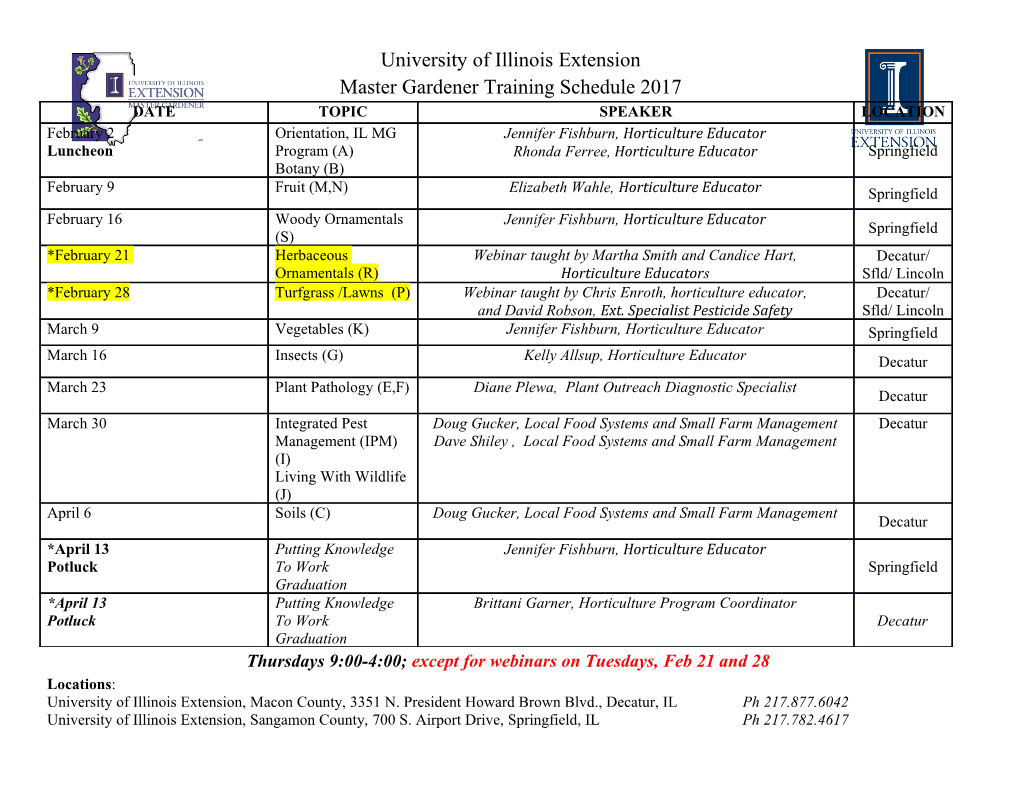
RURAL AND ENVIRONMENTAL ENGINEERING, LANDSCAPE ARCHITECTURE DOI: 10.22616/rrd.24.2018.031 CONCEPTUAL DESIGN OF MODULAR MULTI FUNCTIONAL AGRICULTURAL MOBILE ROBOT Aldis Pecka, Vitalijs Osadcuks Latvia University of Life Sciences and Technologies, Latvia [email protected] Abstract In order to improve competitiveness in today’s business environment, farmers also have to think about the rapid technological development in their enterprises. The most important factor that can positively influence the progress of the agricultural sector is the application of modern, efficient and labor-saving technologies at the various stages of crop growing and processing. Introduction of robotics in the farming processes emerges as one of the options. Current state of technologies allows only a few tasks processed by robots to be technologically and economically viably; the most relevant example is lawn mowing robots. One of the issues that prevents widespread use of robots in agriculture is that there are still no regulations or standards in the robotic sector for the industry to allow each robot manufacturer to follow them, such as mountable equipment communication protocols, dimensions of chassis and body, control systems including sensors and actuators etc. Each robot developer chooses his own approach and interpretation in robot protocols and modules. This article presents a conceptual design of mobile robot “Formica 01” for various agricultural applications. A prototype of the proposed design has been developed and in the article various cases of its usage on strawberry fields have been described. Key words: agricultural, mobile robot, modular. Introduction Verdouw, & Bogaardt, 2017). In automation of Food demand in the world is increasingly growing, greenhouse operations, where the environment is more especially it is relevant for traditional European-type predictable, stationary industrial robots in the form of food. This demand will require the use of agricultural CNC machines are used. Consumer mobile robots are land more effectively, mitigating environmental still in their development stages (Reddy, 2016). The impacts (National Farmers’ Federation, 2013). Some aim of the study is to develop conceptual design of of the negative factors are pollution from fossil mobile robot “Formica 01” for various agricultural fuels and other technical liquids used in engines and applications, such as inspection, transport, sprayer, transmission, land compaction created by using heavy weed destruction etc. based on selected similar designs tractor units, problems arising from monoculture found in literature and compare them. crop growing (land degradation and extensive use of pest and disease fighting chemicals) (Llewellyn & Materials and Methods Demden, 2010). One of the future perspectives is the Mechanical design and drive. The mechanical introduction of mobile robots in agriculture, where construction is based on a four-wheel base, divided groups or even swarms of smaller robots interact into two drive modules each consisting of motors and to process, inspect or harvest crops. Agricultural gearing for two wheels. The blocks are independent robots are forced to operate in highly stochastic and manageable separately, see image below in Figure environment. Changing environmental conditions, 1. Each driving wheel has one 350 W brushed DC such as terrain, road surfaces, ambient lighting, motor at nominal voltage 24 V. Motors have built-in biological objects, which can change color, height, spur gear transmission with ratio 1:9.78, which gives volume and other parameters, pose challenges for 10 Nm torque and 306 rpm revolution speed at motor mobile robot technology (Kim et al., 2011). To enable axis. Motor axis and wheels are coupled by means robot technology to enter the agricultural sector, it of chain transmission with ration 1:4 resulting in the must be constructively simple, highly reliable, flexible total gear ratio of 1:39 and 40 Nm and 76 rpm on the and, last but not least, inexpensive. Consequently, it axis of wheel. Robot wheels are with camera tires and poses a challenge for robot developers to develop with diameter of 400 mm, with maximum load 200 kg various technical solutions. Mobile robot solutions are on each; maximum speed is 10 km·h-1. Self-weight not widely available on the market today. The most of the robot is 100 kg, full weight is 300 kg. With popular and most affordable ones are feeding robots full payload robot can overpass road rise of up to 35 in barns (Lely Juno 100), lawn mowers (Husqvarna degrees. Each wheel is operated at constant speed. To Automower) (Grossi et al., 2016) and drones for field enable the robot to maneuver, different speed is set to imaging in precision agriculture. Scientific articles wheels on each side. The principle is the same as for