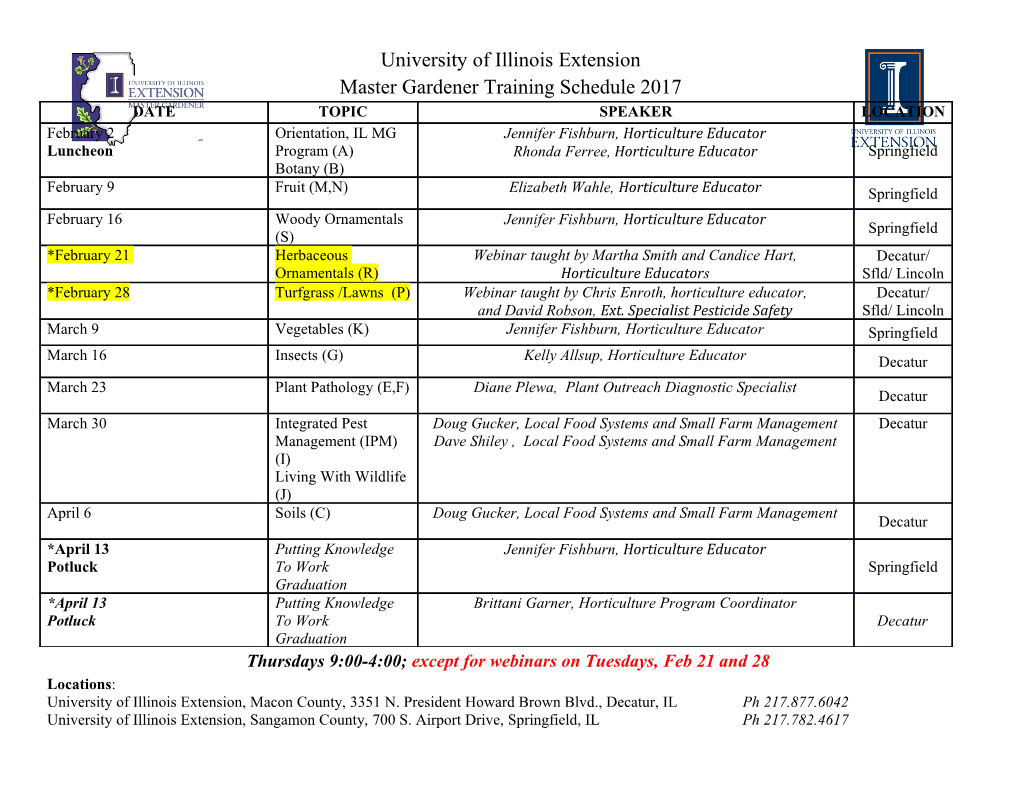
OPERATION, SAFETY AND MAINTENANCE MANUAL 90 – 350 AUTOFORM CNC FORMING CENTER VME II CONTROL FOR MACHINES BUILT BEFORE OCTOBER, 1992 C I N C I N N A T I I N C O R P O R A T E D C I N C I N N A T I , O H I O 4 5 2 1 1 EM-444 (N-09/99) COPYRIGHT 1999 CINCINNATI INCORPORATED AUTOFORM® CNC FORMING CENTER CONTENTS INTRODUCTION SECTION 1 IDENTIFICATION SECTION 2 INSTALLATION UNLOADING 2-1 LIFTING AND MOVING 2-1 FOUNDATION 2-1 ERECTION 2-2 ELECTRICAL ENCLOSURE INSTALLATION 2-3 CLEANING 2-3 LEVELING 2-3 GAGE INSTALLATION 2-4 HYDRAULIC RESERVOIR 2-5 LUBRICATION 2-5 ELECTRICAL CONNECTION 2-5 SECTION 3 SAFETY SAFETY RECOMMENDATIONS 3-1 SAFE OPERATION 3-1 OPERATING RULES 3-2 INSTALLING / REMOVING TOOLING GUIDELINES 3-3 SAFETY SIGNS 3-3 SAFETY GUIDELINES 3-5 SAFETY MAINTENANCE CHECK 3-5 SECTION 4 SPECIFICATIONS PERFORMANCE AND RATINGS 4-1 SPECIFICATIONS CHART 4-2 PRINCIPLE OF OPERATION 4-2 DEFINITION OF TERMS 4-2 CAPACITIES 4-4 PUNCHING CAPACITY 4-4 STRIPPING CAPACITY 4-4 ECCENTRIC LOAD CAPACITY (F-B) 4-4 OFF-CENTER LOAD CAPACITY (L-R) 4-5 SECTION 5 SET-UP & USE TOOL INSTALLATION - SET-UP MENU 5-1 TYPES OF DIES 5-1 TOP OF DIE CALIBRATION FOR UNMEASURED TOOLS 5-5 GAGING - STANDARD BACKGAGES 5-5 CAPACITY 5-5 SELECT GAGE SURFACE 5-6 ADJUST GAGE FINGER POSITION 5-7 GAGE BAR CALIBRATION 5-8 PROGRAM GAGE POSITION(S) 5-8 GAGE FINGER ADJUSTMENT 5-8 WORK SUPPORTS 5-9 OPERATING TECHNIQUES 5-9 TOOLING AND SET-UP 5-9 RUNNING 5-10 SPEED CHANGE/FORMING SPEED 5-10 GAGES 5-10 REMOVING TOOLING 5-10 EM-444 (N-09/99) SECTION 6 MACHINE CONTROLS MACHINE CONTROLS STATION 6-1 AUTOFORM CONTROL STATION 6-3 OPERATOR STATION 6-4 AUTOFORM ELECTRICAL ENCLOSURE 6-5 FOOTSWITCH 6-5 FLOPPY DISK DRIVE 6-5 RS-232/422 COMMUNICATION INTERFACE 6-6 CONTROLS - AUTOFORM OPTIONS 6-6 ADDITIONAL OPERATOR CONTROLS 6-6 DATA CARTRIDGE STORAGE 6-6 RS-232/422 CONVENIENCE PORT 6-6 POWER CLAMP 6-6 CNC BACKGAGES 6-6 CNC FRONTGAGE 6-7 SECTION 7 OPERATION INTRODUCTION TO CNC MACHINE CONTROLS 7-1 SCREEN LAYOUT 7-1 DAILY START-UP 7-9 MACHINE CALIBRATION 7-9 SET-UP MENU 7-10 GAGE BAR CALIBRATION 7-10 TOOLING LIBRARY MENU 7-11 ENTERING A NEW PROGRAM 7-22 JOB DATA MENU 7-22 RAM DATA MENU 7-24 GAGE DATA MENU 7-30 PROGRAM STORAGE MENU 7-37 RUNNING THE MACHINE 