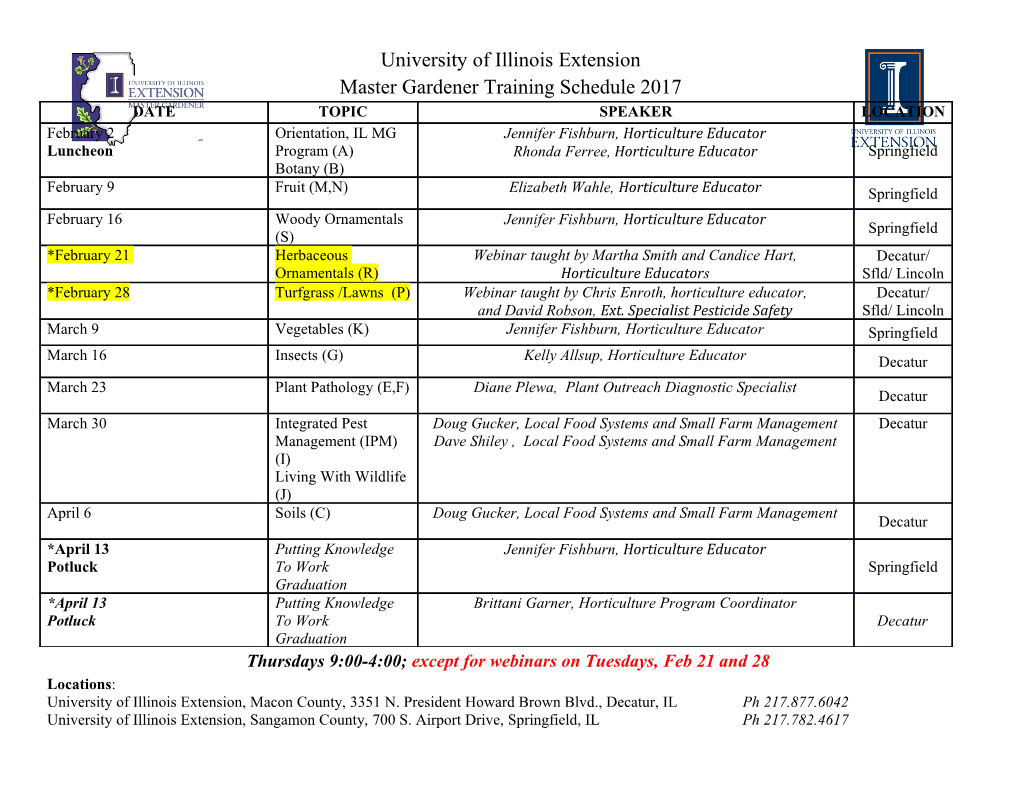
Thin Film | Mass producing high-efficiency SHJ cells/modules Heterojunction technology: The path to high efficiency in mass production Igor Shakhray, Alexey Abramov, Sergey Abolmasov, Ekaterina Terukova & Dmitriy Andronikov, Hevel Group, Moscow, Russia Abstract Heterojunction technology is currently a hot topic actively discussed to 160MWp during the first phase of the project, in the silicon PV community. Hevel recently became one of the first with an average SHJ cell efficiency of 21% being companies to adopt its old micromorph module line for manufacturing demonstrated in mass production. Meyer Burger’s high-efficiency silicon heterojunction (SHJ) solar cells and modules. SmartWire Cell Technology (SWCT) was chosen On the basis of Hevel’s own experience, this paper looks at all the for interconnection in SHJ module assembly. production steps involved, from wafer texturing through to final module During the second phase of the project (June assembly. 2017–May 2019), the production capacity of Hevel’s production line was increased to 260MWp, with Introduction an average cell efficiency of 22.8% obtained in In recent years, many solar cell and module mass production. producers in the silicon PV industry have been forced to adapt their existing production lines to Technology development new technologies in order to be able to deliver As can be seen in Fig. 1, SHJ cells have very highly efficient and low-cost modules to the simple structure and it takes only six process market. The most popular transfer has been steps to fabricate them. Typically, the SHJ cell is from Al back-surface field (Al-BSF) to passivated composed of an n-type c-Si wafer coated on both emitter and rear cell (PERC) technology, since sides with thin intrinsic and doped a-Si:H layers. the latter is compatible with existing production The ultrathin intrinsic a-Si:H layers, with typical lines used for standard technology. Nevertheless, thicknesses of a few nanometres, have a crucial excellent crystalline silicon (c-Si) surface effect on the performance of SHJ cells. The aim of passivation by hydrogenated amorphous silicon these layers is to suppress surface recombination (a-Si:H) offers the possibility to employ the most by chemical passivation of dangling bonds on expensive part of silicon thin-film production the c-Si wafer surface with the formation of lines, namely plasma-enhanced chemical Si-Si and Si-H bonds, as well as to prevent defect vapour deposition (PECVD) systems, for silicon generation by dopant atoms during the deposition heterojunction (SHJ) technology, as recently of doped layers. The doped layers are fully covered realized by Hevel LLC. with indium tin oxide (ITO) films, followed by The simple structure of SHJ solar cells, in screen-printing of contact metal grids for current combination with their high efficiency and collection using a low-temperature conductive low-temperature processing, makes them very (LTC) Ag paste. To enhance the properties of the attractive to the PV industry. This is the reason ITO layers and contact grids, low-temperature why Hevel has decided to start a project on annealing is required. modernizing and transforming its micromorph module production line, which includes a large Wafers for SHJ cells number of PECVD systems (KAI-MT PECVD As in the case of all high-performance c-Si solar reactors from TEL Solar), into a new SHJ line. cells, wafer quality is key to achieving high- The successful conversion of Hevel’s production efficiency SHJ cells. Although record efficiency line for the manufacture of SHJ solar cells and values reported in the literature have been modules was completed in April 2017 using an obtained using high-purity float zone (FZ) c-Si in-house SHJ solar cell technology developed by wafers, the development of the Czochralski its R&D Center for Thin Film Technologies (TFTE process and the continuous improvement of – an R&D unit of Hevel). polysilicon quality have allowed the impurity The annual production capacity was increased concentrations in CZ wafers to be reduced while from an initial 97MWp (for the micromorph line) keeping production costs reasonable. As a result, the open-circuit voltage (Voc) of SHJ cells has recently reached values as high as 750mV. “The simple structure of SHJ solar cells, in Up to now, only monocrystalline CZ wafers combination with their high efficiency and low- have been used for large-scale manufacturing of SHJ solar cells. The electronic properties of temperature processing, makes them very attractive monocrystalline silicon wafers for high-efficiency to the PV industry.” solar cells are determined by impurities and 52 www.pv-tech.org Thin Film | Mass producing high-efficiency SHJ cells/modules (a) (b) Figure 1. (a) Schematic cross-sectional view of a conventional SHJ solar cell. (b) The main steps of the SHJ cell fabrication process sequence. dopant concentrations. Since the measurement further reductions in SHJ cell thickness are also