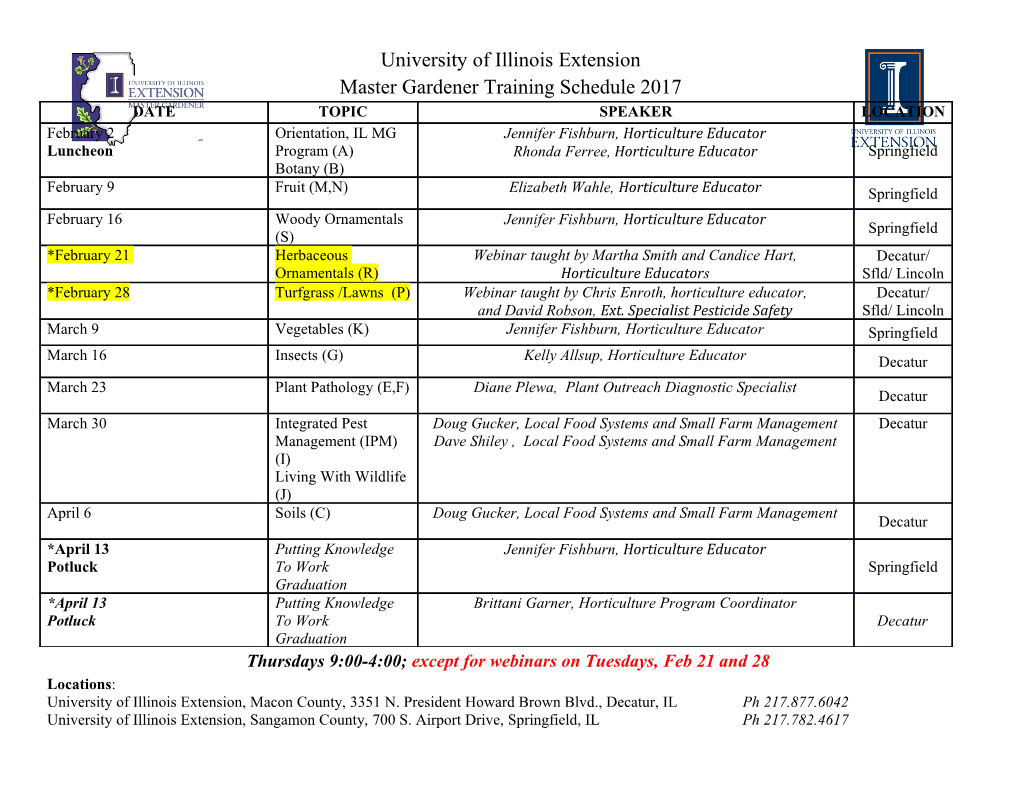
Pocket guide on hem flange bonding 2 Pocket guide on hem flange bonding Contents 1. Introduction to adhesive bonding..................................................... 4 1.1 Body in white production ........................................................... 5 1.2 Adhesive bonding in BIW production ........................................ 6 1.3 What is a hem flange? ................................................................. 7 1.4 Why do you need to hem and bond a flange? .......................... 8 1.5 Challenges in the industry .......................................................... 9 2. Influence factors ................................................................................. 10 3. Process description ............................................................................ 14 3.1 Layouts ......................................................................................... 15 3.1.1 Manual .................................................................................... 16 3.1.2 Automatic – Pedestal ............................................................. 17 3.1.3 Automatic – Robot ................................................................. 18 3.2 Typical materials and system parameters in use ...................... 19 3.3 Hemming methods ...................................................................... 20 3.3.1 Table top hemming ................................................................ 21 3.3.2 Roller hemming ...................................................................... 22 3.3.3 Press hemming ...................................................................... 23 3.4 Additional production steps ....................................................... 24 4. Quality ................................................................................................. 25 4.1 Quality requirements ................................................................... 25 4.2 Quality issues ............................................................................... 26 4.2.1 Squeeze outs .......................................................................... 26 4.2.2 Meander .................................................................................. 27 4.2.3 PVC bubbles ........................................................................... 29 4.3 Test methods ................................................................................ 29 4.3.1 Visual inspections .................................................................. 30 4.3.2 Destructive testing ................................................................. 32 4.3.3 Dye penetration test ............................................................... 33 4.3.4 Ultrasound .............................................................................. 34 5. Atlas Copco solution .......................................................................... 35 Pocket guide on hem flange bonding 3 1. Introduction to adhesive bonding For almost every manufactured product on the market today, parts have to be assembled and attached to each other. Manufacturers increasingly require higher efficiency, speed, and accuracy from the joining technologies they use. In addition, demand is continually growing for new methods and materials to both reduce weight and fuel consumption and increase product performance. Adhesive bonding is one of the few joining technologies that can fulfill these requirements. Bonding is a process designed to join two materials of similar or different characteristics using an adhesive material. bonding sealing insulating Sealing is a method for closing peripheral areas to prevent gases or liquids penetrating or escaping, i.e. to avoid leakages. bonding sealing insulating Insulating is a method of preventing or reducing the passage or transfer of heat, electricity, or sound. bonding sealing insulating 4 Pocket guide on hem flange bonding 1.1 Body in white production In the body shop (body in white; BIW) sheet metal is joined to form the chassis of a car. The applied adhesive fulfills several functions, such as increasing crash performance, vehicle stiffness, and resistance against corrosion in hem flange areas. Depending on the joining task, there are several methods available to fulfill the corresponding requirements. We typically find three application areas linked to BIW production: 1. Structural bonding 2. Stiffening and anti-flutter 3. Hem flange bonding Sometimes there is also a need to seal joints in the area of the filler cap or the headlights. Where do we find the hem flange process? The production of the closure parts (doors, engine hood, trunk, fenders) is a separate process step within the BIW production line. Here we find the hem flange process as one of the most demanding joining processes within the