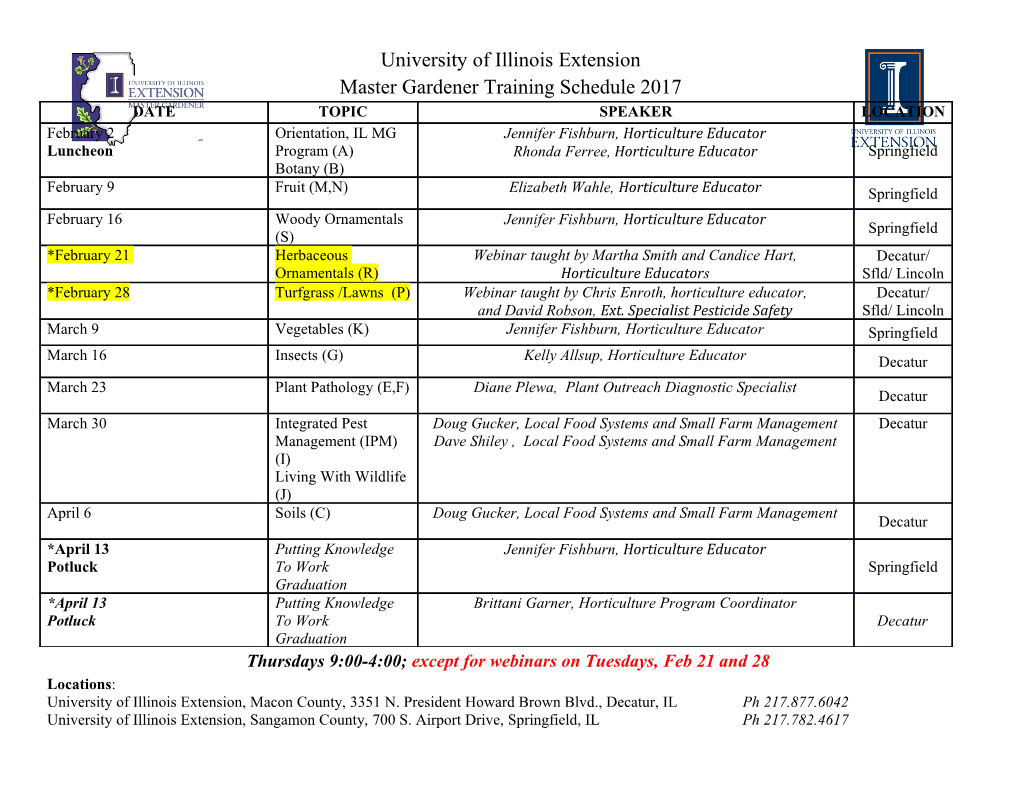
Complete Stokes vector analysis with a compact, portable rotating waveplate polarimeter T. A. Wilkinson,a) C. E. Maurer, C. J. Flood, G. Lander, S. Chafin, and E. B. Flaggb) Department of Physics and Astronomy, West Virginia University, Morgantown, West Virginia 26506, USA (Dated: 15 April 2021) Accurate calibration of polarization dependent optical elements is often necessary in optical experiments. A versatile polarimeter device to measure the polarization state of light is a valuable tool in these experiments. Here we report a rotating waveplate-based polarimeter capable of complete Stokes vector analysis of collimated light. Calibration of the device allows accurate measurements over a range of wavelengths, with a bandwidth of >30 nm in this implementation. A photo-interrupter trigger system supplies the phase information necessary for full determination of the Stokes vector. An Arduino microcontroller performs rapid analysis and displays the results on a liquid crystal display. The polarimeter is compact and can be placed anywhere on an optical table on a single standard post. The components to construct the device are only a fraction of the cost of commercially available devices while the accuracy and precision of the measurements are of the same order of magnitude. The polarization state of light, described by the Stokes vec- mount. The polarimeter presented here provides advantages 1 tor S = [S0;S1;S2;S3] , is of critical importance in a broad in ease of use, functionality, portability, and cost over previ- range of optics-based experiments2. Coupling light to a polar- ous realizations7,9,10. ization maintaining fiber requires that the polarization of the The polarization state of a beam of light can be formally 3 input beam be matched to the polarization axis of the fiber . described by the Stokes vector S = [S0;S1;S2;S3], where S0 = Selectively addressing optically active transitions in quantum IX + IY is the Stokes parameter describing the total intensity, emitters like atoms or quantum dots requires the polarization S1 = IX − IY the linear component, S2 = ID − IA the diagonal state of the incident laser match the dipole moment of the component, and S3 = IR − IL the circular component, where 4 desired transition . Calibration of liquid crystal variable re- Ib with b = fX;Y;D;A;R;Lg denotes the measured intensity tarders (LCVRs), a common polarization manipulation com- of a given polarization1. The manipulation of the polariza- ponent, necessitates precise knowledge of the polarization of tion by a series of optical elements can be described by the the laser to be used as a reference5. These are among many appropriate (4x4) Mueller matrices11–13. Figure 1(a) shows other experimental situations that need highly accurate knowl- the elements of our system, namely a rotating waveplate of edge of the polarization state of light. Therefore, the complete retardance d ≈ p=2 at angle q, followed by a stationary lin- measurement and characterization of the polarization of light ear polarizer at angle a before the detector. Operating the is of widespread interest and importance. Mueller matrices of the optical components on an arbitrary Here we describe a self-contained, portable, inexpensive input Stokes vector, one arrives at a general expression for the polarimeter capable of complete Stokes vector characteriza- intensity signal detected by the photodiode as6,7,14 tion of any input polarization. The polarimeter is based on a 1 rotating quarter-wave (l/4) plate (QWP), a polarizer (called I(q) = [A + Bsin(2q) +C cos(4q) + Dsin(4q)]; (1) the analyzer), and a photodiode in series6. In general, linearly 2 polarized light can be distinguished from circularly polarized where q = wt + f is the orientation angle of the waveplate, light by analyzing the fluctuating light intensity signal inci- with w the angular frequency of rotation and f describing the dent on the photodiode. This approach relies on measuring phase. Allowing for an imperfect retardance of the waveplate the relative amplitudes of the 2w and 4w components of the (d 6= p=2) the coefficients of the frequency components of signal, where w is the angular frequency of the rotating QWP Eq. 1 give the input Stokes parameters by the relations10,15,16 in front of the analyzer7,8. However, to fully measure the S = A −C=tan2(d=2); (2a) Stokes vector, the relative angle between the QWP fast axis 0 2 (FA) and the analyzer transmission axis (TA) must be known S1 = C=sin (d=2); (2b) 9 arXiv:2104.06504v1 [physics.ins-det] 5 Apr 2021 for each period of rotation . We use a photo-interrupter and 2 S2 = D=sin (d=2); (2c) a timing disk to measure the phase of the QWP angle relative to the analyzer for each rotation