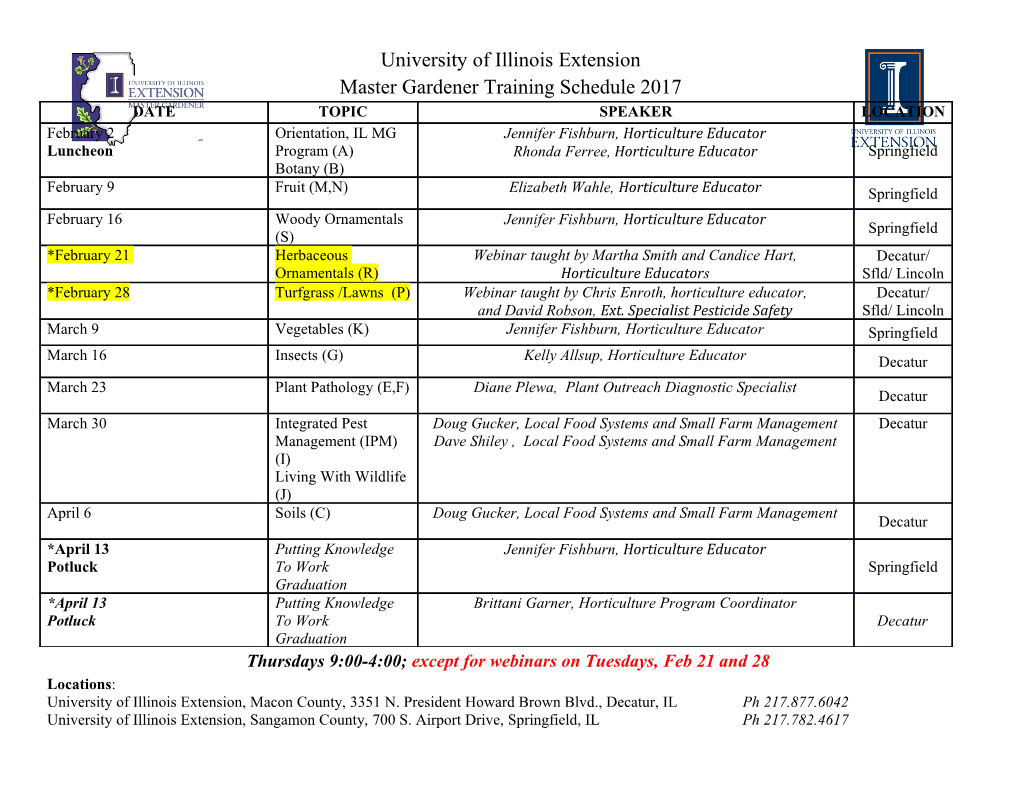
Name ///sr-nova/Dclabs_wip/Failure_Analysis/5113_43-86.pdf/Chap_02/ 18/8/2008 2:54PM Plate # 0 pg 43 © 2008 ASM International. All Rights Reserved. Failure Analysis of Heat Treated Steel Component (#05113G) www.asminternational.org Overview of the Mechanisms of Failure in Heat Treated Steel Components Scott MacKenzie, Houghton International, Inc. “Primum non nocere” — “First do no harm,” attributed to the ancient Roman physician Galen. “Declare the past, diagnose the present, foretell the future; practice these acts ...make a habit of two things — to help, or at least to do no harm” (Ref 1). FAILURES IN STEEL components, like any unanticipated failures. Higher stresses or unan- other material, may have various consequences, ticipated service conditions can cause unfore- such as: seen failure because of complex or increased stress fields. Stress concentrations may become Making the device or component completely more critical because of the increase in loading inoperable for the new application. Preventing an operable device from func- Insufficient design criteria can also be the tioning satisfactorily cause of unforeseen failures. Inadequate Making the device or component unsafe or knowledge of the stress state in the component unreliable, with immediate removal from or inadequate stress calculations can contribute service required to failures. Much higher stress states than initi- Many aspects may also be involved in tracing ally assumed or improper stress assumptions can back to the possible sources of failure of a result in premature service failures. Lack of component. Some of these sources include: consideration of severe environmental, fatigue, or impact conditions may contribute to failure. Design Material issues can usually be attributed to Material issues, such as improper materials either selection of material or material imper- selection or material imperfections (laps, fections rendering it unsuitable for service. In- seams, inclusions, porosity, etc.) adequate material data can also result in Fabrication and processing conditions that may contribute to failure. For Rework example, adequate fatigue data, elevated-tem- Assembly perature tensile data, or creep or corrosion data Inspection may not be available, and the designer may have Storage and shipment to extrapolate or estimate the effects or these Service conditions properties. Maintenance Other sources of failure can be attributed to Unanticipated service conditions material imperfections. For wrought products, Many times, more than one factor contributes to this could be related to segregation, inclusions, a part failure. Rarely is it only one factor. porosity, laps, and seams. For castings, these imperfections could be cold shuts, inclusions, shrinkage, voids, and porosity. Forgings can General Sources of Failure have laps, seams, segregation, and anisotropy in properties from forging flow lines. Design deficiencies are a common source of In one example (Fig. 1), a large roll was heat component failure. Examples include the pre- treated, and several large cracks were observed sence of a sharp notch in regions of high stress or after inspection. This was originally attributed to a fillet radii that is too sharp. Using a component quench cracking. On further examination, it was design for a new application can also lead to determined that a lap was present in the forging, Name ///sr-nova/Dclabs_wip/Failure_Analysis/5113_43-86.pdf/Chap_02/ 18/8/2008 2:54PM Plate # 0 pg 44 © 2008 ASM International. All Rights Reserved. Failure Analysis of Heat Treated Steel Component (#05113G) www.asminternational.org 44 / Failure Analysis of Heat Treated Steel Components indicated by the presence of high-temperature abusive, can cause large temperature gradients oxides in the crack along the crack faces. and localized overheating. This overheating can Manufacture and Processing. Processing cause changes in microstructure—either loca- can have a large influence on properties and the lized softening of the material or localized resulting residual stresses. Typically, this is transformation to martensite and other trans- related to wrong procedures or improperly spe- formation products—resulting in hard spots. cified procedures. Ambiguous processes or In Fig. 2, a large gear was ground after heat specifications can also contribute to failures due treatment. Because of abusive grinding, local to interpretation or application. Simple things temperatures exceeded the austenitization tem- like improper selection of processing sequences perature, and transformation to martensite or procedures or specifications that were not occurred upon cooling. This transformation and followed can also contribute to failure. the resulting residual stresses caused cracking of Cold forming, such as stretching or deep the gear. Temper