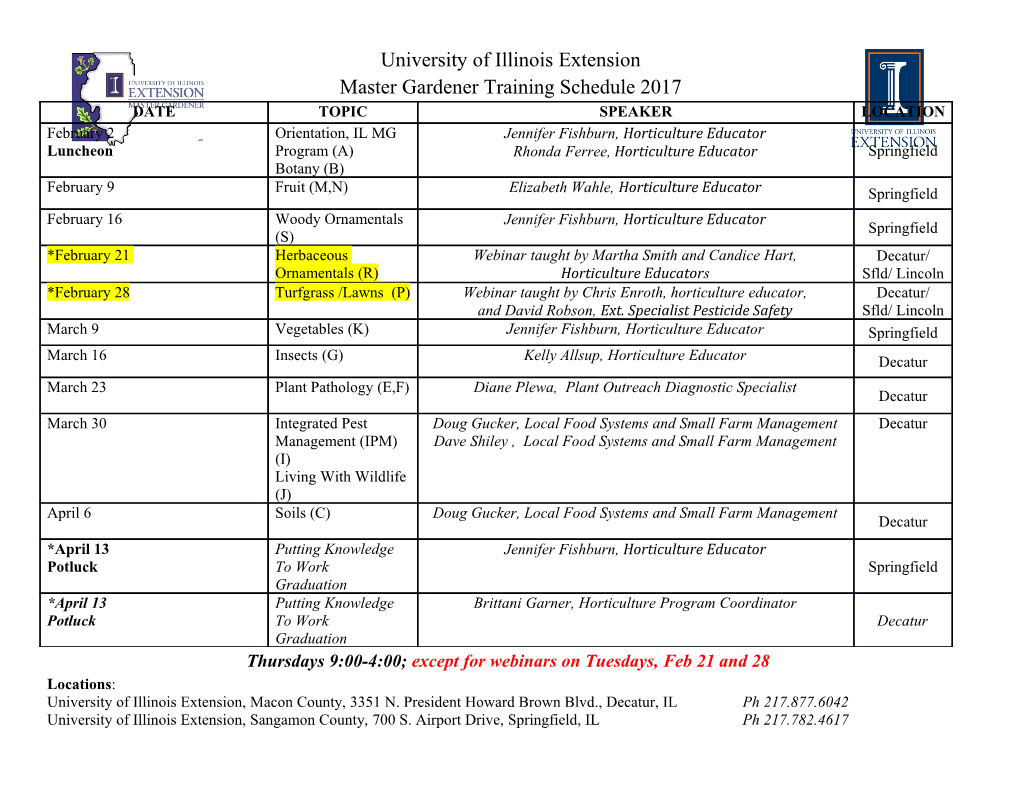
Volume 23, Number 2 - April 2007 through June 2007 The Relationship Between the Workpiece Extension Length/Diameter Ratio and Surface Roughness in Turning Applications By Mr. John Cooper and Dr. Bruce DeRuntz Peer-Refereed Article KEYWORD SEARCH Machine Tools Manufacturing Materials & Processes Metrology Quality Control Research The Official Electronic Publication of the National Association of Industrial Technology • www.nait.org © 2007 Journal of Industrial Technology • Volume 23, Number 2 • April 2007 through June 2007 • www.nait.org The Relationship Between the Workpiece Extension Length/Diameter Ratio and Surface Roughness in Turning Applications Mr. John J. Cooper Jr. is currently working on his Ph.D. in Workforce Education and Development at By Mr. John Cooper and Dr. Bruce DeRuntz Southern Illinois University - Carbondale. He is a teaching assistant in the Department of Technol- ogy and also serves as an adjunct instructor for The advancement of the lathe and sub- eter, and surface roughness of bar stock the Industrial Technology Outreach Program. His research interests include the implementation and sequent modern technologies was made in both supported and unsupported manufacturing areas of lean manufacturing. possible through research leading to the turning operations in an attempt to re- development of optimization tables that duce setup waste in turning operations. list specific feed rates, spindle speeds, and depths of cut for different materi- Literature Review als. These tables are the standard used Since the invention of the modern in industry as a source of reference, engine lathe, researchers have been when making a change from one job to contributing to the body of knowledge another where the machining param- that will optimize the lathe’s productiv- eters of each may be quite different. ity and quality (i.e. surface roughness). The time, material, and tooling costs Surface roughness plays an important associated with the experimental steps role in product quality and is an espe- needed to find the appropriate machin- cially important design characteristic in ing parameters for each new job are many products that are subject to preci- eliminated, giving the company the sion fits, fastener holes, fatigue loads Dr. Bruce DeRuntz is an Associate Professor in advantage of a reduction in setup costs and aesthetic requirements (Wang, the Department of Technology at Southern Illinois University Carbondale. He provides Six Sigma and improved product quality. 2001, Feng & Wang, 2002, and Kalpak- consulting to Fortune 500 companies and teaches jian et al. 2006). Dimensional accuracy courses in Industrial Technology. His experience includes 12 years in the automotive and defense While there are many machining also, together surface roughness greatly industries as a quality engineer and manager. optimization parameters that have been affect useful part life, especially in Bruce holds a Ph.D. in Workforce Education and Development, a M.S. in Manufacturing Systems developed and put into tables, an area cases in which the components will be and is a CSIT and CQE. He is a Certified Quality that has been overlooked is that of cor- in moving contact with other elements Engineer, Certified Senior Industrial Technologist, and ISO 9000 Auditor. relation between the unsupported work- or materials. piece extension length and the resultant surface roughness. The premise of this Recent research that has identified the research is that the use of a tailstock in relationship between surface rough- lathe work for workpiece support may ness and lesser understood turning sometimes be unnecessary. This idea parameters include; surface roughness is investigated to find out if there are versus lubrication and bed material instances where an unsupported work- (Bruni, Forcellese, Gabrielli & Simon- piece can be machined with equivalent cini, 2006), surface roughness versus results to a supported workpiece in tool wear (Pavel, Marinescu, Deis & terms of surface roughness; so the time, Pillar, 2005), surface roughness versus labor, and materials used to center drill burnishing feed rate, force, and speed the workpiece and setup the tailstock (El-Axir & Ibrahim, 2005), and surface are not used needlessly. Therefore, the roughness versus dry turning (Thomas focus of this study is to extend previ- & Beauchamp, 2003). Kalpakjian et al. ously established research on effects of (2006) illustrates a regressing relation- workpiece elastic deformations (Bena- ship between dimensional tolerance and rdos, Mosialos and Vosniakos, 2006) workpiece length, but does not ad- and examine the relationship that exists equately differentiate the surface rough- between the length, at a specific diam- ness correlation between a supported 2 Journal of Industrial Technology • Volume 23, Number 2 • April 