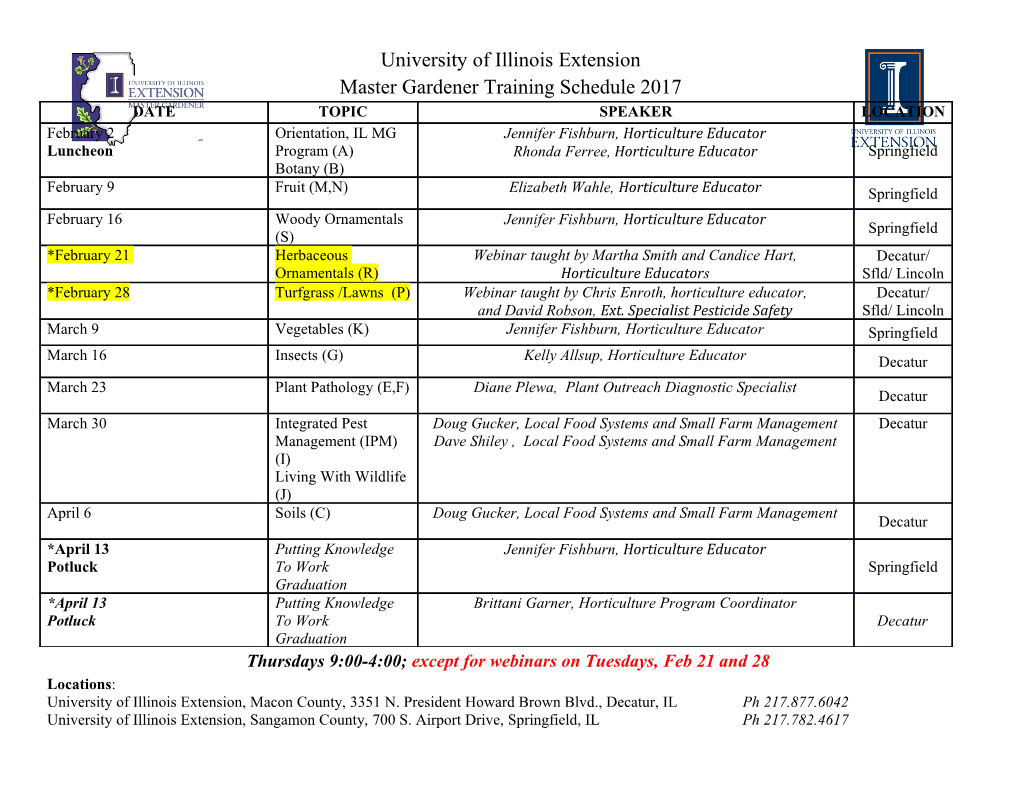
Development of an EV drivetrain for a small car by Ambarish Kulkarni BE, ME (MIE –Aust) A thesis submitted in fulfillment of the requirements for the degree of Doctor of Philosophy Faculty of Engineering and Industrial Sciences Swinburne University of Technology March 2014 Abstract Electrical vehicles (EVs) have a significant role in reducing transportation emissions and the dependence on fossil fuels. The government policies and taxation arrangements to support EVs have created new opportunities. This research has focused on the mechanical design of an in -wheel drivetrain for a small car. An in-wheel drivetrain has been selected to maximise the energy efficiency with reduced transmission loses. As a consequence, packaging of the motor has been confined to the rim envelope. Based on the selection of a specific small car, a corresponding low rolling resistance tyre has been chosen to increase the EV range. Accordingly, an optimised low mass rim has been developed. The conceptual and detailed design of the motor has been based on the rim envelope. In the motor design stage, a focused literature review and specific commercial drivetrain study have been carried out, which revealed that majority of current EVs use permanent magnet motors (PMMs). The main drawbacks of PMM are dependency and availability risks as well as higher costs of the rare earth elements. The switch reluctance motor (SRM) has been identified as a feasible alternative, because it uses more readily available materials such as steel and copper for the magnetic path. However, SRMs have reduced power density for a specific mass, which may result in large unsprung mass and undesirable driving characteristics for the EV. In the conceptual design stage, depending on the magnetic path orientation vertical and horizontal concepts were developed. Among the two alternative concepts developed, the vertical magnetic orientation using virtual reality (VR) has been chosen in the conceptual design. This is based on an assessment of: i) the maximised space utilisation, ii) the optimised magnetic path for stabilising 1mm air gap and iii) ease of the fitment and the assembly. In the detailed design, power density of the SRM has been further maximised by: (i) designing with two stabilised air gaps within the magnetic path and (ii ) space utilisation by integrating the motor with the wheel rather than as an add-on arrangement. In the mechanical sense, the stiffness of motor parts has become crucial for stabilising the air gap between stator and rotor. Therefore, this research has iii accomplished a thermo-structural optimisation using finite element methods (FEM) in ANSYS for motor shaft, hub and motor covers. Additionally, virtual reality (VR) and augmented reality (AR) based simulation studies have been carried out to maximise the space utilisation for the magnetic path. EV performance analyses have been conducted for optimisation of: i) rim, ii) brake, iii) suspension, iv) vehicle weight distribution and v) tyre slip. As the motor occupies the existing brake space and with the available limited packaging space the light weight brake design was essential. To increase the thermal stability and in order to fit within