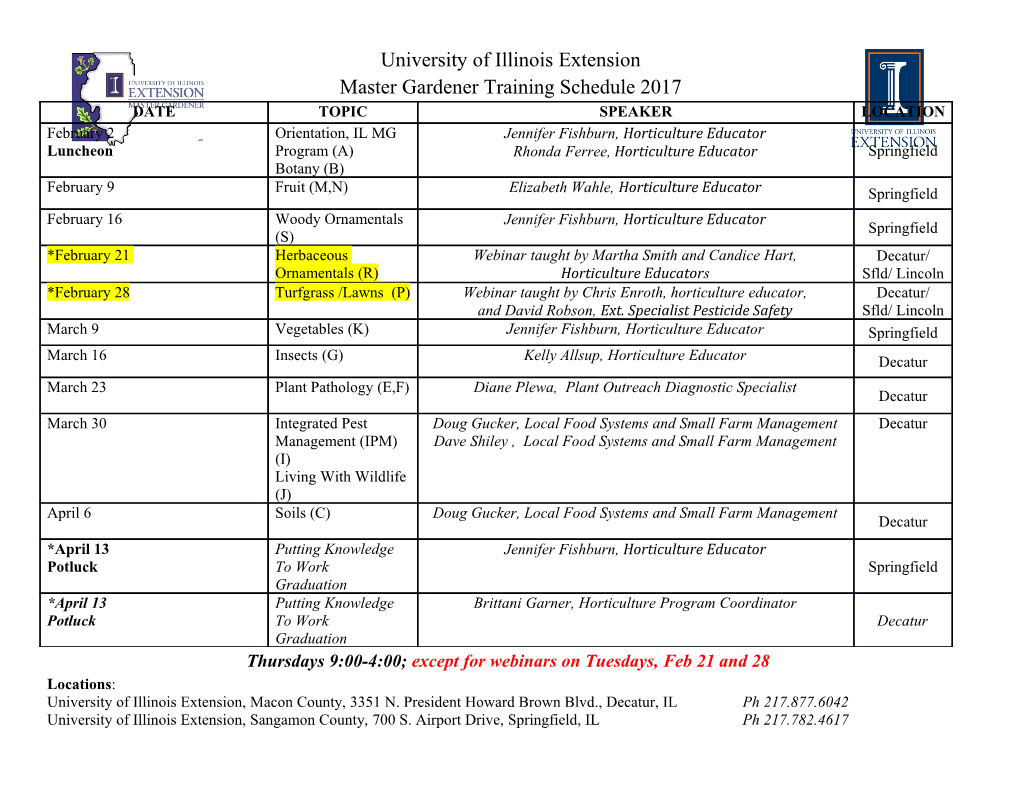
ISIJ International, Vol. 58 (2018),ISIJ International, No. 7 Vol. 58 (2018), No. 7, pp. 1250–1256 Formation and Evolution of Inclusions in Si-killed Resulfurized Free-cutting Steel Qingsong ZHANG,1,2) Yi MIN,1,2)* Haisheng XU1,2) and Chengjun LIU1,2) 1) Key Laboratory for Ecological Metallurgy of Multimetallic Ores (Ministry of Education), Northeastern University, Shenyang, 110819 P.R. China. 2) Northeastern University School of Metallurgy, Shenyang, 110004 P.R. China. (Received on February 8, 2018; accepted on March 28, 2018; J-STAGE Advance published date: May 26, 2018) In order to control the machinability and mechanical property of resulfurized free-cutting steel, the high temperature experiments at laboratory and thermodynamic analysis were carried out to investigate the formation and evolution of inclusions in the processes of refining and solidification. Furthermore, the migration behavior of sulfur was also assessed between the inclusions and the liquid steel. The results showed that the liquid oxysulfide inclusion (Mn,Si)x(O,S)y with trace amount of sulfur formed after FeS addition at 1 600°C. As sulfur segregated in the residual liquid steel during solidification, sulfur rapidly migrated into (Mn,Si)x(O,S)y from the liquid steel at the initial stage of solidification. However, sulfur migrated out from (Mn,Si)x(O,S)y at the middle stage of solidification because MnS precipitated from the supersaturated liquid steel. After the steel solidified completely, sulfur continued to migrate out from the liquid oxysulfide inclusion (Mn,Si)x(O,S)y. When the temperature decreased to 1 250°C, the liquid inclusion (Mn,Si)x(O,S)y transformed to two solid phases of (Mn,Si)xOy and MnS. Finally, the complex inclusion com- posed of (Mn,Si)xOy and MnS formed. KEY WORDS: free-cutting steel; resulfurized; Si-killed; oxysulfide inclusions. related to the oxygen content in steel.8,9) Type I sulfide 1. Introduction inclusions form under the condition of high oxygen content, Resulfurized free-cutting steel is widely used as manu- whereas type II and type III sulfide inclusions are precipi- facturing product due to its favorable machinability. The tated when the oxygen content is low. As for the formation machinability of free-cutting steel depends on the sulfide mechanism of sulfide inclusions, it is widely believed that inclusions formed in steel. During the machining process, type II sulfide inclusions are formed by steady eutectic sulfide inclusions induce stress concentrations to lower reaction, while type III sulfide inclusions are produced by power requirements for shear and facilitate chip fracture.1) unsteady eutectic reaction.10,11) However, there is still a lack However, sulfide inclusions tend to segregate along the of understanding about the formation mechanism of type I grain boundary during solidification and the machinability sulfide inclusions. Steinmentz et al.12) studied the influence was deteriorated. Furthermore, sulfide inclusions deforming of different deoxidizers on the morphology of sulfides and along rolling direction during hot rolling process results in proposed that type I sulfide inclusions were the eutectic the mechanical anisotropy.2) In order to improve the machin- products composed of oxide and sulfide. However, Oikawa