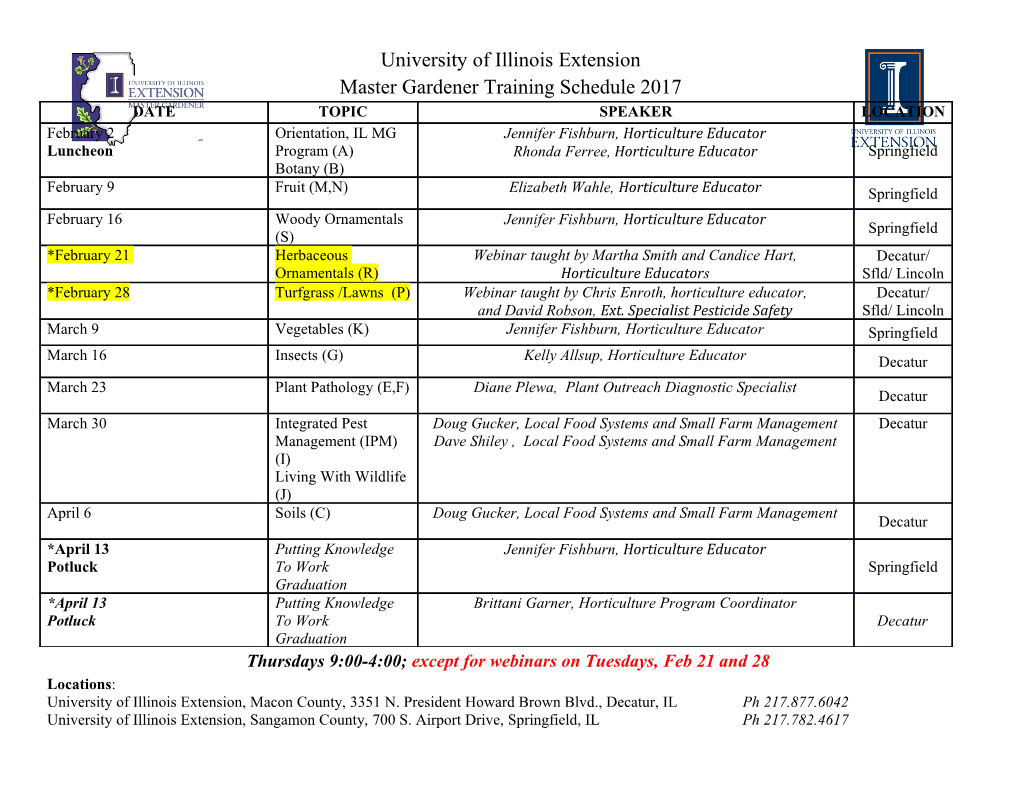
; A Study ON THE Effects OF Sequential TURBOCHARGED Diesel Engines Michael AleXANDER LOONSTIJN A Study on the Effects of Sequential Turbocharged Diesel Engines by Michael Alexander Loonstijn to obtain the degree of Master of Science - Mechanical Engineering at the Delft University of Technology, to be defended publicly on Tuesday July 12, 2016 at 14:00. Student number: 1334298 Project duration: December 1, 2015 – July 12, 2016 Thesis committee: Prof. Ir. J.J. Hopman, TU Delft, committee chair Rear-Admiral(ME)ret. Ir. K. Visser, TU Delft, supervisor Ir. M. de Boer, DSNS, supervisor Prof. Dr. Ir. S. Klein, TU Delft This thesis is confidential and cannot be made public until 12-July-2021. An electronic version of this thesis is available at http://repository.tudelft.nl/. Abstract Sequential turbocharging is a technique where multiple turbochargers are connected to an engine. These turbochargers are switched in sequentially. The manufacturers of engines with this system claim that the part-load and transient performance is better in comparison to engines with a single turbocharger. These claims and other effects in these engines are not well documented in scientific literature. The motivation for this research assignment is the application of the Pielstick PA6B V20 STC on board of the Indonesian navy SIGMA corvettes. The sequentially turbocharged engines have been selected for this design, based on the operating envelope of the engine. At low speed, the sequentially turbocharged engines are able to deliver more torque than a normal turbocharged Diesel engine. Based on the operating envelope, the sequentially turbocharged Diesel engine is able to deliver similar benefits that are normally present in gas turbine and electric motor propulsion systems; high torque at low speed. However, DSNS prefers the use of Diesel engines for their robustness and available maintenance support. The design decision for a sequentially turbocharged Diesel engine during transient and low load operation is evaluated in this report. The TU Delft Diesel B model has been adapted to model the sequential turbocharging strategy. This has resulted in two different models, each with their own benefits and drawbacks. The first model is the Simple STC model; this model gets its name from the simple implementation in Simulink. It is able to reproduce the trends of a sequentially turbocharged engine. The Simple STC model is of the same complexity as the TU Delft Diesel B model, both in application and in computational load. The drawback of this model is that it does not correctly model the transition when the sequential switching occurs, but this error is only present for a few seconds. The Full STC model also gets its name from the implementation in Simulink; in this model the full gas exchange of the sequential turbochargers is modeled. This model is a significantly more complex model than the Simple STC model, both in application as well as in computational load. However, it does provide the possibility to model each turbocharger separately and as a result the transient switching effect is modeled more accurately. Both models have been thoroughly tested in a test-bench environment, both for steady state and transient analysis. The results have proven that the characteristics of a sequentially turbocharged engine are modeled correctly. It was proven that for the sequentially turbocharged engine, there are significant