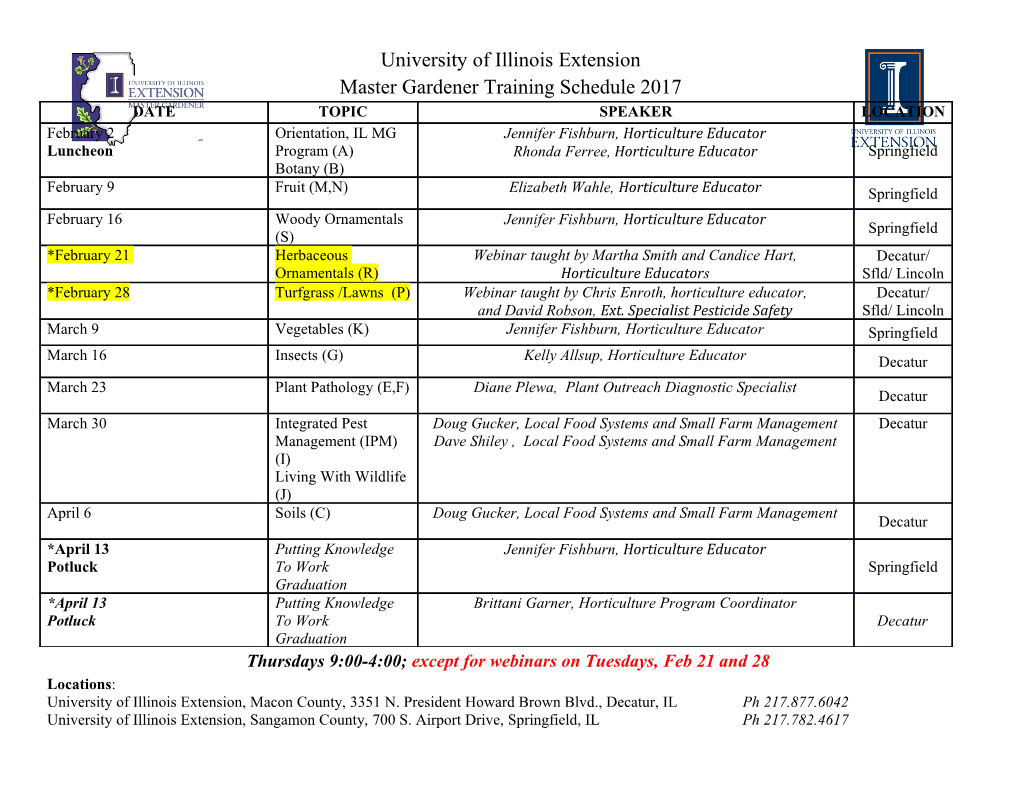
Europaisches Patentamt J) European Patent Office ® Publication number: 0 1 38 531 B1 Office europeen des brevets ® EUROPEAN PATENT SPECIFICATION (§) Date of publication of patent specification: 27.01.88 © Int. CI.4: C 23 G 1/10, C 23 G 1/36, C 23 F 1/18, C 25 F 7/02 (2p/av ApplicationA , - number: 84306812.3 (22) Date of filing: 05.10.84 (§) Process for cleaning copper base materials and regenerating the cleaning solution. (30) Priority: 06.10.83 US 539598 (7$) Proprietor: Olin Corporation 427 North Shamrock Street East Alton Illinois 62024 (US) (43) Date of publication of application: 24.04.85 Bulletin 85/17 ® Inventor: Pryor, Michael J. 98 Maplevale Drive (Ji) Publication of the grant of the patent: Woodbridge Connecticut 06410 (US) 27.01.88 Bulletin 88/04 Inventor: Brock, Andrew J. 44 Royalwood Court Cheshire Connecticut 06410 (US) (§4) Designated Contracting States: DE FR GB IT (74) Representative: Lambert, Hugh Richmond et al D. YOUNG & CO. 10 Staple Inn (58) References cited: London, WC1V7RD (GB) EP-A-0 082 210 US-A-3470 044 US-A-3 671 344 CQ CO in oo CO Note: Within nine months from the publication of the mention of the grant of the European patent, any person may give notice to the European Patent Office of opposition to the European patent granted. Notice of opposition shall Q. be filed in a written reasoned statement. It shall not be deemed to have been filed until the opposition fee has been LU paid. (Art. 99(1) European patent convention). Courier Press, Leamington Spa, England. D 138 531 Description This invention relates to a process for cleaning copper base alloys using an aqueous peroxydisulfuric acid solution and for regenerating the spent cleaning solution. 5 The fundamental cleaning medium used in the copper industry is sulfuric acid at a strength of about 10 to 15% by volume. The extensive use of sulfuric acid is based on the fact that for most brasses and high copper alloys, the annealing oxides are readily soluble in mineral acids. This produces very rapid oxide removal and the resulting cleaning process is, therefore, readily amenable to a short immersion time, continuous operation. 10 However, an increasing number of copper alloys now contain elements which form insoluble, refractory-type oxides. For these alloys, alternative cleaning procedures have been developed. These alternative cleaning procedures generally involve adding an oxidant such as sodium dichromate or hydrogen peroxide to the cleaning solution. While sodium dichromate has been used effectively for years, its use has been discontinued because of its known high toxicity and restrictions on waste treatment and 15 discharge level. While hydrogen peroxide does not suffer from these disadvantages, it is limited by its inherent stability problems. Hydrogen peroxide will decompose to water plus oxygen during storage. In addition and more importantly, the decomposition of peroxide is greatly accelerated by elevated temperatures and/or the presence of dissolved copper in the cleaning solution. These factors limit the maximum etching rates that can be obtained with solutions containing hydrogen peroxide. 20 In response to these shortcomings and the need for an effective oxidising cleaning solution, attention has turned to persulfate solutions. The use of persulfate is attractive for a copper cleaning operation because the end products of the reaction of persulfate with copper are sulfuric acid and copper sulfate. As such, no special waste water treatment is required. Furthermore, the depleted or spent persulfate solution may be regenerated and the copper in the depleted solution reclaimed. Typically, the persulfate cleaning 25 solutions comprise an aqueous solution containing a persulfate salt such as ammonium persulfate or sodium persulfate. Persulfate salts have been used because they are readily available. U.S. Patent Nos. 2,978,301 to Margulies et al., 3,475,242 to Radimer, 3,671,344 to Chiang et al., 3,887,405 to Fong et al. and 4,144,144 to Radimer et al. illustrate the use of aqueous persulfate salt solutions to etch copper materials. The use of electrochemical cells to regenerate spent solutions and to reclaim metal values from the 30 spent solutions are well known in the art. Typically, these cells have at least one anode chamber and at least one cathode chamber physically separated by a membrane. Depending upon the type of solution being regenerated and the chemical reactions sought to be produced, the membrane generally comprises either an ion exchange member or a microporous separator. The spent solution is used as either the anolyte or the catholyte. U.S. Patent Nos. 2,748,071 to Eisler, 2,865,823 to Harris et al., 3,761,369 to Tirrell, 35 3,764,503 to Lancy et al., 4,051,001 to Inoue et al., and 4,149,946 to Burke illustrate some of the electrochemical cells to regenerate the spent cleaning solutions. It has been suggested in the prior art to regenerate persulfate etchants