ability and mechanical property of resulfurized free-cutting et al.5) insisted that type I sulfide inclusions were MnS- steel, it is necessary to control the composition, distribution riched oxysulfide inclusions formed by monotectic reaction. and morphology of sulfide inclusions. The precipitation of Therefore, the formation mechanism of type I sulfide inclu- sulfide inclusions is controlled by the steel composition3,4) sions needs to be further explored. and deoxidization products5,6) in the process of refining and In the production of resulfurized free-cutting steel, semi- solidification. Therefore, it is significant to clarify the for- killed method is often used to control the oxygen content mation and evolution mechanism of inclusions in resulfur- in steel to form type I sulfide inclusions. In order to predict ized free-cutting steel. the composition of deoxidization products in Si-killed steel, According to the classical work by Sims,7) sulfide inclu- Choudhary et al.13) established the equilibrium relation- sions are classified into three types: (1) randomly dispersed ship between the liquid steel and deoxidization products globular sulfides (Type I), (2) rod-like fine sulfides distrib- at the steelmaking temperature and accurately predicted uted along the grain boundary (Type II), and (3) angular the composition of inclusions in carbon steel. Karasev et sulfides (Type III). The type of sulfide inclusions is closely al.14) studied the evolution of inclusions in deoxidization process of Fe-10 wt% Ni alloy with Si, it was found that * Corresponding author: E-mail: [email protected] the morphology of inclusions were spherical and the mean DOI: http://dx.doi.org/10.2355/isijinternational.ISIJINT-2018-105 spatial diameter increased with increasing holding time. © 2018 ISIJ 1250 ISIJ International, Vol. 58 (2018), No. 7 Vantilt et al.15) observed the movement of silicate inclu- Table 1. Chemical compositions of raw materials (wt%). sions on the surface of liquid steel using Confocal Laser Fe Ni Al Mn C Si Mg S Balance Scanning Microscope (CLSM). The results showed that the Pure inclusions tended to cluster under the action of capillary 99.90 0.01 0.018 0.03 0.0021 0.01 – 0.003 0.035 iron force. Actually, the inclusion research is a comprehensive Mn–Fe process, which involves the process of smelting and casting. 12.57 84.20 1.50 1.50 – 0.03 However, most researches about the deoxidization products alloy Pure of silicate inclusions are mainly focused on the refining 99.90 0.10 process, little attention has been paid to the evolution of silicon inclusions during cooling and solidification process. FeS 63.32 36.18 0.50 Apart from deoxidization inclusions, oxysulfide inclu- powder sions which composed of oxide and sulfide are often found in the sulfur bearing steel.16–18) Wakoh et al.19) studied the effect of oxide particles on MnS precipitation in low sulfur steel of Fe-0.1 wt% C-1.0 wt% Mn-0.01 wt% S, it was found that higher MnS precipitation ratio was obtained in the composition range of SiO2–MnO where liquidus temperature was low and sulfide capacity was high. Ohta et al.6) investigated the precipitation and dispersion of SiO2–MnO–MnS in Fe-10 wt% Ni-1.0 wt% Mn-0.04 wt% S alloy, and proposed that MnS precipitated on SiO2–MnO particles during cooling process because