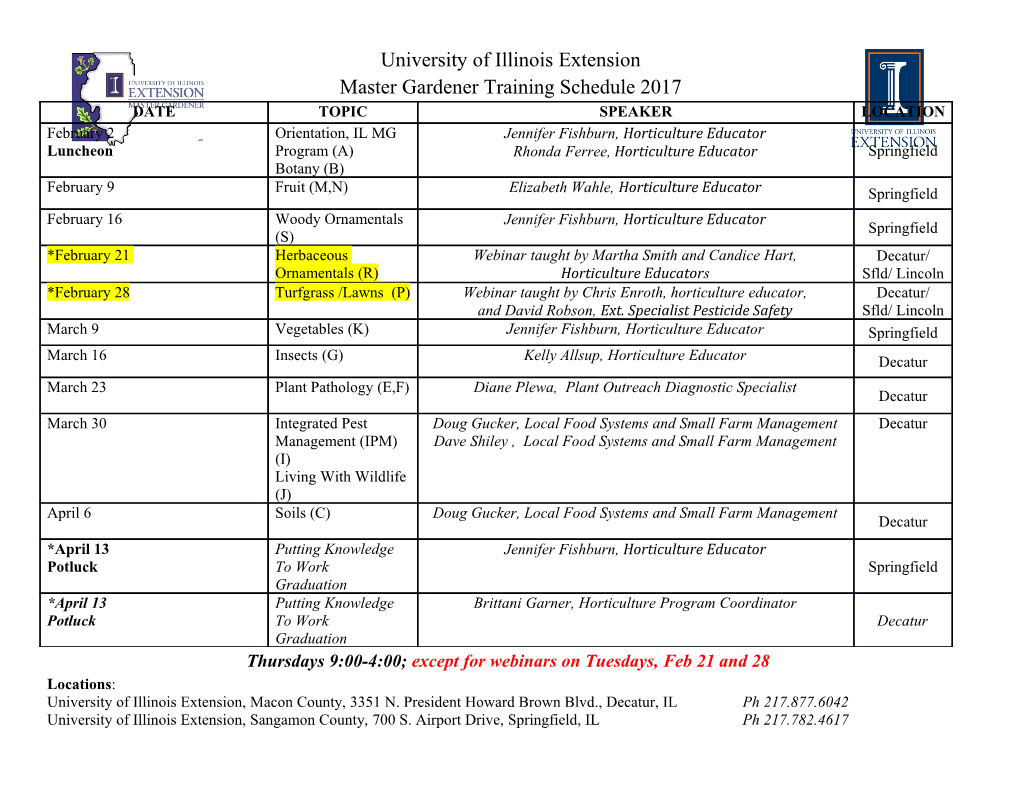
Europäisches Patentamt & (19) European Patent Office Office européen des brevets (11) EP 1 083 194 B9 (12) CORRECTED EUROPEAN PATENT SPECIFICATION Note: Bibliography reflects the latest situation (15) Correction information: (51) Int Cl.: Corrected version no 1 (W1 B1) C08G 73/10 (2006.01) C08G 73/06 (2006.01) Corrections, see page(s) 3 (48) Corrigendum issued on: 20.12.2006 Bulletin 2006/51 (45) Date of publication and mention of the grant of the patent: 10.05.2006 Bulletin 2006/19 (21) Application number: 00307798.9 (22) Date of filing: 08.09.2000 (54) Process for the manufacture of polyaspartic acid Verfahren zur Herstellung von Polyasparaginsäure Procédé de préparation d’acide polyaspartique (84) Designated Contracting States: • Yasuda, Shinzo AT BE CH CY DE DK ES FI FR GB GR IE IT LI LU Ushiku-shi, MC NL PT SE Ibaraki 300-1236 (JP) (30) Priority: 10.09.1999 JP 25797399 (74) Representative: Bassil, Nicholas Charles et al Kilburn & Strode (43) Date of publication of application: 20 Red Lion Street 14.03.2001 Bulletin 2001/11 London WC1R 4PJ (GB) (73) Proprietor: NIPPON SHOKUBAI CO., LTD. (56) References cited: Osaka-shi, Osaka 541-0043 (JP) US-A- 5 688 902 US-A- 5 830 985 US-A- 5 888 959 US-A- 5 929 198 (72) Inventors: • Mukouyama, Masaharu Tsukuba-gun, Ibaraki 300-1236 (JP) Note: Within nine months from the publication of the mention of the grant of the European patent, any person may give notice to the European Patent Office of opposition to the European patent granted. Notice of opposition shall be filed in a written reasoned statement. It shall not be deemed to have been filed until the opposition fee has been paid. (Art. 99(1) European Patent Convention). EP 1 083 194 B9 Printed by Jouve, 75001 PARIS (FR) EP 1 083 194 B9 Description [0001] This invention relates to a polyaspartic acid excelling in biodegradability and a method for the production thereof. [0002] Conventionally polyaspartic acid has been produced by the dehydrating method which comprises heating solid 5 aspartic acid thereby removing water therefrom. Methods which comprise heating solid aspartic acid in the presence of an acid catalyst (US 5688902, US 5457176, and US 5830985) or in the absence of a catalyst (US 5391764 and US 5319145) by using a varying drying machine, a kneading and heating device, or an oven in the neighborhood of 200°C thereby dehydrating and condensing the solid aspartic acid, heating solid aspartic acid in an organic solvent of a high boiling point thereby removing the water of condensation by azeotropy (US 5380817, US 5484945, and US 5756595), 10 have been heretofore proposed for the production of polyaspartic acid. [0003] For the purpose of polymerizing aspartic acid by using sulfuric acid, phosphoric acid, or boric acid as an acid catalyst, methods which comprises continuing the polymerization while removing the water of polymerization, and using water for aiding in uniformly mixing the acid catalyst with the aspartic acid have been disclosed. These methods, however, produce a substantially dried solid polymer by removing the water of polymerization by decompression, exposure to a 15 stream of nitrogen, or azeotropy notwithstanding the relevant reactions proceed in their initial stages in the presence of water. [0004] In these methods the solid aspartic acid tends to form a bulk substance during the course