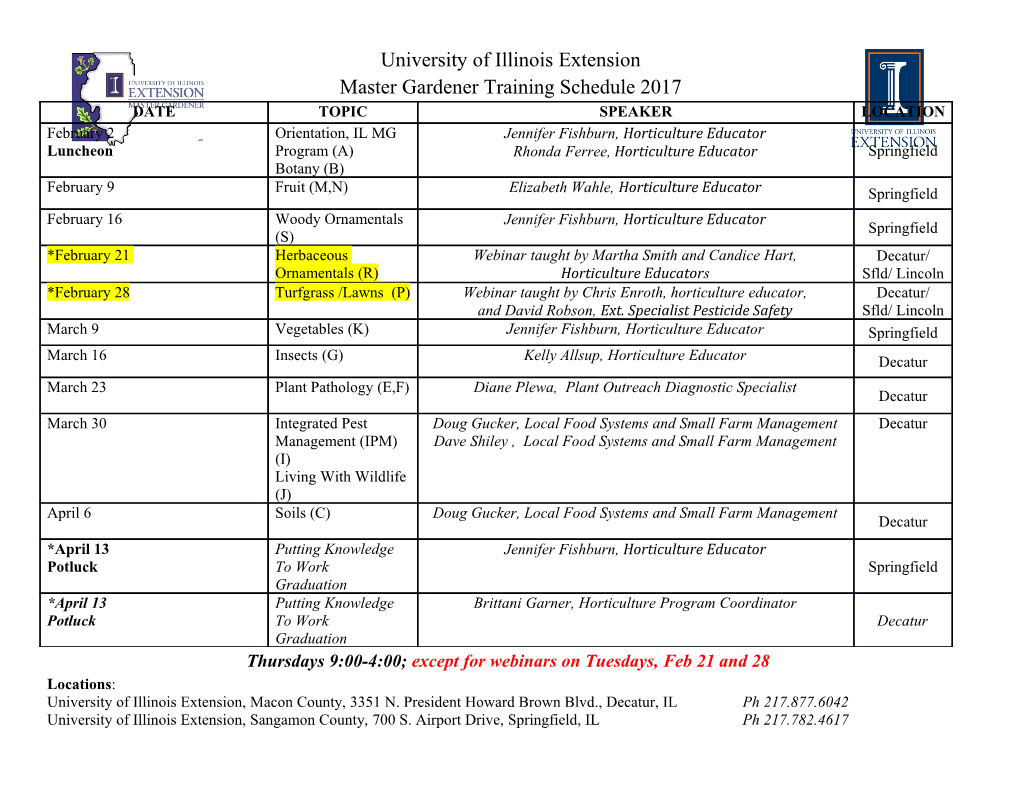
NEACRP-A- 66+- THREE-DIMENSIONAL KINETICS ANALYSIS OF LARGE LMFBR CORES WITH THERMAL HYDRAULIC FEEDBACK Y. Oka, N. Tada*, M. Konomura**, S. Kondo and S. An*** Nuclear Engineering Research Laboratory, Faculty of Engineering, University of Tokyo Tokai-mura, Ibaraki 319-11, JAPAN September 1984 present address: * Toyo Engineering Corp. Higashi Funabashi 6-12-10, Funabashi City, Chiba 213, JAPAN ** Power Reactor and Nuclear Fuel Development Corp. Oa~rai Engineering Center, Oarai-cho, Ibaraki 311-13, JAPAN xxx Tokai University Tomigaya 2-28-4, Shibuya-ku, Tokyo 151, JAPAN 063900.0 ', Abstract, Transient behavior of LMFBRs due to withdrawal of a control rod was analysed by the two-dimensional FXZ-TH code and three-dimensional IBIS. Both calculations agreed well with each other for the transient due to central control rod withdrawal. The analysis oft the behavior against pe- ripheral control rod withdrawal showed that the two-dimensional calculation in R-Z geometry gave 30 % higher fuel temperature rise at 1 second after the initiation. Overpower transient due to withdrawal of a control rod in 1000 MWe homogeneous, radial heterogeneous and axial heterogeneous LMFBR cores were analysed by IBIS. The earliest scram was triggered in the axial heter- ogeneous core and the coolant temperature rise was the smallest. In the case that the scram was not triggered, the fuel temperature reached the melting point before coolant boiling or cladmelting. The largest power increase was observed in the homogeneous cores. The time to reach the fuel melting point was the largest in the axial heterogeneous core due to the small reactivity insertion rate in.the axial blanket. 1. Introduction In the evaluation of large, dilute and'in particular heterogeneous liquid metal fast breeder reactor (LMFBR) performance for the purposes of design, optimization and safety analysis, space-time kinetic calculations are needed. Two-dimensional space- time kinetics calculation code, FX2-TH made feasible.an evaluation of the impor of spatial effects in the calculation of operational fast reactor transients. KU Analysis of local perturbations, however, requires essentially three-dimensional cal- culation. For example, withdrawal of an asymmetric ccintrol rod cannot be modeled by neither two-dimensional R-Z nor triangular geometry. A three-dimensional (hexagonal- Z) nuclear reactor kinetics code IBIS was developed by us for large fast breeder reactor trz+sient analysis. 13,41' The code takes into account feedback effects from changes in both the average fuel and coolant temperatures. Sodium boiling feedback can also be considered in the code, while FX2-TH assumes no bo' Detailed description of IBIS is given in other documents. [ 3yyg tI',",,'yt :"s=yrye;;y reviewed as follows: The code is designed for transient analysis of a fast breeder reactor in hexagonal-Z geometry. The source-free, time-dependent, multi-energy group diffusion equations are used to describe the neutronic behavior of the core. The equations are solved by using the quasi-static method. The point kinetics equations is solved for an ampli- tude function with periodic recalculation of the space- and time-dependent multigroup shape function. Nine-point difference approximation to neutron transport is used to