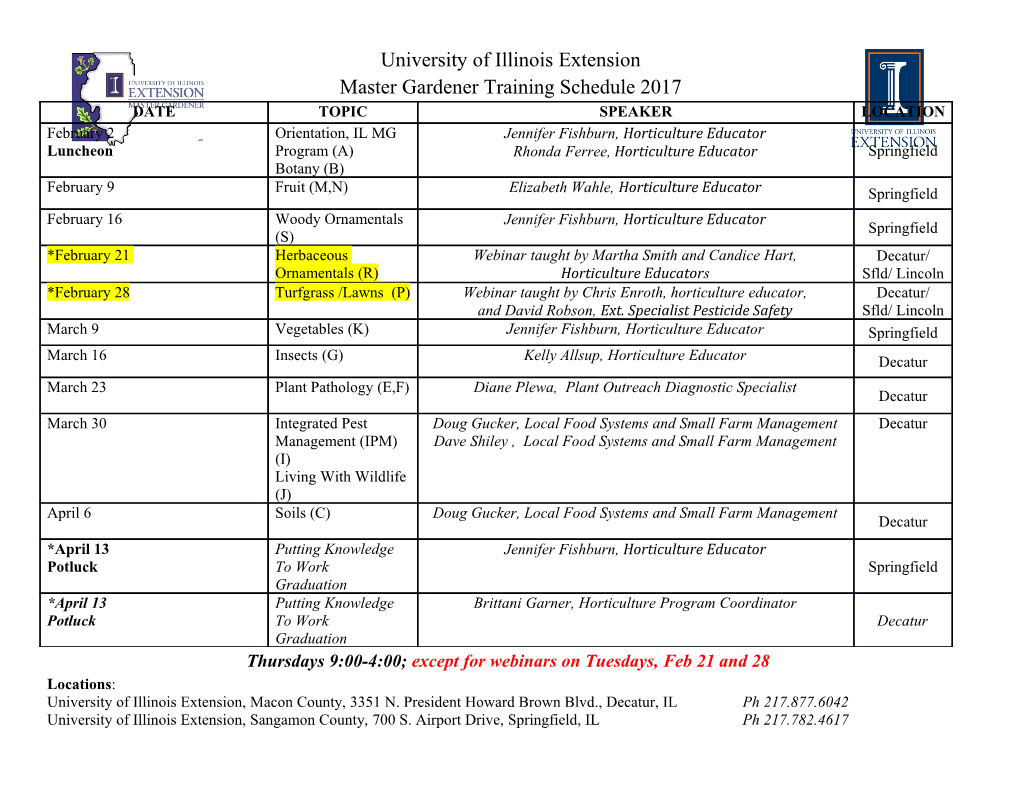
University of Texas at El Paso DigitalCommons@UTEP Open Access Theses & Dissertations 2016-01-01 Design and Performance Evaluations of a LO2/ Methane Reaction Control Engine Aaron Johnson University of Texas at El Paso, [email protected] Follow this and additional works at: https://digitalcommons.utep.edu/open_etd Part of the Aerospace Engineering Commons, and the Mechanical Engineering Commons Recommended Citation Johnson, Aaron, "Design and Performance Evaluations of a LO2/Methane Reaction Control Engine" (2016). Open Access Theses & Dissertations. 671. https://digitalcommons.utep.edu/open_etd/671 This is brought to you for free and open access by DigitalCommons@UTEP. It has been accepted for inclusion in Open Access Theses & Dissertations by an authorized administrator of DigitalCommons@UTEP. For more information, please contact [email protected]. DESIGN AND PERFORMANCE EVALUATIONS OF A LO2/METHANE REACTION CONTROL ENGINE AARON JOHNSON Master’s Program in Mechanical Engineering APPROVED: Ahsan Choudhuri, Ph.D., Chair Norman Love Jr., Ph.D. Tzu-Liang (Bill) Tseng, Ph.D., CMfgE Charles Ambler, Ph.D. Dean of the Graduate School Copyright © by Aaron Johnson 2016 Dedication I would like to dedicate this thesis to my family and friends all of whom have supported me unconditionally in this crazy journey through life. CS. DESIGN AND PERFORMANCE EVALUATIONS OF A LO2/METHANE REACTION CONTROL ENGINE by AARON JOHNSON, B.S. Mechanical Engineering THESIS Presented to the Faculty of the Graduate School of The University of Texas at El Paso in Partial Fulfillment of the Requirements for the Degree of MASTER OF SCIENCE Department of Mechanical Engineering THE UNIVERSITY OF TEXAS AT EL PASO December 2016 Acknowledgements I would like to thank Dr. Ahsan Choudhuri for giving me the opportunity to grow as an engineer and as a person, by allowing me to participate in research at UTEP. I would also like to thank NASA for their mentorship along the way and their belief in the students at cSETR. A special thanks to my committee as well, Dr. Norman Love and Dr. Bill Tseng for giving their time to review my research. I would definitely like to acknowledge a mentor of mine, Mr. Charles Hill, who consistently made sure I was on top of things with my project (even though we always ended right back at the requirements phase). A very special thanks needs to go out to my team both past and present who made all of this possible by their hard work and efforts: Arturo Acosta-Zamora, Jose Luis Mena, Israel Lopez, Raul Ponce, Pedro Nunez, Dylan Ott, and Steven Torres. I am eternally grateful for the time they put into the project and will never forget the sacrifices (long hour weeks/weekends) that were made along the way. I would also like to acknowledge my parents, Jack and Lucy Johnson, my sister, Amanda Johnson, and my girlfriend, Thania Cervantes, for consistently being there to support me. I love you all. Thank you as well to the cSETR staff; specifically, Gloria Salas and KiraLise Silva for consistently putting up with my purchase requests and never getting annoyed with me along the way. Lastly, thank you to all of the casita folks both past and present for making this an incredible ride