of polymerization and, therefore, it needs to perform such actions as disintegration on the bulk substance during the course of polymeri- zation. Particularly when the acid catalyst is used, the polymerization forms a bulk substance like candy, thus this bulk 20 substance must be disintegrated. [0005] Further, the material derived from aspartic acid by heating in these methods is a solid polysuccinimide which is an intermediate of polyaspartic acid. The polysuccinimide is hydrolyzed with a base to produce a polyaspartic acid salt. [0006] It is an object of this invention to obtain directly an acid type polyaspartic acid by a method which avoids forming a bulk substance in producing the polyaspartic acid by condensing an amino acid having aspartic acid essentially. 25 [0007] It is further an object of this invention to provide a polyaspartic acid with improved biodegradability. [0008] The conventional method consists in performing the relevant polymerization while removing the water of po- lymerization. Unexpectedly it has been found that when an amino acid having aspartic acid as an essential component is suspended in water and heated, polyaspartic acid is formed even in the presence of water, the polymer yield exceeds 80%, the formed polymer is obtained in a state dissolved in water, and the polymer is an acid type polyaspartic acid 30 polymer. As a result, this invention has been achieved. [0009] The object of this invention is accomplished by a method for the production of a polyaspartic acid characterized by the steps of mixing an amino acid having aspartic acid as an essential component with water and heating the resultant mixture in a vessel having an inner pressure exceeding 0,3 mPa. [0010] Further, the object of this invention is accomplished by a polyaspartic acid having such biodegradability that 35 the ratio of biodegradation per 7 days of BOD is not less than 45%. [0011] By the method of production according to this invention, a polyaspartic acid (containing an amino acid having polyaspartic acid as an essential component) having an excellent biodegradability can be obtained by an extremely simple procedure. [0012] The polyaspartic acid of this invention is excellent particularly in biodegradability. 40 [0013] Since the polyaspartic acid of this invention excels in biodegradability, it is suitable as detergent additives, dispersion stabilizers, scale preventing agents, humectants, and fertilizers. [0014] The above and other objects, features and advantages of the present invention will become clear from the following description of the preferred embodiments. [0015] The term "polyaspartic acid" as used herein also embraces salts of polyaspartic acid. The counterions of 45 polyaspartic acid include, but not limited to those below, for example alkali metals and alkaline earth metals, specifically sodium, potassium, magnesium, calcium, strontium, and ammonium cations. [0016] This invention uses, as the raw material, an amino acid having aspartic acid as an essential component. The aspartic acid can be used in the form of L-, D-, or a mixture thereof. The aspartic acid may additionally incorporate therein one or more other amino acids in an amount up to 99 % by weight, preferably 5 to 99% by weight, based on the weight 50 of the aspartic acid. Suitable examples of the other amino acids may include glycin, alanine, asparagine, glutamic