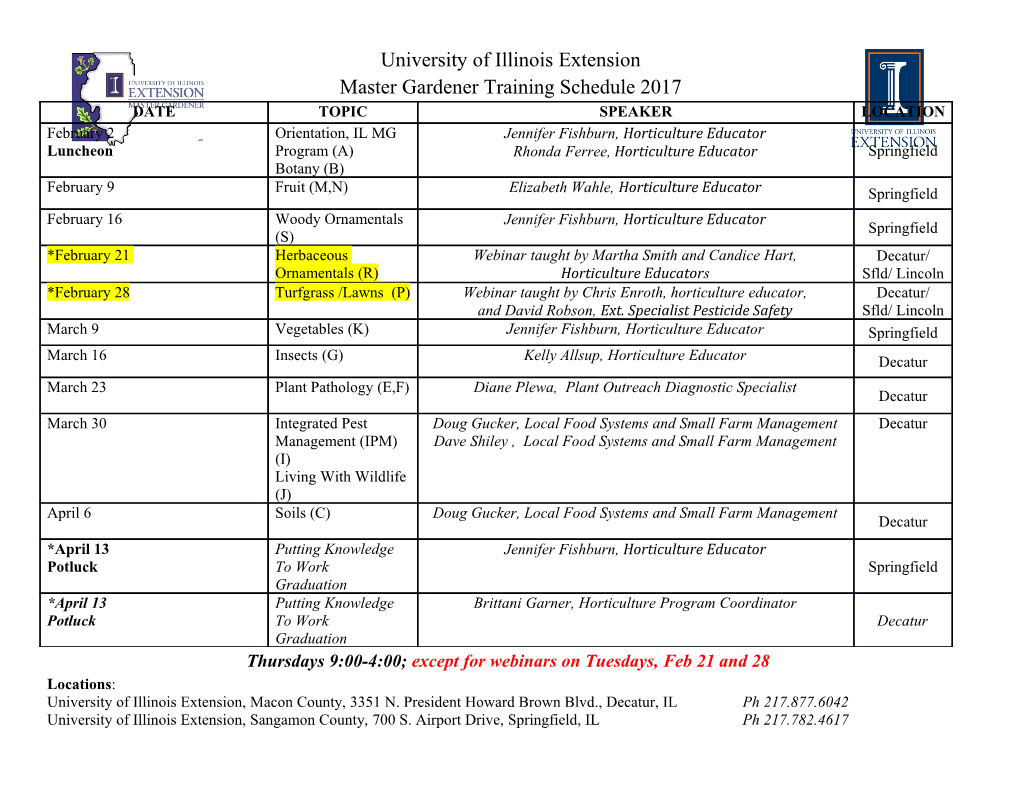
Journal of Advanced Mechanical Design, Vol. 4, No. 1, 2010 Systems, and Manufacturing Optimum Design of Thrust Air Bearing for Hard Disk Drive Spindle Motor* Mohd Danial IBRAHIM**, Tadashi NAMBA**, Masayuki OCHIAI*** and Hiromu HASHIMOTO*** **Graduate School of Science and Engineering, Tokai University 1117, Kitakaname, Hiratsuka City, Kanagawa Prefecture 259-1292, Japan E-mail: [email protected] *** Depatment of Mechanical Engineering, Tokai University 1117, Kitakaname, Hiratsuka City, Kanagawa Prefecture 259-1292, Japan Abstract This paper describes the application of geometry optimization method proposed by Hashimoto to the design of air lubricated thrust bearings used for HDD spindle motors. The optimization is carried out to maximize the dynamic stiffness of air films because the low stiffness is a serious problem of thrust air bearings in the actual application to HDD spindle motor. The optimized dynamic stiffnesses are obtained by changing the allowable film thickness, which is corresponding to the tolerance of bearings. The results obtained show that the optimized thrust air bearings have the comparable stiffness to the oil lubricated thrust bearings and it is verified theoretically that this type of thrust air bearing can be used for HDD spindle motors. Key words: Hard Disk Drive, Spindle Motor, Thrust Air Bearing, Geometrical Optimum Design, Bearing Stiffness 1. Introduction Hard disk drive (HDD) has been playing a big role in the area of informative multimedia as the main storage media for electronics devices. The back bone of these media storage technology actually lies in the revolutionary part of the spindle motor supported mainly by the oil lubricated thrust and journal bearings. Among various types of thrust bearings used in HDD spindle motors, spiral and herringbone types of grooved bearings are widely used. Although oil lubricated thrust bearing has high dynamic stiffness compared to air lubricated thrust bearing, it is not an exaggeration to say that the current commercialized oil lubricated thrust bearings are coming to its limit where high rotational speed leads to high friction losses, wear, seal problems due to oil leakage, oil contaminations and degradations, as explained by Landsdown(1). The air lubricated thrust bearing which has lower friction losses has a higher probability for reducing the total power consumption, as it poses low environmental load. Furthermore, the air lubricated thrust bearing does not have sealing problems, and its oil-less design makes it a maintenance free equipment. Therefore, high speed air lubricated thrust bearing with high dynamic stiffness and low friction torque is strongly expected to be the next most applicable thrust bearing. Several investigators(2)~(7) tried to analyzed the thrust bearing characteristics for HDD spindle. Most of these papers treated the oil lubricated thrust bearings. Regarding to air lubricated thrust bearings, Xue and Stolarski(8) analyzed the performance of air lubricated spiral groove thrust bearings using the control (9) volume method. Zhang et. al proposed a spindle motor for 3.5" HDD with a combination *Received 3 Aug., 2009 (No. 09-0424) [DOI: 10.1299/jamdsm.4.70] of