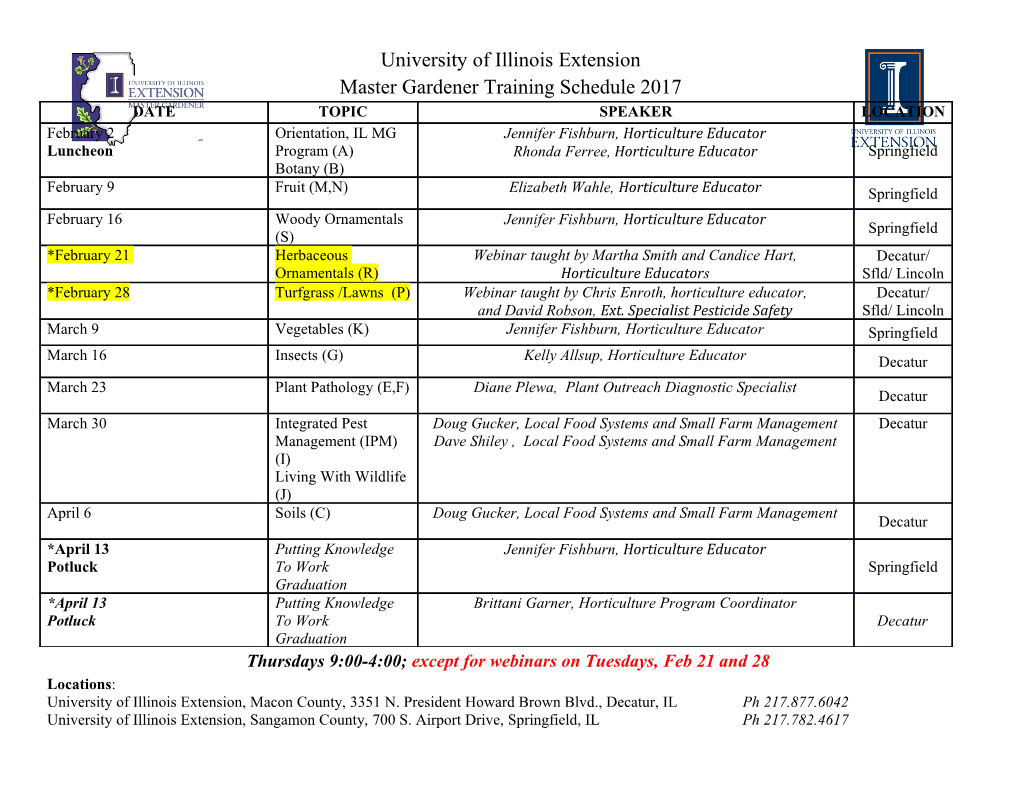
MASTER'S THESIS Challenges with Deep Mining Case Studies at Mindola and Mufulira Underground Mines, Zambia Kristoffer Berglund Daniel Günther 2014 Master of Science (120 credits) Natural Resources Engineering Luleå University of Technology Department of Civil, Environmental and Natural Resources Engineering Challenges with deep mining Case studies at Mindola and Mufulira underground mines, Zambia Kristoffer Berglund & Daniel Günther MSc-thesis in Rock Mechanics and Rock Engineering Department of Civil, Environmental and Natural Resources Engineering Lulea University of Technology SE – 971 87 Lulea Sweden ii Preface This MSc-thesis in Rock Mechanics and Rock Engineering is the final work that finishes our studies towards an MSc-degree in Natural Resources Engineering. It stands for 30Hp and was carried out during the spring and summer of 2013 at the Department of Civil, Environmental and Natural Resources Engineering at Lulea University of Technology. First of all we would like to thank Prof. Erling Nordlund and Dr. Jenny Greberg at LTU for granting us the opportunity to conduct this thesis in collaboration with the I2Mine project. This gave us the chance of a life time to visit the mines in Zambia and experience and learn things we never would have learnt elsewhere. This has been incredibly inspiring and we are forever grateful. We would also like to extend our great appreciation to the staff of the Mufulira and Mindola mines; for their great hospitality, the time and the experience they shared with us to make this study possible. We would also like to thank Dr. Ping Zang and Dr. Daniel Johansson for their guidance and the inspiring discussions we have shared. Finally we would like to thank PhD. Student Sraj Banda who arranged the trip to Zambia and took care of all the practicalities associated to the mine visits. We would also like to thank him for the inspiration, help, encouragement, advice and guidance he has given us during this study, without you it would not have been possible. Personal acknowledgements by the authors: First of all I would like to thank my friend Kristoffer Berglund for all the good times we have shared during our studies. I would like to thank my father for all the proofreading you have had to endure and for all the guidance you have given me through my entire study time you have been a huge support and I am forever grateful. I would also like to thank my mother for always believing in me providing me the support and confidence to reach goals I did not think I could reach. My fiancée Ida the joy in my life who has always stood by my side, words cannot express what you mean for me. Last I would like to dedicate all my work in this report to my beloved grandpa who passed away during my studies in April 2011. Daniel Günther Luleå September 2013 iii I would like to thank my family for always being there for me during my time as a student. A special thanks to my friend Daniel Günther for all the fun and mischief we have experienced together. Kristoffer Berglund Luleå September 2013 iv Abstract In pace with our ever increasing demand for metals and with many of the known deposits already exploited, the mining industry is forced to enter into unexplored territories in the search for new deposits. The depth of our earth is one of them; mining operations are currently taking place at greater depths than ever before and exploration into the depths continues. But with the depth new challenges to mining has risen and existing challenges has become even greater. This study will try to shine some light on these challenges, their possible solutions and the considerations that has to be made regarding them. This report is divided into two parts; part A and part B. In part A, two case studies are presented from two deep mines in Zambia. These mines were visited and investigated for this study. In part B the challenges these mines face due to the depth of mining are presented and analyzed. The analysis is based on literature studies, information gathered on site, basic calculations and numerical modeling performed in the finite element program Phase2 by RocklabTM. The case studies were performed as a part of the I2Mine research project. The I2Mine research project aims to realize the vision of an invisible, zero impact deep mine. The mines that were studied are Mufulira Copper mine and Mindola Copper mine which are located to the Copperbelt region of Zambia. Both are owned and operated by Mopani Copper Mines Plc. which is the main employer in the region. The Mufulira mine has a proven and probable ore reserve of 19 million Tonnes and has at the current copper price an expected mine life of 25 years. The main mining method in Mufulira is a variant of Sub level Open Stoping locally referred to as Mechanized Continuous Retreat. The mine is