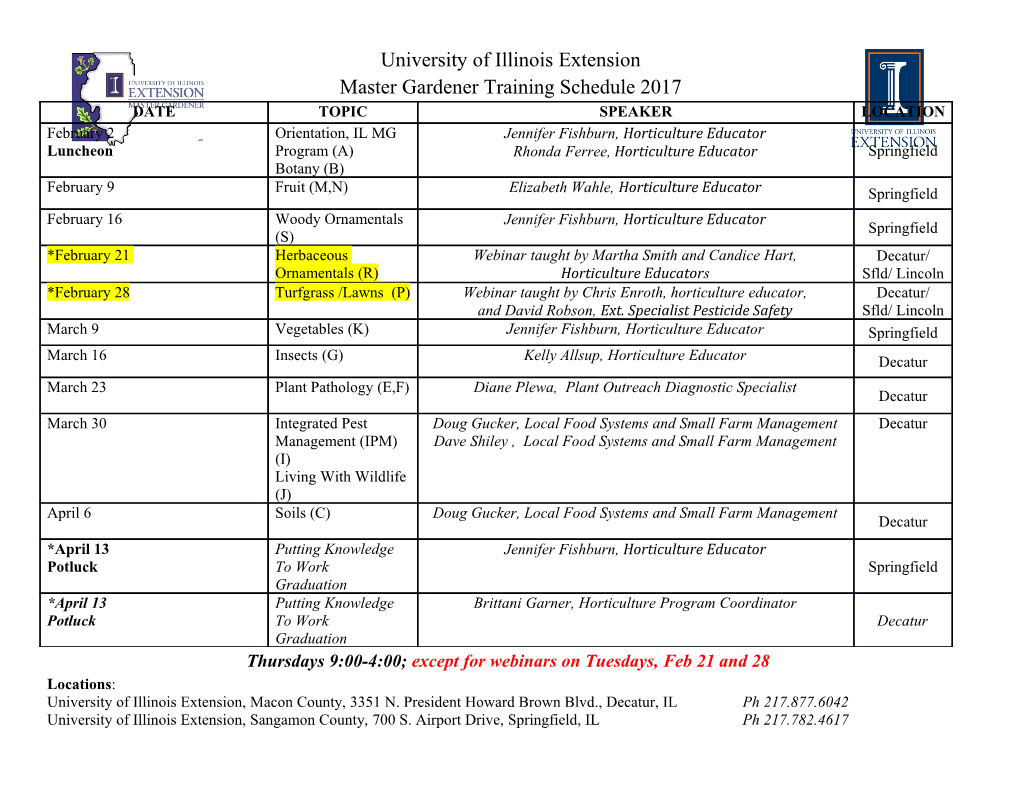
Olefins - Part 1 Industrial Chemistry Process Scheme for Sections 3 - 3.3.2 Butenes Natural Gas lwet I Oil Gas Gas Naphtha Oil Vacuum Distillation iiHydrotreating Naphtha Catalytic and Steam Thermal Crack- Process &--Crac kin ------l Where they come from Ethylenenm Propene Acetylene Ethylene Fuel Gas Ethylene Propene CL- C5- Pyrolysis Fraction Fraction Gasoline , + I 112.2.1 CL-Riffinate C5- Raffinate Ethylene 2-Butene manufacture Ratfinate I1 isobutene or n- Butenes n- and lsopentenes n-Pentenes lsobutene Oligomers n- and lsobutane n- and lsopentanes n- and lsopentanes 68 3. Olejins most valuable C4 olefin source: As shown in Table 3-3, a significantly higher fraction of steam cracking of naphtha butenes is obtained from steam cracking of naphtha than from Which C4 are obtainedcatalytic by cracking steam of gas oil. Therefore cracking? naphtha steam cracking is the more interesting technology for production of unsatu- rated C4 compounds. decrease of total C4 and C4 olefins, but As the cracking- severity increases, both the total yield of the increase Of butadiene under high severity C4 fraction and the proportion of butenes decrease, while the cracking conditions (consequence of butanedesired higher C2H4isobutane yield) proportion of butadiene increases due to its higher stability: Table 3-3. Composition of Cq fractions from steam cracking of naphtha and catalytic cracking of gas oil (in wt%). but-1-ene (E)-but-2-ene Steam cracking Catalytic cracking 1-butene Cracked products Low High (FCC) zeolite trans-2-butene severity seventy catalyst butadiene is stable even under high- 1,3-Butadiene 26 47 0.5 severity conditions (thermodynamically Isobutene 32 22 15 favored because of the conjugation-- energy__ 1-Butene 20 14 12 of 3.5 kcal ,mol) 14.7 kJ trans-2-Butene 7 6 12 (Z)-but-2-ene 2-methylprop-1-ene cis-2-Butene 7 5 11 cis-2-butene isobutene Butane 4 3 13 Isobutane 2 1 31 Vinylacetylene Ethylacetylene ] 2 ] 2 ] - 1,2-Butadiene buta-1,3-diene In steam cracking, the yield of the C4 fraction parallels the butadiene boiling range of the feedstock, beginning with 2-4 wt% from ethane/propane, reaching a maximum of 10-12 wt% from naphtha, and decreasing to 8-10 wt% from gas oil. principle of separation of C4 fraction: The C4 fraction cannot be separated into its components eco- similar boiling points demand more selec- nomically by simple distillation due to the close proximity of tive physical and chemical separation their boiling points. Therefore, more effective and selective methods than distillation physical and chemical separation procedures must be em- separation procedures for the C4 fraction: ployed. The processing of a C4 fraction begins with the separa- 1st stage of Cq separation: tion of the butadiene, as described in Section 5.1.2. separation of HzC=CH-CH=CH2 via After extraction of the major portion and removal of the resid- extraction or extractive distillation with ual butadiene, for example by selective hydrogenation (e.g., selective solvents remaining Cq fraction = raffinate 'Bayer cold hydrogenation' or IFP selective hydrogenation), a mixture is obtained consisting essentially of isobutene, the n- today frequently denoted Raffinate I to distinguish it from Raffinate 11, which is butenes and butane. This is termed the C4 raffinate and has the