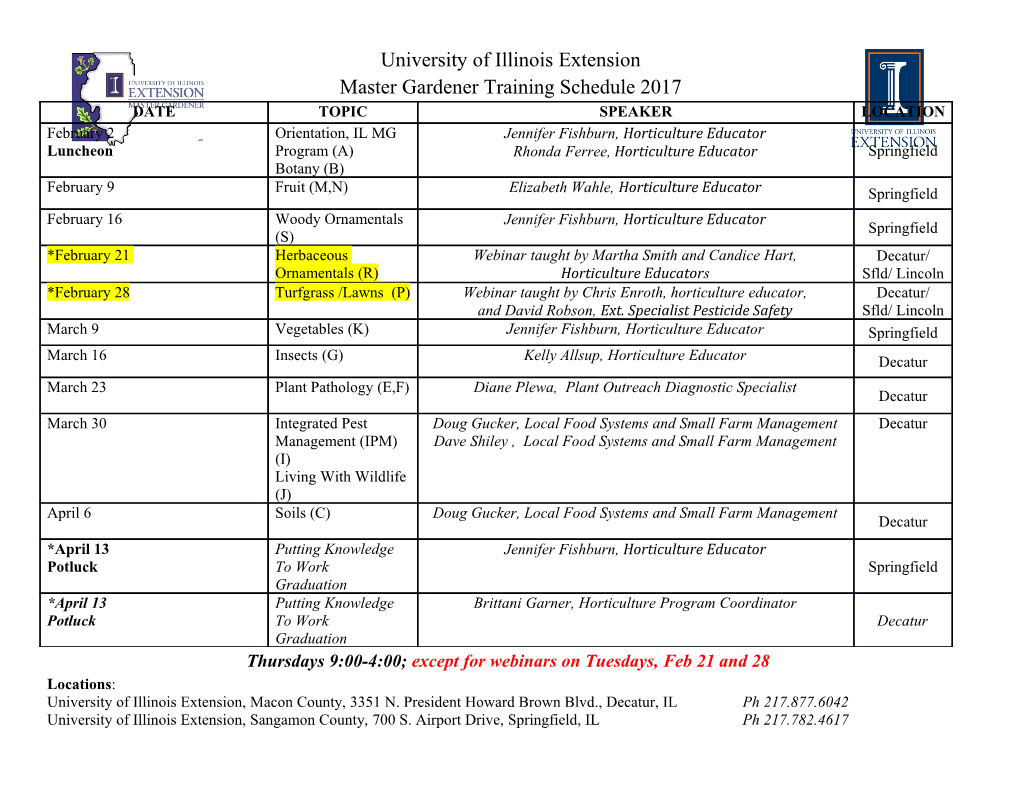
Ind. Eng. Chem. Res. 2002, 41, 1393-1411 1393 REVIEWS Future Directions of Membrane Gas Separation Technology Richard W. Baker* Membrane Technology and Research, Inc., 1360 Willow Road, Suite 103, Menlo Park, California 94025 During the past 20 years, sales of membrane gas separation equipment have grown to become a $150 million/year business. More than 90% of this business involves the separation of noncondensable gases: nitrogen from air; carbon dioxide from methane; and hydrogen from nitrogen, argon, or methane. However, a much larger potential market for membrane gas separation lies in separating mixtures containing condensable gases such as the C3+ hydrocarbons from methane or hydrogen, propylene from propane, and n-butane from isobutane. These applications require the development of new membranes and processes. In this review, the existing gas separation applications are surveyed, and the expected growth of these and potential new applications of gas separation membranes over the next 20 years are described. The improvements in gas separation technology needed to produce these changes in the membrane industry are also discussed. Introduction nitrogen selectivities of 6-8. Membranes made from these polymers could produce better than 99% nitrogen In 1980, Permea (now a division of Air Products) 1,2 and offered a cost-competitive alternative to delivered launched its hydrogen-separating Prism membrane. liquid nitrogen for many small users. This application This was the first large industrial application of gas has grown to represent about one-third of new nitrogen separation membranes. Since then, membrane-based production capacity; to date, 5000-10 000 nitrogen gas separation has grown into a $150 million/year systems have been installed worldwide. Finally, mem- business, and substantial growth in the near future is branes are also being used for a variety of small but likely. In this review, current membrane gas separation growing applications, such as the dehydration of com- applications are surveyed, and some predictions of likely pressed air and the separation of hydrocarbons from future developments are made. nitrogen or air. A milestone chart summarizing the Membranes were known to have the potential to development of membrane gas separation technology is separate important gas mixtures long before 1980, but displayed in Figure 1. the technology to fabricate high-performance mem- A list of the principal gas separation applications and branes and modules economically was lacking. The the approximate market size of each application is given development of high-flux anisotropic membranes and in Table 1. These market estimates are based on the large-surface-area membrane modules for reverse os- value of the new membrane equipment produced each mosis applications occurred in the late 1960s and early year. In some areas, such as nitrogen-from-air separa- 1970s. Permea then adapted this technology to mem- tions, the equipment producers often install the systems brane gas separation. Its polysulfone hollow-fiber mem- on an own-and-operate basis, selling the nitrogen pro- brane was an immediate success, particularly for the duced to the end user. The market for this service separation and recovery of hydrogen from the purge gas business is significantly larger than that for the equip- streams of ammonia plants. Within a few years, Permea ment given in Table 1. systems were installed in many such plants. This success encouraged other companies to advance their Current Membrane Technology own technologies. By the mid-1980s, Cynara (now part Gas Separation Membranes. Currently, only eight of Natco), Separex (now part of UOP), and GMS (now or nine polymer materials have been used to make at part of Kvaerner) were using cellulose acetate mem- least 90% of the total installed gas separation mem- branes to remove carbon dioxide from natural gas.3 At brane base. Several hundred new polymer materials about the same time, Generon (now part of MG) have been reported in the past few years, and many introduced a membrane system to separate nitrogen have substantially higher permeabilities and selectivi- from air. These first air separation systems were based ties than those listed in Table 1. Thus, it is surprising on poly(4-methyl-1-pentene) (TPX) membranes with an that so few are actually used to make industrial oxygen/nitrogen selectivity of about 4. These membranes membranes. However, permeability and selectivity are were only competitive in a few niche areas requiring only two of the criteria that must be met to produce a 95% nitrogen, but by 1990, Generon, Praxair, and useful membrane; others include the ability to form Medal4,5 had all produced custom polymers with oxygen/ stable, thin, low-cost membranes that can be packaged into high-surface-area modules.6 * Tel.: 