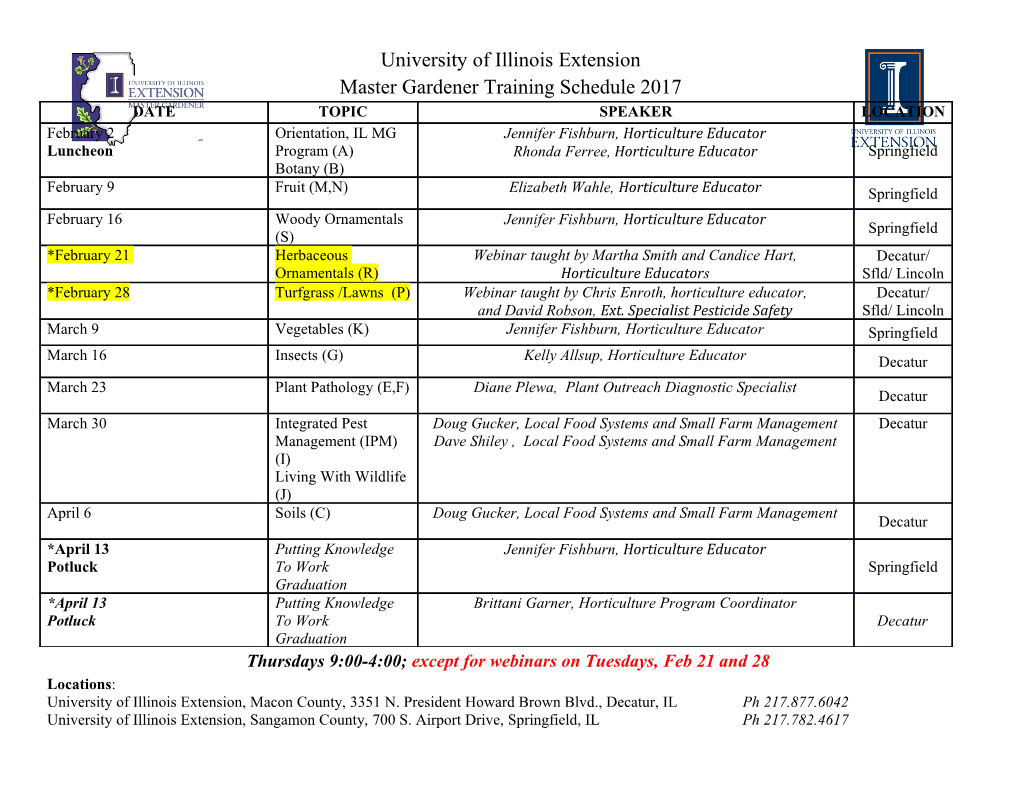
FREDERICK BENTHAM Theatre Consultants Services, London Control and stage lighting The key to stage lighting is control-optical, mechanical and electrical. Taken really seriously what we have to do is not just to illuminate the stage but to paint a picture with light. Before long that picture has to be replaced by another. This second picture may differ totally from its predecessor or but so slightly as to represent only small change of accent-a stressing of one area or a playing down of another. The tempo of such a change will have to range from the twinkling of an eye to a languid, virtually imperceptible creep. The use of the expression, ‘ paint a picture with light ’ suggests an artist in charge, but this is rarely achieved. It is a sad feature that specialist lighting designers may be skilled in the art of stage lighting but they are neither artists nor is what they do Art. They form one of a team concerned with the mechanics of putting a play on. Strive as we may, the various technical developments over the years, instead of making it easier for the artist to take over, in fact put him more and more in the hands of such a specialist. The artist sees the possibilities but he is scared off by the cumbersome complications of lighting as a medium. Nevertheless I and a few others like me have continued to work on the assumption that an instrumental approach is possible and that an artist should be able to sit down at some console vaguely related to an organ in form, there to function like an accompanist to fill in the essential link between the actor, the scenery and the audience’s eyes. On rare occasions one feels the message might be got over better with just light and the scenery. The lighting in that case almost takes on a solo role: I say ‘ almost ’ because when I have gone that far it has always seemed necessary to have music. Such variations for lighting and music can be conveniently called ‘ colour music ’ and may be regarded as fun for the switchboard operator to train on and certainly as an excellent means of trying out and demonstrating a new lighting control. It could well be that frustration, at the lack of a safety valve in the form of such ‘ solo ’ lighting, accounts for the overuse of lighting in some stage productions. Then again in the ergonomics of the equipment provided there may be a tendency to design for all contingencies, whereas if one applied the maxim, ‘ don’t worry, it may never happen! ’ the facilities provided might be easier for ordinary mortals to understand. There is an obvious point which may get overlooked. Because light cannot perform in limbo, it is much harder to design an instrument to play it than one to play sound. Our installation completed, all we are left with will be a hundred or so meaningless patches of light awaiting a show on the stage which will tell us where to direct and how to focus them. Indeed, quite often all we are left with is a lot of circuits terminating in socket outlets. Electrically live they may be, but this does not make them come alive! With this in mind let us see where this type of theatre equipment has in fact got to. Stage lighting can be said to have begun in 1881 when the new Savoy Theatre, London, opened with the Gilbert and Sullivan opera, Patience. It is not the lighting required for this opera that makes this date important but the fact that for the first time anywhere an entire theatre was lit by electricity-using in fact Swan filament lamps and Siemens equipment. A good contemporary account of this installation appeared in the journal 225 Frederick Bentham Engineering of 3 March 1882. The account shows the theatre’s need even then to fade lights in and out with dimmers (of which there were six) rather than just to switch them on or off. In order that this article may become an eyewitness account, it is convenient to jump to 1932 and the opening of the Shakespeare Memorial Theatre (now known as the Royal Shakespeare) at Stratford-upon-Avon. There were 56 dimmers-a rather low number for a theatre of this importance. Indeed seen at this distance the stage lighting installation as a whole was very modest and an equivalent theatre of that time in Germany would have had about double the amount. The switchboard was a large cumbersome affair due to the British practice (which took an unconscionable time a-dying) of mounting the dimmers directly behind their operating handles. A lot of theatre electricians derived great comfort from the stout metal links joining the two. Except that in this case eight of them were liquid type and had to be operated remotely by tracker wire, all the rest were metal resistance. The