acid, lysine, valine, leucine, isoleucine, phenylalanine, methionine, histidine, proline, serine, threonine, and cysteine. Among other amino acids mentioned above, L-glutamic acid, L- alanine, and L-lysine prove particularly preferable because they are inexpensive and the polymers produced have high water solubility. [0017] In this invention, polyaspartic acid can be produced by heating an amino acid having aspartic acid as an 55 essential component (hereinafter occasionally referred to simply as "aspartic acid") in the presence of water. [0018] The amount of the water to be used in the polymerization, though not particularly limited, generally has a lower limit of not less than 0.2 times, preferably not less than 0.5 times, and more preferably not less than 1 times and an upper limit of not more than 40 times, preferably not more than 20 times, and more preferably not more than 10 times 2 EP 1 083 194 B9 the weight of the amino acid having aspartic acid as a main component. The amount of the water is preferred to be in the range of 0.2 to 40 times, especially 0.5 to 20 times, based on the weight of the amino acid having aspartic acid as the main component. If the amount is less than 0.2 times, the shortage will be at a disadvantage in suffering the resultant polymer to assume a bulk form. If this amount exceeds 40 times, the excess will be at a disadvantage in suffering the 5 aqueous solution of the produced polymer to have an unduly low concentration and rendering the polymerization une- conomical. [0019] The heating temperature in the polymerization, though not particularly limited, generally has a lower limit of not less than 140°C, preferably not less than 150°C, and more preferably not less than 160°C and an upper limit of not more than 300°C, preferably not more than 250°C, and more preferably not more than 220°C. The heating temperature is 10 preferred to be in the range of 140 to 300 °C, especially 150 to 250 °C. If the heating temperature is less than 100°C, the shortage will be at a disadvantage in lowering the yield of polymer. Conversely, if it exceeds 300°C, the excess will be at a disadvantage in impairing the biodegradability, one of the characteristics of the produced polymer. [0020] The reaction is generally performed in a closed vessel proof against pressure, therefore, preferred to have an inner pressure exceeding 0.3 MPa, preferably in the range of 0.5 - 4 MPa. 15 [0021] An acid catalyst is preferably added in the polymerization of an amino acid. Commendably, an organic or inorganic acid having a lower pKa value than that of aspartic acid is used as the acid catalyst. Suitable examples of the inorganic acid may include phosphoric acids such as orthophosphoric, metaphosphoric, and polyphosphoric acids, phosphonic acids, phosphinic acids, sulfuric acid, sulfurous acid, pyrosulfuric acid, boric acid, and trifluoromethane sulfonic acid. Suitable examples of the organic acid may include acidic phosphoric esters such as methyl phosphoric, 20 ethyl phosphoric, and phenyl phosphoric acids, phosphonic esters such as methyl phosphonic, ethyl phosphonic, butyl phosphonic, lauryl phosphonic, stearyl phosphonic, and phenyl phosphonic acids, and methane sulfonic acid and para- toluene sulfonic acid.
Details
-
File Typepdf
-
Upload Time-
-
Content LanguagesEnglish
-
Upload UserAnonymous/Not logged-in
-
File Pages12 Page
-
File Size-