of these parameters require special techniques possible without significant losses in efficiency, that can hardly be used in the mass production the implementation of thinner wafers in mass process, the minority-carrier lifetime and wafer production is currently limited by handling issues, resistance are usually measured in practice and resulting in excessive wafer breakage rates. constitute the main parameters for determining A slight decrease in I sc here is partially the quality of wafers or ingots. These parameters compensated by the Voc gain, leading to a very usually vary along and across ingots, and their small (<0.1%) efficiency loss when switching profiles depend on the details of the ingot growth to 150µm as-cut wafer thickness in the cell process and post treatment. Consequently, it has production. At the module level, the cell efficiency been proposed to use the measured lifetime/ loss is fully compensated by a 10% decrease in resistance ratio as a cumulative measure of wafer cell-to-module (CTM) ratio. The overall benefit of and heterojunction qualities. Recent studies have switching to 150µm wafers is on average around also shown that for SHJ cells with V oc > 750mV, 1–1.5W per module. passivated wafers with a lifetime-to-resistivity The latest update to wafers was carried out ratio above 4ms/Ωcm must be used. in May 2019. The existing SHJ production line is The most significant advantage of SHJ able to adapt wafers of size 157.35mm × 157.35mm technology in terms of cost reduction is that all (M2+ wafer type). The use of such wafers with process steps are performed at low temperatures an optimized contact grid design leads to a (< 250°C), favouring the use of thin wafers power increase per cell of 0.15W (Fig. 3). Hevel’s for SHJ solar cell production. Recent progress R&D Center is also currently working on further in wafer slicing technology as a result of the developments using M4 and M6 wafers as well as implementation of diamond wire technology full square wafers and wafers with lower oxygen has resulted in the mass production of low- concentration. cost wafers with thicknesses less than 160µm. Wafers with an as-cut thickness of 150µm have recently been successfully implemented in the SHJ production process without module “An enhanced cleaning procedure is necessary for power losses, as illustrated in Fig. 2. Although the production of high-efficiency SHJ cells.” 54 www.pv-tech.org Mass producing high-efficiency SHJ cells/modules | Thin Film Wafer texturing and cleaning residual organic, ionic and metallic contamination As with other c-Si PV technologies, wet chemical (originating from the wet etching/texturing treatment is the first step in the SHJ cell solutions) from c-Si wafer surface. In addition, production sequence. The following steps are heavy deionized (DI) water rinse steps are used usually included: between each chemical treatment. The wet chemical treatment ends with a short HF dip, • Etching of the highly defective surface part of which removes native oxide and passivates the the wafer (surface damage etch – SDE). c-Si surface with hydrogen atoms prior to the a-Si:H PECVD processes. • Forming of the special surface morphology Much effort has been devoted at Hevel to (texture) which reduces light reflection from stabilizing and optimizing the wafer texturing the wafer surface (TEX). and cleaning processes. One of the steps of the optimization was a change to a single-component • Cleaning of the wafer surface to remove organic texturing additive; such an optimization enabled and metal impurities. an increase in batch lifetime and a reduction in the consumption of chemical reagents. While the first two steps based on isotropic (SDE) and anisotropic (TEX) alkali etching Surface passivation and junction formation are similar to those used in other silicon PV High-quality surface passivation is key to technologies, the last step is significantly achieving high values of V oc in high-efficiency different. To obtain high-quality surface silicon-based solar cells. An insertion of thin passivation, the wafer surface should be extra (< 10nm) hydrogenated amorphous silicon (a-Si:H) clean. An enhanced cleaning procedure is layers between the c-Si wafer and the doped a-Si:H therefore necessary for the production of high- layers leads to higher V oc values in comparison efficiency SHJ cells; this includes the removal of to those registered in the case when intrinsic www.vonardenne.biz XEA|nova® L XENIA up to 10000 wafers/h FUTURE-PROOF COATING EQUIPMENT width: up to 3 m MAXIMUM PERFORMANCE FOR MINIMUM CAPEX PER GIGAWATT Are you looking for coating equipment with a low cost of ownership for crystalline or thin-film photovoltaics and for technologies such as HJT, IBC, CIGS or passivated contacts? We can provide you with future-proof technology and system solutions for all scales of production.
Details
-
File Typepdf
-
Upload Time-
-
Content LanguagesEnglish
-
Upload UserAnonymous/Not logged-in
-
File Pages9 Page
-
File Size-