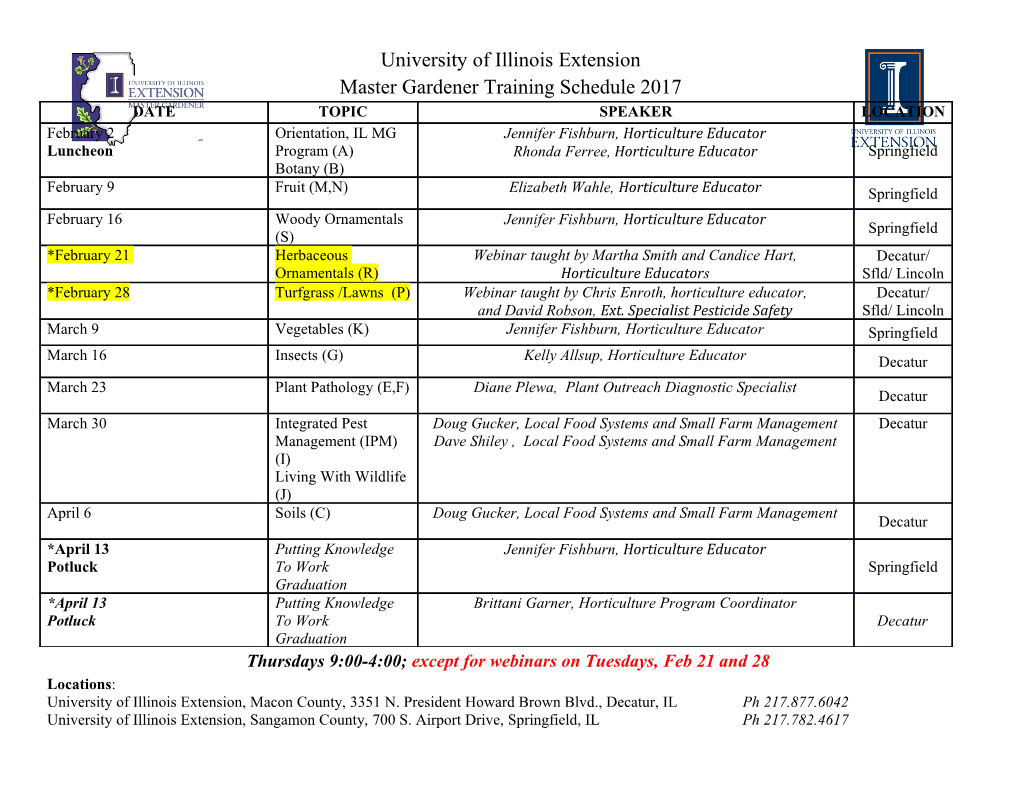
Development of an expert system for cutting-off process selection. CHOW, K. L. Available from the Sheffield Hallam University Research Archive (SHURA) at: http://shura.shu.ac.uk/19464/ A Sheffield Hallam University thesis This thesis is protected by copyright which belongs to the author. The content must not be changed in any way or sold commercially in any format or medium without the formal permission of the author. When referring to this work, full bibliographic details including the author, title, awarding institution and date of the thesis must be given. Please visit http://shura.shu.ac.uk/19464/ and http://shura.shu.ac.uk/information.html for further details about copyright and re-use permissions. 101 536 557 4 36 ^ 3 0 2 . Sheffield Hallam University REFERENCE ONLY ProQuest Number: 10694345 All rights reserved INFORMATION TO ALL USERS The quality of this reproduction is dependent upon the quality of the copy submitted. In the unlikely event that the author did not send a com plete manuscript and there are missing pages, these will be noted. Also, if material had to be removed, a note will indicate the deletion. uest ProQuest 10694345 Published by ProQuest LLC(2017). Copyright of the Dissertation is held by the Author. All rights reserved. This work is protected against unauthorized copying under Title 17, United States C ode Microform Edition © ProQuest LLC. ProQuest LLC. 789 East Eisenhower Parkway P.O. Box 1346 Ann Arbor, Ml 48106- 1346 Development of an Expert System for Cutting-off Process Selection K. L. Chow A thesis submitted in partial fulfilment of the requirements of Sheffield Hallam University for the Degree of Master of Philosophy November 1995 CONTENTS ITEMS PAGE Abstract i Acknowledgements » List of figures iii List of tables iv Chapter 1 Introduction 1 1.1 Background 1 1.2 Aims and objectives 1 1.3 Cutting-off process 2 1.4 Problems in selecting cutting-off process 4 Chapter 2 Literature Review 7 2.1 Introduction 7 2.2 Cutting-off process selection 7 2.3 Reported uses of expert systems for selection tasks 11 2.4 Reasons for using an expert system in preference to conventional program 14 2.5 Expert system tool selection 17 2.6 Conclusions 19 Chapter 3 Cutting-off process selection: Industrial practice in U.K. 20 3.1 Introduction 20 3.2 Objectives of survey 20 3.3 Survey design 20 3.4 Selection of the survey method 21 3.5 Design of questionnaire 21 3.6 Survey data analysis 24 3.7 Survey results 24 3.7.1 Cutting-off process user company 25 3.7.2 Cutting-off tool manufacturer 33 3.7.3 Cutting-off machine manufacturer 35 3.8 Discussions 36 Chapter 4 Knowledge engineering for cutting-off process selection 39 4.1 Review of knowledge engineering 39 \ 4.2 Knowledge elicitation 40 4.3 Results of the knowledge elicitation 41 4.4 Development of selection methodology 43 4.4.1 Selection methodology 43 Chapter 5 Development of cutting-off process selection expert system 46 5.1 Introduction 46 5.1.1 Identification of problem 46 5.1.2 Task analysis 46 5.1.3 Information processing 46 5.1.4 Prototype development 47 5.1.5 System development and test 47 5.2 The cutting-off process selection system 48 5.2.1 First level: hardness 48 5.2.2 Second level: Material 