7-39 RUN MODE MENU 7-39 QUICK BEND MENU 7-43 MANAGEMENT DATA MENU 7-45 MACHINE CONFIGURATION MENU 7-48 DIAGNOSTICS 7-49 MEMORY DIAGNOSTICS 7-49 DISPLAY CONTROLLER TESTS 7-50 INPUT / OUTPUT TESTS 7-50 FILE SYSTEM 7-51 SYSTEM ERRORS 7-51 STROKE DIAGNOSTICS 7-52 FAULT HISTORY 7-52 LOAD / UPDATE APPLICATION 7-53 TERMINAL MODE 7-53 STATUS AND DIAGNOSTIC LEDS 7-54 STATUS DISPLAY FUNCTIONS 7-54 SUMMARY 7-56 FILE MENU 7-57 FILE TRANSFER MENU 7-57 FILE UTILITY MENU 7-60 FILE PREFERENCES MENU 7-63 COMMUNICATIONS SET-UP MENU 7-64 CAD MENU 7-67 INTRODUCTION TO CAD MENU FEATURES 7-67 PART STORAGE MENU 7-67 PART DESIGN MENU 7-68 SHAPE LIBRARY 7-76 SECTION 8 OPTIONS ADDITIONAL OPERATOR CONTROLS 8-1 AUTO CROWN 8-1 AUTOFORM ADAPTIVE BENDING 8-1 BACKGAGES 8-1 GAGE ASSEMBLIES 8-1 GAGE FINGERS 8-2 PROGRAM GAGE POSITION(S) 8-3 R-AXIS / Z-AXIS DISABLE 8-3 HEAVY DUTY BACKGAGE 8-4 SIX-AXIS BACKGAGE 8-5 SPECIAL STEP PROGRAMMING 8-6 CONTINUOUS RUN MODE 8-7 DATA CARTRIDGE STORAGE 8-7 CNC FRONTGAGE 8-8 CNC FRONTGAGE SET-UP 8-8 CNC FRONTGAGE OPERATION 8-9 PROGRAMMING 8-10 CNC FRONTGAGE SAFETY SIGNS 8-11 GRAPHICS SOFTWARE 8-11 OFFLINE PROGRAMMING 8-12 MANUAL FRONTGAGES 8-12 POWER CLAMP 8-12 PRESENCE SENSING SAFEGUARDING INTERFACE 8-13 PROGRAMMABLE FOOTSWITCH 8-13 OPERATION IN RUN MODE 8-14 SECTION 9 MAINTENANCE & ADJUSTMENTS LUBRICATION 9-1 HYDRAULIC OIL 9-2 OIL FILTERS 9-3 CHECKING AND SETTING HYDRAULIC PRESSURES 9-3 AIR FILTER / BREATHER 9-5 OIL LEVEL / TEMPERATURE SWITCH 9-5 HYDRAULIC UNIT OPTIONS 9-6 OIL COOLER 9-6 OIL HEATERS 9-6 CYLINDERS 9-6 MOTOR / PUMP 9-6 VALVES 9-6 TILT LIMIT SWITCHES 9-6 SWIVEL END-GUIDE BEARING 9-7 ENCODER ADJUSTMENT 9-7 RELEVEL RAM 9-8 USING SPECIAL CONTROL FUNCTION 9-8 MECHANICALLY 9-9 CLOSED HEIGHT ADJUSTMENT 9-9 CARRIAGE ADJUSTMENT 9-9 STANDARD DUAL DRIVE BACKGAGE 9-9 SIX-AXIS BACKGAGE (Optional) 9-10 HEAVY DUTY BACKGAGE (Optional) 9-10 TAPERED BACKGAGE (Optional) 9-10 MACHINE LEVEL 9-10 ELECTRICAL 9-10 MAINTENANCE CHECKLIST 9-10 TROUBLESHOOTING 9-11 CRT DISPLAY ERROR MESSAGES 9-11 OTHER PROBLEMS 9-33 SECTION 10 SERVICE AND PARTS ORDERING REPAIR PARTS 10-1 RETURNING PARTS FOR CREDIT 10-1 SERVICE 10-1 TECHNICAL TRAINING 10-1 ❦ AUTOFORM is a registered trademark COPYRIGHT 1999 of CINCINNATI INCORPORATED CINCINNATI INCORPORATED