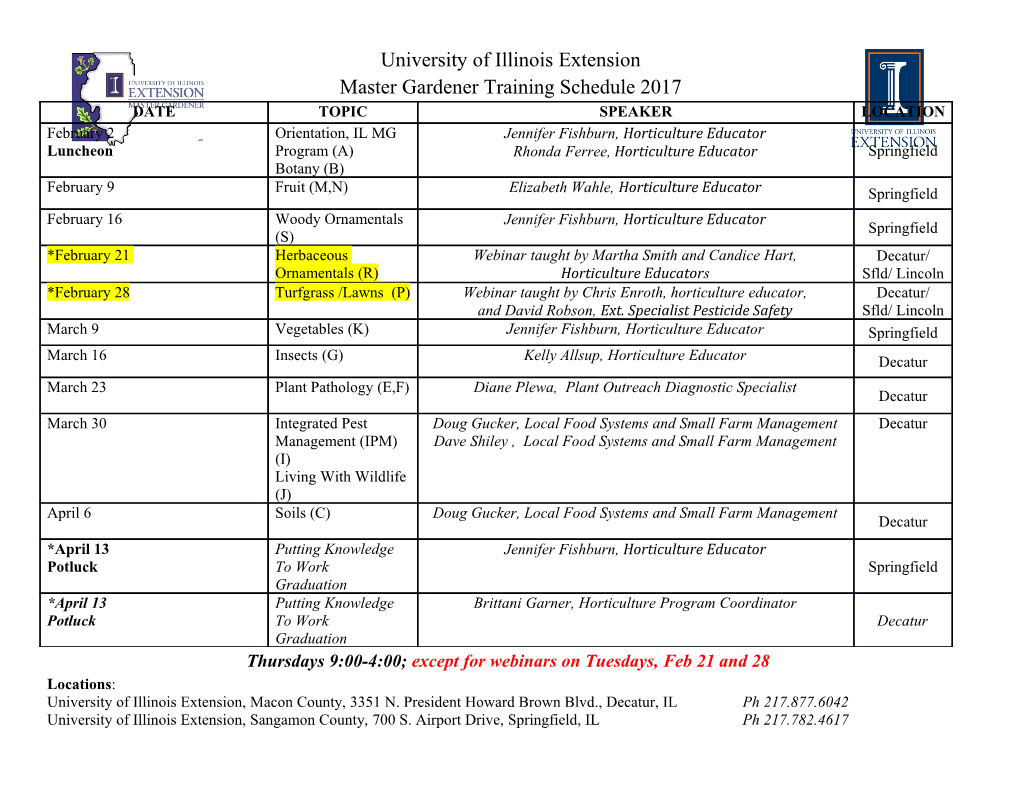
materials Technical Note Diamond-Like-Carbon Coated Dies for Electromagnetic Embossing Marius Herrmann 1,2,3,*, Björn Beckschwarte 1,3, Henning Hasselbruch 4, Julian Heidhoff 3,4, Christian Schenck 1,2,3, Oltmann Riemer 4 , Andreas Mehner 4 and Bernd Kuhfuss 1,2,3 1 Bremen Institute for Mechanical Engineering–Bime, University Bremen, 28359 Bremen, Germany; [email protected] (B.B.); [email protected] (C.S.); [email protected] (B.K.) 2 MAPEX Center for Materials and Processing, University Bremen, 28359 Bremen, Germany 3 University of Bremen, 28359 Bremen, Germany; heidhoff@iwt-bremen.de 4 Leibniz Institute for Materials Engineering–IWT, 28359 Bremen, Germany; [email protected] (H.H.); [email protected] (O.R.); [email protected] (A.M.) * Correspondence: [email protected]; Tel.: +49-0421-2186-4822 Received: 8 September 2020; Accepted: 29 October 2020; Published: 3 November 2020 Abstract: Electromagnetic forming is a high-speed process, which features contactless force transmission. Hence, punching operations can be realized with a one-sided die and without a mechanical punch. As the forces act as body forces in the part near the surface, the process is especially convenient for embossing microstructures on thin sheet metals. Nevertheless, the die design is critical concerning wear like adhesion. Several die materials were tested, like aluminum, copper as well as different steel types. For all die materials adhesion phenomena were observed. To prevent such adhesion an a-C:H-PVD (Physical Vapor Deposition)-coating was applied to steel dies (X153CrMoV12) and tested by embossing aluminum sheets (Al99.5). By this enhancement of the die adhesion was prevented. Furthermore, the die surface was structured with tribology-effective patterns that were generated by micro hard milling. The embossing quality was topographically analyzed with respect to different initial surface states of the sheets. It was identified that thicker sheets facilitate better embossing results. Moreover, the initial sheet surface has a decisive influence on the embossing quality, whereby the characteristic of the topography showed different susceptibility on the initial sheet surface state. Keywords: impulse forming; adhesion; micro hard milling; hardened tool steel; a-C:H coating 1. Introduction In electromagnetic forming a contactless force transmission is used to realize a high-speed forming process and applied to processing sheet metal with thicknesses greater than 1 mm [1] as well as tubes [2]. During the process, a high current peak is generated by short-circuiting a capacitor bank via a coil. Thus, an electromagnetic field is generated and an eddy current in an electrically conductive workpiece occurs. Due to the repulsive force (Lorentz’ force) between coil and workpiece, the workpiece is accelerated into an embossing die, see Figure1. In the case of thin sheets, the penetration depth of the magnetic field is larger than the sheet thickness (skin depth > sheet thickness). Thus, the magnetic wave penetrates the die material as well and hence, an eddy current is generated in the forming die. The impact of such a current was investigated by Cao [3]. He generated the current in the die by using a further tool coil and found that a higher current density in the die enlarges the forming depth. The thickness of the sheet influences also the current density in the primary working coil which in turn affects the magnetic field [4]. Materials 2020, 13, 4939; doi:10.3390/ma13214939 www.mdpi.com/journal/materials Materials 2020, 13, 4939 2 of 10 Materials 2020, 13, x FOR PEER REVIEW 2 of 10 FigureFigure 1. Electromagnetic 1. Electromagnetic embossing: embossing: ( a(a)) scheme;scheme; ( (bb)) height height profile profile of ofinitial initial sheet sheet surfaces. surfaces. MotivatedMotivated by the by advantagesthe advantages of the of the process process like like contactless contactless force force transmission transmission and and thus thus a a one-sided one- die [5sided], high die strain [5], high rates strain [6] as rates well [6] as as changes well as inchange plastics in material plastic material properties proper [7],ties the [7], process the process is applied is to formingapplied [8], cuttingto forming [9], [8], joining cutting [10 [9],] and joining embossing [10] and [embossing11]. The process [11]. The is process also used is also to used process to process large parts large parts in way of incremental free forming [12], as well as incremental joining [13]. Besides the in way of incremental free forming [12], as well as incremental joining [13]. Besides the macro range the macro range the process can also be used in the micro range, so that edge radii down to 120 µm can process can also be used in the micro range, so that edge radii down to 120 µm can be achieved without be achieved