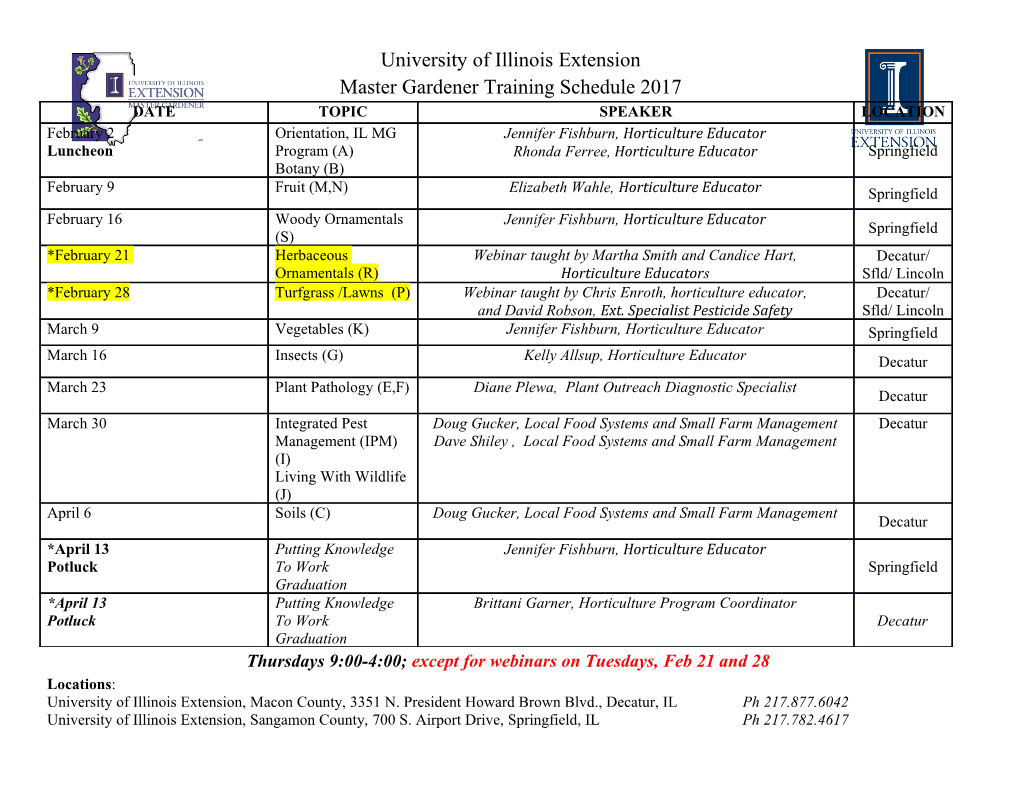
71st International Astronautical Congress (IAC) – The CyberSpace Edition, 12-14 October 2020. Copyright ©2020 by the International Astronautical Federation (IAF). All rights reserved. [KEYNOTE] IAC-20-C4-7-1 The Synergetic Air-Breathing Rocket Engine (SABRE) - Development Status Update Feast, S. Reaction Engines Limited, Building F5, Culham Science Centre, Abingdon, Oxfordshire, OX14 3DB, UK [email protected] Abstract This paper provides an overview and development status update on the Synergetic Air-Breathing Rocket Engine (SABRE), currently under development at Reaction Engines in the UK. SABRE is a new class of propulsion system which incorporates elements of both air-breathing and rocket technologies with light-weight, high performance heat exchangers. The resulting engine is a high efficiency rocket system, capable of using air as its oxidiser during the initial ascent phase of the launch up to hypersonic (Mach 5) flight speeds in the atmosphere. Beyond this point, SABRE can transition to operate as a pure liquid fuelled rocket engine, using liquid oxygen (LOX) from tanks on- board the launch vehicle to continue to provide high thrust propulsion at higher speed and altitude. The air-breathing capability offered by SABRE provides a significant mass saving which enables a number of architectural and design benefits, leading to a practical, low-cost reusable aircraft-like launch vehicle. This brings many positive operational attributes compared to present-day launch vehicles (with vertical take-off and landing), such as improved reliability, increased launch cadenced, robust mission abort capability, greater re-entry cross range and reduced ground operations complexity. The full development of SABRE and its prospective vehicle applications is a complex engineering undertaking, requiring a multitude of sub-systems and technologies. However, due to the modular system architecture of SABRE, many of the technology development activities can be performed in parallel and can also significantly capitalise on the substantial experience and heritage of the existing space launch and aerospace industry, including their well-established supply chain. The overall SABRE development programme follows an agile aerospace development process with a carefully structured incremental development logic, designed to mature the overall system technology to an acceptable level in order to achieve operational readiness with minimum cost and risk. Some new and novel enabling technologies are introduced into the SABRE design (most notably the high performance light-weight heat exchangers) and early de-risk of these have been the focus of the SABRE development programme to date. Reaction Engines have already undergone an extensive and successful development and test programme to de-risk the heat exchanger technology – most recently (in 2019) the air pre-cooler was successfully ground tested under Mach 5 equivalent conditions, becoming a world first achievement in this area of technology. In addition to an update on the SABRE programme, this presentation will also address the key challenges and opportunities associated with the development of the various SABRE technologies Keywords: (SABRE, Development, Hypersonic, Precooled, Air-breathing, Rocket) Acronyms/Abbreviations 1. Introduction Commercial-Off-The-Shelf (COTS) The SABRE engine has been under development by Air-breathing core ground development (DEMO-A) Reaction Engines for over 30 years. During this time a Rocket systems ground development (DEMO-R) significant understanding of its applicability to Space launch has been made, together with a strong maturity Nacelle systems ground development (DEMO-N) of its overall design and performance. Hypersonic Test Bed (HTB) Today, the SABRE programme is receiving High-Temperature Heat Exchanger Test (HTX) significant interest and support from government Liquid Hydrogen (LH2) agencies and industry, having demonstrated many of the Liquid Oxygen (LOX) critical technologies previously considered to be a major Return-to-Launch-Site (RTLS) challenge for the overall concept. SABRE is now Single Stage to-Orbit (SSTO) progressing into a new phase, focusing towards integrated development and testing for many of its Synergetic Air-Breathing Rocket Engine (SABRE) major systems and building the supply chain for the full Technology Readiness Level (TRL) product engine. This paper sets out to both introduce the Two-Stage-to Orbit (TSTO) SABRE system as well as provide an overview and status update for the current development programme. IAC-20-C4.7.1 Page 1 of 12 71st International Astronautical Congress (IAC) – The CyberSpace Edition, 12-14 October 2020. Copyright ©2020 by the International Astronautical Federation (IAF). All rights reserved. 