herringbone type grooved thrust and journal air bearings, in which spindle designs were Copyright © 2010 by JSME considered with a very severe tolerance of 0.5µm to improve bearing stiffness. Despite that 70 Journal of Advanced Mechanical Design, Vol. 4, No. 1, 2010 Systems, and Manufacturing there were only few researches regarding air lubricated thrust bearings in HDD, most of the researches only focus on the available conventional groove geometries such as spiral or herringbone groove as the subject to improve the bearing stiffness. Hashimoto et. al(10),(11) originally developed the optimization method to maximize the dynamic stiffness of air lubricated thrust bearings, but there is no application example of this model for HDD spindle motor. In this paper, a new application of Hashimoto’s method to design an optimal groove geometry for thrust air bearing used for HDD spindle motor is described, and some numerical examples of optimized results were presented. 2. Nomenclature b1 : groove width [m] b2 : land width [m] c : damping coefficient of air film [N·s/m] f (X) : objective function gi(X) : constraint functions; (i =1~16) ha : allowable film thickness [m] hg : groove depth [m] hr : flying height (gap between shaft and lower groove surface) [m] hu : gap between shaft and upper groove surface [m] K : dynamic stiffness of fluid film [N/m] k : spring coefficient of fluid film [N/m] N : groove number ns : rotational speed of spindle [rpm] Pa : atmospheric pressure [Pa] p0 : static component of fluid film pressure [Pa] pt : dynamic component of fluid film pressure [Pa] ri(i =1 ~ 4) : coordinate of radius direction [m] Rout : bearing outer radius [m] Rin : bearing inner radius [m] Rs : seal radius [m] rs : seal ratio; ( = Rs /R out ) Δr : divided divisions of radius [m] Tr : frictional torque on the bearing surface [N·m] W : load capacity [N] X : vector of design variables α : groove width ratio; (=b1 /(b1+ b2)) β : air inflow angle [deg] δ : gap between shaft and upper and lower groove surface [m] μ : viscosity of lubricant [Pa·s] θ : circumference direction of coordinate [deg] ξ : radial coordinate of groove geometry η : angular coordinate of groove geometry Φ : phase angle [deg] th φi : groove geometry design parameter; (displacement for i point of shift from the initial groove geometry to a new point ) [deg] ωd : natural damped frequency [rad/s] ωf : squeeze frequency of shaft revolution [rad/s] ωs : shaft angle velocity [rad/s] Subscripts max : maximum value of stated variables min : minimum value of stated variables 71 Journal of Advanced Mechanical Design, Vol. 4, No. 1, 2010 Systems, and Manufacturing 3. Formulation of Optimum Design and Vibration Analysis 3.1 Modification Method of Groove Geometry In this paper, the initial groove geometry of thrust air bearing is flexibly modified using the cubic spline interpolation function. The cubic spline function is a cubic polynomial equation in each section of (ri, ri+1) (i=1,2,…,n). The condition required for the cubic spline function is a continuity of a second order derivative of the function at each nodal point. The cubic spline interpolation function is expressed as the following equation. θ" (r ) 3 θ" (r ) 3 θ()r = i ()r − r + i+1 ()r − r 6Δr i+1 6Δr i (1) ⎛ θ" ()r Δr 2 ⎞ r − r ⎛ θ" ()r Δr 2 ⎞ r − r + ⎜θ r − i ⎟ i+1 + ⎜θ r − i+1 ⎟ i ⎜ ()i ⎟ ⎜ ()i+1 ⎟ ⎝ 6 ⎠ Δr ⎝ 6 ⎠ Δr Considering that θ˝(ri) = 0 for i = 0 and i = n+1, θ˝(ri) (i=1~n) are given as follows; ⎡ 2 1 2 ⎤ ⎡θ" ()r1 ⎤ ⎢ ⎥ ⎡d1 ⎤ ⎢ ⎥ 1 2 2 1 2 ⎢ ⎥ θ" ()r ⎢ ⎥ d θ" = ⎢ 2 ⎥ = A−1d , A = ⎢ % % % ⎥ , d = ⎢ 2 ⎥ (2) ⎢ # ⎥ ⎢ ⎥ ⎢ # ⎥ ⎢ ⎥ 1 2 2 1 2 ⎢ ⎥ θ" r ⎢ ⎥ d ⎣ ()n ⎦ ⎢ ⎥ ⎣ n ⎦ ⎣ 1 2 2 ⎦ where d in Eq. (2) is expressed as the following. 