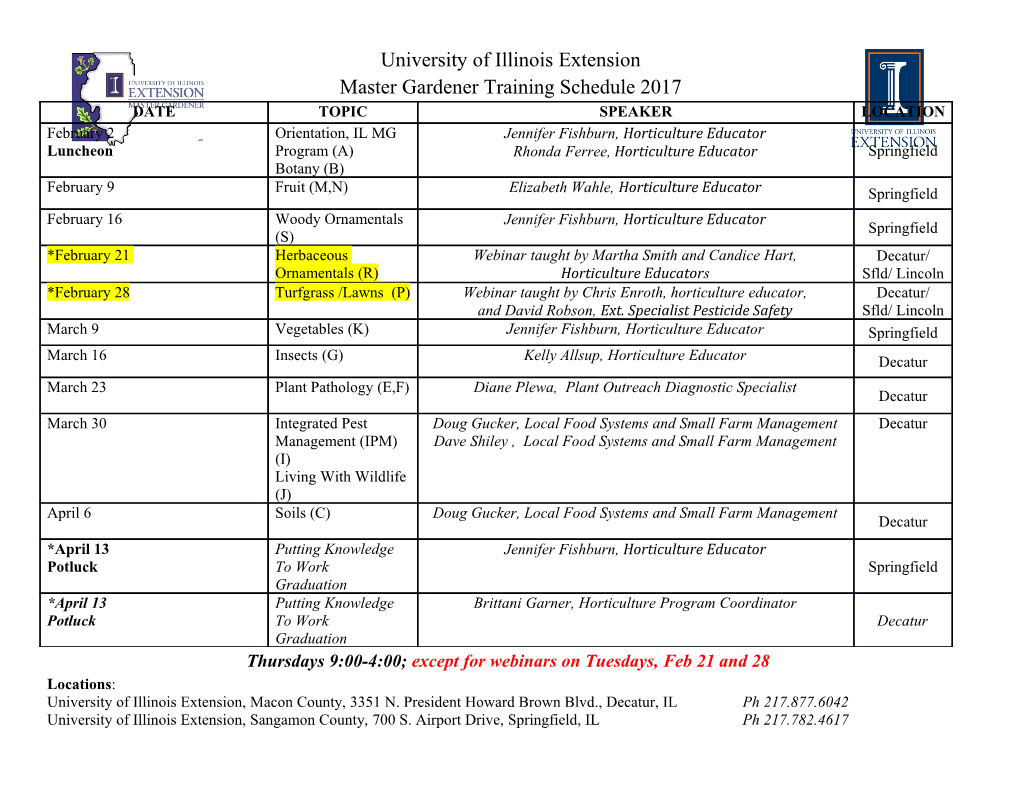
The Design of a Micro-turbogenerator by Andrew Phillip Camacho Department of Mechanical Engineering and Materials Science Duke University Date: Approved: Jonathan Protz, Supervisor Devendra Garg Rhett George Thesis submitted in partial fulfillment of the requirements for the degree of Master of Science in the Department of Mechanical Engineering and Materials Science in the Graduate School of Duke University 2011 Abstract (micro-turbogenerator design) The Design of a Micro-turbogenerator by Andrew Phillip Camacho Department of Mechanical Engineering and Materials Science Duke University Date: Approved: Jonathan Protz, Supervisor Devendra Garg Rhett George An abstract of a thesis submitted in partial fulfillment of the requirements for the degree of Master of Science in the Department of Mechanical Engineering and Materials Science in the Graduate School of Duke University 2011 Copyright c 2011 by Andrew Phillip Camacho All rights reserved except the rights granted by the Creative Commons Attribution-Noncommercial Licence Abstract The basic scaling laws that govern both turbomachinery and permanent magnet gen- erator power density are presented. It is shown for turbomachinery, that the power density scales indirectly proportional with the characteristic length of the system. For permanent magnet generators, power density is shown to be scale independent at a constant current density, but to scale favorably in actuality as a result of the scaling laws of heat dissipation. The challenges that have affected micro-turbogenerators in the past are presented. Two of the most important challenges are the efficiency of micro-turbomachinery and the power transfer capabilities of micro-generators. The basic operating principles of turbomachinery are developed with emphasis on the different mechanisms of energy transfer and how the ratio of these mechanisms in a turbine design relates to efficiency. Loss models are developed to quantify entropy creation from tip leakage, trailing edge mixing, and viscous boundary layers over the surface of the blades. The total entropy creation is related to lost work and turbine efficiency. An analysis is done to show turbine efficiency and power density as a function of system parameters such as stage count, RPM, reaction, and size. The practice of multi-staging is shown to not be as beneficial at small scales as it is for large scales. Single stage reaction turbines display the best efficiency and power density, but require much higher angular velocities. It is also shown that for any configuration, there exists a peak power density as a result of competing effects iv between the scaling laws and viscous losses at small sizes. The operating principles of generators and power electronics are presented as are the scaling laws for both permanent magnet generators and electro-magnetic induction generators. This analysis shows that permanent magnet generators should have higher power densities at small sizes. The basic concepts of permanent magnet operation and magnetic circuits are explained, allowing the estimation of system voltage as a function of design parameters. The relationship between generator voltage, internal resistance, and load power is determined. Models are presented for planar micro-generators to determine output voltage, internal resistance, electrical losses, and electromagnetic losses as a function of geom- etry and key design parameters. A 3 phase multi-layer permanent magnet generator operating at 175,000 RPM with an outer diameter of 1 cm is then designed. The device is shown to convert 10 W of input shaft power into DC electric power at an efficiency of 64%. A second device is designed using improved geometries and system parameters and operates at an efficiency of 93%. Lastly, an ejector driven turbogenerator is designed, built, and tested. A thermo- dynamic cycle for the system is presented in order to estimate system efficiency as a function of design parameters. The turbo-generator was run at 27,360 RPM and demonstrated a DC power output of 7.5 mW. v Contents Abstract iv List of Tables ix List of Figuresx Acknowledgements xv 1 Introduction1 1.1 Background and Motivation.......................1 1.1.1 Concept..............................1 1.1.2 Challenges.............................8 1.1.3 Review of Previous Work..................... 22 1.2 Research Objectives, Goals, and Design Overview........... 31 2 Micro-turbine Design and Performance 33 2.1 Concepts of Turbomachinery....................... 33 2.1.1 Operating Concepts........................ 33 2.1.2 Conservation Laws and Governing Equations.......... 37 2.1.3 Turbine Reaction, Flow Type, and Stage Count........ 39 2.2 Micro-turbine Design........................... 42 2.2.1 Turbine Efficiency and Loss Accounting............. 