourF, Parivash Yavari Forushani, and Nurseli UyanikFF Department of Chemistry, Islamic Azad University, Shahreza Branch, P.O. Box 311-86145, Shahreza, Isfahan, I. R. Iran *Organic Polymer Chemistry Research Laboratory, College of Chemistry, Isfahan University of Technology, Isfahan 84156, Iran **Department of Chemistry, Istanbul Technical University, 80626 Maslak, Istanbul, Turkey (Received August 21, 2007; Accepted January 19, 2008) Abstract: The α,ω-diacrylate poly(dimethylsiloxane) (DA-PDMS) containing vinyl ester of versatic acid/vinyl acetate (Veova-10/VAc) was prepared by emulsion copolymerization of (DA-PDMS), Veova-10 (with VAc), and auxiliary agents at 85 ℃ in the presence of ammonium peroxodisulfate (APS) as an initiator. Sodium dodecyl sulfate (SDS) and nonylphenol ethylene oxide-40 units (NP-40) were used as anionic and nonionic emulsifiers, respectively. The resulting copolymers were characterized by using Fourier transform infrared spectroscopy (FT-IR). Thermal properties of the copolymers were studied by using thermogravimetric analysis (TGA) and differential scanning calorimetry (DSC). The morphology of copolymers was also investigated by scanning electron microscopy (SEM) and then the effects of variables such as temperature, agitation speed, surfactant kinds, molecular weights, initiator, and DA-PDMS concentrations on the properties of the silicone-containing Veova-10/VAc emulsions were examined. The calculation of monomer conversion versus time histories indicates that by increasing the DA-PDMS concentration the polymerization rate and the number of polymer particles decrease, respectively. Keywords: emulsion copolymerization, silicone containing emulsions, α,ω-diacrylate poly(dimethyl- siloxane), vinyl ester of versatic acid, vinyl acetate. Introduction interior architectural coatings, adhesives and paints),3,4 the poly(vinyl acetate)(PVAc) based latexes are particularly Water-based adhesives have become increasingly im- attractive. Moreover, the copolymerization of VAc with other portant as the range of applications of polymer materials monomers (such as vinyl chloride,5 vinyl versatate,6 acrylate,7-12 widens. Currently, worldwide efforts are aimed at reducing vinyl propionate, methacrylate, maleate acid, ethylene or the volatile organic solvent content of most adhesive ma- acrylonitrile2 provides useful latexes with a wide range of terials. This has promoted the search for a new generation properties. The Veova-10/VAc emulsion copolymer is one of high performance water-based adhesives to replace the of the most important industrial latexes, widely used in 1-3 conventional solvent-based technology. architectural coatings market. This copolymer can be dried Due to their potential industrial application (exterior and at room temperature or under heated conditions, which has †To whom correspondence should be addressed. a relatively good durability. Therefore, aqueous Veova- E-mail: [email protected] 10/VAc polymer emulsions have been widely used as a resin 95 96 Hamid Javaherian NaghashᆞShadpour MallakpourᆞParivash Yavari ForushaniᆞNurseli Uyanik for aqueous paints. However, the Veova-10/VAc and/or (HEC) was supplied from Fluka and used without further acrylate copolymers, when exposed to UV lights and en- purification. Water was distilled and deionized. All of the vironmental conditions its quality, is deteriorated. As a result, solvents such as N,N-dimethylformamide (DMF), dimethyl- it loses its gloss retentivity.13 sulfoxide (DMSO), N-methylpyrrolidone (NMP), and dime- In order to solve these difficulties, it was proposed to add thylacetamide (DMAC) were purchased from Merck and silicone to an aqueous Veova-10/VAc and acrylate polymer distillated before using for reactions. emulsions to increase the coating resistance to UV light, Polymerization Procedure. Continuous emulsion copolymeri- oxygen, water and various types of solvents. These will zation was carried out using a 500 mL, 5-necked round improve the durability of the coating.14-17 Also, Yamaya and bottom flask equipped with a reflux condenser, stainless steel coworkers18 emphasized that silicone resins, resulting from stirrer, sampling device and two separate feed streams. The hydrolytic condensation of silane compounds, could be used first feed stream was a solution of VAc, Veova-10, DA- since they are able to form films having high hardness, water, PDMS, and anionic surfactant. The other feed was the initiator and heat resistance. solution with 3.0×10-3 molL-1 concentration. Before emulsion In this work, the influence of DA-PDMS co-monomer copolymerization start-up, the reaction vessel was first charged on the emulsion copolymerization of Veova-10/VAc with with the desired amounts of water, emulsifier, NaHCO3 