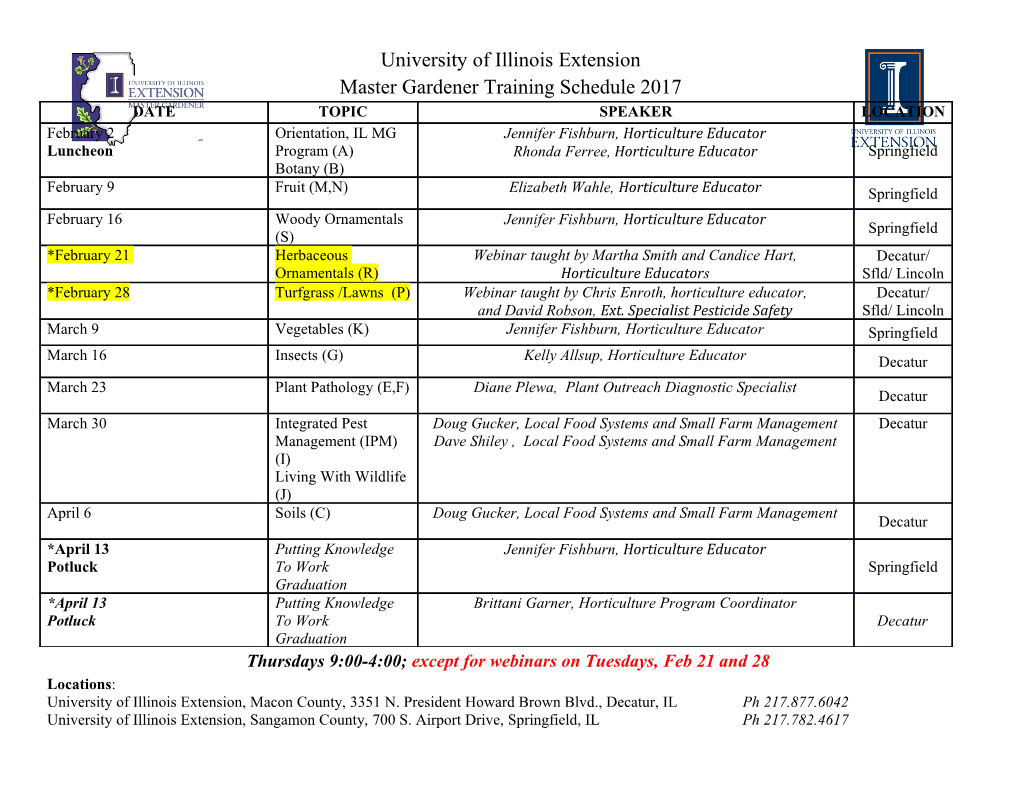
Liquid EPDM Dispersion iquid ethylene propylene Recently, formulations Additionally, industrial In recent studies, three diene rubber (L-EPDM) blending the L-EPDM heat-cure formulations have coating formulations from Lhas been known in the (Figure 1) with other com- been developed for a broad a commercially available coatings industry for many mon coatings resins have range of temperatures. This low-molecular-weight liquid years. These elastomers have been developed. Elastomeric paper will discuss L-EPDM EPDM (L-EPDM) were found utility in ambient cure acrylics, alkyds and polyure- waterborne suspension and demonstrated; a peroxide liquid-applied roof coatings. thanes have been blended blend properties, coating crosslinking mechanism and These resins, formulated into with the L-EPDM without formulation, application and a sunshine UV crosslinking waterborne liquid coatings, the use of compatibiliz- curing methods, and final mechanism, and a dual-cure may be cured with peroxides, ers. Each of these systems film properties. system that uses both perox- metal driers, or UV radiation has seen unique property ide and UV.3,4,5 and can be used in ambient improvements, such as These formulations all maintenance coatings for flat surface wetting, adhesion, INTRODUCTION generate good EPDM rubber or low-slope roofs. impact strength, and more. Ethylene-Propylene Diene properties after crosslinking, (EPDM) rubber has been including high mechanical used extensively in auto- strength, low-temperature motive, wire and cable, flexibility, hydrophobic- roof membrane, and ther- ity, and adhesion to polar moplastic vulcanite (TPV) substrates. The formulations applications because of the meet industrial requirements ease of processing due to the as protective coatings in solid polymer’s unique structure.1,2 content, rheology, curing Many of the properties of speed, shelf life, pot life, and EPDM, notably, ozone and can be produced at a cost UV resistance, low-moisture consistent with commercial permeability, and excellent elastomeric acrylic coatings. high- and low-temperature These coatings were also properties, make it an ideal formulated to be used as material for exterior coatings. liquid roofing membranes PHOTO COURTESY OF LION ELASTOMERS COURTESY PHOTO By Gregory J. Brust and John D. Jacquin Liquid EPDM Dispersion Lion Elastomers and showed improved When blended with surfac- dispersion with commer- coatings resins. Several performance over solid tants and dispersed in water cially available elastomeric new formulations using this EPDM sheets and elasto- at 50–55 wt % solids, it is acrylics, improved wetting dispersion are also discussed, meric acrylic coatings in designated T65D. Properties over low-energy substrates including direct to metal and terms of ease of installation, of T65D are shown in Table and in increase in tensile high temperature industrial solar reflectance, water 1. The paths to formulating modulus is achieved. coatings. New formulations resistance, and weather a peroxide-cured, a sun- This work demonstrates using the L-EPDM dispersion durability. shine-UV cured, and an oxi- the ability of this L-EPDM as a co-binder with waterborne A previous paper reported