discuss numerous mobile robot designs. Well- known caterpillar tractor. players in the agricultural industry like John Deere, Space between the drive modules is dedicated to Bosh, Monsanto have also made large investments the frame with power source (battery unit), control in the development of agricultural robots (Wolfert, system module and application-specific equipment 202 RESEARCH FOR RURAL DEVELOPMENT 2018, VOLUME 1 CONCEPTUAL DESIGN OF MODULAR MULTI FUNCTIONAL DOI: 10.22616/rrd.24.2018.031 AGRICULTURAL MOBILE ROBOT Aldis Pecka, Vitālijs Osadčuks Payload box DOI: 10.22616/rrd.24.2018.031 Battery pack and controll unit Payload box Motor Battery pack andGear controll box unit Figure 1. Mechanical construction of “Formica 01”. Figure 1. Mechanical construction of “Formica 01”. (trolley,Space soilbetween sampler, the drive weed modules fighting is dedicated unit etc.). to theThe frame this with battery power setup source the (battery robot unit),can go control on asphalt system road Motor drivemodule modules and applicationare designed-specific so that equipment they can (trolley, be easily soil sampler,at the weedmaximum fighting speed unit etc.). of approximately The drive modules 0.5 are h. One detacheddesigned from so that the they central can be frame easily detachedusing screws; from the and central of frame the usingreasons screws; using and lead-acid applicatio nbatteries equipment instead then of can be changed. From this also comes the strength of the proposed design. It is possible to adjust easily the track application equipment then can be changed. From Gearlithium-based box ones is the possibility to charge and thiswidth also tocomes make possiblethe strength the operation of the proposedof robot along design. plant rowsdischarge with different them at sizes temperatures. below –10 °C, without It is possible to adjust easily the track width to make significant loss in capacity. Besides battery unit the possible the operation of robot along plant rows with Batteryframe unit between drive modules holds the main control Central unit Figure 1. Mechanical construction of “Formica 01”. different sizes. module, which consists of motor driver power stages, Space between the drive modules is dedicated to the frame with power source (battery unit), control system Power source and electrical system design. electronic24 V controlDC unit (ECU) for the motor, lighting, Lead-acidmodule and batteries application are used-specific as a powerequipment source. (trolley, Two soilexternal sampler, equipment weed fighting control unit4 xand etc.). sensor The reading, drive modules motor are DC/DC 4 x batteriesdesigned are so connected thatControl they can inunit series be easily5V with detached the total voltagefrom the centraldrivers frame and usingsingle screws; board and computer applicatio Raspberryn equipment PI then WiFi PWM of 24 V and average energy charge 960 Wh. Using Motorfor high driver level control4 (localization,MotorMotor path planning, can be changed. From this also comes the strength of theMotorMotor proposed driver driver design. It is possibleMotor to adjust easily the track width to make possible the operation3.3V of robot along plant Motorrows driver with different sizesMotor. SPI Electronic 4 control unit 4 x (ECU) AnalogBattery signal unit Central unitPWM Inductive sensors RC reciver 24 V DC4 RC Pulse 4 x wireless DC/DC 4 x Control unit 5V WiFi PWM Motor driver 4 MotorMotor MotorMotor driver driver Motor RC 3.3V Motor driver Motor Bluetooth wireless PC SPI WiFi Electronic RC transmitter Bluetooth4 Play controlApplication unit : - Control Sation 4 RC 4 x (ECU) BluetoothAnalog signal PWM - Telemetry Inductive sensors RC reciver 4 RC Pulse wireless Figure 2. Mechanical construction of the mobile robot. Power source and electrical system design. Lead-acid batteries are used as a power source. Two batteries are connected in seriesRC with the total voltage of 24 V and average energy charge 960 Wh. Using this battery setup Bluetooth the robot canwireless go on asphalt road at the maximumPC speed of approximately 0.5 h. One of the reasons using lead- acid batteries instead of lithium-basedWiFi ones is the possibility to charge and discharge them at temperatures below RC transmitter Application: Bluetooth Play –10 °C, without significant loss in capacity. Besides battery unit the frame between Sationdrive 4modules RC holds the - Control Bluetooth - Telemetry Figure 2. Mechanical construction of the mobile robot. Figure 2. Mechanical construction of the mobile robot. Power source and electrical system design. Lead-acid batteries are used as a power source. Two batteries are RESEARCHconnected inFOR series RURAL with DEVELOPMENTthe total voltage of2018, 24 VOLUMEV
Details
-
File Typepdf
-
Upload Time-
-
Content LanguagesEnglish
-
Upload UserAnonymous/Not logged-in
-
File Pages5 Page
-
File Size-