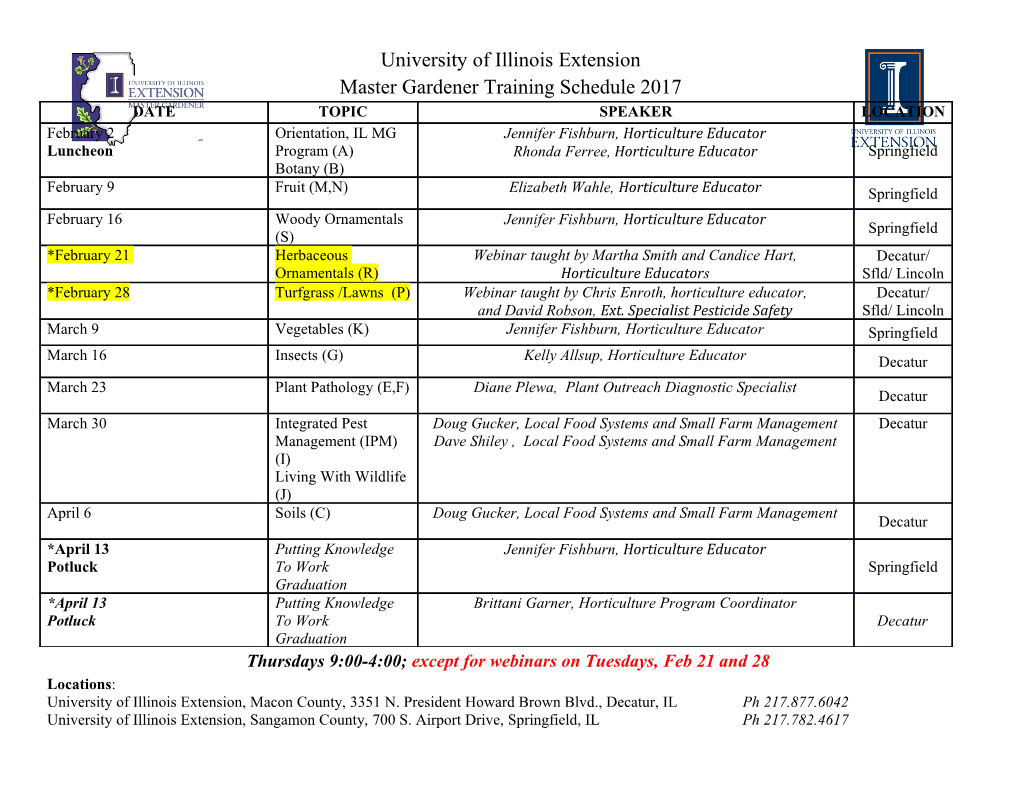
International Research Journal of Engineering and Technology (IRJET) e-ISSN: 2395-0056 Volume: 07 Issue: 08 | Aug 2020 www.irjet.net p-ISSN: 2395-0072 COMPREHENSIVE OVERVIEW OF HYBRID VEHICLE DRIVETRAINS Zelieus Namirian1 1Student, Mechanical Engineering, Mumbai University, India ---------------------------------------------------------------------***--------------------------------------------------------------------- Abstract: The goal of this study is to promote a deeper briefly addresses hybrid battery and fuel cell vehicles (BEVs understanding of the EMS, basics, along with hybrid drive and FCVs) as other alternative power trains. trains by reviewing the current literature and defining the key research needs. The facets of optimization for powertrain and 1.1 POWER TRAIN, DRIVE TRAIN DEMARCATION EMS operation within the research sector are extensive. This article outlines the vital keys for achieving optimal control The powertrain or power plant in a motor vehicle strategies, highlighting gaps in expertise, and providing contains the main components producing power and suggestions for future study. This study's contributions are as reallocating the electricity to the ground surface, water, or follows: First, an outline of EMS, power / drive train concepts, air. That in itself includes the engine, transmission, drive various sequences, Series, Parallel and Power split (series / shafts, differentials, and final drive (driving wheels, seamless parallel) topologies, and their system configuration is given track as in defense tanks or caterpillar tractors, rudder, etc.). alongside various vehicle modelling approaches. The In a wider context, the powertrain comprises all the elements remainder of this report is structured as a section that that are used to turn storage energy (chemical, electrical, classifies hybridization types-mild/moderate, Descriptions of nuclear, kinetic, future, etc.) into kinetic power for Full HEVs (FHEVs), Plug-in HEVs (PHEVs), and identifies the propulsion. This covers multi-power and non-wheel-based prospective prospects for potential research developments. vehicle use. Finally, a few closing thoughts. Hybrid powertrains also include one or more electric Key Words: EMS-Energy Management Systems, HEVs- traction engines which work to drive the wheels of the Hybrid Vehicles, Drive Trains, Series vehicle. All-powered vehicles ("electric cars"), depending Hybrids/Drivetrains, Parallel Hybrids/Drivetrains, entirely on electric motors for propulsion, remove the engine Power Split Hybrids, Full Hybrids, Plug-in Hybrids. altogether. 1. INTRODUCTION The driveline or drivetrain of a motor vehicle is composed of the powertrain components except the engine.In Hybrid cars achieve decreased fuel consumption by fact it is the collection of components that supply power from adding both an energy storage system and a means of the engine or motor of a vehicle to the wheels of the vehicle. transforming the stored energy into mechanical motion in The configuration of the drivetrain in hybrid-electric cars the drive train, in addition to an internal combustion (IC) defines how the electric motor operates in tandem with the motor. Such hybrids can also transform mechanical motion traditional engine. The drivetrain has an impact on the into renewable energy. The holding unit may be a pump, a mechanical performance, fuel consumption, and purchase flywheel, compressible fluid, elastomer, or ultra-capacitor in price of the vehicle. This is the part of a car that varies a more general sense. The way to transfer energy between according to whether a car is front-wheel, rear-wheel, or storage and mechanical motion is by using one or more four-wheel drive, or less-common six-wheel or eight-wheel engines / generators (e.g., electrical, pneumatic, hydraulic). drive, after the prime mover. In motor mode, these devices convert stored energy into mechanical movement to drive the vehicle and in generator mode, these devices convert vehicle movement into stored 1.2 POWER TRAIN DESIGN AND EMS (ENERGY energy by supplying part of the vehicle braking mechanism MANAGEMENT SYSTEMS) (regeneration). Likewise, a fuel cell car is also a hybrid in which the fuel cell replaces the internal combustion engine, The hybrid and electric vehicle powertrain but this design would also need extra energy storage to configuration protocol covers various stages, while the satisfy peak power demands and enable the fuel cell to be present analysis focuses on the topology of the powertrain scaled to the typical power need. and the construction of an EMS (Energy Management System). With that in view, Fig. 1 is an example of a system- In addition to adding an electric motor, hybrid level design process for an energy-efficient powertrain. designs that have idle-stop and regenerative braking