50 5.2.3 Third level: Tolerance 51 5.2.4 Fourth level: Surface finish 52 5.2.5 Fifth level: Kerf loss 53 5.2.6 Sixth level: Cross section 54 5.3 Cutting parameter selection system 54 5.4 Cost analysis system 57 5.5 Report 57 Chapter 6 System testing 58 6.1 Introduction 58 6.2 Testing procedure 59 6.3 Phase testing 60 6.3.1 Phase 1 60 6.3.1.1 Phase 1 section 1 60 6.3.1.2 Phase 1 section 2 60 6.3.2 Phase 2 test 66 6.3.3 Phase 3 test 67 6.4 Discussion of results 70 6.5 Analysis and correlation 70 6.5.1 Cutting-off process 70 6.5.2 Cutting-off parameter 71 Chapter 7 Discussions and future work 73 Conclusions 75 Future work 78 References 79 Appendices Appendix 1 Sawing process 1 A. 1.1 Power hacksaw 1 A. 1.2 Circular sawing 5 A. 1.3 Friction cutting 9 A. 1.4 Abrasive disc cutting 11 A. 1.5 Band sawing 13 A. 1.6 Oxyfuel gas cutting 18 A. 1.7 Arc cutting 19 A. 1.8 Laser beam cutting 20 A. 1.9 Wateijet cutting 21 Appendix 2 Expert System Building Tools 22 A.2.1 ESE - Expert System Environment 22 A.2.2 Knowledge Tool (KT) 22 A.2.3 Adviser (ICL) 23 A.2.4 Knowledge Based Management System (KBMS) 23 A.2.5 Application Expert (AE) 24 A.2.6 Knowledge Engineering System (KES) 24 A.2.7 XI Plus 25 A.2.8 KAS 25 A.2.9 EXPERT 27 A.2.10 AGE 28 A.2.11 EMYCIN 29 Appendix 3 Mail Questionnaires 30 A.3.1 Process user 30 A.3.2 Cutting-off machine tool manufacturer 39 A. 3.3 Cutting-off machine manufacturer 41 Appendix 4 Expert System Verification 43 Appendix 5 Testing Examples 45 A.5.1 Phase 2 test examples 45 A.5.2 Phase 3 tests - Industrial testing 50 Appendix 6 Manufacturing Cost Calculations 53 Abstract The manufacturing engineer is faced with many different processes and a wide variety of alternative combinations of parts and cutting-off tools. The problem is therefore to select the optional and most economical combinations of processes and parameters for cutting-off a given product. To assist in this problem, each cutting-off tool or machine manufacturer and supplier recommends cutting conditions for their products which are neither consistent nor have a scientific base. As with other machining technologies, the cutting-off process domain has an abundance of data, but veiy little documented knowledge. It was proposed to undertake an investigation into the possibility of using a knowledge-based system for the selection of cutting-off processes, cutting-tools and the associated parameters. This project uses a survey to investigate the U.K. industry practice in the selecting of cutting-off process and machines used in their business and the nature of their business. The survey method, design and survey questionnaires as well as the findings are also reported. From the survey finding and interviews with experts, a prototype system structure has been developed. This system is similar to an expert's thinking in solving a problem. The structure of the system and how it works is also revealed in this report. The steps in building an expert system are discussed in this report, it states what is knowledge acquisition and the problems and methods used in knowledge acquisition. After the system was built, it was subjected to a through test programme. The testing procedure and industry validation process are discussed in the report. The