42 2.2.2 Characterization of the Flow................... 47 2.2.3 Boundary Layer Losses...................... 48 vi 2.2.4 Trailing Edge Losses....................... 51 2.2.5 Tip Clearance Losses....................... 54 2.2.6 Scaling Effects on the Efficiency of Gas Turbines........ 57 2.3 Conclusion................................. 66 3 Permanent Magnet Micro-generator Design and Performance 68 3.1 Concepts of Permanent Magnet Generators............... 68 3.1.1 Operating Concepts, Scaling Laws, and Generator Selection. 68 3.1.2 Magnetic Circuits and Modeling................. 76 3.1.3 Electric Circuits and Modeling.................. 86 3.1.4 Magnetic Materials and Configuration............. 89 3.2 Device Performance............................ 94 3.2.1 Device Geometry and Parameters................ 94 3.2.2 Flux and Induced Voltage.................... 99 3.2.3 Generator Coil Resistance.................... 102 3.2.4 Maximum Power Transfer Capabilities............. 104 3.2.5 Loss Mechanisms......................... 105 3.2.6 Power Output, Efficiency, and Layer Count........... 110 3.3 Conclusion................................. 111 4 Experimental Results of an Ejector Driven Micro-turbogenerator 113 4.1 Introduction................................ 113 4.2 Thermodynamic Cycle.......................... 114 4.3 Experiment and Results......................... 116 4.4 Conclusion................................. 119 5 Conclusion and Future Work 121 5.1 Summary and Conclusions........................ 121 vii 5.2 Future Work................................ 124 Bibliography 125 viii List of Tables 3.1 Voltage results.............................. 101 3.2 Maximum power dissipation....................... 105 3.3 Eddy current losses............................ 107 3.4 Ohmic losses in the stator windings and power electronics....... 109 3.5 Load power and efficiency as a function of layer count......... 110 4.1 Efficiency approximations........................ 117 4.2 Experimental results........................... 118 ix List of Figures 1.1 A micro-turbine engine operating a Brayton cycle...........3 1.2 Scaling laws for heat dissipation in a conductor............6 1.3 Energy density of micro-turbogenerators relative to Li-ion batteries.7 1.4 TS diagrams for a Brayton cycle.....................8 1.5 Gas flow path for a micro-turbine.................... 10 1.6 Velocity triangles of a turbine stage................... 11 1.7 Thermal resistance structures...................... 12 1.8 A magnetizing head............................ 13 1.9 Leakage flux permeating incorrect sectors during magnetization... 14 1.10 Trapezoidal magnetization profile of an annular permanent magnet. 14 1.11 Discrete magnet pieces arranged peripherally around the generator rotor 15 1.12 A silicon frame for discrete peripherally arranged magnet pieces... 15 1.13 Coil winding patterns for 2D micro-generators............. 17 1.14 Silicon laminations within the stator back iron to reduce eddy currents 18 1.15 Temperature effects on magnetization.................. 18 1.16 A single-zone combustor schematic................... 19 1.17 Schematic of a dual zone combustor................... 21 1.18 A catalytic micro-combustor....................... 21 1.19 A 10 mm axial impulse turbine..................... 22 1.20 SEM photograph of the MEMS turbocharger.............. 23 x 1.21 Cross sectional view of the turbomachinery............... 23 1.22 A bird's eye SEM photograph of the MEMS turbine.......... 23 1.23 A split SEM view showing the concentric turbine stages........ 24 1.24 A fully packaged micro-combustor.................... 25 1.25 Schematic of a dual zone combustor................... 25 1.26 A catalytic combustor schematic..................... 26 1.27 Schematic of a ball bearing supported turbo-generator........ 26 1.28 Original and optimized winding patterns................ 27 1.29 A comparison between SmCo and NdFeB generators as a function of temperature................................ 27 1.30 Power density and ejector efficiency as a function of the nozzle throat diameter.................................. 28 1.31 Suction draft performance versus entrainment ratio.......... 29 1.32 A schematic of a MEMS power plant utilizing a Rankine cycle.... 29 1.33 Cross sectional schematic of the fully integrated permanent magnet turbogenerator.............................. 30 1.34 The original turbogenerator and power electronics........... 31 2.1 A control volume for a general turbo-machine............. 33 2.2 Velocity triangles for the exit flow from a rotor blade......... 34 2.3 A fluid element in a centrifugal field................... 36 2.4 Velocity triangles for an impulse turbine rotor blade row....... 39 2.5 Velocity triangles for a reaction turbine rotor blade row........ 40 2.6 Multistage
Details
-
File Typepdf
-
Upload Time-
-
Content LanguagesEnglish
-
Upload UserAnonymous/Not logged-in
-
File Pages144 Page
-
File Size-