the C4 fraction after separation of isobutene composition shown below: in the 2"d stage Uses of butenes Alkylation of aromatics for gasoline additives Homo- and co-polymers (iso-butene, 1-butene) Hydroformylation to C5 aldehydes and alcohols Synthesis of MTBE Dehydrogenation of n-butenes to butadiene Thermolysis of isobutene to isoprene How to separate C4 olefins Distillation is not an option since boiling points are too close to one another between –10 °C to 5 °C Separation occurs in different steps separation of separation of butadiene isobutene C4 mixture Raffinate I Raffinate II How to separate butadiene 1) Chemical separation with [Cu(NH3)2]OAc (not competitive nowadays) ASSIGNMENT: Find out why PRINCIPLE: butadiene forms a complex with Cu(I) whereas the other C4 components do not. The complex can reversibly form pure butadiene. 2) Extractive distillation with Acetone, furfurol, acetonitrile, dimethyacetamide, dimethylformamide, N-methylpyrrolidone PRINCIPLE: butadiene is more soluble in the solvents above than the rest of the fraction. Simplified reactor scheme: C4* (Raffinate I) Butadiene solvent Extraction degasser column Solvent Butadiene + C4* Solvent + Butadiene How to separate isobutene 1) Molecular sieving (not competitive nowadays) ASSIGNMENT: Find out why PRINCIPLE: Linear C4 will adsorb in the pores of the zeolite (3-10 Å) whereas branched ones will not. 2) Further chemical reactions: - Reversible hydration to form t-butanol - Reversible esterification to methyl t-butylether (MTBE to TBME) - H+-catalyzed oligomerization to form di- and triisobutene - Lewis acid-catalyzed polymerization to form polyisobutene Reversible processes hydration to form t-butanol + H O+ 3 OH Acids: H2SO4 (50-60%), HCl, Acidic ion exchange resins Regeneration of isobutene with SiO2/Al2O3 catalyst in liquid or gas phase esterification to methyl t-butylether (MTBE) [H+] + MeOH O MTBE Catalyst: Acidic ion exchange resin Uses of MTBE: Increases octane number, reversible reaction not desired. Raffinate II is subjected to isomerization of n-butenes to give isobutene, which is further converted to MTBE. Irreversible processes H+-catalyzed oligomerization to form di- and triisobutene [H+] 2 Acid: H2SO4 or ion exchange resin Simple technology but isomerization is a major side reaction Lewis acid-catalyzed polymerization to form polyisobutene L.A. n n Catalysts: -BF3 (BASF, MW between 1000-2500) additive to fuels and lubricants -AlCl3 (Cosden, MW between 200 - 2700) plasticizer, adhesives Purification of Raffinate II At this point we have a mixture of linear butenes and butanes. A separation by reaction - e.g. by hydration - is not needed due to the exclusive reactions of butenes. Butanes are inert. Separation of n-butanes from n-butenes can be done by extractive distillation and of the isomers of butene by distillation. 1-butene Important to have pure to get the polymer of poly-1-butene (PB-1), used as blending material for polyethylene and polypropylene. It is used as is in flexible packaging, compounding, pressure piping and hot melt adhesives. Synthesis via: 1) dimerization of ethylene: [Cat] 2 [Cat]: Ti(OR)4 + AlR’3 2) Oligomerization of ethylene and separation (see SHOP).
Details
-
File Typepdf
-
Upload Time-
-
Content LanguagesEnglish
-
Upload UserAnonymous/Not logged-in
-
File Pages11 Page
-
File Size-