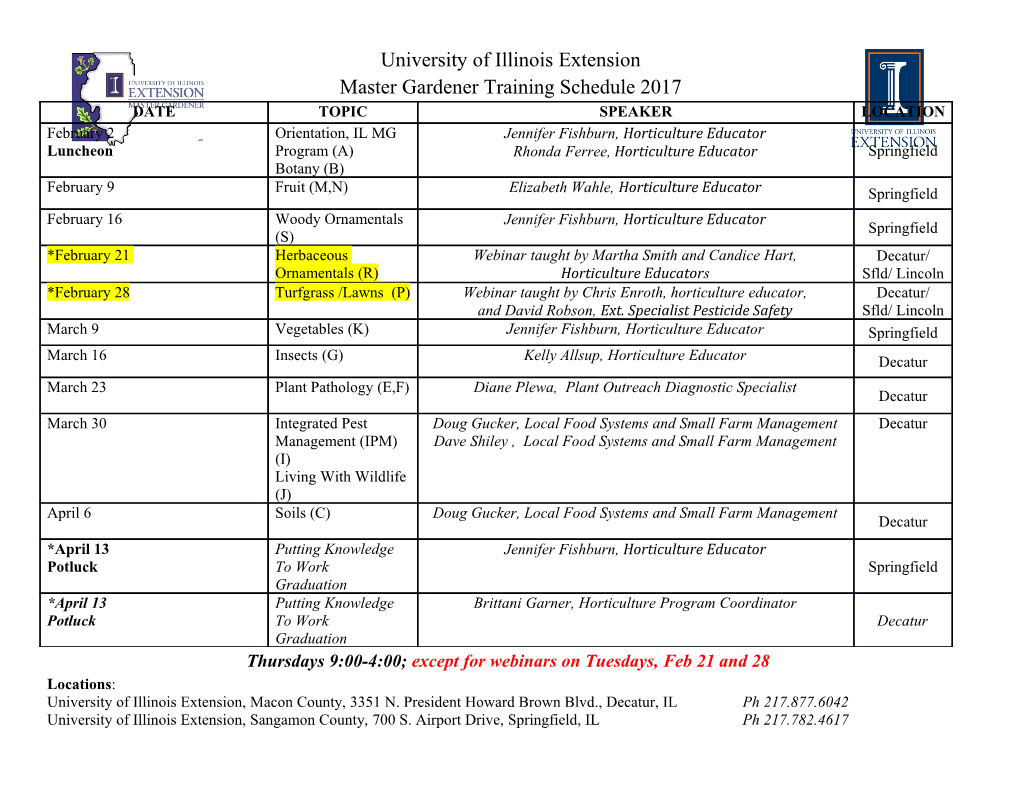
Design and Performance of a Gas-Turbine Engine from an Automobile Turbocharger by Lauren Tsa.i SUBMITTED TO THE DEPARTMENT OF MECHANICAL ENGINEERING IN PARTIAL FULFILLMENT OF THE REQUIREMENT FOR THE DEGREE OF BACHELOR OF SCIENCE IN MECHANICAL ENGINEERING AT THE MASSACHUSETTS INSTITUTE OF TECHNOLOGY JUNE 2004 © 2004 Lauren Tsai. All rights reserved. The author hereby grants to MIT permission to reproduce and to distribute public paper and electronic copies of this thesis document in whole or in part. Signature of Author: Department of Mechanical Engineering May 7, 2004 Certified by: - Professor Ernest Cravalho Professor of Mechanical Engineering Thesis Supervisor 0 Accepted by: . Professor Ernest Cravalho Chairman, Undergraduate Thesis Committee Department of Mechanical Engineering - qMA' CHUS-.iS tN$'TiTUX OF TECHNOLOGY JUN 0 8 205 1 ARCHIVS LIBRARIES Desigll and Performance of a Gas-Trblilne Engine from a Autolnobile Turbocharger L beTsi Lauren Tsai Submitted to the Department of Mechanical Engineering on May 7, 2004 in Partial Fulfillment of the Requirements for the Degree of Bachelor of Science in Mechanical Engineering ABSTRACT The Massachusetts Institute of Technology Department of Mechanical Engineering teaches thermodynamics and fluid mechanics through a pair of classes, Thermal Fluids Engineer- ing I & II. The purpose of this project was to design and fabricate a gas-turbine engine for demonstration use in these two classes. The engine was built from an automobile tur- bocharger with a combustion chamber connected between its compressor and turbine. Pres- sure and temperature sensors at different points of the engine cycle allow students to monitor the performance of the individual engine components and the complete engine cycle. Thesis Supervisor: Ernest Cravalho Title: Professor of Mechanical Engineering 2 Contents 1 Introduction 7 2 Gas Turbine Power Plants 8 2.1 The Brayton Cycle ............ 9 2.2 First Law Analysis of the Brayton Cycle 10 3 Gas Turbine Components 11 3.1 Compressors............ .................... 11 3.2 Turbines............. .................... 11 3.3 Combustion Chambers ...... .................... 12 3.4 Measuring Cycle Efficiency .... .................... 13 4 Automobile Turbochargers 13 5 Engine Overview 14 6 Selection of the Turbocharger 15 7 Combustion Chamber Design 17 7.1 Analysis of Combustion Reaction ..... .... I......... 19 7.2 Fuel Flow into the Combustion Chamber . .............. 22 7.3 Flange Design ............... .............. 24 7.4 Stress Analysis .............. .............. 25 8 Auxiliary Systems 27 8.1 Lubrication and Cooling System ...... ................... 27 8.2 Ignition System ............... ................... 28 8.3 Pressure and Temperature Measurement ................... 30 9 Status of the Project & Recommendations 30 References 31 3 List of Figures 1 Completed Gas-Turbine Engine ............. .... 8 2 Components of a Basic Gas Turbine Engine [4] .......... 9 3 Brayton Cycle Processes [14]............. ...... 10 4 Typical Turbocharger Design[10]................. 14 . 5 Compressor Map ......................... 15 6 Turbine Map ........................... 16 7 Combustion Zones[7] ....................... 