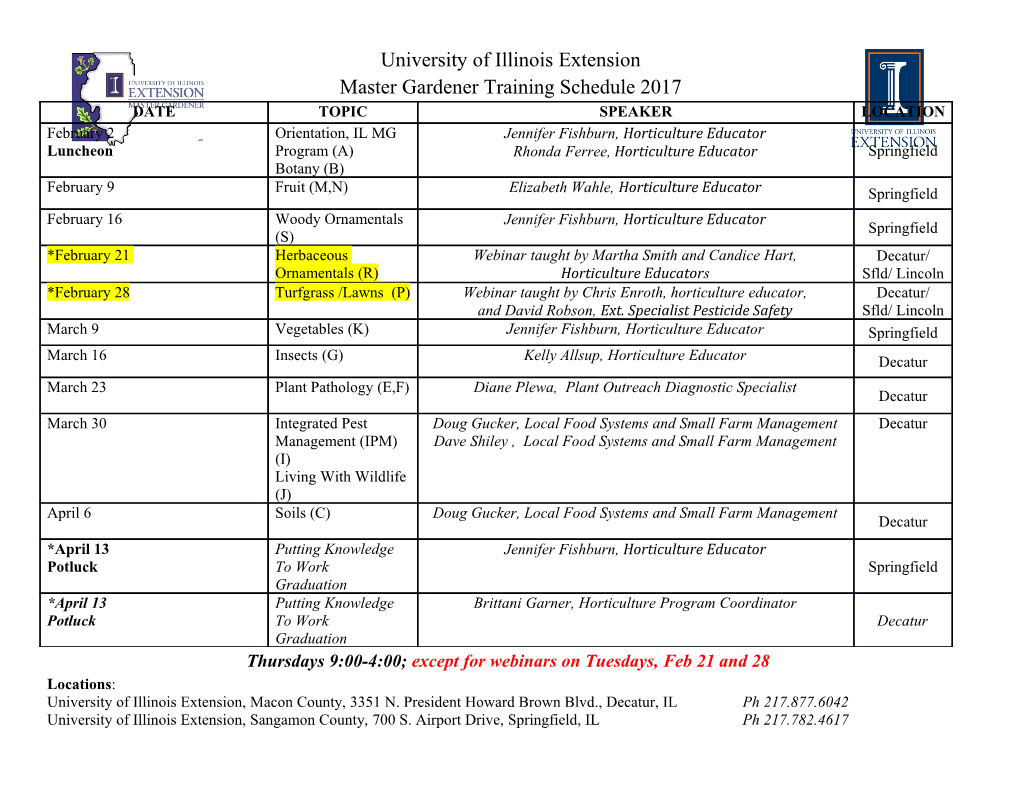
View metadata, citation and similar papers at core.ac.uk brought to you by CORE provided by National Aerospace Laboratories Institutional Repository A Methodology for Afterburner Evaluation J.J. Isaac *, N.R. Ramesh *, V.S. Krishnakumar *, C. Rajashekar *, S.R.Shyamsundar*, A.P. Haran+ and V.Sundararajan+ Abstract: A preliminary investigation of the performance of an afterburner module proposed by the Gas Turbine Research Establishment, Bangalore for the Kaveri engine has been carried out. The investigation, which was both theoretical and experimental, evaluated the afterburner configuration on the basis of flame stability, combustion efficiency and total pressure loss. An evaluation methodology, which was formulated, has been em- ployed to arrive at design modifications for improved performance. INTRODUCTION afterburner leads to increased exit veloci- ty and thrust. In order to achieve better take-off characteristics, higher rate of climb and The current trend towards high turbine meet performance demands during tac- discharge temperature and the require- tical maneuvers, the thrust of an aeroen- ment for satisfactory operation over ex- gine has to be augmented by employing tended fuel/air ratios and flight maps has an afterburner. The main advantages of complicated the application of conven- using the afterburning gas turbine cycle tional afterburner technology to modern is that the weight and size of the aug- jet engines. Weight penalties dictate a mented engine are much less than that short afterburner. Hence, the flame hold- of a turbojet engine which can produce er/fuel injector configuration has to be the same maximum thrust periodically. chosen as a compromise between ac- Afterburning consists of the introduction ceptable ignition/good flame stability cha- and burning of kerosene fuel between racteristics and low total pressure loss / the engine turbine and the jet propelling high combustion efficiency for the stipu- nozzle. Due to structural limitations, the lated afterburner length (Ref.1). Fuel ato- maximum gas temperatures approaching misation/ mixing, flame stabilisation and the turbine are limited to around half the flame spreading are yet not fully unders- adiabatic flame temperature. Conse- tood. Consequently, the selection of the quently, the gas leaving the turbine will best flame holder geometry, width and still contain a considerable proportion of blockage, fuel injector geometry and loca- oxygen. Secondary burning of fuel in the tion, fuel injector-flameholder separation and afterburner length is a time consum- ing exercise (Ref.1). -------------------------------- * National Aerospace Laboratories, Bangalore + Gas Turbine Research Establishment, Bangalore ---------------------------------------------------------------- Paper presented at the 3rd National Conference on Air Breathing Engines and Aer- ospace Propulsion, IIT, Madras, 28-30th Dec. 1996. 1 It is clear that the successful de- methods.. Particular emphasis was placed sign/development of an efficient after- on flame stability, combustion efficiency burner requires a good knowledge of the and the optimum geometric blockage and coupling of complex fluid flows with chem- after burner length. Computer graphics ical reaction processes. The complexity studies of flame holder configurations of the aerothermodynamics and chemical were carried out on an IRIS workstation processes that occur together in an after- of the CSIR Centre for Mathematical burner does not allow the adoption of a Modelling and Computer Simulation (C- purely analytical approach to component MMACS). design and performance prediction. In practice, a semi-empirical treatment is al- Extensive flow visualisation studies of ways adopted. afterburner models were then carried out in the water tunnel of the Experimen- A methodology for afterburner evaluation tal Aerodynamics Division, National Aero- is presented. It has been employed to space Laboratories (NAL). A specially evaluate an afterburner module for the set-up fuel spray rig was used to study Kaveri engine. the spray qualities of different types of fuel injectors in the Combustion Labora- METHODOLOGY tory, Propulsion Division. The approach has been to de- Detailed model tests with combustion vise/develop rapid screening and evalua- were then carried out in the Combustion tion methods with which to check out af- Laboratory of the Propulsion Division, terburner configurations (typically fig.1) NAL. The tests included checking satis- and to restrict actual testing only to those factory ignition determining the flame sta- promising configurations. The strategy bility characteristics as well as measure- has been to adopt a three pronged attack. ment of combustion efficiency and cold and hot pressure losses. All inlet condi- The afterburner module was checked tions were