and journey. v Abstract Liquid oxygen (LOX) and liquid methane (LCH4) are a propellant combination viewed as a potential enabling technology for spacecraft propulsion. Reasons why LOX/LCH4 is being used as an alternative propellant source include: it is less toxic than other propellants, it has the possibility to be harvested on extraterrestrial soil, LCH4 has a higher energy density than liquid hydrogen (LH2; commonly used on vehicle main engines), and LOX/LCH4 has comparable performance to other well-known propellant combinations. Through the continued partnership between the National Aeronautics and Space Administration (NASA) and the University of Texas at El Paso (UTEP) a LOX/LCH4 reaction control engine (RCE) was developed and researched. The RCE was developed for the purpose of being integrated into two UTEP LOX/LCH4 vehicles, Janus and Daedalus, and was designed based on previous engines tested both at NASA and the center for space exploration and technology research (cSETR) lab. This report details the design process and manufacturing of the engine, cold flow studies evaluating injector design, and preliminary hot fire tests to give insight into engine performance. vi Table of Contents Acknowledgements………………………………………………………………………….v Abstract……………………………………………………………………………………..vi List of Tables………………………………………………………………………………..ix List of Figures………………………………………………………………………………x Chapter 1: Introduction………………………………………………………………………1 Chapter 2: Reaction Control Engine Background……………………………………………3 Chapter 3: RCE Development Purpose………………………………………………………5 3.1 Janus and Daedalus Vehicle Overview…………………………………………..5 3.2 Vehicle Flight Profiles…………………………………………………………...7 3.3 Vehicle Development………………………………………………………….…9 Chapter 4: RCE Design Requirements……………………………………………………...10 Chapter 5: RCE Component Design………………………………………………………....15 5.1 Nozzle and Chamber Design………………………………………………….…15 5.2 Injector Design…………………………………………………………………..17 5.3 Ignition Method………………………………………………………………….19 5.4 RCE Assembly for Testing and Flight…………………………………………..21 Chapter 6: Manufactured Reaction Control Engine…………………………………….……24 6.1 Chamber and Injection Orifices……………………………………………….....24 6.2 Nozzle…………………………………………………………………………....25 6.3 Spark Plug with Extended Electrode…………………………………………….26 6.4 Inspection on Machined Parts…………………………………………………....27 6.5 Welded Engine Assembly………………………………………………………..27 Chapter 7: Cold Flow Testing………………………………………………………………..29 7.1 Water Test Set Up……………………………………………………………..…29 7.2 Data Acquisition………………………………………………………………....31 7.3 Test Results……………………………………………………………………....32 7.4 FFC Testing and Validation………………………………………………..……36 vii Chapter 8: Preliminary Hot Fire Testing…………………………………………………….38 8.1 Test Bunker Facility……………………………………………………………..38 8.2 DAQ and Instrumentation Controller……………………………………………42 8.3 Hot Fire Test Results…………………………………………………………….44 8.3.1 Gas/Gas Testing………………………………………………………………….44 8.3.2 Liquid/Liquid Testing……………………………………………………………50 Chapter 9: Future Work and Conclusions…………………………………………………...56 9.1 Proposed Hot Fire Test Matrix…………………………………………………..56 9.2 Potential Incorporation of Additive Manufacturing……………………………..57 9.3 Overall Conclusions……………………………………………………………...61 Bibliography………………………………………………………………………………….62 Appendix:…………………………………………………………………………………….64 Vita……………………………………………………………………………………….......74 viii List of Tables Table 4.1: Top Level RCE Requirements. .................................................................................... 