period. We combine our op- S3 = B=sin(d): (2d) tical setup with an Arduino microcontroller for analysis. Our implementation is thus able to measure any arbitrary input po- The relationships of the coefficients in Eq. 1 to different larization, while resting on only a single standard optical post frequency sinusoids means the Fourier transform provides a natural tool for determination of the Stokes vector. The lin- ear components of the Stokes vector (S1, S2) depend only on the 4w part of the signal, while the circular component (S3) a)Electronic mail: [email protected] depends only on the 2w part. Using this fact, one can eas- b)Electronic mail: [email protected] ily determine the degree of linear or circular polarization of 2 (a) (b) Photodiode Linear (c) Polarizer Photo Interrupter Detector Linear Polarizer Motor α Rota�ng QWP Photodiode θ=ωt+ϕ y Polarizer(α) Broadband Zero-Order Polarizer(γ) Timing QWP(θ) QWP(ε) Disk x QWP Polarimeter FIG. 1. Measurement part of the polarimeter shown (a) schematically, and (b) as a 3-D image of the physical device. The QWP is mounted on a hollow axle motor with azimuth q = wt + f, where w is the angular frequency of rotation and f the phase of the rotation, and a is the azimuth of the linear analyzer. (c) The optical setup for calibration and characterization of the device. The upstream polarizer has azimuth g, and the upstream QWP has azimuth e. the light without knowing the phase of the signal, as in the use this longitude as feedback for the calibration. In principle implementation by Bobach et al.7. However, to measure the this can be achieved entirely by hand with a careful alignment complete Stokes vector of the light, the components C and D of the QWP in its mount. In practice this proves difficult and must be separated, and thus the phase of the signal (f) must time consuming due to the lack of fine control of our custom- be known. made QWP mount designed for use with the hollow axle mo- The angle f determines the position of the FA of the QWP tor (design in supplemental). So we add in software the ability at the beginning of each period of rotation. In principal, the to offset the measured signal by 360◦=64 = 5:625◦, where 64 signal may be analyzed and the Stokes vector determined for is the number of data points sampled from the photodiode per any choice of analyzer angle a and phase angle f. How- period (see Fig. 2(a)). Using these two methods in tandem to ever, situations where the analyzer does not lie in the de- set 2y = (0 ± 1)◦ for an X-polarized input calibrates the de- sired measurement basis (a 6= 0;p=2), or the QWP FA is vice quickly and accurately. Note that the software offset al- not parallel or perpendicular to the analyzer at the start of lows the physical phase angle f to differ from zero. However, a new period (ja − fj 6= 0;p=2), lead to unnecessary com- this difference leads only to a phase shift of the signal that is plications in Eq. (1) and the subsequent Fourier analysis. corrected by the software offset. This method essentially al- Thus, we will limit ourselves to cases where a = 0;p=2 and lows misalignment of f in increments of 5:625◦, rather than ja − fj = 0;p=2. The remaining choices of analyzer angle a specifically requiring f = 0. and QWP trigger angle f, of which there are four, affect the The voltage signals from the photodiode and the photo- signs in Eq. (1). For a = f = 0, Eq. 1 is the result, while for interrupter are sent to a small circuit board containing an Ar- the choice a = 0, f = p=2 the second term becomes nega- duino Pro-Micro controller for signal processing. The user tive and the equation matches those found in15 and16. In our can control the duration of the software offset using a poten- current implementation we chose the case of Eq. (1) where tiometer connected to an analog input of the Arduino. Adjust- a = f = 0. ment of the offset combined with physical realignments of the Figure 1(b) shows a 3-D image of our experimental mea- QWP in its mount form the basis of our calibration procedure. surement apparatus. As in the previous implementation by The Arduino performs the fast Fourier transform (FFT), cal- Bobach et al.7 we mount the QWP on a model airplane mo- culates the Stokes vector components, and displays the results tor with a hollow axle, which allows light to pass through on a small liquid crystal display (LCD). The circuit diagram, the axle to the analyzer and detector. Attached to the rotat- a detailed description of the calibration procedure, and the Ar- ing part of the motor we place a thin, circular metal timing duino code are included in the supplemental.
Details
-
File Typepdf
-
Upload Time-
-
Content LanguagesEnglish
-
Upload UserAnonymous/Not logged-in
-
File Pages5 Page
-
File Size-