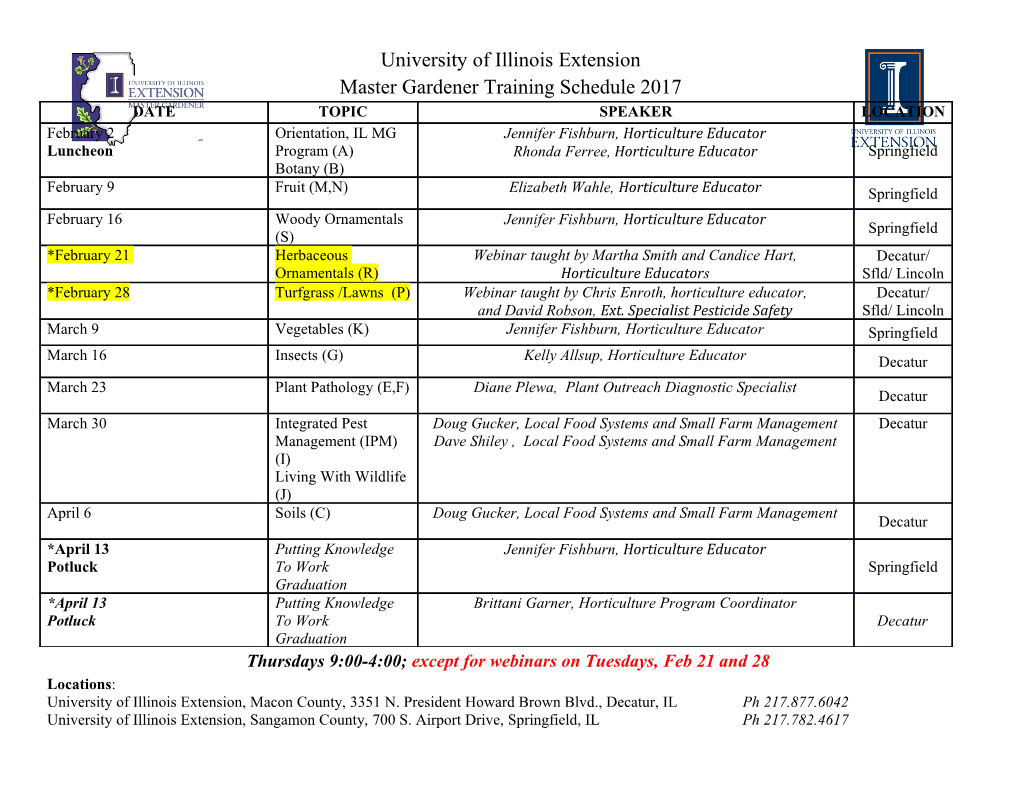
Europaisches Patentamt 0 091 393 J) European Patent Office Publication number: B1 Office europeen des brevets EUROPEAN PATENT SPECIFICATION into.4: G 01 M 17/02, G 01 B 11/08, Date of publication of patent specification: 02.11.88 G 01 P 3/60 Application number: 83630053.3 Date of filing: 05.04.83 System for testing a tire to avoid a torque steer effect. Proprietor: THE GOODYEAR TIRE & RUBBER Priority: 05.04.82 US 365593 COMPANY 1144 East Market Street Akron, Ohio 44316-0001 (US) Date of publication of application: 12.10.83 Bulletin 83/41 Inventor: Brown, Jack Edward, Jr. 936 Merriman Road Akron Ohio 44303 (US) Inventor: Dutt, William Randall Publication of the grant of the patent: 139 Hametown Road 02.1 1.88 Bulletin 88/44 Copley Ohio 44321 (US) Inventor: Glemming, David Allen 3630 Portage Point Boulevard States: Akron Ohio 44319 (US) Designated Contracting Inventor: Greenhorn, Richard James DEFRGB 2341 Lynnwood Drive Stow Ohio 44224 (US) Inventor: Heisler, Michael Guy References cited: 221 Asbury Road 089 783 Ithaca New York 14850 (US) GB-A-1 Inventor: Muhl, John Siegfried US-A-4 173 850 3311 Shellhart Road Norton Ohio 44203 (US) Inventor: Vandale, Leonard Albert 1023 Johnston Street Akron Ohio 44306 (US) co Inventor: Winslow, Douglas Lynn 41 Jalan Beka Damansara Heights Kuala Lumpur (MY) CO 0 Representative: Weyland, Joseph Jean Pierre Patent 5> Goodyear Technical Center Luxembourg Department Avenue Gordon Smith o L-7750 Colmar-Berg (LU) o Within nine months from the publication of the mention of the grant of the European patent any person may Note- of shall notice to the European Patent Office of opposition to the European patent granted. Notice opposition give until the fee has been CL be filed in a written reasoned statement. It shall not be deemed to have been filed opposit.on 111 paid. (Art. 99(1 ) European patent convention). Courier Press, Leamington Spa, England. 0 091 393 Description Background of the invention The present invention relates generally to tire testing devices and more particularly to a method of 5 testing a tire in order to reduce the torque steer effect when the tires are used with an automotive vehicle. Torque steer generally refers to an undesirable tendency of an automotive vehicle to move or turn laterally when torque, or thrust, is applied to its driven wheels. Torque is applied, for example, when the vehicle accelerates or decelerates. The torque steer effect is particularly acute in cars that are steered and driven by the same wheels. w "Front wheel drive" vehicles are normally steered and driven by the same wheels and accordingly are influenced by the torque steer effect. In recent years, the number of such cars produced has increased significantly. Overcoming the torque steer effect has thus become increasingly important. One example of a device for measuring the characteristics of a tire is disclosed in US — A — 4,173,850. This prior art patent relates to a method for measuring tangential force variations in pneumatic tires. In the 15 method disclosed in this patent, pneumatic tires are mounted on a wheel rim, inflated to an operating pressure, and rotated under a predetermined load against a loading drum. Force transducers on the axis of the loading drum measure the tangential force variation as the tire rotates. The patent, however, does not mention the measurement of the effective rolling radius of the tire as set forth below. 20 Summary of the invention In attempting to reduce the effect of torque steer. Applicant realized that torque steer could be caused by a variety of additive factors, such as plysteer or the design of the vehicle itself. Applicant also recognized that the radius of a tire could play an important part in avoiding undesired torque steer characteristics. The radius of a static, inflated tire changes as a load, or weight is placed on it. Applicant has noted, 25 however, that knowledge regarding the static, loaded radius of a tire is of only limited importance in attempting to eliminate the torque steer effect. Applicant has ascertained, however, that the radius of a tire also changes as it rotates, and particularly as it rotates under a load. This latter type of radius — the radius of a tire as it revolves under a load — is referred to as the "effective rolling" radius. It can be thought of as the radius of an imaginary, perfectly 30 round circle that has the same circumference as the tire when the tire is revolving under a load. After substantial effort, Applicant discovered that if the "effective rolling" radius of each steerable, driving wheel is kept within a close tolerance, the torque steer effect can be signifiantly reduced. Just as the radius of a tire change as it begins to revolve under a load, the rolling circumference of a tire also, of course, changes in proportion to how the rolling