solve shape function equation in hexagonal geometry. Successive over-relaxhtion method (SOR) is used for an accerelation of the calculation. The neutronic solutions are based on a three group cross section set. In the present study the cross sections are collapsed from JARRI fast 25 group set. The purpose of thermal-hydraulic calcu- lation of IBIS is to reasonably predict the initiation time and the propagationof sodium voiding, and to obtain the temperature distribution of fuel pellet. The fuel heat transport model employs a solutionof the heat conductibn equation in an one- dimensional(radia1) fuel pellet, gap, clad and coolant configuration. Axial and angular conduction of heat are thought to be relatively unimportant for the class of problems under consideration with IBIS. The channel is divided into axial segments (up to 20), and the temperature calculations are made for each of the sections in succession following the direction of coolant flow. Some assumptions are also iu- eluded in the thermal analysis: 1. Behavior of one-subassembly can be represented by the single fuel pinaudits associated coolant model. 2. The geometry does not change and the fuel does not expand. 3. No heat transport occurs between subassemblies. 4. The pressure changewhichis induced by sodiumvoiding in a subassembly has uo effect on another subassembly. Two different models are used for simulating boiling expulsion. A slip-flow two-phase model is used for the initial portion and up to short time after flow reversal when resonably large void fraction exists. Since the slip-flow model is less meaningful from a physical standpoint when vaporvoid fraction is approaching 1.0 and coolant is being expelled from both ends of the channel, a switch is then made to a simple slug model to continue the voiding calculation. Throughout all the coolant-dynamics calculations, the coolant channel geometry is assumed to remain intact. The calculated temporary and spatial void distribution is then used to obtain the coolant-voiding component of feedback reactivity. a 2.Conpaxison of 2-D and 3-D kinetics Au overpower transient due to the withdrawal of a single control rod was analysed by FX2-TH (two-dimensional) and by-IBIS (three-dimensional). The results are compared in chapter 2.1 for central control rod withdrawal of a homogeneous LMFBR and in chapter 2.2 for peripheral control rod withdrawal. The core coufigu- rations are shown inFig. I. The reactor power is 500 MW thermal and active core size is 1 n high and 1.85 m in diameter. The core characteristics are summarised in Table I. The values are similar to the parameters of Super Pheuix 1, but the radial blanket assemblies are replaced by the stainless steel reflectors for the simplicity of calculation. Only one control rod is located in the core at the position C or P in Fig. 1. All others are fuel assemblies with axial blanket regions. Both R-Z and triangular geometry were used for FX2-TN analysis. Equivalent radius was used for the R-Z model in order that the volume should be the sane as that of the Hexagonal-Z model. The transverse buckling for triangular geometry analysis was determ'ned by using the two-dimensional diffusion calculation code, APOLLO in R-Z geometry. &I a 2.1 Withdrawal of a central control rod Enrichment of the core and the B4C volume