BIW manufacturing. Pocket guide on hem flange bonding 5 1.2 Adhesive bonding in BIW production These days implementing lightweight materials is an overriding consideration in vehicle construction, but car manufacturers still are on the lookout for methods to improve stiffness, increase crash durability and reduce metal/material fatigue, all the while contributing to weight reduction. Structural bonding Typically, the high-strength, high-viscosity adhesives which are used to join metal sheets are dispensed as a continuous bead or as a stitched bead. “Stitching” or “constricting” beads is a popular method to reduce the environmental impact (such as welding fumes) of spot welding in combination with adhesives. Stiffening and Anti-Flutter Doors, hoods and bonnets often consist of several parts which require flexible connections. They reduce vulnerability to vibrations and noise during driving. The dispensed beads or dots act both as dampeners and spacers between the inner and outer parts. Hem flange bonding The hemmed seams of hang-on parts like doors have to be precisely filled with high-strength adhesive for crash- safety reasons. Additionally, the filling avoids corrosion. Applying a continuous bead is the favored way for many manufacturers today. A method to improve production quality in hem flange bonding is the Swirl technology. 6 Pocket guide on hem flange bonding 1.3 What is a hem flange? The hem flange describes a mechanical joint design which is used for joining inner and outer closure panels, as in metal doors, hoods, bonnets, or liftgates. To increase crash resistance the gap between the hemmed panels is filled with high-strength adhesive which also prevents corrosion. 1 Nesting: The inner panel will be nested with the outer panel where adhesive has already been applied. Plane-parallel nesting brings the optimal result. 2 Hemming: Mechanical forming via different methods which gives the hem its final shape. 3 Final hem: An optimal filled hem excluding air prevents corrosion needs period for consistency. Pocket guide on hem flange bonding 7 1.4 Why do you need to hem and bond a flange? Hemming parts hides the cutting edges of the metal sheets. This helps both to prevent injuries and to improve the external appearance. While the adhesive between the inner and outer sheet fulfills a structural function, it also helps to prevent corrosion. Mechanical joining techniques as well as spot-welding are not suitable for the hem flange production, since they would leave unwanted visible spots on the joints. This is why adhesive bonding plays an extremely important role in the BIW production of all closure parts. 8 Pocket guide on hem flange bonding 1.5 Challenges in the industry Hang-on partsB need a high degree of quality and therefore require an optimal adhesive application. Hem flange bonding is one of the most challenging process D stepsC in the BIW production process. A Did you know? Hem flange joints are one of the most demanding joining processes in automotive BIW production. Automotive manufacturers are facing challenges such as: • Optimal filling inside the hemmed area • Avoiding air ducts which lead to corrosion • Complex geometries of the components • Clean application patterns with sharp outer edges Insufficient filling Material squeeze out Corroded door flange Pocket guide on hem flange bonding 9 2. Influence factors The quality of the final hem flange is influenced by many different factors. The graph shows a range of factors involving the inner and outer sheet, the application pattern, the adhesive material, the nesting and hemming process and process steps in paint shop applications. Inner sheet Outer sheet Application Nesting Hemming • Thickness • Volume • Component • Hemming method • Geometry • Positioning feed • Force applied to • Oiling status • Bead width • Movements component • Punching edge • Filling rate • End position • Plasticity behavior • Distance to of the material component • Unequal cross- • Accuracy of robot section shapes • System settings • Handling stiffness Material transportation • Viscosity • Temperature Paint shop • Aging • E-coating • Air bubbles a oven • Dirt contamination • Filling material • Seam sealing • Gap size curing in oven 10 Pocket guide on hem flange bonding Inner and outer sheet: Tolerances of thickness or geometry A rule of thumb says that a steel sheet coming from the stamping and cutting should have a maximum oiling of 5 g/m² process can significantly impact hem to ensure optimal adhesion. Aluminum flange quality. The oiling status of the metal sheets should be cleaned to achieve a sheets directly influences the adhesion of maximum oiling of 0.5 g/m². the adhesive applied on the metal sheet. Application: The adhesive
Details
-
File Typepdf
-
Upload Time-
-
Content LanguagesEnglish
-
Upload UserAnonymous/Not logged-in
-
File Pages40 Page
-
File Size-