features, and in their traditional counterpart model, the IC First, a topology for the powertrain will be selected engine is also downsized from this. Hybrid vehicle depending on a vehicle's expected transport allocation architectures using an internal combustion engine are considering the trade-off between cost and performance. included in this review, and battery-energy storage. It also The second step, based on the chosen topology, is to decide © 2020, IRJET | Impact Factor value: 7.529 | ISO 9001:2008 Certified Journal | Page 1 International Research Journal of Engineering and Technology (IRJET) e-ISSN: 2395-0056 Volume: 07 Issue: 08 | Aug 2020 www.irjet.net p-ISSN: 2395-0072 the technology and measurements needed for the respective of the FTP evaluation period, on which the conclusions in hybrid elements, including the energy storage system (e.g., this study are based.[5] battery, supercapacitor and/or fuel cell), electric motors, and DC-DC/DC-AC converters. 2. HYBRID VEHICLE POWER TRAIN SYSTEM TOPOLOGIES The objective function of the EMS optimization problem is usually combined with the selection of topology As already mentioned, Hybrid vehicle drive trains relay for the powertrain, while the equipment and size of power for hybrid vehicles to the driving wheels. A hybrid components are viewed as constraints of optimization. EMSs vehicle has multiple motive forms:[4] should play a key role in designing sustainable cars for young generations. An EMS’s key aim is to divide the input By burning oil, a hybrid may receive its energy, but capacity by choosing optimum multi-motif outlets to meet switch between an electric motor and a combustion moving demands. Therefore, an effective EMS can help to engine. minimize fuel consumption by taking into account battery An internal combustion engine and batteries in efficiency (i.e. current rate and lifetime) and tailpipe diesel hybrid vehicles or ultra-capacitors. emissions. A power tank and fuel cell electric engine battery. Hybrid electric cars incorporate an ICE combined with a battery or supercapacitor that can recharge the batteries or fuel the engine. Other electric powertrains use energy-saving flywheels. Overhead electric lines and batteries in Trolley hybrid buses.(One of the first examples of hybrid land transportation is New Jersey's 'trackless' trolleybus trial, which lasted from 1935 to 1948 and normally used wired traction then. The trolleybus Fig. 1. System-level strategy used to accomplish an energy- was built with an internal combustion engine (ICE) efficient powertrain to control the mechanical drivetrain directly, and not Source- [1] to produce energy for the traction engine. This Due to the dynamic configuration of powertrain systems and allowed the vehicle to be used for income service unpredictable driving situations, designing a highly effective where touch wire was not available. and flexible EMS is a daunting activity though. In fact, the EMS would provide a fairly simple and efficient real-time HEVs are therefore classified as providing an internal controller with a reasonable processing speed for a global combustion engine and one or more electrical machines optimisation algorithm to be applied. which can provide tractive force to propel the vehicle in any combination. An exception to this concept is the basic idle- There are abundant hybrid vehicles in fabrication, stop configuration which does not have tractive force however, diesel hybridization (compression ignition; CI) extracted from electricity. This section focuses on the core vehicles are projected to offer much lower performance characteristics of the major powertrain topologies for PHEVs advantages than gasoline vehicle hybridization, in part (Plug-in HEVs) / FEVs (Full Electric vehicles). First of all, it is because traditional CI vehicles also have lower fuel important to understand the operating modes of a consumption than equivalent gasoline vehicles. Additionally, powertrain topology to devise an EMS optimization problem. CI vehicles do have very low fuel consumption at idle, Different powertrain topologies with different capacities may rendering idle-stop’s advantages less desirable. Conventional be configured by changing the drive source relation CI power trains are more costly than their gasoline equivalent, which, when applied to the hybridization prices, A coupling may be either mechanical or electrical. Based makes a CI hybrid power train very costly with the extra on the geometric arrangement of the drives, turbines, savings in fuel consumption offered over and above either and engines, hybrid designs fall into three classes — switching to a hybrid or CI power train alone. As a result, parallel, linear, and mixed series / parallel
Details
-
File Typepdf
-
Upload Time-
-
Content LanguagesEnglish
-
Upload UserAnonymous/Not logged-in
-
File Pages10 Page
-
File Size-