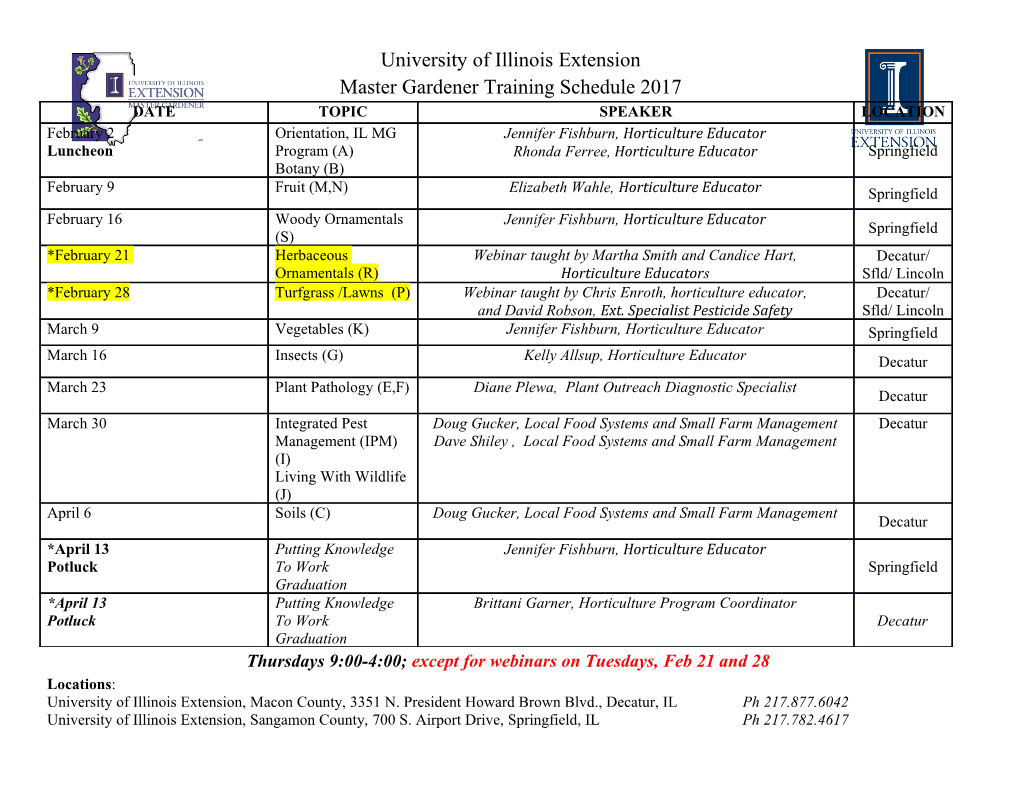
ANALYSIS OF GEAR PAIR CONTACT TO PRIDICT EFFICIENCY 1Mr. Ravindra S. Lahane, 2Dr. H. P. Jawale # Mechanical Engineering Department, D Y Patil College of Engineering Akurdi, Savitribai Phule Pune University Mechanical Engineering Department, Visvesvaraya National Institute of Technology Nagpur University Email: [email protected], [email protected] Abstract—Gear pair is higher pair point varies over the path of contact of the gear meshes contact is under the stress. Due to that point ranging between 94% to 99.5%. contact get converted into line contact. There are other benefits to improving gear Deformation due to contact losses some efficiency as well. Since the efficiency losses energy during meshing of gear is generally amount to additional heat generation within the neglected, but so many researchers calculate gearbox, several gear failure modes including efficiency of gear drive by practically and scoring and contact fatigue failures are directly analytically is upto 98% for metal only.if the impacted by the efficiency of the gear pair. A error due to deformation in transmission in more efficient gear pair generates less heat, and gear box is small no one proposed this kind therefore, it is likely to perform better in terms of work is workout in this paper. such failures. In the process, demands on the Keywords— Gear pair, Contact, capacity and the size of the lubrication system Deformation, Efficiency. and the amount and quality of the gearbox I. INTRODUCTION lubricant are also eased with improved Efficiency of spur and helical gear systems has efficiency. This also reduces the overall weight become an increasingly important research topic of the unit contributing to further efficiency as the fuel economy requirements for today’s improvements. passenger vehicles and rotorcraft are more The total efficiency loss of the gearbox is stringent, not only due to fuel cost, but also attributable to sliding and rolling frictional losses environmental concerns associated with energy between the gear teeth, windage losses due to utilization and air pollution. Improved gear complex interactions with the air surrounding the system efficiency also results in less frictional gears, and oil splashing and churning losses heat generation within the gearbox, resulting in inside the gearbox, as well as the losses improvements in gear failure modes such as associated with the bearing and seals. While scoring and pitting, and lower-capacity churning and windage losses are mostly lubrication systems. Sliding friction contributes geometry and speed related, friction losses are about 98% of the total power loss for gear trains mainly associated with sliding velocities and operating at relatively low speeds (less than 2000 load. Friction losses of hypoid gears are of rpm input speed). Rolling frictional losses primary interest here since they are a major decrease with increased load while windage source of losses in a drive train. As a common losses are only significant for gears running at automotive application, the drive train of a rear- very high speeds (greater than 3000 rpm). The wheel-drive (or all-wheel-drive) car or truck results also showed that the overall efficiency contains one (or two, one rear and one front) axle ISSN(PRINT):2394-6202,(ONLINE):2394-6210,VOLUME-1,ISSUE-5,2015 45 INTERNATIONAL JOURNAL OF ADVANCES IN PRODUCTION AND MECHANICAL