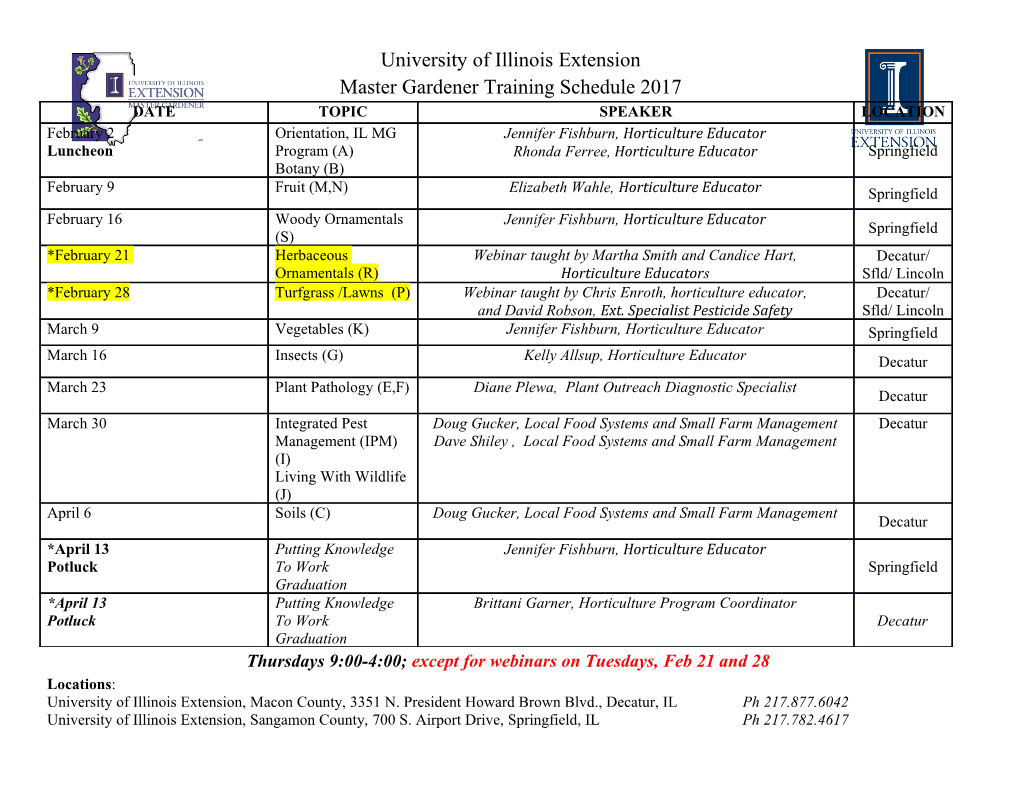
Torque and Reactive Power Control of a Doubly-Fed Induction Machine by Position Sensorless Scheme Wei Cheng Longya Xu Student Member, IEEE Senior Member, IEEE The Ohio State University Department of Electrical Engineering 2015 Neil Avenue Columbus, Ohio 43210 L. Introduction scheme is proposed. Compared to the other position sensorless schemes for doubly fed machine, &e proposed Doubly fed wound rotor induction machine with control method uses only the rotor voltages and currents vector control is very attractive to the high performance, as the feed back signals, which substantially reduces the variable speed drive and generating applications[ 1-31. costs and enhances relibility of the position sensorless In variable speed drive application, the so-called slip control scheme of the doubly fed AC machine[8,9]. power recovering scheme is a common practice where the Independent control of torque and reactive power is also power due to the rotor slip belowlabove synchronous possible, and the doubly fed system can achieve unity or speed is recovered to/supplied from the power source, leading power factor, in addition to variable speed resulting a high efficiency variable speed system. In operation. variable speed generating application, the doubly fed induction machine is most suited for variable-speed constant-frequency generating systems in which the speed of the prime mover is allowed to vary within a A. Configuration of Doubly Fed Induction Machine certain range (sub- and super synchronous speed), but the System output electrical power is always maintained at a constant frequency. In such a case, the doubly fed The configuration of a variable speed doubly induction machine is actually in the dual mode of fed induction machine system is shown in 1. variable speed drive system. Fig. The fundamental feature of the doubly fed induction machine system, including the drive and generating systems, is that the power processed by the power converter is only a small fraction of the total BiWional A system power. Therefore, for a very large rating system Power-Flow - it is possible to use a high-frequency switching PWM Convcttcr - converter to achieve high performance, such as fast dynamic response, low harmonic distortion, high efficiency, etc., without cost penalty. However, a high resolution rotor position sensor is generally needed for Fig. 1 Configuration of Doubly fed Induction Machine the proper operation of the doubly fed induction machine system systems. The major component of the system is a wound rotor Research has been very active in recent years to induction machine which needs to be excited at both the eliminate position sensors in field orientation stator and rotor terminals. It is common practice that the controlled cage rotor induction machine and the results stator winding is connected to the AC power supply are promising[4-61. In a cage rotor induction machine, directly, while the rotor winding is connected to the the rotor current is passively induced and the rotor field power supply through a variable frequency power is subsequently defined by the induced current. Yet, for converter. To obtain sub- and sup-synchronous speed the doubly excited induction machine the rotor field is operation, the power converter of the rotor winding must explicitly defined by the external excitation source be able to handle slip power in both directions [2] using which requires synchronization with respect to the stator a PWM voltage source inverter. Among the three power field. Therefore, without using a shaft position sensor, flow ports, i.e. the stator terminals. the rotor terminals, vector or field orientation control of a doubly fed and the rotor shaft, the rotor terminals act as the energy induction machine is more complicated than that of a regulating port, balancing the power flow of the entire singly-excited cage rotor machine. system. For example, when the shaft speed is below synchronous speed, a small portion of power is subtracted from the system through the rotor terminals In this paper, a novel control strategy to so that the power input to the system through the stator realize torque and reactive power control of a doubly winding is balanced by the power output from both excited induction machine using position sensorless 0-7803-1993-1194 $4.00 0 1994 IEEE 496 mechanical shaft and the rotor circuit. Similarly, when C. Reactive Power Control Through Rotor Currents the shaft speed is above synchronous speed, a small portion of power is added to the system through the rotor The reactive power of the doubly fed induction circuit. While the example is given in terms of motor machine system can be controlled through the rotor operation, it is straightforward to prove that for current vector to realize unity or.leading power factor generator operation, the rotor circuit functions in a operation. Assuming that the required reactive power to similar manner. the stator is Q, which can be