benefits for having two different turbocharger modes. Under steady state conditions, the mass supplied to the engine is of better quality in terms of mass flow and pressure for each of the different turbocharging modes in their respective working regions. This increased quality of air supply leads to lower temperatures, lower fuel consumption and higher available power for the same power rating. The Simple STC model has been applied in a model of the complete SIGMA corvette to simulate acceleration tests and to test new control strategies. This has provided insight into the limits of the engine-propeller-hull interaction during acceleration. The propeller and ships ability to absorb power are limiting the engine’s available power when the results are analyzed in the operational envelope. It has been proven that the engine needs to ramp-up in speed almost instantaneously to utilize the full available power. The engine is not able to ramp-up that fast due to the dynamic interaction of the engine and turbocharger. When accelerating the engine it was found that at higher acceleration rates the turbocharger does not spin up fast enough and as a result the air excess ratio decreases during acceleration; this phenomenon is also known as turbo-lag. The maximum acceleration limit is determined to be 12.8 [rpm/s] which results in a minimum air excess ratio of 1.5. An alternative control strategy based on a minimum air excess ratio has been analyzed but this method did not result in a good control alternative. It did however give some insight into the maximum possible acceler- ation limits and provides a basis for future research into alternative control strategies. iii Nomenclature Table 1: A list of all the abbreviations used in this report. Abbreviation Full name AC Air Cover AF Air Filter BDC Bottom Dead Center BMEP Brake Mean Effective Pressure CAC Charge Air Cooler COM Compressor CYL Cylinder DE Diesel Engine DSNS Damen Schelde Naval Shipbuilding EC Exhaust Close ENG Engine EO Exhaust Open GB Gearbox HE Heat Exchanger HTHE High Temperature Heat Exchanger IC Inlet Close IO Inlet Open IR Inlet Receiver IV Inlet Volume LMTD Log Mean Temperature Difference LTHE Low Temperature Heat Exchanger NRMSE Normalized Root Mean Square Error NTU Number of Transfer Units OR Outlet Receiver PROP Propeller RMSE Root Mean Square Error SFC Specific Fuel Consumption SIGMA Ship Integrated Geometrical Modularity Approach SIL Silencer STC Sequential Turbocharging SV Silencer Volume TC Turbocharger TDC Top Dead Center TUR Turbine v vi 0. Nomenclature Table 2: A list of all the symbols used in this report. Symbol Unit Description A [m2] Area cp [J/kg/K ] Specific heat, at constant pressure cv [J/kg/K ] Specific heat, at constant volume D [m] Diameter h [W /m2/K ] Convective heat transfer coefficient I [kg/m2] Inertia k [W /m/K ] Thermal conductivity L [m] Length M [Nm] Torque m [kg] Mass m˙ [kg/s] Mass flow N [r pm] Rotational speed n [hz] Rotational speed P [W ] Power Q [W ] Heat R [J/kg/K ] Gas constant r [m] Radius T [K ] Temperature V [m3] Volume W [W ] Work X [0 1] Fuel rack ¡ x [0 1] Air fraction ¡ · [ ] Specific heat ratio: c /c ¡ p v ¹ [kg/s/m] Dynamic viscosity ! [r ad/s] Rotational speed !