INTRODUCTION CINCINNATI AUTOFORM The AUTOFORM is a hydraulically driven, servo-controlled press brake. Linear encoders constantly monitor the bed-to-ram position, feeding this information to the Control. The Control is a programmable microcomputer, interfaced by the operator through a keyboard using a conversational program display on a color monitor. The program controls the vertical movement of the ram and movement of the backgage. After a program is entered either the machine can be run or the program stored in internal memory. The AUTOFORM Control allows an individual job to be quickly set- up and run as well as complicated, multi-bend parts or long run jobs. After a program is run, the program and related set-up information can be saved for future use. PART QUALITY The following factors affect part quality: ✦ Press Brake condition and repeatability ✦ Operator ability ✦ Condition of tooling ✦ Quality of material CINCINNATI machines are designed to be rugged and durable. However, improper adjustment or lack of maintenance can reduce the quality of parts produced on that machine. These factors may also affect the repeatability of the machine. A machine that will not consistently reverse at the same point or will drift out-of-level will not produce uniform parts. Operator ability obviously affects part quality and production rate. CINCINNATI INCORPORATED provides many design features in the machine and optional acces- sories to aid even the most experienced operator to produce consistent parts. The operator or set-up person must select the best tooling from those available. The type of gaging, material supports or other special equipment will affect how the part is produced. Selecting the proper bend sequence is important to obtain quality parts and for operator safety. CINCINNATI offers both Operator and Maintenance training programs at our factory to address these problems. This training may cover subjects from the basics of forming to the use of the machines microcomputer controls. Worn, damaged or poor quality dies or filler blocks can directly affect part quality. Using good tooling, selecting the correct tooling for the job and setting them up properly can produce good part quality. Quality of material can affect angular