and sodium dodecyl sulfate and nonylphenol ethylene oxide- initiator solution respectively. During polymerization process 40 units as mixed emulsifiers were investigated. The stability the reaction mixture was stirred at a rate of 200 rpm and and the copolymerization kinetics of the Veova-10/VAc the temperature was maintained at 60 ℃. After 5 min a small emulsion modified by DA-PDMS were compared with portion of the monomer mixture was added to the flask at Veova-10/VAc. Also, the effects of temperature, agitation a period of 20 min. Then, the temperature was kept at 85 ℃ speed, surfactant kinds and their weights and also initiator until the end of polymerization. The polymerization was per- and (DA-PDMS) concentrations on the properties of the formed under air atmosphere to investigate the effect of copolymers were examined. The properties of the latexes temperature, agitation speed, initiator and DA-PDMS con- including heat stability and (Tg) were measured and evaluated. centration on monomer conversion. A typical recipe for the In addition, the structure of the terpolymers was also clarified. preparation of a 52% solid product and the process is given in Table 1 and Scheme 1, respectively. Experimental In order to determine the conversion percentage during the polymerization process, it was necessary to withdraw Materials and Equipment. Reagent grade VAc (Fisher Scien- samples at various intervals from the reaction vessel. These tific Co) was further purified by distillation in a rotary eva- samples are relatively small so that the overall composition porator at reduced pressure of 30 mmHg to remove inhibitor. in the reactor is not seriously affected. Once a sample is The Veova-10 provided by Achema (Lithuania) was also removed and put in a watch glass, polymerization is terminated distillated under vacuum and stored at 0 ℃ to avoid thermal by the addition of 7 ppm hydroquinone. Then two drops of polymerization. The DA-PDMS was a commercial product ethanol is added to the sample as a coagulant agent and of Goldschmidt Chemical Corp., Germany (Tegomer V-Si the contents of the watch glass were evaporated at room 2150 with Mn =1298±70 g/mol). It was dried at 70 ℃ in a temperature, and then dried to a constant weight in a vacuum vacuum oven for 48 h before using. NaHCO3 (Merck) was analytical grade and used directly without further purification. Table 1. Polymerization Recipe at 85 ℃ Sodium lauryl sulfo acetate (SLSA), sodium methyl cocoil Compound Initial charge Feed Total torat (SMCT) and sodium dodecyl sulfate (SDS) were Veova-10(g) 1.00 8.86 9.86 purchased from Hoechst AG Germany and used directly VAc(g) 3.86 34.74 38.60 without further purification. Sodium dodecyl benzene sulfonate Variable DA-PDMS(g) 10% w 90% w (SDBS) and dioctyl sodium sulfosuccinate (DSS) provided (0-5) by Henkel KGaA Germany and used as received. Sodium Protective colloid:HEC 0.26 - 0.26 lauryl ether sulfate (SLES) and sodium cocoil isotionate (SCI) Buffer: NaHCO3(g) 0.75 - 0.75 were kindly supplied from Akzo Chemicals BV, Netherlands Initiator:(NH4)2S2O8(g) 0.10 0.40 0.50 Demineralized water(g) 126 - 126 and used also as received. Nonylphenol ethylene oxide-40 Nonionicemulsifier:Nonylphenol 5.00 - 5.00 units (NP, Iconol NP-40, BASF), Germany and initiator APS Ethylene oxide-40 units, NP-40(g) (Fisons), were used as received. Hydroxyethyl-cellulose Anionic emulsifier:SDS(g) 0.50 4.50 5.00 폴리머, 제32권 제2호, 2008년 A Study of DA-PDMS Containing Veova-10/VAc Emulsion Copolymerization 97 O * R CH3 C O CH CH2 + A + O CH CH O OH 3 3 OH CH CH C O CH CH CH OSi(CH ) O Si (CH ) O CH CH CH O C CH CH 2 2 2 2 m 2 m 2 2 2 CH CH B 3 n 3 + CH 3 O R C C O CH CH 1 2 R C 2 emulsion copolymerization R1=R2=C7H15 _ R*=ᆞOH and SO4 CH3 CH3 .............. .............. CH CH ( CH2 CH (CH2) Si O Si (CH2) 2 ) m m n CH CH CH CH CH ( 2 CH 3 n 3 2 ) n O O C O C O CH3 CH3 C R 1 R 2 Scheme 1. A:VAc, B:DA-PDMS, C:Veova-10. oven. The conversion percentage was determined gravi- copolymers, respectively. Although the produced copolymers metrically. The number of polymer particles per unit volume have low solubility in various solvents such as toluene, of water (NT) was calculated from the monomer conversion benzene, acetic acid, xylene, DMF, DMSO, NMP, acetone and XM and the volume average diameter of the polymer particles, dichloroetane, which makes it difficult for their characteri- 19-21 dv was determined by a scanning electron microscope, zation, their morphology as well as thermal properties gave using the following equations: important information about their structure and property relation.
Details
-
File Typepdf
-
Upload Time-
-
Content LanguagesEnglish
-
Upload UserAnonymous/Not logged-in
-
File Pages8 Page
-
File Size-