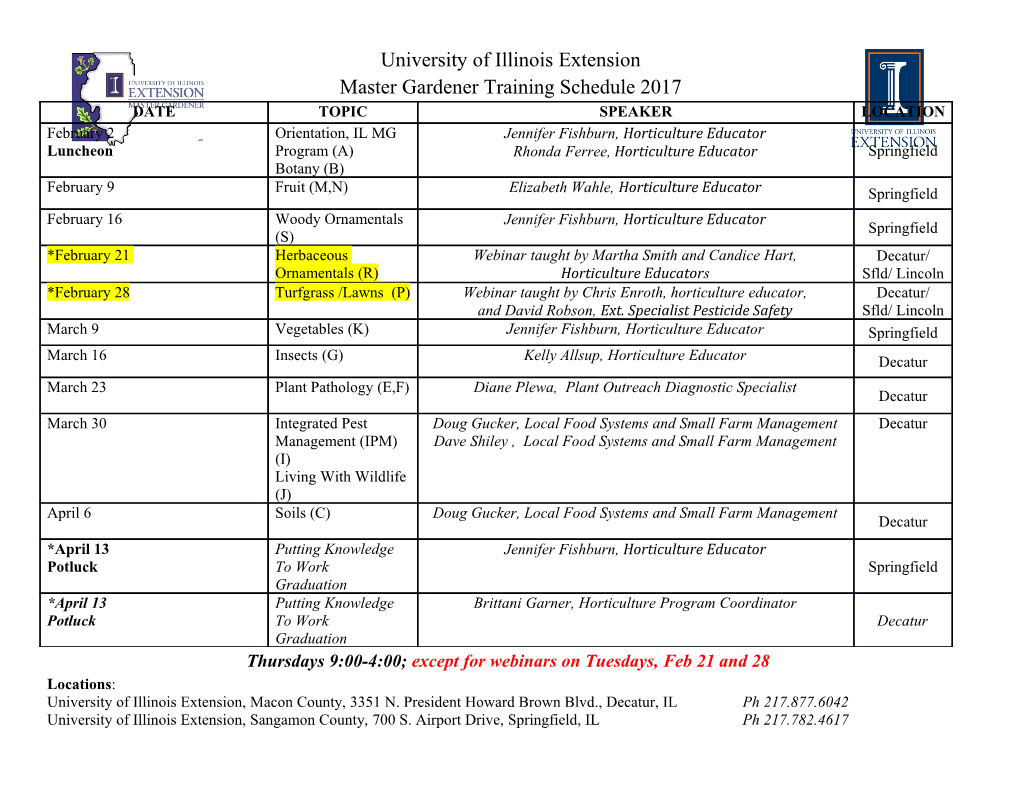
View metadata, citation and similar papers at core.ac.uk brought to you by CORE provided by Repository for Publications and Research Data Research Collection Conference Paper Energy Equivalent of Compressed Air Consumption in a Machine Tool Environment Author(s): Züst, Simon; Gontarz, Adam; Wegener, Konrad Publication Date: 2013 Permanent Link: https://doi.org/10.3929/ethz-a-009959904 Rights / License: In Copyright - Non-Commercial Use Permitted This page was generated automatically upon download from the ETH Zurich Research Collection. For more information please consult the Terms of use. ETH Library 11.5 Energy Equivalent of Compressed Air Consumption in a Machine Tool Environment S. Züst 1, A. Gontarz 2, K. Wegener 2 1 inspire AG Zurich, Switzerland 2 Institute of Machine Tools and Manufacturing (IWF), Swiss Federal Institute of Technology, Switzerland Abstract Compressed air has many applications in machine tools. Compared to the potential energy stored in the fluid tank its production requires a large amount of energy. In addition to the potential energy, heat loss does occur as by-products. Dependent on the amount of heat loss, energy consuming cooling is required. For life-cycle investigations of machine tools, the gray energy and environmental impacts of compressed air consumptions have to be known. This work presents a theoretical approach to quantify the energy equivalent of compressed air and its by-products. A model based approach is set up to describe the required physical relationships for the compressor and its peripheral components. Measurements obtained from a shop floor compressed air supply have been used to validate the results of the theoretical approach. Concluding from the analysis, a general approach for the theoretical energy equivalent calculation, including the compressor and treatment of heat loss, is possible. Keywords: Compressed air equivalent, machine tool modeling, energy monitoring 1 INTRODUCTION compressed air, the need of a common unit for consolidation Compressed air is a frequently used energy carrier in and respective conversion equivalents is obvious. machine tools. Some examples of possible applications are Goal of this work is the derivation and validation of an pneumatic components, tool handling or protection of electrical energy equivalent for compressed air used by a machine components by sealing air. Compressed air is a machine tool. As the machine tool environment is a thermal resource consumed by the machine and therefore related to sensitive area, heat sources and heat sinks must be the energy and resource efficiency. Energy efficient machine evaluated with care. The equivalent must further be tool design is an emerging topic. In this context, the ISO adaptable for various conditions, e.g. different pressure standard 14’955-1 is under development and has reached the levels, system characteristics, operational schedules and level of a drafted international standard (DIS) [1]. For an degrees of system integration. energy analysis according to the new standard, all energies supplied to the machine tool must be known. Further, the 2 STATE OF THE ART energy content of all the resources must be expressed in a common unit, in order to allow a synthetisation of the different Electric energy equivalents for compressed air can be energy flows to the total consumption but also for comparison obtained from measurements or estimated by models. of different energy carriers. Measured energy equivalents are specific for a certain compressed air system configuration, whereas models allow Compared to other energy carriers, compressed air is a cost a generic parametrizable approach. Gauchel [5] introduced intensive medium [2, 3]. The cost is mostly caused by the assessment approaches for compressed air, that are in line electricity needed for the compressor supplying compressed with assessment and improvement approaches from Energy air [4], amplified by inefficiencies and thermal effects making Schweiz [8]. Joseph and D’Antonio [9, 10] showed different up to 93% of the electric input power [5]. Machine tools ways for the compressed air system assessment. The generate heat loss during operation; therefore excess heat is authors mentioned a production effort of 0.12 to 0.27 kWh/m3 an issue of great importance. Whereas the supply of at nominal conditions for supply pressures in the range of 7 to compressed air causes excess heat in a remote part of the 8 bar. Nominal conditions are defined in DIN 1343 [11]. For factory, the use of compressed air, i. e. the decompression in the sake of simplicity only the unit ‘m3’ is further on used, a machine tool, represents a heat sink, causing a direct referring to cubic meter at normal conditions. Modeling of impact on its thermal conditions. compressed air supply from the view of energy