datively cured system were dispersion to be blended with acrylates and alkyds are also on a waterborne dispersion discussed. The mechanical other common waterborne presented. of L-EPDM used for coatings properties approach their and adhesives.6,7 L-EPDM solventborne counterparts. TABLE 1—Typical Properties of T65D dispersion used in this study These low-VOC coatings is Trilene® 65D (T65D). T65 retain the low-temperature Property Standard Typical Value is a low-molecular-weight flexibility, hydrophobicity, Appearance Milky white polymer of EPDM consisting excellent adhesion, and Weight solids (%) in water ASTM D3960 50–55 of 45 wt % ethylene, 45 wt % low-water vapor transmis- Brookfield Viscosity (cP @ 25 °C) ASTM D2196 5,000–8,000 propylene, and 10 wt % dicy- sion. It was also shown that pH Value (@ 25 °C) ASTM D7946 8–9 clopentadiene monomers. by blending this L-EPDM Specific Gravity (g/cc @ 25 °C) ASTM D4052 0.95 Propylene Content (wt %) ASTM D3960 45 FIGURE 1—Simplified Structure of L-EPDM Dicyclopentadiene (wt %) 10 VOC (g/l) 0 Typical particle size (microns) 1-2 Mw ~47,000 Tg (C) DSC -47 Solids wt loss (% @ 400 °C in air) TGA 10 APEO Not present Shelf life (years) 2 ©ADOBESTOCK | WHITE78, GRISPB, VIDEO-STOCKORG, TK New Waterborne Coatings Formulations With Liquid EPDM Dispersion EXPERIMENTAL The pigment and polymer mixtures, All tests were conducted following ASTM where applicable, were then allowed standards with standard lab equipment. Blending L-EPDM Dispersion sufficient mixing at 1,000 rpm to form a Each coating was applied to desired with Other Binders final smooth liquid paint. Coatings were substrates including cold-rolled steel T65D was weighed into a 100g MAX allowed to equilibrate for 1 week at room (CRS), Lineta charts, and release paper, SpeedMixer cup. An amount of temperature before testing. The paint using a Gardco® wet-film applicator co-binder was then weighed into the properties were then measured for spe- to 0.2–0.5 mm thickness. Dry times cup to produce a 10 wt % co-binder to cific gravity, solid content and viscosity. for formulations in Tables 2–4 were theL-EPDM blend. Samples were mixed at 2,000 rpm with a FlackTek high- TABLE 2—Co-Binders Used for Blends with T65D speed mixer until a homogenous disper- Material Type Manufacturer sion was formed. Of this blend, 10–15 g was transferred to a glass vial for Rovene® 6120 100% Acrylic latex Mallard Creek Polymers stability testing. An additional amount Acronal® PLUS 4230 Acrylonitrile-acrylic latex BASF of co-binder was added to the remaining UCAR® 3176 A Styrene-acrylic latex Dow Chemical blend to prepare a 20 wt % blend. Rhoplex® 2100-EC Styrene-acrylic latex Dow Chemical This process was repeated for blends Beckosol® AQ 206 Alkyd latex Polynt in 10 wt % increments up to 90 wt % 5060-BC-70 Water-reducible alkyd Gabriel Hexamethoxymethyl-melamine- co-binder. No attempt was made to Resimine® 745 Prefere Melamines compatibilize the blends with added formaldehyde resin High-imino methylated melamine- surfactants. Samples were left undis- Resimine AQ7551 Prefere Melamines turbed at ambient conditions for 3 formaldehyde resin months to watch for separation/desta- Urotuf® F108 Polyurethane dispersion Polynt bilization. Co-binders