radius changes. The circumference of the tire 35 revolving under a load is referred to as "effective rolling" circumference. The effective rolling radius of a revolving, loaded tire cannot be accurately ascertained simply by determining the distance from the center of the tire to road surface. This is partly due to the deformation that the upper portion of the tire undergoes when it revolves under a load. The upper portion of the tire, which is not in contact with the road, tends to bulge out. As a result, the tire has a larger effective rolling 40 circumference than is suggested by the distance between the center of the tire and the roadway. Thus, the measurement of such a distance cannot accurately indicate the tire's effective rolling circumference or effective rolling radius. The present invention is characterized by the means recited in appended claim 1. It is thus an object of the present invention to substantially reduce the torque steer effect. Other objects 45 of the invention are: (1) to easily and quickly determine the effective rolling radius of a tire; (2) to conveniently measure the effective rolling circumference of a tire; (3) to allow tires to be more closely matched before they are mounted on a vehicle and thus reduce customer complaints about the torque steer effect; and 50 (4) to use a small number of components to determine the effective rolling parameters of a tire so that the invention may be readily and inexpensively manufactured. Description of the drawing These and other objects, advantages, and features of the present invention will hereafter appear in 55 connection with the accompanying drawing, wherein like numbers refer to like parts throughout and wherein: Figure 1 is a perspective view of an automotive vehicle having two front tires that have been tested in accordance with a preferred form of the present invention; Figure 2 is a schematic diagram illustrating, in exaggerated detail, the differences between an go unloaded radius, a loaded radius, and an effective radius, in order to explain the operation of a preferred form of the present invention; Figure 3 is a block diagram showing the steps in manufacturing a tire which has been tested according to the method of the present invention; Figure 4 is a partial, front elevational view of a preferred form of the present invention, showing two 65 chucks in a spaced relation; 0 091 393 Figure 5 is a partial, front elevational view of a preferred form of the present invention, showing two chucks in a closed relation and a cross section of a tire; Figure 6 is a schematic diagram illustrating the interaction of a tire and a rolling load drum in a preferred form of the present invention; 5 Figure 7 is a graph illustrating the interaction between a first detector, a second detector, and a processor in a preferred form of the present invention; Figure 8 is a short flowchart showing an overview of the program under which the microprocessor of the present invention operates; and Figure 9 is a detailed flowchart illustrating the program under which the microprocessor of the present w invention operates. Description of a preferred embodiment Referring to Figure 1, an exemplary automotive vehicle 11 having front wheel drive is shown. The automotive vehicle 1 1 includes a drive train assembly 13, a steering assembly 15, a set of front, steerable 15 wheels 17, 19 and associated tires 21, 23, and a set of rear non-steerable wheels 25, 27 and associated tires 29, 31. The drive train assembly 13 includes a power plan 33 and two shafts 35, 37, each of which is interconnected with one of the two front wheels 17, 19 (Figure 1). The two front wheels 17, 19 are thus rotatably driven and propel the vehicle 11. 20 The steering assembly 15 includes a steering wheel 39. The steering wheel 39 is connected to the two front wheels 17, 19 (Figure 1). Since the vehicle 1 1 has front wheel drive, the effect of torque steer is particularly noticeable. Thus, if the power plant 33 provides torque, or thrust, to the two front wheels 17, 19 (and the radii of the two front tires 21, 23 are not properly "matched"), the vehicle 11 will tend to move or turn laterally, even though the 25 steering wheel 39 has not been turned. Usually, under such circumstances, the vehicle 11 tends to turn toward the tire having the smaller radius. Applicants have discovered that if the two front tires 21, 23 are "matched" within certain tolerances, the effect of torque steer is substantially reduced. The "matching" process involves the determination of a particular type of radius of the tires 21, 23. 30 The profile of a fully inflated tire, standing free and unassociated with any vehicle, is defined by a dotted, circular line 41 in Figure 2a.
Details
-
File Typepdf
-
Upload Time-
-
Content LanguagesEnglish
-
Upload UserAnonymous/Not logged-in
-
File Pages56 Page
-
File Size-