consumption Power measurements on machine tools have shown a was performed by Schmidt et.al. [12], D’Antonio [10], and substantial share of energy for the thermal conditioning of the Hütter [4]. The theoretical values for adiabatic compression manufacturing process and of the machine tool itself, are mentioned by Harris et.al [13] to be in the range of 0.08 to including compressed air consumption [6]. For the evaluation 0.10 kWh/m3, dependent on the pressure. The authors as of energy efficiency of machine tools as well as for modeling well demonstrate the quantification of heat recovery influence for analysis and optimization purposes, quantification of to the system efficiency by an exgergy based approach. energy needs on component level by selective The resulting compressed air energy equivalents of Schmidt, measurements are essential. This is required by ISO/DIS D’Antonio, Hütter and Harris are in the range of 0.08 to 14’955 [1] and is successfully demonstrated by Gontarz et.al. 0.14 kWh/m3. Application and use of such equivalents were [7]. In case of multiple energy supplies, i. e. electricity and successfully shown in energy monitoring and assessments The 11th Global Conference on Sustainable Manufacturing 394 S. Züst, A. Gontarz, K. Wegener [14, 15]. All mentioned publications of compressed air energy described in Figure 2: Air enters the air system at certain equivalents consider the ratio between electrical power input conditions, is compressed by the compressor and cooled to to the compressor and volumetric flow per time. Energy the temperature out. The compressed air is stored in a vessel consumptions due to secondary effects, like the treatment of until it is used by a machine tool. As shown in Figure 2, the heat loss, are not included. A more comprehensive energy inlet, production and consumption are locally separated, equivalent for compressed air is required, which includes the preventing heat exchange in between. thermal effects and distribution system pressure losses as Production of the compressed air includes the compressor, well. Thermal effects and losses are in general very specific the cooler and the vessel. Since the cooler is often integrated for each site. The new approach is thereto demanded to be in the compressor, both components will be modeled as one. adoptable to different systems, which leads to a model based Objective of this system is the provision of the systems equivalent. Promising modeling approaches of compressed downstream with compressed air at pressure level pcomp. For air consuming devices by Harris et.al. [16-18] encourage a this process, the following model is used: The pressure is model based approach for the compressed air production ✞ raised adiabatically by ✝ p pcomp, resulting into a temperature electric power demand as well. raise. A subsequent isochoric cooling lowers the intermediate gas temperature to in. Compression and cooling are 3 METHODOLOGY repeated, until pcomp is reached. Using the first law of thermodynamics for a steady state system, the following In order to fulfill the above mentioned goals and energy demand for the compressor results: requirements, a three-stage procedure is applied: 1. Identification and modeling of the relevant electric ✡ ✌ ✏ 1 ✓ pcomp ✍ ✑ ✗ ✖ ✕ ✔ ✔ ✔ ✔ ✟ energy, pneumatic work and heat flows within a Wcomp ☛Vn n Rs in ln (2) ✍ ✑ ✘ p ✟ ☛ ✎ compressed air system. comp ✒ in ✠ ☞ 2. Formulation of the theoretical energy equivalent for compressed air based on the results of the modeling. The term in square brackets from Equation (2) represents the fluid dynamical work required for the compression, where the 3. Validation of the theoretical results and assumptions from first part includes the combined motor and shaft efficiency the system modeling by measurements within a case ✙ comp of the system. Gas properties are included in the study. specific gas constant Rs and the density ✚ n at normal To derive the required energy equivalent for compressed air, conditions. Heat losses generated by the compressor due to a model based approach is presented. The used system friction and ohmic losses are described by the compressor model and its boundaries are shown in Figure 1. The model efficiency ✙ comp as well: inputs consist of the demanded amount of compressed air Vn ✥ ✢✣✤ ✜ and inlet air conditions, represented by pressure pin and Qcomp Wcomp ✛1 comp (3) temperature in. The outputs of the model are the required electric energies Wel and thermal losses Qth. The isochoric temperature drop of the compressed gas within Given this dependency and the system boundary above, the the cooler requires a heat flux ✦ extr. Integrating this flux energy equivalent in this approach is defined as: results in the
Details
-
File Typepdf
-
Upload Time-
-
Content LanguagesEnglish
-
Upload UserAnonymous/Not logged-in
-
File Pages7 Page
-
File Size-