supply was 230/460 V three wire DC. Where, as here, there were relatively few lighting circuits, dimmers were used mainly to fade from one lighting picture to another which accounts for the very crude mastering arrangements. Individual levers could be locked onto their shaft by a half turn of the handle and the big wheel turned from the centre. In any case extra labour to help push a few levers was readily available. No finesse was possible because the whole contraption was very large and therefore mounted out of the way on the side of the stage, with a rotten view therefore of the effects it produced. This kind of control survived a long time both here and in North America, although more sophisticated (but more expensive) equipment soon became available. During the 1930’s one had the frustrating experience of watching theatres rewire and instal new switchboards of this old type, at supply authority expense, to cater for the changeover to three phase AC. It might be thought that the first task was to get rid of resistance as a means of dimming but although autotransformers became common in Germany the energy saving was of little account compared to the increased capital cost. There was no subsidized theatre in Britain in those days. Nor was the facility of dimming a variable load to the same curve considered all that important. What was required was to reduce the size of the switchboard so as to turn it into a compact control panel or console-the load carrying dimmers and switches simply had to be remote from their controls. The German theatre achieved this with massed runs of tracker wire terminating in a compact regulator with a number of ingenious mechanical devices for mastering. The centres at which the levers were mounted went down from four and a half to one and a half inches. The real solution, however, was to have an electrical rather than a mechanical linkage between the dimmers and the control panel. There were two possibilities: a servo system operation of resistance or autotransformer dimmers or else an all electric system where there would be no moving parts. In fact the next lighting control the Stratford- upon-Avon theatre was to have was of this latter type. The dimmers were thyratron valves, used directly in the lamp circuit and grid controlled remotely by a potentiometer. Many years earlier indirect thyratrons providing the saturating current for load carrying reactors had been used in the United States for occasional prestige installations, the most famous of which was that in Radio City Music Hall. Installed in 1933 and consisting of 314 dimmers, it is still in use. The Stratford thyratron installation was put in for the summer season of 1951. There were 144 dimmers and although the control panel was duplicated (figure 1) it was still compact enough to be put into the Royal Box in the centre of the Dress Circle. It can be Control and stage lighting 227 appreciated that this position alone, no matter what the additional control facilities, represented a great step forward; the operator was able to see the effects produced on the stage. However, the duplicate panels with their massed control levers at one inch centres were also very important since this arrangement enabled one lighting picture to be held on the first panel while the second was being prepared and vice versa. Figure 1. 144 thyratron dimmers remotely controlled from a two preset desk. Similar to Stratford 1951. Although the thyratron installation remained in use until the end of 1971, it was rather temperamental and turned out to be more wasteful in use than a corresponding bank of resistances would have been. The trouble was that the heater filaments of the valves represented a considerable load since they all had to be on continuously ‘ at the ready ’ whether the circuit was in use at the time or not. Much puzzlement was caused at the time by the fact that these rooms were so much warmer than resistance dimmer rooms until it was realised that there was roughly the equivalent of a 10 kW fire burning continuously. There followed in consequence a revival of interest in the servo, and a golden decade of electromechanical remote control followed in this country. The system used was decidedly primitive but it was very reliable : iron wheels on a constantly revolving drive shaft were gripped by pairs of electromagnets and linked to cranks above and below the dimmer pivot to provide reversal. As many as 120 dimmers would be mounted in four or five tiers as one bank and driven by one variable speed motor.
Details
-
File Typepdf
-
Upload Time-
-
Content LanguagesEnglish
-
Upload UserAnonymous/Not logged-in
-
File Pages9 Page
-
File Size-