made out of three ore bodies which dip at around 45°, the ore is extracted in stopes and no backfilling is employed since the mining progresses downward. Current mining level is at a depth of 1540 meters and both ore and waste rock is hoisted to the surface. Ventilation is performed mechanically with no complementing air-conditioning. The rock mass failures are generally stress induced and the mine also experience some mining induced seismicity mostly connected to pillar burst and caving of the stopes. The Mindola mine is a copper and cobalt mine which has a total measured and indicated ore reserve of 28 million tones and an annual production of 1.1million tones putting the life of mine at 25 years. The mining method used for production at Mindola Shaft is a variation of sublevel stoping known as the Vertical Crater Retreat (VCR) method. The ore body in Mindola is on average 12 meters wide with dip varying from 56° to 72°, the ore is extracted in stopes and backfilling is employed. The current production level is located at 1570 m depth and plans are made to deepen the mine further in order to extend its life. The ventilation system in the Mindola mine is based on a technique that creates a pressure difference between the mine and the surface by sucking air out of the mine and letting fresh air in. The most common failure mechanisms v experienced are slow and time dependent deformations and in some cases stress concentrations in combination with unfavorable rock structures. After conducting the two case studies at Mindola and Mufulira it was evident that Mufulira was experiencing great geotechnical challenges due to stress induced by the mining method. The main problem is that the MCR method leaves behind crown pillars which acts like stress windows and causes high stresses in the footwall drifts. In Mindola they have faced a similar problem but they dealt with it by changing the mining method, so that they now backfill the stopes. By that they don't have to leave behind any crown pillars which would have acted as stress windows. The change of mining method have also had positive effects on the production as it means less development and that the waste no longer has to be hoisted to the surface. By implementing the same changes in Mufulira similar results could be expected. A numerical analysis was performed with the objective to investigate how a change in mining method would affect the high stress levels in Mufulira. The numerical analysis was performed using the finite element software Phase2 based on data received from the mine. One of the major goals of the analysis was to determine what a change in mining method would imply for the location of the footwall drifts since these had been moved further and further away from the stopes as the depth had increased. Results from the numerical analysis indicated that changing the mining method in Mufulira would severely decrease the stress levels in the footwall. The major reason for that was that the change of method would eliminate the stress windows and by that lower the stress in the footwall. This would then mean that the footwall drifts could be placed much closer to the stope, reducing both hauling distance as well as development time. From the two case studies it could also be concluded that both mines faces great ventilation challenges with respect to heat. The mines reported temperatures in the range of 32°C wetbulb in the production areas at the current mining level. The reason for the high temperatures is that air is heated by both autocompression, which is a function of surface temperature and depth, and by thermal radiation from the host rock, which has at deepest part of the mine an internal temperature of around 50°C due to the geothermal gradient. In order to lower these temperatures the mine plans to expand the vertical infrastructure of the ventilation system and thereby increase the airflow. With respect to these problems analyses were conducted with the objective to validate the mines proposed solutions and determine if other solutions could be applicable. In the analysis different means of air-conditioning were studied. Two factors of major importance for ventilation with regards to heat were identified: The critical depth and the critical rock temperature. These factors represents the limits were the air basically no longer has any cooling potential due to either autocompression and / or thermal radiation from the rock. vi The results indicated that both mines have passed both the critical depth and the depth of the critical rock temperature. The conclusion could be made; that the solution of increasing the air velocity in order to lower the temperatures would only add to the heat load.
Details
-
File Typepdf
-
Upload Time-
-
Content LanguagesEnglish
-
Upload UserAnonymous/Not logged-in
-
File Pages129 Page
-
File Size-