chosen to conform to those out analytically employing semi-empirical stipulated by GTRE . DIFFUSER MIXED AFTERBURNER CONE FUEL SPRAY BARS RING RADIAL EXHAUST FLAME NOZZLE HOLDER Fig. 1. Kaveri Engine 2 ANALYTICAL STUDIES keep total pressure losses down to per- missible levels. The maximum heat that Total pressure loss can be added increases and the total pressure loss decreases as the inlet Mach The afterburner is typically used for the number decreases. Moreover, stabilisa- time limited operation of takeoff, climb and tion of flames becomes easier as the combat maneuvers. Hence, the diffuser inlet Mach number decreases. Hence, it flame holder/fuel injector system should is conventional practice to incorporate be so designed to achieve high perfor- a diffuser between the turbine exit mance in the afterburning phase and to plane and the afterburner combustion give rise to low dry loss in the non- zone. These theoretical estimates were afterburning phase. arrived at by considering the afterburner section as a constant area duct with sim- The total pressure loss of an afterburn- ple heating and internal drag corres- er is mainly composed of that due to the ponding to a weighted equivalent flame diffuser, the drag of the flame holder/fuel holder/fuel ring assembly geometric injector system and the combustion blockage and drag coefficient. process. It is recognized that it is ne- cessary that a system total pressure loss Flame holder blockage has to be incurred in order to achieve design objectives such as large tem- Flame stabilisation in a high velocity perature rise, wide temperature modula- stream of a combustible mixture is rea- tion, high efficiency, short duct length dily accomplished by introducing a bluff and to affect a stabilizing effect on body which produces in its wake a low combustor aerodynamics. However, this velocity recirculatory flow. Although the total pressure loss has a serious impact mechanism of flame stabilisation is still on engine thrust. Typically, a 1% in- not fully understood, adequate experimen- crease in total pressure loss will result in tal data is available for its behaviour to be a 1% decrease in thrust. predicted accurately. An examination of the flame stability correlating equation n m Vbo/PD T = f ( ) would reveal that an increase in the characteristic dimension D or a decrease in the velocity Vbo past the flame holder would improve flame stabili- ty. An increase of pressure P, tempera- ture T as well as operation at equivalence ratios ( ) close to unity would lead to im- proved flame stability. However, an in- crease in D and hence in flameholder blockage would increase the velocity past the flameholder for a given duct size. This would impair flame stability. Hence, there is an optimum value of the flame- holder size for a given approach stream velocity for which peak flame stability is attained Fig. 2. Total pressure loss-effect of geometric blockage and inlet Mach num- ber Fig. 2 shows that serious efforts should be made to reduce the afterburner inlet Mach number and characteristic flame holder blockage and drag coefficient to 3 aerodynamic blockages in the range 0.25 to 0.40 could be chosen to suit other con- siderations. It would be logical for the choice to tend to the higher values from flame spreading considerations. Fig.4 shows that the corresponding geometric blockages should lie in the range 0.20 to 0.30. Fig. 3 . Variation of stability parameter with aerodynamic blockage - 2D The aerodynamic blockage of a flame- holder has been shown to have a signifi- cant effect on flame stability (Fig.3). The variation of the aerodynamic blockage with the flameholder geometric blockage has been determined (Fig.4). It is seen that the aerodynamic blockage is no longer directly proportional to the geome- tric blockage at high blockages. From a Fig. 4. Variation of aerodynamic blockage knowledge of the optimum aerodynamic with geometric blockage-conical flame blockage for a given flameholder shape, holders the corresponding geometric blockage could be deduced and practical flame- Quasi-morphological studies holder sizes chosen at the design stage. The optimum aerodynamic blockage is In conventional practice, flameholder seen to decrease with an increase in ap- systems employed in turbofan afterburn- proach Mach number (Fig.3). ers consist of `Vee' gutter arrays arranged in the form of rings or radials or a com- In order to minimise weight, the diffuser bination of both. At present, a general is kept as short as possible without flow methodology is not available for the selec- separation from the inner cone. The tion of the flameholder array geometry to flame holder/fuel injector system is also achieve optimum flame coverage and located
Details
-
File Typepdf
-
Upload Time-
-
Content LanguagesEnglish
-
Upload UserAnonymous/Not logged-in
-
File Pages12 Page
-
File Size-