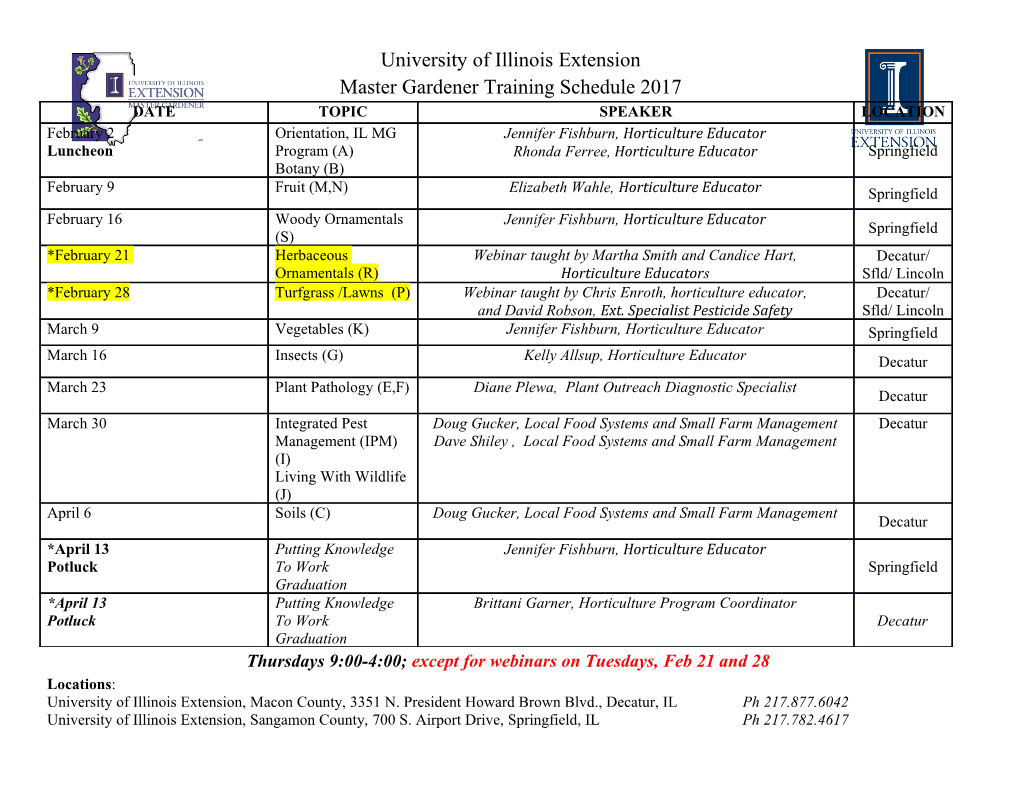
Experimental and theoretical analysis of friction stir welding of Al–Cu joints Ahmed O. Al-Roubaiy, Saja M. Nabat & Andre D. L. Batako The International Journal of Advanced Manufacturing Technology ISSN 0268-3768 Int J Adv Manuf Technol DOI 10.1007/s00170-013-5563-z 1 23 Your article is protected by copyright and all rights are held exclusively by Springer- Verlag London. This e-offprint is for personal use only and shall not be self-archived in electronic repositories. If you wish to self-archive your article, please use the accepted manuscript version for posting on your own website. You may further deposit the accepted manuscript version in any repository, provided it is only made publicly available 12 months after official publication or later and provided acknowledgement is given to the original source of publication and a link is inserted to the published article on Springer's website. The link must be accompanied by the following text: "The final publication is available at link.springer.com”. 1 23 Author's personal copy Int J Adv Manuf Technol DOI 10.1007/s00170-013-5563-z ORIGINAL ARTICLE Experimental and theoretical analysis of friction stir welding of Al–Cu joints Ahmed O. Al-Roubaiy & Saja M. Nabat & Andre D. L. Batako Received: 5 June 2013 /Accepted: 16 December 2013 # Springer-Verlag London 2014 Abstract This paper presents a study of friction stir welding Keywords Friction stir welding . Aluminium . Copper . of aluminium and copper using experimental work and theo- Dissimilar joint . Pin offset retical modelling. The 5083-H116 aluminium alloy and pure copper were successfully friction-stir-welded by offsetting the pin to the aluminium side and controlling the FSW parame- ters. A theoretical analysis is presented along with key find- 1 Introduction ings. The process temperatures are predicted analytically using the inverse heat transfer method and correlated with The joining of dissimilar materials is becoming increasingly experimental measurements. The temperature distribution in important in industrial applications [1]. Many emerging ap- the immediate surroundings of the weld zone is investigated plications such as power generation, chemical, petrochemical, together with the microstructures and mechanical properties of nuclear, aerospace, transportation and electronic industries the joint. This was supported by a finite element analysis using require the joining of dissimilar materials using different COMSOL Multiphysics. In this study, two rotational speeds methods, especially friction welding and friction stir welding were used and a range of offsets was applied to the pin. The [2]. Due to the different chemical, mechanical and thermal microstructure analysis of the joints was undertaken. This properties of materials, the joining of dissimilar materials revealed some particles of Cu inclusion in the nugget zone. presents more challenges than joining similar materials. The energy dispersive spectroscopy showed a higher diffusion Kimapong and Watanabe [3] carried out experiments in rate of aluminium towards the interface while copper main- welding aluminium alloy 5083 to mild steel. They investigat- tained a straight base line. ed the effects of pin rotation speed and the position of the pin axis on the tensile strength and microstructure of the joint. In their study, maximum tensile strength was obtained when the pin offset was 0.2 mm towards the steel. With large offset, the A. O. Al-Roubaiy steel fragments scattering in the aluminium alloy matrix be- Materials Engineering Department, College of Engineering, Babylon University, Babylon, Iraq come larger in size leading to the formation of voids. e-mail: [email protected] However, when joining dissimilar materials using friction stir welding (FSW), the problems arise not only from a mate- S. M. Nabat rial properties point of view but also from the possibility of the Materials Engineering Department, College of Engineering, Kufa University, Kufa, Iraq formation of brittle inter-metallic phases and low melting e-mail: [email protected] point eutectics. The inter-metallic compounds in an Al–Cu system were found in the friction welding of the oxygen-free * A. D. L. Batako ( ) copper to pure aluminium and in the cold roll welding of Al/ GERI, Liverpool John Moores University, Byrom Street, Liverpool L3 3AF, UK Cu bimetal [2]. FSW has a greater potential of making high- e-mail: [email protected] quality welds with dissimilar material compared to fusion Author's personal copy Int J Adv Manuf Technol welding. However, previous studies indicated that few sound observed that very low or very high welding temperatures dissimilar FSW joints were obtained. led to joint defects. In their work, the inter-metallic com- Cu–Al joints are inevitable in certain applications due to pounds and their effects on the mechanical properties of the unique performances such as higher electric and heat conduc- joints were investigated. The best joint tensile shear properties tivity, corrosion resistance and mechanical properties. were achieved at the rotational