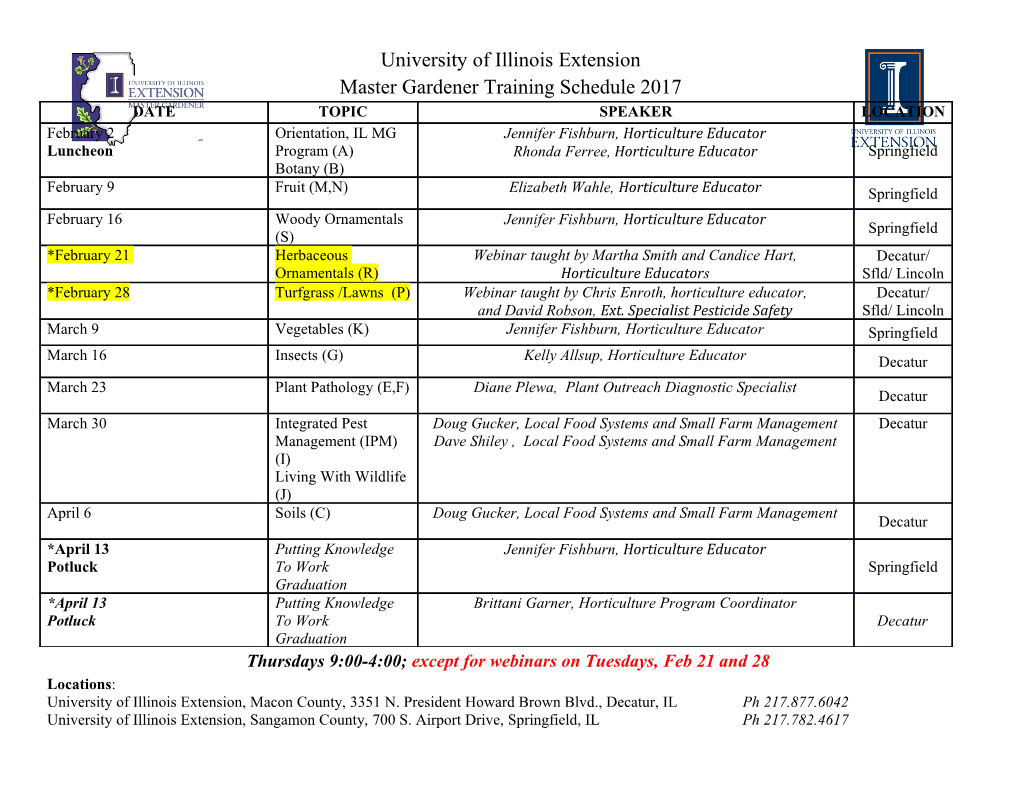
J Wood Sci (2005) 51:33–37 © The Japan Wood Research Society 2005 DOI 10.1007/s10086-003-0610-2 ORIGINAL ARTICLE Atsushi Mori · Kazuhisa Tashiro · Kyoko Makita Masahiro Takatani · Tadashi Okamoto Development of room-temperature curing aqueous emulsion-type acrylic adhesive I: effect of monomer composition on the initial adhesive strength Received: September 10, 2003 / Accepted: December 22, 2003 Abstract For the purpose of developing a new aqueous During the course of our study on the development of emulsion-type adhesive for wood or paper use that does non-formaldehyde-type adhesives for wood or paper use, not release formaldehyde or volatile organic solvents, a we examined an aqueous emulsion of acrylic copolymers honeymoon-type acrylic adhesive was examined. An adhe- with both rapid room-temperature curing properties and a sive system consisting of acrylic monomers copolymerized strong final adhesive strength. According to our strategy, with functional monomers and a cross-linking agent was the adhesive strength immediately after jointing arises selected for the purposes of increasing initial adhesive through the interaction of keto groups, copolymerized in strength and ensuring room-temperature curing. The initial the acrylic copolymer or present in a colloid stabilizer of the adhesive strength increased by the use of cross-linkers such emulsion, with amino groups of cross-linkers, in addition to as dihydrazides and also polymeric methylene diphenyl the tack of some acrylic monomers. Final strength would be diisocyanate (pMDI). Thus an adhesive with reasonable to generated by the full condensation of the keto groups with good initial adhesive strength and room-temperature curing amines. Diacetone acrylamide (DAAM) is selected as the was obtained. The effect of pMDI on the initial adhesive acrylic monomer having a keto group,1 and acetoacetylated strength was not significant and decreased when the amount poly(vinyl alcohol) (AAPVA)2–4 is used as the colloid stabi- of acrylamide in a copolymer was high. lizer for the above purpose (Fig. 1).5 The effects of mono- mer composition and cross-linker on the initial adhesive Key words Acrylic emulsion · Honeymoon · Acetoacetyl · properties are described in this report. PVA · Diacetone acrylamide · Cross-linking Experimental Introduction All chemicals used were commercial reagents and were Demand for safe housing materials of little detriment to the used as received unless specifically described. environment is increasing. In particular, there is a public A typical procedure for preparation of AAPVA was as request for a decrease of formaldehyde emissions from follows: to a 1-liter four-neck flask equipped with a me- housing materials prepared using conventional wood adhe- chanical stirrer, a reflux condenser, a dropping funnel, and a sives, such as urea and phenol resins, and volatile organic nitrogen gas inlet, was added 52.8g of poly(vinyl alcohol) materials, such as xylene and toluene. Solutions for such a (PVA; average degree of polymerization, 