etch examination of the gear drawing, can develop highly localized residual using dilute nitric acid in water in the regions of stresses. Local changes in microstructure can cracking showed evidence of localized abusive occur. Because of the changes in reduction, a grinding. large anisotropy in material properties also re- Identification of parts can also cause failure to sults. Due to the drawing operation, cracks or initiate. This is from localized impact or electro- microcracking can occur. This could be due to etching. Localized mechanical stress concen- improper lubrication or improper die design. trations or changes in microstructure can occur. The localized changes in ductility can also con- This creates either a mechanical or micro- tribute to failure. structural notch or stress concentration. Machining and grinding can create high Heat treatment can cause a variety of different residual stresses from either machining practice root causes for failures. Overheating, decarbur- (feeds and speeds) or improper cutting tool ization, quenching, tempering, annealing, and selection, material, or geometry. Grinding, if other heat treatments can cause failure to occur. Fig. 1 A large roll was found to have cracks on the outer and inner surfaces of the forging. These cracks were found during final inspection. During examination of metallographic sections taken from the roll, high-temperature oxides were found on the crack faces, strongly suggesting forging laps. Name ///sr-nova/Dclabs_wip/Failure_Analysis/5113_43-86.pdf/Chap_02/ 18/8/2008 2:54PM Plate # 0 pg 45 © 2008 ASM International. All Rights Reserved. Failure Analysis of Heat Treated Steel Component (#05113G) www.asminternational.org Overview of the Mechanisms of Failure in Heat Treated Steel Components / 45 This could also include improper austenitization There are also several embrittlement mech- temperatures and times. Decarburization is the anisms caused by the use of improper tempering result of a low-carbon surface from improper temperatures. Temper embrittlement and blue atmosphere control. Typically, there is a deple- brittleness are just two of the common mech- ted carbon layer at the surface that, when anisms that can occur from improper heat quenched, is softer than the core material. This treatment and tempering operations. soft layer can be completely devoid of carbon Cleaning, pickling, and electroplating op- (complete decarburization) or only partially erations can also cause potential failures or depleted in carbon (partial decarburization). contribute to them. Hydrogen charging of high- This decarburized layer can contribute to pre- strength steels from the dissociation of hydro- mature fatigue failures, because the surface gen on the surface of high-strength steel can material is different than the designer expected, occur from cleaning operations in acids. Char- or failure can result from high residual stresses ging of hydrogen from high current densities created at the surface from the quenching in electroplating can cause hydrogen embrittle- operation. The low-carbon surface area can also ment unless proper baking procedures are used result in distortion—again, high residual tensile to allow the hydrogen to diffuse out. Electro- stresses at the surface with low surface hardness. plating can also cause high residual tensile Carburization is similar to the effects of de- stresses, which can contribute to crack initiation. carburization. In this case, there is a higher sur- Welding can cause many different problems. face carbon than expected. High residual tensile These problems can be cracks that are initiated stresses can result as well as increased distortion. from improper welding procedures, high resi- Quenching can also contribute to high resi- dual stresses, porosity from inadequately dried dual stresses or the formation of cracks or weld rods, or dirty workpieces. Microstructural microcracking. Transformation stresses from notches or stress concentrations from the heat- quenching cause the high residual stresses. affected zone and the transition to the base These high residual tensile stresses can drasti- material can be the result of improper preheat cally reduce the fatigue strength or have other and postheat. Improper weld penetration, weld ramifications in service. geometry, and excessive weld current (under- Overheating can cause excessive grain cutting) can also cause mechanical stress con- growth, with resulting increases in hardenability centrations (Fig. 3). and increased embrittlement. Underheating can The mast arm failure shown in Fig. 3 (Ref 2) cause poor mechanical properties, because there was the result of weld bead undercutting and was an incomplete transformation to austenite
Details
-
File Typepdf
-
Upload Time-
-
Content LanguagesEnglish
-
Upload UserAnonymous/Not logged-in
-
File Pages45 Page
-
File Size-