the limited space an increased surface area and reduced thickness disc brake has been designed. To minimise the thermally excited instability, FEM based optimisation has been carried out. A further ride and comfort study of an EV suspension using a quarter car and a Bode plot analysis has confirmed handling of the large unsprung mass. Life cycle of the EV suspension using the rain flow counting method and Palmgren-Miner rule has established the fatigue performance. The AR analysis has resulted in identification of operator safety and tyre serviceability using the NOISH equation. Finally, the performance of the EV specification has been demonstrated based on the range, fitment and the weight distribution models. In conclusion, this research has developed an in- wheel SRM drivetrain for a small car, which can be disseminated to the other vehicles with minimal modifications. Key words: EV, drivetrain, SRM, in-wheel, FEM, VR, AR, brake, rim, tyre and suspension iv Acknowledgement First of all I express my deep sense of gratitude and appreciation to my principal supervisor Professor Ajay Kapoor (Swinburne University of Technology, Melbourne Australia), for his in-depth knowledge, constant encouragement and guidance throughout this research. I gratefully acknowledge him for his intellectual contributions and timely advice. Moreover, I would like to sincerely thank him for his kind support, attention, care, constant encouragement, and persistence for excellence, which helped to perform such a challenging task. Next, I extend special thanks to my coordinating supervisor Dr. Mehran Ektesabi (Swinburne University of Technology, Melbourne Australia), for his great contributions and recommendations throughout this research. Always gave me constructive feedback and I am greatly benefited with his extensive domain knowledge on motors. Furthermore, my heartily thanks are dedicated to the Faculty of Engineering and Industrial Sciences, (Swinburne University of Technology, Melbourne Australia) and its staff, for developing me into a serious researcher. Also, I sincerely acknowledge Auto CRC for funding this research as a part of visionary program and greatly appreciate their financial support. Many thanks to Dr. Gary White (Research Manager for Auto CRC) and Dr. Howard Lovatt (Stream Leader, CSIRO), for mentoring me during this research. I also acknowledge Associate Professor Ekambaram Palaneeswaran, (Swinburne University of Technology, Melbourne Australia), for being a great mentor and philosophic supporter during my PhD. Finally, I wish to express my special thanks to my wife Sandhya Kulkarni, for her incredible cooperation, infinite love and encouragement all throughout this journey. Especially, I express deep sense of love and gratitude to my children, Anagha and Arnav, for their sacrifices and cooperation throughout this period. I am very much thankful to all my family members, friends and well-wishers who have been constantly supporting directly or indirectly during completion of my PhD research. v vi Dedicated to: My lovely wife and two kids vii viii Declaration I declare that this thesis represents my own work and has not been previously submitted to meet requirements for an award at this or any other higher