400–600; saponifi- problem involve the use of formaldehyde catchers and cation, more than 96mol%), 450ml of dimethyl sulfoxide development of nonformaldehyde adhesives and aqueous (DMSO), and 2.4g of acetic acid as a catalyst. The mixture emulsion-type adhesives. was warmed to 60°C and stirred under nitrogen until com- plete dissolution was attained. Diketene (25.21g, 25mol% to OH groups of PVA) was added dropwise to the solution, A. Mori · K. Tashiro and the mixture was stirred at 500rpm for 1h. Then ethanol Division of Applied Life Chemistry, Graduate School of Agriculture, and hexane were added to the solution, and the insoluble Kinki University, Nara 631-8505, Japan polymeric material generated was collected by filtration. K. Makita · M. Takatani · T. Okamoto (*) The polymeric precipitate was dissolved in distilled water, Department of Agricultural Chemistry, Faculty of Agriculture, Kinki and dialyzed through a dialysis membrane (size 36). University, 3327-204 Nakamachi, Nara 631-8505, Japan Tel. ϩ81-742-43-7383; Fax ϩ81-742-43-1445 AAPVA product was obtained after freeze-drying of the e-mail: [email protected] dialyzate (Fig. 2). The degree of acetoacetylation of 34 Table 1. Monomer composition of base-resin varnisha Symbol Initiator Monomers mixture Additives after Additive after solvent removal dissolution DTBP DTBP MMA MAA EA BA DAAM AM/H2O Water 25% aq NH4OH Water A, D 0.32 0.5 5 20 10 61 20 – 100 16 250 B 0.35 0.5 – 20 – 60 20 – 100 15 250 C 0.35 0.5 – 20 – 60 – 20/20 100 15 450 E 0.35 0.5 – 10 – 60 30 – 100 6 250 Data given as mass in grams DTBP, di-t-butyl peroxide; MMA, methyl methacrylate; MAA, methacrylic acid; EA, ethyl acrylate; BA, n-butyl acrylate; DAAM, diacetone acrylamide; AM, acrylamide; aq, aqueous a 1,2-propanediol methyl ether acetate (60g) was used as a solvent during polymerization and removed afterwards Table 2. Monomer composition of adhesive Ba Adhesive BRV-B BA Styrene DAAM GMA EDMA B-1 25 62.5 10 11 0.25 0.5 B-2b 25 62.5 10 11 0.25 – B-3 25 62.5 10 11 – 0.5 B-4 25 62.5 10 – 0.25 0.5 B-5 25 62.5 – 11 0.25 0.5 B-6 25 – 10 11 0.25 0.5 Data given as mass in grams Fig. 1. Carbonyl substrate. DAAM, diacetone acrylamide; AAPVA, BRV-B, base-resin varnish B; GMA, glycidyl methacrylate; EDMA, acetoacetylated poly(vinyl alcohol) ethylene dimethacrylate a H2O 6g was added with BRV-B b An extra 50g of water was added and the mixture was heated to 140°C under nitrogen. Then a solution of di-t-butyl peroxide (DTBP) in a small portion of PMA was added dropwise to the flask and the nitrogen flow was stopped. A mixture of DTBP, methacrylic acid (MAA), methyl methacrylate (MMA), ethyl acrylate (EA), butyl acrylate (BA), and DAAM was added to the flask over 3h. Stirring was continued for a further 3h after the Fig. 2. Acetoacetylation of poly(vinyl alcohol) (PVA) addition was completed. PMA was removed from the solu- tion under reduced pressure, and the residue was dissolved in dilute aqueous ammonium hydroxide to give base-resin 1 varnish A (BRV-A). AAPVA [D (%)] was determined by H nuclear magnetic AA Preparation of adhesive A: to a reaction