testing results are analysed to show that the use of using an expert system in the selection of cutting-off process is feasible. Acknowledgements The author would like to express his thanks to Mr. G. Cockerham and Mrs. J. Grove for their advice, guidance and assistance on many occasions during the time spent on the research programme. He would also like to offer thanks to Dr. D. Gillibrand and Dr. T. Perera for their advice in the writing up and final auditing of the thesis. Thanks to the members of the academic and technical staff who have made contributions to the success of the research programme. Their support of this project is very much appreciated and in particular the help given to maintain contact with the supervisor following his move away from Sheffield. Finally, the author would like to express his gratitude to his parents and other members of his family for their continuing support and encouragement during the duration of the research project. List of figures Page Figure 1.1 Cutting action 3 Figure 2.1 Hardness of various tool materials as a function of temperature 8 Figure 2.2 Different cutting-off process tolerance range 8 Figure 2.3 Different cutting-off process surface finish ranges obtainable 9 Figure 2.4 Kerf loss of different cutting-off process 10 Figure 3.1 Cutting-off process user questionnaire layout 21 Figure 3.2 Cutting-off tool manufacturer questionnaire layout 22 Figure 3.3 Cutting-off machine manufacturer questionnaire layout 22 Figure 3.4 Number of employees employed in the cutting-off process user companies 25 Figure 3.5 Industry sector of the survey respondents 26 Figure 3.6 Production type of survey respondents 26 Figure 3.7 Personal responsible for selecting cutting-off processes 27 Figure 3.8 Personal responsible for selecting cutting-off machines 27 Figure 3.9 Personal responsible for selecting cutting-off tools 28 Figure 3.10 Personal responsible for selecting cutting-off parameters 28 Figure 3.11 Resources used to select cutting-off machine 29 Figure 3.12 Resources used to select cutting-off tool 29 Figure 3.13 Types of cutting-off machine tools used by the respondents 3 0 Figure 3.14 Cutting-off process employed by users 30 Figure 3.15 Cutting-off tools used by survey respondents 31 Figure 3.16 Cutting-off tool materials used by users 31 Figure 3.17 Types of materials cut by survey respondents 3 2 Figure 3.18 Cutting-off machine operator skill levels 32 Figure 3.19 Number of employees employed in the cutting-off tool manufacturer companies 33 Figure 3.20 Types of cutting-off tool manufactured by cutting-off tool companies 34 Figure 3.21 Cutting tool materials produced by cutting-off tool companies 34 Figure 3.22 Number of employees employed in the cutting-off machine manufacturer companies 35 Figure 3.23 Types of cutting-off machine produced by machine manufacturers 36 Figure 4.1 The first expert's selection procedure 42 Figure 4.2 The second expert's selection procedure 42 Figure 4.3 Cutting-off process selection system 45 Figure 5.1 Prototype system flow diagram 50 Figure 5.2 Cutting-off process parameter selection system
Details
-
File Typepdf
-
Upload Time-
-
Content LanguagesEnglish
-
Upload UserAnonymous/Not logged-in
-
File Pages148 Page
-
File Size-