using electrochemical cells. In one such persulfate etchant regeneration technique, the spent etchant is treated to remove a substantially persulfate-free mixture containing ammonium persulfate and the corresponding metal sulfate. The 40 substantially persulfate-free mixture is then transferred to the cathode chamber of an electrochemical cell where it is used as the catholyte. The remainder of the spent solution is transferred to the anode chamber of the cell where it is used as the anolyte. The cathode and anode chambers of the cell are separated by a diaphragm which permits at least hydrogen ions to pass freely between the anolyte and the catholyte while preventing any substantial amounts of persulfate in the anolyte from mixing with the catholyte. By passing 45 an electric current between the anolyte and catholyte, metal is plated out of the cathode and persulfate values are produced at the anode. U.S. Patent No. 3,406,108 to Radimer et al. illustrates this technique for regenerating spent persulfate etchants. The primary deficiency of this technique is its complexity which renders it commercially unacceptable. A second and simplertechnique is illustrated in U.S. Patent No. 3,470,044 to Radimer. In this technique, 50 the spent aqueous ammonium persulfate etching solution is used as the anolyte or an electrochemical cell. An electrolyte such as an acidic bisulfate or a Jpisulfate containing electrolyte is used as the catholyte of the cell. The cathode and anode sections of the cell are separated by a cathodic exchange membrane which permits the dissolved metal ions to pass from the anolyte into the catholyte but which prevents any substantial amount of persulfate in the anolyte from mixing with the catholyte. By passing an electric 55 current through the catholyte and the anolyte, dissolved metal is removed from the solution at the cathode and sulfate values are converted to persulfate values at the anode. While simpler, this second technique is believed to be inefficient and commercially unacceptable. The production of temperature sensitive, oxidizing cleaning solutions such as persulfate etchants often require electrolyte temperatures to be maintained within certain critical limits during processing. Therefore, an 60 electrochemical cell for regenerating such a temperature sensitive solution should have some means for controlling electrolyte temperature. Furthermore, special anodes are often required to improve cell efficiency. Such temperature control means and special anodes are known in the art. U.S.S.R. Patent Nos. 311,502 and 470,307 both to Markov et al. illustrate some special anode constructions. In accordance with the present invention, a relatively simple but yet highly efficient process for 65 cleaning copper base materials is provided. The copper base material is cleaned by immersion in an 2 0 138 531 aqueous peroxydisulfuric acid solution containing peroxydisulfuric acid in a concentration in the range of about 1 N to about 5N, preferably from about 1 .5N to about 2.5N. The cleaning of the copper base material is carried out with the solution having a temperature in the range of about 15°C to about 30°C, preferably from about 20°C to about 25°C. 5 As the amount of copper dissolved in the cleaning solution increases and/or the amount of peroxydisulfuric acid becomes substantially depleted, the etching rate or cleaning power of the solution decreases. When the cleaning power or etching rate of the solution reaches a level where it is no longer feasible to clean the copper base material within commercial time constraints, the solution is withdrawn from the cell and replaced by a fresh cleaning solution. Thereafter, the withdrawn spent cleaning solution is w recirculated to an electrolytic cell for regeneration. In accordance with the present invention, the spent cleaning solution is introduced into the anode chamber of the electrolytic cell for use as an anolyte. An aqueous sulfuric acid solution containing from about 10% to about 50%, preferably about 15% to about 25%, by volume sulfuric acid is introduced into each cathode chamber of the cell as a catholyte. The anode chamber is preferably separated from each 15 cathode chamber by a membrane-type structure. By applying an electric current across the cell, copper from the spent or depleted cleaning solution is plated out at the cathode and sulfate ions are oxidized to persulfate ions at the anode. It has been found that overall efficiency of the cell can be increased by making a halide addition to the anolyte. Depending upon the halide used, the addition would be in the range of about 10 ppm to about 500 20 ppm. For example, the halide addition may be either from about 100 ppm to about 200 ppm of a chloride such as hydrochloric acid or from about 50 ppm to about 100 ppm of a fluoride such as hydrofluoric acid.
Details
-
File Typepdf
-
Upload Time-
-
Content LanguagesEnglish
-
Upload UserAnonymous/Not logged-in
-
File Pages13 Page
-
File Size-