650-328-2228. Fax: 650-328-6580. E-mail: rwbaker@ To obtain high permeation rates, the selective layer mtrinc.com. of gas separation membranes must be extremely thin. 10.1021/ie0108088 CCC: $22.00 © 2002 American Chemical Society Published on Web 02/21/2002 1394 Ind. Eng. Chem. Res., Vol. 41, No. 6, 2002 Figure 1. Milestones in the development of membrane gas separations. Table 1. Principal Gas Separation Markets, Producers, and Membrane Systems (2000) principal markets/ principal membrane company estimated annual sales material used module type Permea (Air Products) large gas companies polysulfone Medal (Air Liquide) nitrogen/air ($75 million/year) polyimide/polyaramide hollow fiber IMS (Praxair) hydrogen separation ($25 million/year) polyimide Generon (MG) tetrabromo polycarbonate GMS (Kvaerner) mostly natural gas separations spiral-wound Separex (UOP) carbon dioxide/methane cellulose acetate Cynara (Natco) ($30 million/year) hollow fiber Aquilo polyphenylene oxide Parker-Hannifin polyimide hollow fiber vapor/gas separation, air Ube dehydration, other ($20 million/year) GKSS Licensees plate-and-frame silicone rubber MTR spiral-wound Typical membranes have effective thicknesses of less strength.7 Membranes can be formed as flat sheets or than 0.5 µm and often less than 0.1 µm. Many of these as fine capillaries (hollow fibers) 50-500 µm in diam- extremely thin membranes are made by a variant of the eter. Figure 2a shows the structure of this type of polymer phase separation process invented by Loeb and membrane. Sourirajan in the 1960s. These membranes have a thin, The method used to prepare anisotropic phase sepa- dense, nonporous skin layer that performs the separa- ration membranes limits the number of materials that tion, supported on a finely microporous substrate made can be formed into high-performance membranes. For from the same material that provides mechanical this reason, membranes are increasingly formed as Ind. Eng. Chem. Res., Vol. 41, No. 6, 2002 1395 tion cost, depending on the market. However, the importance of this cost advantage is often overstated. Gas separation plants, especially in refinery and pet- rochemical operations, require the membrane modules to be packaged in code-stamped steel pressure vessels fitted with expensive controls, valves, and instrumenta- tion. Such plants also involve large compressors. The membrane module cost is often only 10-25% of the total cost. This means that significant reductions in mem- brane cost might not markedly change the cost of the complete plant. To date, two-thirds of the total gas separation market has involved the separation of nitrogen or water from air and of hydrogen from ammonia purge gas or syngas. These are clean gas streams, free of components that might foul or plasticize the membrane, so hollow-fiber modules function well. However, growing application areas for membranes are in natural gas treatment, refineries, and petrochemical plants, where the gas streams contain high levels of plasticizing, condensable Figure 2. Gas separation membranes made by the Loeb- Sourirajan phase separation process or as composite membranes vapors that degrade membrane performance. The gas by a solution-coating procedure.7 might also contain suspended particulates or oil mist, which are easily trapped in stagnant areas of the composite structures of the type shown in Figure 2b. module and lead to irreversible membrane fouling. The Composite membranes also contain less than1gofthe gas streams also vary in composition and flow. To selective polymer per square meter of the membrane, address these issues, robust membrane systems able to whereas anisotropic Loeb-Sourirajan membranes can handle changes and upsets are required. Significantly use 40-60 g of the selective polymer per square meter more careful and expensive pretreatment to avoid these of membrane. Increasingly, the new membrane applica- problems is required in hollow-fiber membrane systems tions require expensive, custom-made polymers for the than in spiral-wound units. The balance between the selective layer. These polymers can cost $10-20/g or benefits of low-cost hollow-fiber and more reliable spiral- more; therefore, they cannot be economically fabricated wound modules is more even in these applications. into Loeb-Sourirajan-type membranes. Composite membranes consist of two or more layers Current and Future Applications of different materials. The support layer is made by the Air Separation. Nitrogen. A simplified drawing of a - Loeb Sourirajan procedure using a casting solution nitrogen-from-air separation system is shown in Figure formulation such that the top skin layer is very finely 4. The feed air is compressed to 8-10 atm with a low- - microporous
Details
-
File Typepdf
-
Upload Time-
-
Content LanguagesEnglish
-
Upload UserAnonymous/Not logged-in
-
File Pages19 Page
-
File Size-