fraction of the central control rod were determined from the results of steady state calculations by using FX2-TH code in R-Z geometry under the following condition : (1) The effective multiplication factor (keff ) should be unity at full insertion of the rod (2) The worth of the rod should be about one dollar. The enrichment of the Pu02 fuel was 15.69 % and the B4C volume fraction in the control rod was 0.562 X. Steady state of the reactor was analysed by IBIS and FX2-TH (triangular geometry). The results are compared in Table II. Values of keff agree rather well with each other. Thus the diffusion calculation routine of IBIS is verified. The radial temperature distributions in the core are compared in Fig. 2. The central control rod was fully inserted. R-Z geometry was used for FX2-TH the calcu- lation. Both coolant and fuel temperature distributions agree very well. The result shows that the steady state thermal and hydraulic calculation of IBIS is valid. Radial reactor power distributions also agree well with each other. Transient behavior due CO withdrawal of the central control rod was analysed by FXZ-TH and IBIS. The rate of the withdrawal was 100 cm/set. The net reactivity, taking into account thermal and hydraulic feedback effects, for this rate of inser- tion is shown in Fig. 3 as a function of time. The fuel temperature increase in the hottest subassembly during the transient is displayed in Fig. 4. The net reactivity and the temperature increase predicted by IBIS agrees well with that of FXZ-TH in R-Z geometry. Thus we think that IBIS is also valid for fast breeder reactor transient analysis with reactivity feedback effect. The slight difference of net reactivity which is observed in Fig. 3 is due to difference in the rod geometry in hexagonal-z and R-Z approximation. The slight difference may also be due to the numerical error of the calculation. The prediction of FXZ-TH calculation in triangular geometry fails, because axial movement of the control rod cannot be well simulated by the constant decrease of B4C concentration in the rod. Abrupt decrease of net reactivity is observed,at 1.0 set since there is no axial blanket region in the triangular model. 2.2 Withdrawal of a peripheral control rod Comparison of two-dimensional calculation by FX2-TH and three-dimensional calcu- lationby IBIS was also made in the analysis of an overpower transient due to as- ymmetric reactivity insertion by a peripheral control rod. The core configuration for the analysis is the same as shown in Fig; 1, but the only one control rod locates at the peripheral position'"P". AC first enrichment of the core and B4C volume fraction of the control rod were determined from steady state calculation in the same way as in chapter 2.1. The effective multiplication factors with full-in and full out of the control rod are shown in:~the left column of table III. The difference in L effective multiplication factors or the control rod worth differs with one another. Both FX2-TH calculations had approximations: The peripheral control rod was repre- sented by a ring-shape in the R-Z geometry and axial temperature distribution was neglected in the triangular geometry.
Details
-
File Typepdf
-
Upload Time-
-
Content LanguagesEnglish
-
Upload UserAnonymous/Not logged-in
-
File Pages18 Page
-
File Size-