2. SABRE Engine Overview To achieve the required cooling, an air pre-cooler (heat exchanger) is placed between the air-intake and 2.1 SABRE Operational Overview core engine. The precooler reduces and maintains the intake air temperatures at near constant conditions, SABRE is a combined cycle air-breathing and rocket providing a fixed design point for the core engine. The engine. The design of SABRE is intended to address the precooler also allows continuous operation of the air- limitations of any single propulsion system by breathing core engine beyond the conventional combining jet engine, ramjet and rocket engine operating limits imposed on conventional gas-turbines technologies, integrated together into a single engine (~Mach 2.5) throughout the entire air-breathing portion nacelle. The main capability SABRE offers is the ability of the ascent trajectory up to Mach 5. to operate as an air-breathing engine for part of the During air-breathing operation, the SABRE cycle ascent, reducing the overall weight of oxidiser carried uses its liquid hydrogen fuel as a heat sink, the cooling on the vehicle, giving a significant improvement in the requires a heat exchanger that is both lightweight, as overall mass ratio of the launch system it is used upon. well as able to extract multiple MW of heat required to reduce the stagnation temperature of captured air at Mach 5 from 1350 K down to low temperatures. A simplified representative overview of the SABRE thermodynamic cycle is presented in figure 2, highlighting the main fluid streams and heat exchangers used for thermal management. The air pre-cooler operates as part of a closed-loop cooling system, which forms an integral part of the core engine thermodynamic power cycle. The cooling loop Fig. 1. SABRE Engine Installed Layout uses high pressure helium as its working fluid and coolant inside the air pre-cooler. The helium rejects heat SABRE has two separate modes of operation during through a separate heat exchanger with the cold the launch ascent trajectory. At take-off from a runway cryogenic liquid hydrogen fuel (already on the vehicle), and up to flight speeds of around Mach 5, SABRE which acts as the overall a heat sink for the cycle. operates in ‘air-breathing mode’, taking in atmospheric The helium is continuously circulated around the air through a conical intake as a source of oxidiser for closed loop between the high-temperature pre-cooler the hydrogen fuel. Beyond Mach 5, the air-breathing (heat source) and very low temperature LH2 heat systems shut down and the intake cone translates to a exchanger (Heat sink). The large temperature difference fully closed position. The engine then transitions over to around the helium loop is used thermodynamically, as a a pure liquid fuelled rocket engine using a separate on- heat engine, as a means of generating internal work; the board supply of liquid oxygen as the source of oxidiser. high-temperature helium downstream of the pre-cooler In ‘rocket mode’ SABRE has higher thrust to continue is expanded through a turbine which drives the core to accelerate the launch vehicle to orbital or near-orbital engine turbo-compressor. In addition to this, the helium velocity, depending on the mission and vehicle design. is also used in a similar way to drive the fuel pump and This results in a single integrated propulsion system that helium circulator turbines. This results in a highly can serve across the entire flight envelope from stand- efficient engine cycle with all combustion gasses being still to orbital insertion speeds with potential to achieve directed for propulsive power out the engine nozzle. Single Stage-to-Orbit (SSTO) or be used as part of a Two-Stage-To-Orbit (TSTO) horizontal launch architecture. 2.2 SABRE Functional Overview During air-breathing mode, supersonic air is captured by the intake and slowed to sub-sonic speeds inside the engine nacelle, allowing conventional jet- engine compressor technology to be used within the air- breathing core engine. However during this process, the high kinetic energy of the air is converted to heat, due to slowing and compression through the intake and at high Mach numbers this requires significant cooling prior to Fig. 2. Representative SABRE thermodynamic cycle ingestion into the core engine. IAC-20-C4.7.1 Page 2 of 12 71st International Astronautical Congress (IAC) – The CyberSpace Edition, 12-14 October 2020. Copyright ©2020 by the International Astronautical Federation (IAF). All rights reserved. During air-breathing mode, the fuel flow required Reaction Engines has already performed an for air cooling (i.e. for the helium cycle heat rejection) extensive development and test programme to de-risk exceeds the flow actually required for stoichiometric the precooler
Details
-
File Typepdf
-
Upload Time-
-
Content LanguagesEnglish
-
Upload UserAnonymous/Not logged-in
-
File Pages12 Page
-
File Size-