ENGINEERING (IJAPME) gearbox that is formed by a hypoid final drive i. Efficient power transmission systems ensure reduction unit and a differential. Unlike parallel fuel economy of automobiles, marine vessels and axis gears that may have a mechanical efficiency aircrafts. well over 99 percent, the efficiency of hypoid ii. With less fuel consumption, less pollutant gears usually falls into the range of 86 to 97 gases and particulate are emitted to the percent depending on the amount of relative environment sliding induced the gear geometry. This is mainly As the recent work is on the gear contact, when because sliding velocities in a hypoid gear gear pair is rotated due tensional effect due to that contact are significantly larger than parallel-axis causes the small deformation in the profile causes gears. As a result of this, an axle unit that is minor loss in energy that error affects in formed by a single hypoid gear set has the same transmission efficiency. levels of (and in May applications more) power 1. Gear pair is the higher pair with line loss as a manual or automatic transmission that contact under the stress , line contact get contains many spur or helical gears. This converted into surface contact i.e. lower pair due presents the hypoid gear drive as a prime to that degree of freedom is zero hence motion candidate for any efficiency improvement will not possible, law of gearing is not possible efforts. at all point due to series of deformation. Until now many researchers have worked on 2. The motion will takes place because of static and dynamic contact of contact with the additional deformation with satisfaction of Gosselin etal [1] applied a new methodology law of gearing. based on FEM to analyze the contact stress and 3. Resistance to the motion is due to : displacement of the line contact condition in spur a. Friction b. Additional deformation gears. 4. Tractive forces causes the deformation at Braucr Zanzi and Pedrero and Guing and etal point of contact, hence some Energy is utilized [2] on Tooth contact analysis and stress analysis for Local Deformation. Practically, complete of gear drives. Strain Energy is not regained under elastic Umezawa and Ishikawa [3] presented deformation. experimental studies for the deflections and NOMENCLATURE: moments of a gear tooth. Chabert et al also presented valuable results Z1 No. of teeth on pinion using finite element method (FEM) on the Z2 No. of teeth on gear stresses and deflection of spur gear teeth induced α Pressure Angle by a static load. m Module Litvin etal [1] developed computer programs dp Pitch circle Diameter of Gear1 that integrate computerized design, tooth contact dg Pitch circle Diameter of Gear2 analysis and automatic modeling and finite A Addendum of gear element simulation of a new type of helical gear D Dedendum of gear drives. t Tooth thickness w Face width Vedmar and Henriksson introduced a method P Circular pitch to use the deformations of the gears to determine F Applied load vector the variation of the gear mesh stiffness and the Pmax Maximum contact stress boundary of the action between the gears.Little Fi Load per unit width research has been reported on finite element σH Maximum Hertz stress based methods to investigate the dynamic a Contact width contact/impact problems of gear drives. h Working depth GEARS are the most common power H Whole depth transmission systems in industrial