17 8 Concentric Shell Design ..................... 18 9 Cross-Section of the Combustor as Air Enters from the Compres;sor . 21 10 Fuel System Components ......... ............ 22 11 Fuel Hook ............................. 23 12 Flanged and bolted pipe with a uniform internal pressure p psi, and a longi- tudinal tensionP lb.[13]..................... 25 13 Melling Model M-68 Oil Pump .................. 27 14 Generator......... .................... 28 15 Combustion Chamber Inlet ............. ....... 29 16 Baffle Part Drawing ........................ 33 17 Compressor Flange Part Drawing ........ ... ..... 34 18 Compressor Outlet Plate Part Drawing ......... .... 35 19 Exhaust Plate Part Drawing ................... 36 . 20 Flame Tube Part Drawing .................... 37 21 Flow Plate Part Drawing ..................... 38 22 Fuel Connector Part Drawing .................. 39 23 Fuel Hook Part Drawing ..................... 40 24 Shell Part Drawing ............... ......... I . 41 25 Shell Assembly Drawing ................ ..... 42 26 Shell Plate Part Drawing ..................... 43 27 Support Pin Part Drawing .................... 44 28 Turbine Inlet Assembly Drawing ................. 45 29 Turbine Inlet Plate Part Drawing . 46 4 List of Symbols Symbols are listed in alphabetical order. Values are listed for symbols denoting constants. Symbol Meaning a internal diameter of combustor A 1 area at the fuel hook inlet Am total required cross-sectional area of bolts Aml total required cross-sectional area of bolts for operating conditions Am 2 total required cross-sectional area of bolts for gasket seating At area at the fuel hook outlet b diameter of gasket bolt placement Cd flow coefficient of propane through the fuel hook holes Cp specific heat at constant pressure cv specific heat at constant volume Cv flow coefficient through the propane valve d outer diameter of combustor flange f see Equation 46 F longitudinal tension force in the cylinder g gravitational acceleration G mean diameter of gasket contact face ratio: P h cv combustor flange thickness h enthalpy h enthalpy of a particular compound at a given T and P ho -TP _ enthalpy of formation hT,p - h25oC,latm enthalpy to raise a compound to temperature T H total hydrostatic end force of combustor flange Hp total joint contact surface compression load on combustor flange m gasket factor 2 mass flow rate bending moment in combustor flange MO efficiency Ti h molar flow rate, NWR net work ratio P air pressure Q heat transfer R gas constant p density of propane specific entropy tangential hoop stress in the flange 82 tangential bending stress in the flange Sl longitudinal direct stress in the cylinder 5 List of Symbols, Continued Symbol Meaning Scl' longitudinal bending stress in the cylinder Sc,max maximum longitudinal stress in the cylinder Sfl radial direct stress in the flange S/l radial bending stress in the flange S allowable bolt stress value t wall thickness of combustor T air temperature TI see Equation 46 -2 see Equation 46 W ~ velocity Vactual volumetric flow rate of propane VO shear stress in combustor flange Wshaft shaft work transfer WmI minimum required bolt load for combustor operating conditions Wn2 minimum required bolt load for combustor