2007 through June 2007 • www.nait.org and unsupported workpiece in relation The third interview was with a setup process. The experiments, involving to its length. man in a job shop, whose area of seven different workpiece lengths and expertise was lathe work. He gave an only on the diameter of 1”, focused on The practice of choosing appropri- estimate of 1:4, which he felt would a straight cut of a half inch that was ate process parameters can be quite be appropriate for a straight cut, using made from the end of each workpiece. difficult. To make this determination low carbon steel. When asked about The resultant surface roughness was currently requires time consuming trial the unsupported workpiece extension measured for each of the test incre- and error experimentation which is length/diameter ratio reference chart, ments. The surface roughness values costly in time and material resources. he said he felt there was a definite need reflected the difference in surface finish The solution to this dilemma, according for this type of reference in industry as the workpiece extension length to to Wang (2001), is to develop a chart to because of the amount of trial and error diameter ratio changed. Since previ- serve as a quick reference for industry necessary to optimize the machining ously published research on this spe- to determine pre-chatter conditions, so process (Western Machine Tool & Die, cific subject is very limited, the results poor surface roughness can be avoided. personal communication, December 20, of the study were based on empirical Cutting condition values could be put 2005). evidence obtained during the course of in a formula to evaluate whether the the experiments performed during this cutting conditions would produce a The fourth interview was with an exec- research. This research project was de- chatter-free workpiece. Work in this utive of manufacturing operations. He signed to address the issue in a general area has already begun with the devel- was also unaware of such a formula and manner, focusing on straight turning opment of a knowledge-based system stated “The lack of a formal procedure of low carbon steel using a finishing for the prediction of surface roughness was a problem, especially for the new cut. The experiment was carried out in in turning process (Abburi & Dixit, machinists who had no past experience a setting which closely replicated an 2006). This would eliminate guesswork with which to base a judgment call on.” actual manufacturing facility. The re- by optimizing cutting parameters and He felt there was a very real need to es- search laboratory used is situated in the controlling the quality required for tablish some form of reference material College of Engineering, Department of desired surface finishes. relevant to the unsupported workpiece Technology, Manufacturing Processes extension length/diameter ratio (Kelm Laboratory, at Southern Illinois Uni- This study attempted unsuccessfully to Accubar, personal communication, De- versity Carbondale. The SIUC labora- find existing literary evidence of unsup- cember 28, 2005). Although there is no tory equipment chosen for use in the ported workpiece extension length/di- clear agreement on what an appropriate experimental process are all commonly ameter ratio studies, where the surface ratio should be, there is consensus as to available at industrial manufacturing roughness values were equivalent to the need for such a standard. suppliers. They include the following: those of supported turning. In addition • Bridgeport EZPATH SD CNC Lathe to the past research conducted in this Purpose of the Study (ROHM No. P5354 three jaw chuck) area, the researcher sought out experts The purpose of this study is to identify • Brown & Sharpe Pocket Surf Surface explicitly involved with work utilizing a region along the length of the work- Roughness Tester, Range: Ra - 1µ” to lathe applications. An interview with the piece where the surface roughness val- 250µ” first expert, who specialized in tooling ues of the unsupported workpiece were • Brooks Rockwell Hardness Tester applications, revealed no knowledge statistically comparable to those of the • Kennametal Tool Holder: Part No. of previous formulas for determining supported workpiece. A reference chart MCLNR-124B (Right Hand Tool the unsupported workpiece extension was then developed to illustrate where Holder – Combination lock pin and length/diameter ratio in turning op- an operator could forego the use of the top clamp) erations. He cited a rule of thumb of tailstock during setups. This chart, like • Kennametal Coated Carbide Inserts: “3-5:1” (3 to 5 inches length in ratio to the commonly used feed rate, spindle Part No. CNMG 432 FN, Grade every 1
Details
-
File Typepdf
-
Upload Time-
-
Content LanguagesEnglish
-
Upload UserAnonymous/Not logged-in
-
File Pages7 Page
-
File Size-