of the partition of the dissolved sulfur between steel and liquid SiO2–MnO. In order to understand the formation mechanism of SiO2– MnO–MnS, Reddy et al.20) and Koyama et al.21) measured the solubility of MnS in SiO2–MnO melts, the results showed that the solubility of MnS increased with increas- 22) ing the ratio of MnO/SiO2. Hasegawa et al. and Woo et al.23,24) experimentally investigated the phase relations for SiO2–MnO–MnS slag system at temperatures ranging Fig. 1. Schematic diagram of heating furnace. (1 Movable baffle, from 1 200°C to 1 500°C. And the oxysulfide compound 2 Gas outlet, 3 Furnace tube, 4 MoSi2 rod, 5 Graphite cru- composed of SiO2–MnO–MnS was found as a stable solid cible, 6 MgO crucible, 7 Crucible supporter, 8 Thermo- phase at the temperature lower than 1 300°C. Previously, couple, 9 Cooling water, 10 Gas inlet). most experimental investigations on oxysulfide inclusions have been focused in the low sulfur steel, but the formation mechanism of SiO2–MnO–MnS and the migration of sulfur are still not clear clarified in the high sulfur steel, especially in the resulfurized free-cutting steel. In the present study, the formation and evolution of inclu- sions in Si-killed resulfurized free-cutting steel were studied in the process of refining and solidification. The field emis- sion scanning electron microscope (FE-SEM) and energy dispersive spectrometer (EDS) were employed to analyze the morphologies and chemical compositions of inclusions. Based on the thermodynamic analysis, the migration behav- ior of S elements between inclusions and the liquid steel was Fig. 2. Melting and sampling sequences of present experiments. also investigated. steel to control the oxygen content. The oxygen activities 2. Experimental Methods were directly measured before and after silicon addition 2.1. Experimental Procedures using the electrolyte oxygen probes. Subsequently, the The raw materials included pure iron, Mn–Fe alloy, pure melts were respectively held for 1 min, 5 min and 10 min silicon and FeS powder. The compositions of raw materials at 1 600°C and then sampled by a quartz tube, followed by are listed in Table 1. The experiments were carried out in rapid quenching in the ice bath. Finally, FeS powder was the tube furnace heated by MoSi2 rods with two continu- inserted into the molten steel to adjust the sulfur content ously temperature measuring thermocouples. The schematic and the steel was sampled 5 min later. Thereafter, the melts of heating apparatus is shown in Fig. 1. were cooled to 1 200°C at a rate of 3°C·min −1 and then to The details of experimental process are provided in Fig. room temperature by cutting off the power supply to the 2. Firstly, about 400 g pure iron was heated to 1 600°C furnace. The samples after slow cooling were used to study under argon atmosphere, then a certain amount of Mn–Fe the evolution of inclusions during solidification. alloy and pure silicon were successively added to the liquid 1251 © 2018 ISIJ ISIJ International, Vol. 58 (2018), No. 7 2.2. Analysis Methods through a polycarbonate membrane film filter with an open The contents of Si, Mn and S in the sample S5 after slow pore size of 0.45 μm.
Details
-
File Typepdf
-
Upload Time-
-
Content LanguagesEnglish
-
Upload UserAnonymous/Not logged-in
-
File Pages7 Page
-
File Size-