flask similar to resonance (NMR) spectroscopy from the percentage ratio that described above was added BRV-A (25g), distilled of peak area due to acetyl protons at 2.2ppm to the area of water (6g), triethylamine (1g), a small amount of 2,2Ј- methylene proton peaks of the PVA main chain appearing azobis(4-methoxy-2,2Ј-dimethylvaleronitrile) (AMVN), in the range of 1.2–2.0ppm multiplied by 1.5. The D of the AA and ammonium peroxodisulfate (APS), at 55°C under sample prepared as above was 10.6%. nitrogen. Then a mixture of BA 62.5g, styrene 10g, DAAM 10g, ethylene glycol dimethacrylate (EDMA) 0.5g, and Synthesis of adhesives glycidyl methacrylate (GMA) 0.25g was added to the flask dropwise and stirring was continued for 5h with occasional The adhesives were prepared by a two-step procedure. additions of AMVN and APS to give adhesive A. The base-resin varnish was prepared first, and then the Other base-resin varnishes and adhesives were prepared adhesive was prepared in the presence of the base-resin similarly according to the monomer compositions in Tables varnish. 1–5. Preparation of base-resin varnish A: to a 500-ml four- Conversions of monomers and solid contents of adhe- neck separable flask equipped with a mechanical stirrer, a sives were determined according to the industrial test reflux condenser, a dropping funnel, and a nitrogen inlet, method JIS K6833 and the results are summarized in Table was added 1,2-propanediol methyl ether acetate (PMA) 6. 35 Table 3. Monomer composition of adhesive Ca Table 6. Solid contents and monomer conversions of adhesives Adhesive BRV-C BA AM Styrene GMA EDMA Adhesive Solid content (g) Conversion (%) C-1 25 62.5 5 10 0.25 0.5 Dried for 24h Theoretical C-2 25 62.5 10 10 0.25 0.5 C-3 25 52.5 20 10 0.25 0.5 A 53.7 55.7 96.5 C-4 25 42.5 30 10 0.25 0.5 B-1 58.8 55.0 106.9 C-5 25 62.5 5 – – – B-2 44.4 43.1 103.2 C-6 25 62.5 10 – – – B-3 56.2 55.0 102.2 C-7 25 52.5 20 – – – B-4 52.3 52.1 100.2 C-8 25 42.5 30 – – – B-5 51.5 52.4 98.2 B-6 30.4 31.6 96.5 Data given as mass in grams C-1 39.7 57.4 69.2 BRV-C, base-resin varnish C a C-2 43.2 58.3 74.0 H2O (15 g) and ethanol (15g) were added with BRV-C C-3 44.8 58.3 76.9 C-4 52.5 58.3 90.0 C-5 38.3 55.2 69.3 C-6 39.4 56.3 70.0 C-7 37.8 56.3 67.2 Table 4. Monomer composition of adhesive Da C-8 46.1 56.3 81.9 D-0 42.3 55.7 75.9 Adhesive DAAM AAPVA DAA D-2 48.4 55.7 87.0 D-7 48.1 55.7 86.5 A10–D-10 41.0 55.7 73.7 D-0 – 10 (0%) D-12 41.5 55.7 74.6 D-2 – 10 (2.5%) D-14 30.6 55.7 55.1 D-7 – 10 (7.5%) D-19 33.4 55.7 60.0 D-10 – 10 (10.2%) D-22 38.0 55.7 68.3 D-12 – 10 (12.6%) E-1 42.7 49.4 86.5 D-14 – 10 (14.3%) E-2 31.4 40.2 78.0 D-19 – 10 (19.6%) E-3 39.8 47.0 84.6 D-22 – 10 (22.6%) E-4 27.1 37.5 72.2 Data given as mass in grams E-5 48.5 47.0 103.2 AAPVA, acetoacetylated poly(vinyl alcohol); DAA, degree of acetoacetylation a Other ingredients are the same as adhesive A, except for use of base- resin varnish D instead of base-resin varnish A Table 5.
Details
-
File Typepdf
-
Upload Time-
-
Content LanguagesEnglish
-
Upload UserAnonymous/Not logged-in
-
File Pages5 Page
-
File Size-