gasket seating x± molar flow rate of propane molar flow rate of air z vertical position 6 1 Introduction The Massachusetts Institute of Technology Department of Mechanical Engineering teaches thermodynamics and fluid mechanics through a pair of classes, Thermal Fluids Engineering I & II. The courses cover the basic principles of thermodynamics, fluid mechanics, and heat transfer. This includes the rate processes involved with heat and work transfer, steady flow components of thermodynamic plants, and energy conversion cycles. The purpose of this project was to design and fabricate a gas-turbine engine that is suitable for use as a classroom demonstration. The gas turbine designed and built for this project illustrates the operation of the Brayton cycle. The Brayton cycle is a convenient cycle to demonstrate because it involves a combination of standard components, which are used in many other energy conversion applications. The Brayton cycle consists of a compressor, a heat exchanger, a turbine, and another heat exchanger. The gas turbine engine operates on an open version of the Brayton cycle and allows students to measure the temperature and pressure changes associated with each system component. The students can then use these values to calculate the performance of the engine components as well as the overall cycle efficiency. In order to make the engine suitable for demonstration use, there were several require- ments. The engine had to be portable so that it could be easily moved to the desired location. It also needed run on an easily attainable fuel and at a safe maximum temperature. The state of the air flow through the engine also needed to be measurable at each point of the engine cycle so that students could compare the predicted and measured performance of the engine. The construction of the engine involved the design and selection of each component of the gas turbine and the engine's auxiliary systems. The engine is based around an automo- bile turbocharger comprised of a compressor and turbine that operate on a common shaft. Between the outlet of the compressor and the turbine inlet is a combustion chamber. The design and fabrication of the combustion chamber represents the bulk of the work for this thesis. In addition to these main system components, the cooling and lubrication system runs oil through the turbocharger, a generator creates a spark to ignite the fuel, and a series of components is used to control the flow rate of fuel to the engine. The completed engine is shown in Figure 1. This thesis is the continuation of the project begun by Keane Nishimoto for his under- graduate thesis requirement[11]. His thesis included the selection of the turbocharger, the purchase of the oil pump for the lubrication and cooling system, and the initial idea of a concentric shell design for the combustion chamber. This thesis begins with a description of the basic thermodynamic theory behind gas turbine engines, examining the cycle of the energy conversion system and the individual components involved. Then, there is a brief introduction to automobile turbochargers,
Details
-
File Typepdf
-
Upload Time-
-
Content LanguagesEnglish
-
Upload UserAnonymous/Not logged-in
-
File Pages46 Page
-
File Size-