speed of 825 rpm and welding Consequently, Al and Cu are replacing steel in electricity speed of 32 mm/min. supply systems due to their higher electric conductivity [4] Galvão et al. [12] analysed and compared the influence of in heat exchangers and various types of components in elec- the welding conditions on the evolution of the torque during trical machinery to obtain lightweight products [5]. One of the similar and dissimilar friction stir butt welding of 5083-H111 difficulties in Al–Cu joints is that the Al easily oxidizes at aluminium alloy and copper. They observed that the average elevated temperature. Welding cracks are also observed in torque is strongly affected by the materials to be welded, joints created by brazed or fusion of Al–Cu. Therefore, a since, for all welding parameters, the lowest average torque high-quality weld joint of Al–Cu is difficult to obtain by values were registered during dissimilar welding. Some dif- means of conventional welding methods [6]. ferences in instantaneous torque evolution, during welding, Li et al. [7] studied the microstructure and mechanical were observed depending on base material combinations. A properties of the weld joint where pure copper was welded strong fluctuation in instantaneous torque was registered in to 1350 aluminium alloy by FSW. They observed that the dissimilar welding with the copper at the advancing side. This hardness in the copper side was higher than the aluminium was related with the large inter-metallic content in the welds. side. They also showed that there were no inter-metallic Genevois et al. [13] investigated the joining of A1050 formations in the interface between the copper and alumini- aluminium alloy with commercially pure copper by friction um. Their work revealed a mixed ductile fracture during stir welding. The pin tool was located exclusively on the Al tensile tests of the joints. side, and there was no mixing of either material through the Galvao et al. [8] investigated the influence of the FSW weld. The bonding resulted only from the reactive inter- process parameters on the formation and distribution of inter- diffusion; therefore, this process is named friction stir diffu- metallic phases at the interface of the joint between the copper sion bonding. The reactive inter-diffusion of Al and Cu led to and aluminium. Their work pointed out that under lower heat the formation of a very thin layer (200 nm) of inter-metallic input, only a thin inter-metallic layer distribution along Al/Cu compounds at the Al/Cu interface. The analysis of the micro- interface was formed inside the nugget. They reported that structure indicated that this thin layer was formed after the increasing the heat input promoted material mixing and the stirring action of the tool pin. Two inter-metallic compounds formation of increasing amount of a rich inter-metallic were detected, namely the Al2Cu (θ)andAl4Cu9 (γ) phases. structure. Lambrakos et al. [14] used an inverse problem approach to Lui et al. [9] used a butt barrier method to achieve a better the analysis of friction stir welding where they used thermo- appearance of the weld. Their work showed that the voids in couple measurements as input information. The calculated the weld decreased with the increase of the pin rotational temperature field is scaled according to the peak temperature speed (1,000 rpm). However, this improvement reached a measured by a thermocouple at a specific point on the bottom critical speed (1,500 rpm) where the voids began to increase. surface of the workpiece. Xue et al. [10] investigated the effect of welding parameters In this paper, high-quality Al–Cu joints were successfully on mechanical properties, the interface microstructure and achieved by offsetting the pin to the Al side and controlling surface morphology for butt joining of 1060 aluminium alloy the FSW parameters. The microstructures and mechanical and pure copper. They obtained a good defect-free joint only properties of the obtained joints were investigated. The pur- when the hard Cu plate was fixed at the advancing side. A pose of this work is to study the capability of joining Al–Cu large volume defect was observed when the soft Al plate was and the effect of FSW parameters on the quality of the joint. placed at the advancing side. Their experiments also obtained The distribution of the temperatures and the heat flux during good defect-free joints under large pin offsets of no less than this process is also investigated. 2 mm to the Al matrix. A good metallurgical bonding between the Cu bulk/pieces and Al matrix was achieved. Bisadi et al. [11] studied FSW for joining sheets of 2 Experimental procedures AA5083 aluminium alloy with pure copper and the effects of process parameters including rotational and welding speeds Aluminium alloy (5086-H116) and pure copper (99.972 % on the microstructures and mechanical properties of the dif- purity) plates were butt-welded using an AJAX universal ferent joints.
Details
-
File Typepdf
-
Upload Time-
-
Content LanguagesEnglish
-
Upload UserAnonymous/Not logged-in
-
File Pages14 Page
-
File Size-