1 d = 2θ" ()r + θ" ()r (3) 1 1 2 2 3()θ(r )−2θ(r )+θ(r ) d = i−1 i i+1 ()i = 2,3,",n −1 (4) i Δr 2 1 d = θ" ()r + 2θ" ()r (5) n 2 n−1 n An arbitrary groove geometry can be represented by finding the spline function in all sections of the target groove geometry by using Eqs.(1) and (2). 3.2 Governing Equations for Optimization Figure 1 shows an overview of a HDD spindle motor, which is supported by a combination of thrust and journal bearings. Figure 1(a) illustrates a typical HDD structure being considered in this paper which is made of a combination of clamped upper and lower surfaces of thrust bearings shown in Fig. 1(b). Figure 2 shows the initial groove geometry and feasible region for optimum design of the thrust air bearing treated in this paper. In the optimization, the initial geometry is selected as a spiral groove as shown in Fig. 2(a), and the feasible region is divided into four regions in the radial direction as shown in Fig. 2(b), because there is insignificant effect on the optimized results for the number of regions over four. In formulating the optimum design problems on groove geometry, the design variable vector X, consisting of the angle variation φi (i=1~4) in the circumferential direction from the initial geometry to k-th step geometry as shown in Fig. 2(b) and the other bearing dimension parameters rs, hg , and α, are defined as follows. 72 Journal of Advanced Mechanical Design, Vol. 4, No. 1, 2010 Systems, and Manufacturing X = (rs ,hg ,α,ϕ1 ,ϕ2 ,ϕ3 ,ϕ4 ) (6) As can be seen from Fig. 2(b), in the optimization process, the most inner point of the curve is fixed, the groove geometry is gradually evolved to optimize the later mentioned objective function from initial stage to the final stage, and the groove geometry is revised step by step using the cubic spline interpolation function. In order to design the thrust air bearing and apply it to the current commercialized HDD, the bearing design parameters have to be constrained with some restrictions based on the total specification of a HDD characteristic. The constraint conditions are shown in the following; gi ()X ≤ 0 (i =1~ 16) (7) where the constraint functions in Eq.(7) are defined as follows. g1 = rs min − rs , g 2 = rs − rs max , ⎫ ⎪ g3 = hg min − hg , g 4 = hg − hg max , ⎪ ⎪ g5 = α min − α , g 6 = α − α max , g 7 = ϕ 1min − ϕ1 , ⎪ ⎬ (8) g8 = ϕ1 − ϕ1max , g9 = ϕ 2min − ϕ 2 ,g10 = ϕ 2 − ϕ 2max , ⎪ g = ϕ − ϕ , g = ϕ − ϕ , g = ϕ − ϕ ,⎪ 11 3min 3 12 3 3max 13 4min 4 ⎪ ⎪ g14 = ϕ 4 − ϕ 4 max , g15 = ha − hr , g16 = −c ⎭ Thrust bearing Shaft Journal bearing (a) Overview of a spindle motor (b) Initial spiral grooved thrust bearing Fig.
Details
-
File Typepdf
-
Upload Time-
-
Content LanguagesEnglish
-
Upload UserAnonymous/Not logged-in
-
File Pages12 Page
-
File Size-