14 Table 6.1: Inspection of key features within RCE. ....................................................................... 27 Table 7.1: Water test results for both the LOX and LCH4 lines. ................................................. 33 Table 7.2: Test results for FFC cold flow studies. ........................................................................ 37 Table 8.1: Hot fire test results for gas/gas testing. ........................................................................ 45 Table 8.2: Hot fire test results for liquid/liquid testing. ................................................................ 50 Table 8.3: Engine performance results for liquid/liquid testing. .................................................. 50 Table 8.4: Uncertainty analysis on thrust stand measurement. ..................................................... 51 Table 8.5: Predicted chamber pressures based on RPA software. ................................................ 54 Table 9.1: Proposed test matrix for liquid/liquid testing. ............................................................. 56 Table 9.2: Test matrix and results of water testing the LOX injection ports. ............................... 59 ix List of Figures Figure 2.1: Motivation behind RCS thruster, NASA’s project Morpheus vehicle. ........................ 3 Figure 2.2: RCS Thruster Assembly and Components. .................................................................. 4 Figure 3.1: Conceptual Design of Vertical Test Bed, Janus ........................................................... 6 Figure 3.2: Conceptual Design of Suborbital Test Bed, Daedalus ................................................. 7 Figure 3.3: Janus Flight Profile ....................................................................................................... 7 Figure 3.4: Daedalus Flight Profile ................................................................................................. 8 Figure 4.1: Specific Impulse vs Expansion Ratio at varying mixture ratios, Pc = 100 psi...........11 Figure 4.2: Chamber Temperature vs Chamber Pressure at varying mixture ratios. .................. ..12 Figure 4.3: Specific Impulse vs Mixture Ratio for Janus & Daedalus engines. ........................... 13 Figure 5.1: Cross sectional view of nozzles for both Janus (nozzle A) and Daedalus (nozzle B) RCEs. ............................................................................................................................................ 16 Figure 5.2: Cross sectional view of the chamber showing regions which would be cut to reduce chamber length and further study L* effects. ............................................................................... 17 Figure 5.3: Cross sectional view of the RCE detailing injection inlets. ......................................
Details
-
File Typepdf
-
Upload Time-
-
Content LanguagesEnglish
-
Upload UserAnonymous/Not logged-in
-
File Pages87 Page
-
File Size-