machinery, Ac addendum circle diameter automobiles, aircrafts, marine vessels et cetera. Dc dedendum circle diameter The efficiency of these power transmission CR Contact Ratio systems is an important design factor due to the CL Contact Length following R1 Radius of Gear1 reasons: R2 Radius of Gear2 ISSN(PRINT):2394-6202,(ONLINE):2394-6210,VOLUME-1,ISSUE-5,2015 46 INTERNATIONAL JOURNAL OF ADVANCES IN PRODUCTION AND MECHANICAL ENGINEERING (IJAPME) L length of cylinder may have complicated geometries and material Ft Tangential Force properties and may deform in a seemingly Fr Radial Force arbitrary way. With the rapid development of Fn Normal Force computational mechanics, however, great Ei Young’s Modulus of elasticity progress has been made in numerical analysis of µ Poisson’s ratio the problem. Using the finite element method, ∂x in x-direction many contact problems, ranging from relatively ∂y Deformation in y-direction simple ones to quite complicated ones, can be ∂z Deformation in z-direction solved with high accuracy. The Finite Element σ Normal Stress Method can be considered the favourite method τ Shear Stresses to treat contact problems, because of its proven σxx, σyy, σzz Normal Stress in X, Y and Z success in treating a wide range of engineering Direction problem in areas of solid mechanics, fluid flow, εxx, εyy, εzz Normal Elastic Strain in X, Y and heat transfer, and for electromagnetic field and Z Direction coupled field problems. An easy way to comply τxy, τyz, τxz Shear stress component in XY, with the conference paper formatting YZ and XZ Plane requirements is to use this document as a γxy, γyz, γxz Shear strain component in XY, template and simply type your text into it. YZ and XZ Plane 2 How to Solve the Contact Problem There are many types of contact problems that may be encountered, including II.CONTACT ANALYSIS OF TWO contact stress, dynamic impacts, metal CYLINDRICAL forming, bolted joints, crash dynamics, and 1. Why is the Contact Problem Significantly assemblies of components with interference fits, Difficult etc. All of these contact problems, as well as Despite the importance of contact in the other types of contact analysis, can be split into mechanics of solids and its engineering two general classes (ANSYS), applications, contact effects are rarely seriously Rigid - to - flexible bodies in contact, taken into account in conventional engineering Flexible - to - flexible bodies in contact. analysis, because of the extreme complexity In rigid - to - flexible contact problems, one or involved. Mechanical problems more of the contacting surfaces are treated as involving contacts are inherently linear elastic being rigid material, which has a much higher behavior. stiffness relative to the deformable body it First, the actual region of contact between contacts. Many metal forming problems fall into deformable bodies in contact is not known until this category. the solution has been obtained. Depending on the Flexible-to-flexible is where both contacting loads, materials, and boundary conditions, along bodies are deformable. with other factors, surfaces can come into and go Examples of a flexible-to-flexible analysis out of contact with each other in a largely include gears in mesh, bolted joints, and unpredictable manner.
Details
-
File Typepdf
-
Upload Time-
-
Content LanguagesEnglish
-
Upload UserAnonymous/Not logged-in
-
File Pages15 Page
-
File Size-