education institution. To the best of my knowledge and belief, the thesis contains no material previously published or written by another person except where due acknowledgement has been made. Ambarish Kulkarni Date: 12-03-2014 ix x Contents Abstract iii Acknowledgements v Declaration ix Contents xi List of Figures xix List of Tables xxvii List of symbols xxix List of Abbreviations xxxvi Chapter 1 Introduction 1.1 Chapter overview 1 1.2 Background of research 1 1.2.1 Environmental issues 2 1.2.2 Government policies 4 1.2.3 Commercial viability 8 1.2.4 New opportunities 10 1.3 Research problem 13 1.4 Aim and objectives of research 14 1.5 Scope of the research 15 1.6 Overview methodological approach and outline 15 Chapter 2 Selection of an EV drivetrain 2.1 Chapter overview 19 2.2 Drivetrain selection 20 2.2.1 Conventional drivetrain 20 2.2.2 In-wheel drivetrain 21 2.2.3 By-wheel drivetrain 22 2.2.4 Drivetrain configuration selection 22 2.3 EV drivetrains in commercial cars 23 2.4 Motor selection 30 xi 2.4.1 Standards for motor design 30 2.4.2 Motor metaphors 31 2.4.3 Motor selection criteria 34 2.4.4 Brush and induction motors 35 2.4.5 Permanent magnet motor 37 2.4.6 Shortfalls of permanent magnet motor 40 2.4.7 Switch reluctance motor 41 2.4.8 Motor selection for an EV drivetrain 45 2.5 Summary 47 Chapter 3 Vehicle and wheel selection 3.1 Chapter overview 49 3.2 Vehicle selection for an in-wheel SRM 50 3.2.1 Vehicle mass to power requirement ratio 50 3.2.2 Mudguard clearance requirement 52 3.3 Car digitisation for virtual design 54 3.3.1 Digitisation process 54 3.3.2 Rim-tyre envelope 57 3.3.3 Brake system space requirement 58 3.4 Rim design 59 3.4.1 Rim-tyre sizes 60 3.4.2 Rim design 62 3.4.3 Material selection 65 3.4.4 Rim topology optimisation 67 3.4.4.1 Rim optimisation flow diagram 68 3.4.4.2 Finite element modelling 69 3.4.4.3 Material and boundary conditions 70 3.4.4.4 Loading 71 3.4.4.5 Finite element results 72 3.5 Tyre selection 76 3.6 Valve selection 80 3.9 Summary 81 xii Chapter 4 Motor design for an EV drivetrain 4.1 Chapter overview 83 4.2 Motor conceptual design 84 4.2.1 Preliminary free hand sketches 84 4.2.2 Concept evaluation 88 4.2.3 Magnetic path details 92 4.3 Motor detailed design 94 4.3.1 Motor packaging 95 4.3.1.1 Stage one motor design 96 4.3.1.2 Stage two motor design 97 4.3.1.3 Final motor design 98 4.3.2 Bearing selection 101 4.3.3 Shaft design 108 4.3.3.1 Finite element modelling-shaft 109 4.3.3.2 Load and boundary conditions-shaft 110 4.3.3.3 Finite element results-shaft 110 4.3.3.4 Finite element modelling-motor 111 4.3.3.5 Load and boundary conditions-motor 112 4.3.3.6 Finite element results -motor 113 4.3.3.7 Nut selection for motor assembly 114 4.3.3.6 Shaft final design 115 4.4 Summary 116 Chapter 5 Mechanical optimisation of motor 5.1 Chapter overview 121 5.2 Weight reduction of motor covers 122 5.2.1 Material selection 122 5.2.2 Mass optimisation 124 5.2.2.1 Finite element modelling 124 5.2.2.2 Load and boundary conditions 125 5.2.2.3 Finite element results 126 5.3 Space utilisation and assembly sequencing 126 xiii 5.3.1 Virtual
Details
-
File Typepdf
-
Upload Time-
-
Content LanguagesEnglish
-
Upload UserAnonymous/Not logged-in
-
File Pages341 Page
-
File Size-