tolerances of the bend. This is due to normal material thickness variations found in commercial steels as well as hard and soft spots in the metal. Using a good grade of material and the proper tooling set-up will minimize the variations. SECTION 1 IDENTIFICATION AUTOFORM CNC FORMING CENTER 1 2 3 4 3 2 5 6 7 8 9 10 23 12 11 15 12 22 13 21 14 20 19 18 17 16 15 1. LEFT HOUSING 8. AUTOFORM CONTROL PENDANT 17. STANDARD GAGE BAR 2. CYLINDER MANIFOLD & VALVES (2) 9. MAIN DISCONNECT SWITCH 18. PALMBUTTON OPERATOR STATION 3. COUNTERBALANCE MANIFOLD 10. FLOPPY DISK DRIVE 19. FOOTSWITCH AND VALVES (2) 11. ELECTRICAL ENCLOSURE 20. AUTO CROWN AUXILIARY CROSS 4. RAM 12. LINEAR ENCODER (2) MEMBER (Optional) 5. RIGHT HOUSING 13. CAPACITY PLATE 21. AUTO CROWN CYLINDER (Optional) 6. RIGHT CYLINDER 14. FILLER BRACKET 22. BED 7. PENDANT ARM 15. BED SHOE (2) 23. LEFT CYLINDER 16. DIE CLAMPS FIGURE 1-1 – Front View EM-444 (N-09/99) 1-1 AUTOFORM CNC FORMING CENTER 1 2 3 4 5 6 12 7 8 9 11 10 1. HOUSING BRACE / HYDRAULIC RESERVOIR 7. ENCODER BRACKET 2. DRIVE MOTOR AND PUMP 8. OPERATOR’S MANUAL POCKET 3. HYDRAULIC MANIFOLD AND VALVES 9. LEVELING SCREW (4) 4. HYDRAULIC FLUID SPECIFICATION PLATE 10. RESERVOIR DRAIN VALVE 5. OIL SIGHT GAGE & THERMOMETER 11. BACKGAGE ARM ASSEMBLY 6. LEFT RAM CLAMP (Behind Encoder Bracket) 12. TILT LIMIT SWITCHES FIGURE 1-2 – Rear View ❦ 1-2 SECTION 2 INSTALLATION UNLOADING After receiving your CINCINNATI AUTOFORM, care- fully remove the contents of the one or more boxes shipped with the machine. All of the machine’s optional accessories and small parts are in these boxes, such as wrenches and leveling shims. Check all of these parts with the packing list. Claims for shortages should be made within ten days. Most machines are shipped assembled on skids. Some of the longer length machines are shipped with the bed removed and bolted to the rear of the housings and some are shipped disassembled. Remove all shipping paper from the wrapped parts of the machine. Leave the shipping skids, bed and ram bracing and electrical enclosure attached to the machine until it has been moved to its final location.
Details
-
File Typepdf
-
Upload Time-
-
Content LanguagesEnglish
-
Upload UserAnonymous/Not logged-in
-
File Pages176 Page
-
File Size-