used in this paper Urotuf F982 Polyurethane dispersion Polynt included acrylic, acrylonitrile-acrylic, Styrofan® 4215 Carboxylated SBR latex BASF Denka Performance and styrene acrylic latexes, alkyd latex, Neoprene Latex Polychloroprene latex and water-reducible alkyd, melamine Materials formaldehyde resins, polyurethane Michem® dispersion Maleated polypropylene wax dispersion Michelman dispersions, carboxylated styrene-buta- diene, chloroprene rubber latexes, and TABLE 3—Clear Coating Formulation wax dispersions. Co-binder product Ingredient Material Manufacturer grams names can be found in Table 2. Trilene® 65D EPDM dispersion Lion Elastomers 58.51 Coating Formulation and Testing Mineral Spirits Coalescing solvent 2.60 Ricon® 156 Liquid polybutadiene Cray Valley 0.52 Tables 3–7 list the formulations used in SR-350 TMPTMA Crosslinker Sartomer 1.56 this study. Table 3 is a clear formula- 10% Co Hydro-Cure IV Metal drier catalyst Borchers 0.13 tion. Table 4 is a T65D modified-acrylic 12% Zr Hydro-Cem Metal drier catalyst Borchers 0.71 coating. Table 5 presents a series of Halox® FlashX® 150 Rust Inhibitor ICL Phosphate Specialty 0.32 T65D modified-alkyd coatings. Tables 6 Total 64.35 and 7 show peroxide-initiated, heat- cured T65D formulations for industrial coatings. TABLE 4—Pigmented, 65:35 Acrylic:T65D Modified Coating Formulation For all pigmented formulations, dis- persant was dissolved in water before Ingredient Material Manufacturer grams pigment was added. This was then Trilene® 65D EPDM Dispersion Lion Elastomers 85.7 mixed at 2,000 rpm with a FlackTek Rovene® 6120 Pure acrylic emulsion Mallard Creek Polymers 151.2 high-speed mixer until a homogenous Mineral Spirits Coalescing solvent 3.8 dispersion was formed. Catalysts or Ricon® 156 Liquid polybutadiene Cray Valley 0.8 peroxides, if used, were then added to SR-350 TMPTMA crosslinker Sartomer 2.3 the pigment dispersion, and mixed a 10% Co Hydro-Cure IV Metal drier catalyst Borchers 0.2 further 2 minutes. Crosslinkers and 12% Zr Hydro-Cem Metal drier catalyst Borchers 1.0 coalescing solvents were mixed in a DI H2O Diluent 47.7 scintillation vial until fully dissolved, DisperBYK® 2055 Pigment dispersant BYK 3.2 and then added to the L-EPDM polymer Atomite EP7705 Calcium carbonate filler Eager Polymers 77.5 dispersion or T65D:co-binder blend and Ti-Pure® R-706 TiO2 pigment Chemours 68.9 mixed at 2,000 rpm with a FlackTek high-speed mixer until a uniform mix- ZnO Pigment U.S. Zinc 19.9 ture was achieved. Total 462.2 50 | AUGUST 2021 measured following ASTM D1640 using oven for 15–30 minutes. The 50:50 sample was removed from each oven every a Gardco Ultracycle dry-time recorder formulation from Table 4 was also cured 5 minutes to check degree of cure. and then allowed to cure indoors at at 60 °C and 80 °C for 1 hour with a dry After drying, the coating film was ambient conditions for 7 days to achieve timer. The formulation in Table 6 was used to measure physical properties final properties before testing. coated in triplicate and placed in an including pencil hardness, crosshatch Formulations in Table 5 were placed
Details
-
File Typepdf
-
Upload Time-
-
Content LanguagesEnglish
-
Upload UserAnonymous/Not logged-in
-
File Pages9 Page
-
File Size-