without failure during deep drawing of thin sheets [14]. Higher deformation degrees failurecompared during deep to conventional drawing of thinforming sheets are [ 14possible]. Higher and deformation thus the limits degrees of the compared deformation to conventional can be formingextended are possible [15]. Further and thusadvantages the limits in electromagneti of the deformationc forming can are be the extended reduction [ 15of ].wrinkling Further [16] advantages and in electromagneticspringback [17]. forming Both are are especially the reduction of great of wrinklinginterest for [16 the] and electromagnetic springback [17embossing]. Both are process. especially of greatHowever, interest the for formation the electromagnetic of an air cushion embossing can have process. a negative However, influence theor justify formation the rebound of an air [18]. cushion can have aSurfaces negative with influence embossed or microstructures justify the rebound are of grow [18].ing industrial interest [19], either for optical Surfacesfunctions with[20] or embossed with tribological microstructures effects [21]. are The of later growing are used industrial for example interest on semi-finished [19], either sheets for optical functionsfor reducing [20] or withthe friction tribological force in effects dry deep [21 ].draw Theing later operations are used [22]. for Electromagnetic example on semi-finished embossing has sheets been investigated in the macro [23] as well as the micro range [20]. Kamal et al. examined two-stage for reducing the friction force in dry deep drawing operations [22]. Electromagnetic embossing has electromagnetic embossing of microstructures and dealt with problems of significant die wear and beensheet-die investigated welding. in the They macro concluded [23] as that well die as materials the micro as range well as [20 coatings]. Kamal should et al. be examined investigated two-stage to electromagneticmitigate these embossing problems of [11]. microstructures First investigations and dealt of withcoated problems dies have of been significant carried die out wear for and sheet-dieelectromagnetic welding. Theyforming. concluded DLC (Diamond-Like-Carbon) that die materials as coatings, well as soft coatings layers should (MoS2) beand investigated Ti/TiAlN to mitigatemultilayers these problems on the dies [11 ].while First forming investigations 1.5 mm ofthick coated aluminum dies have sheets been were carried investigated out for electromagneticand the die forming.wear DLCcould (Diamond-Like-Carbon) be reduced significantly [24]. coatings, Vogli et soft al. suggest layers (MoS2)DLC coatings and Ti to/TiAlN be more multilayers suitable due on the dies whileto their forming better wear 1.5 resistance mm thick [25]. aluminum sheets were investigated and the die wear could be reduced significantlyIn this study, [24 coated]. Vogli dies et al.for suggestelectromagneti DLC coatingsc embossing to be of more thin suitablesheets are due investigated. to their better For wear resistanceelectromagnetic [25]. embossing, solutions for reducing the adhesion phenomena needs to be found like die coatings but the coating performance needs to take into account considering eddy current in the In this study, coated dies for electromagnetic embossing of thin sheets are investigated. die by the penetrating of the magnetic wave. Thus, the adhesion tendency of the workpiece material For electromagneticas well as the die embossing, wear are solutionsexamined. forFinally, reducing the embossing the adhesion of tribology-effective phenomena needs patterns to be foundis like diecharacterized coatings butand theevaluated. coating performance needs to take into account considering eddy current in the die by the penetrating of the magnetic wave. Thus, the adhesion tendency of the workpiece material2. Materials as well asand the Methods die wear are examined. Finally, the embossing of tribology-effective patterns is characterized and evaluated. 2.1. Die Manufacturing 2. MaterialsAt first, and different Methods die materials (not coated) were investigated to evaluate the adhesion tendency of aluminum workpiece (Al99.5, EN AW-1050A) to ground die surfaces. Beside aluminum alloy 2.1. Die(AlCuMgPb, Manufacturing EN AW-2007), also copper (E-Cu57, EN CW004A) and three steel types were Atinvestigated, first, different that is, die austenitic materials chrome-nickel (not coated) steel were (X5CrNi18-10, investigated EN toevaluate 10088-3) and the adhesiontwo cold working tendency of aluminumdie steels workpiece (90MnCrV8, (Al99.5, EN EN 90MnCrV8 AW-1050A) and to X153CrMoV12, ground die surfaces. EN X153CrMoV12). Beside aluminum The X153CrMoV12 alloy (AlCuMgPb, was additionally investigated with
Details
-
File Typepdf
-
Upload Time-
-
Content LanguagesEnglish
-
Upload UserAnonymous/Not logged-in
-
File Pages10 Page
-
File Size-