expressed in the d-q-0 reference frame as B. Basic Equations and Operation Principles The operation principle of the variable speed The reactive power Qs can be referred to the rotor side and doubly fed induction machine can be conveniently expressed in terms of rotor quantities as analyzed by the classical rotating field theory with the well-known d-q-0 transformation. By inspection, the stator and rotor equations are written as follows in the matrix form. if the reactive power consumed by the stator leakage inductance is very small and neglected. After the d-q-0 transformation, the equations, in the synchronous reference frame, are In a doubly fed induction machine the airgap flux is determined largely by the stator voltage which (3) has a constant magnitude and frequency. Hence, it is reasonable to further assume that the airgap flux is constant. According to Eqs. (11) and (12), if the rotor current idr is controlled, the reactive power or the power where we is the speed of the synchronous reference frame, factor can be controlled. Again, for reactive power and wjs the rotor speed. control, the rotor speed and the rotor position must be known for the rotor current vector projection. (see Appendix) The torque equation becomes Lu. Estimation of Toraue Anele and Rotoy wherein &,,, = &,& -AbLts SDeed and $dm =&dr --iqdr Ltr As discussed above, in order to have precise control over the torque and reactive power (or power In Eq. 6 is the spatial angle between the airgap flux (5), factor) of the doubly fed induction machine, we need to and rotor current vectors (named torque angle in this paper) seen in the synchronous reference frame. With maintain a controllable torque angle, 6, or a controllable the alignment of the airgap flux to the d-axis of the rotor current vector, liqdri. For the doubly fed induction reference frame, we will have machine system using a high resolution shaft encoder, A+,,=&+,, and hm=O. (7) the rotor position is constantly sensed to ensure that the The torque equation is reduced to required slip frequency, CO,, satisfies the equation w, = we- 0,. The orientation of the rotor current vector is realized Te-22 -?E Ihdml Iiqrl (8) by the final tuning of the slip frequency so that the In order for rotor current vector in command currents i and idr are projected orthogonal 4,. synchronization with the stator current vector, the and parallel to the airgap tlux respectively. In the frequency of the rotor current, a,, must satisfy the slip following sections, we will discuss how i,, and idr are frequency constraint projected to the right position without the use of a costly w, = oe-w, (9) position sensor. Furthermore, for field orientation control, 6 must be maintained at go', or equivalently, the current vector has A. Estimation of Torque Angle to maintain orthogonal to the airgap flux. For a general vector control, the rotor current vector is controlled with It is extremely important to realize that the a predetermined angle with respect to the airgap flux. It electromagnetic torque can be viewed as the result of the is because of Eq. (9) and the field orientation or vector interaction between rotor current and airgap flux, control that the rotor speed and position must be regardless of the seleciion of the reference frame. That measured (or estimated) instantaneously so that the rotor is, Equations current vector can be correctly positioned. 497 A ^h m i r + Lxm ixr cos$= 2 (20) km ir Taking the inverse of sin6 and cos6 terms, the torque angle 6 is uniquely determined. Similar to the computation of sine term, the needed inputs for Eq. (20) are rotor side variables which are readily available and no are equivalent. In Eqs. (13-14), we have used subscripts additional sensing is needed. of d-q, and x-y to differentiate the selection of the reference frames tied to the synchronous and rotor circuit B. Control of Torque Angle frame respectively. Since Eqs. (13-14) are equivalent, observation of the magnitudes of flux and current, as well It is interesting to note that by using the rotor as the electromagnetic torque, are independent of the voltages and currents, the torque angle 6 is estimated reference frame selection. One can estimate the toraue without any transformation. Nevertheless, the estimated angle in one reference frame. and then use the estimated A results in other reference frames. Furthermore, the airgap angle 6 can be used in any other reference frames. Using flux can be estimated from either the stator, rotor or the estimated angle of ^s as the feedback variable, it is combined circuit. Therefore, one can always choose the possible to force the actual 6 to follow the desired value. most convenient circuit, that of the stator or rotor, in the The scheme of the torque angle estimation and control is most convenient reference frame, the rotor or summarized as shown in Fig.
Details
-
File Typepdf
-
Upload Time-
-
Content LanguagesEnglish
-
Upload UserAnonymous/Not logged-in
-
File Pages7 Page
-
File Size-