˙ [r ad/s2] Rotational acceleration ½ [kg/m3] Density List of Figures 1.1 Alfred Buechi, inventor of the turbocharger (source: ABB Turbo Systems LTD. Baden, Switzer- land).......................................................1 1.2 The current Schwitzer-BorgWarner model S3 on the left has a slightly higher airflow range than the older Schwitzer model made in the 60’s for Cummins Engine Company. While the intended applications are different, it’s easy to see the dramatic design differences that have come about from computer-aided designs, improved materials and manufacturing processes (source: Diesel Injection Service Company, Inc.)......................................2 1.3 A diagram of the gas exchange in an STC engine (source: dieselnet.com)...............3 1.4 Sigma 9113-class corvette, KRI Diponegoro (source: DSNS).......................4 2.1 a) compressor matched to high engine load. b) compressor matched to low engine load (source of map image: MAN TC NA34 project guide)...............................8 2.2 compressor map of the permanent turbocharger in a sequential turbocharged engine with 2 equal turbochargers (source of map image: MAN TC NA34 project guide)..............9 2.3 A variable geometry turbine at high and low engine RPM. (source: Source: www.import-car.com) 10 2.4 Schematic of the location of a waste gate in an internal combustion engine(source: www.dieselnet.com). 10 2.5 A mechanical turbo compounding system (source: Boretti [3])..................... 11 2.6 A electric turbo compounding system (source: www.scania.com/global/engines)......... 12 2.7 A hybrid turbocharger for marine application (source: www.mhi-global.com)............ 12 2.8 Frequency converters used by Ono et al. (source: Ono et al. [13])................... 13 3.1 pressure in cylinder of a diesel engine (source: Schulten [16])..................... 17 3.2 volume and resistor element with their respective in- and outputs (source: Schulten [16])..... 18 3.3 volume and resistor network of a turbocharged Diesel engine (source: Schulten[16])........ 18 4.1 A schematic overview of the low and high temperature dual-pass heat exchanger.......... 22 4.2 A thermal network for the heat transfer of fluids through a wall.................... 23 4.3 Charged air cooler outlet temperature, observed and simulated results for constant and cor- rected water inlet temperature........................................ 23 4.4 Effectiveness – NTU curves for a cross flow heat exchanger (source: Glasgow College of Nautical Studies)..................................................... 26 4.5 Comparison of proposed equation to the graphical data (source of underlying image: Glasgow College of Nautical Studies).......................................... 26 4.6 An overview of the air cooler sub-model................................. 27 4.7 Results of the alternative charged air cooler model plotted with the observed data set....... 27 4.8 Results of all model evaluations....................................... 29 5.1 A detail of the sequential turbocharger implementation in the Diesel B model........... 33 5.2 Operating map of the Pielstick PA6B V20 engine on board the SIGMA corvettes (source: DSNS). 33 5.3 Top level of the turbocharger control sub system............................. 34 5.4 Subsystem for switching from single to dual turbocharger operation, logical AND operator.... 34 5.5 Subsystem for switching from dual to single turbocharger operation, logical OR operator..... 34 5.6 Steady state turbocharger speed with switching for both increasing and decreasing load....
Details
-
File Typepdf
-
Upload Time-
-
Content LanguagesEnglish
-
Upload UserAnonymous/Not logged-in
-
File Pages183 Page
-
File Size-