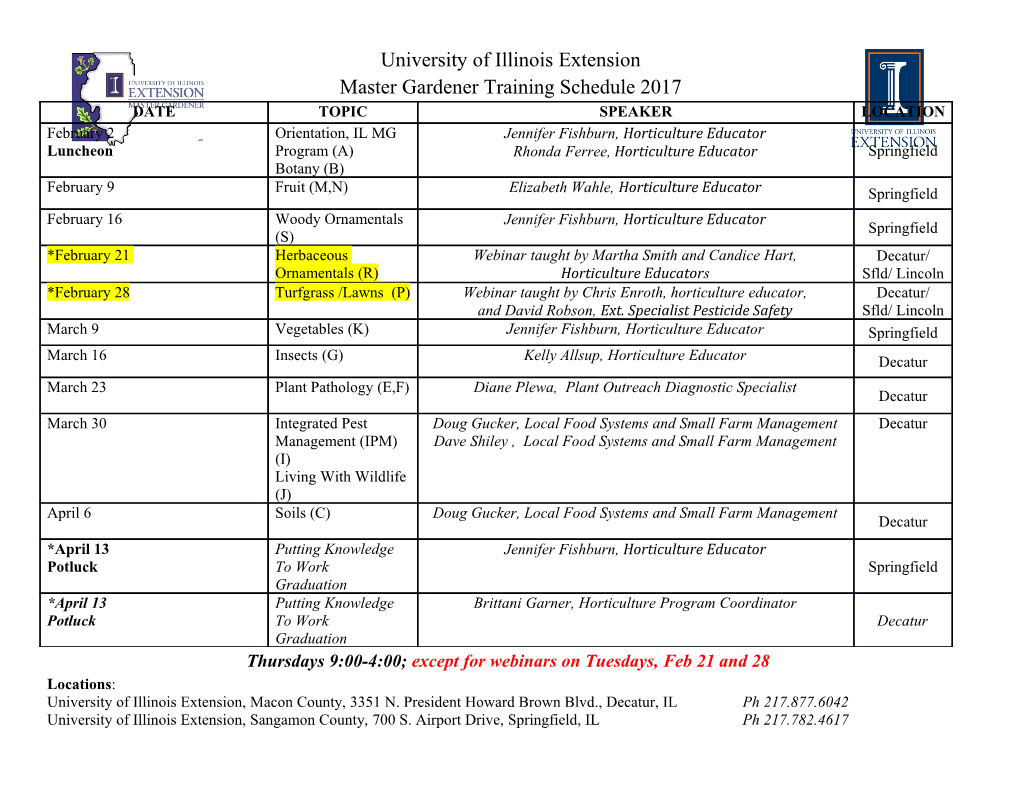
Volume 3, Issue 5, May – 2018 International Journal of Innovative Science and Research Technology ISSN No:-2456-2165 Review on Intermetallic and Ceramic Nanoparticle Coatings for Application in High Temperatures Gaurav Siwal, Mechanical Engineering Department, Dronacharya Group of Institutions, Greater Noida, U.P. Member of ISTE Abstract:- As compared to material with ordinary grain decide the electrical, optical and magnetic properties. As the size, Nano Materials have special properties. The Idea is to particle is reduced in size these energy bands get thin and study the properties and coating techniques for ceramic sharp. For Nano sized particles the electrons get scattered on and intermetallic nanostructure which could be deposited the surface and resistivity increases. as a protective layer. Some methods include Inert gas condensation, PVD, CVD, Sol-gel, Electrochemical D. Optical property deposition, thermal spray, and pulsed electro-spark When the size of a crystal becomes smaller and deposition. The composition of the material and comparable to wavelength of visible light, nanoparticles microstructure can be controlled using different electrodes, partially transmit the light which results in change of color. For and adjusting the parameters of the setup. Nano Material example Au nanoparticle of size between 30 - 500nm appears coatings on surface can modify chemical, mechanical and blue to red in color from larger to smaller size. electronic properties. It can also improve high-temperature corrosion and corrosive wear resistance. These E. Magnetic Property modification techniques can have various applications in The total magnetic moment is the property which turbine blades, engine parts for petrochemical, aerospace depends upon number of atoms; it depends upon the size of the and electronic device industries. cluster. It enhances orbital and spin moments on the surface of tiny nanoparticle. As the cluster size is increased at few Keywords:- Nanoparticles, Synthesis of nanoparticles, Nano nanometers the spin moment decreases because the presence of ceramics, Intermetallic, Deposition, Coating. atoms with low coordination number on the surface. I. INTRODUCTION F. Catalytic Property Surface atoms are the active centers for the catalytic The paper is all about a review on application of process. As compared common grain size material Nano nanomaterial in high temperatures. General aspects of material have more number of atoms on the surface. Due to nanomaterial as compared to bulk materials is discussed. which the Nano materials are highly reactive catalyst. [1] Various methods for synthesis of nanomaterial, Intermetallic Nano materials and Nano ceramics. Coating methods for Nano III. SYNTHESIS OF NANOPARTICLES materials and application in materials which are exposed to high temperatures. A. Physical Vapor Deposition (PVD) PVD is a thin film deposition process in which the II. PROPERTIES OF NANOMATERIALS material is heated to form vapors in high vacuum environment. These Vapors are deposited on a conductive surface as a pure A. Surface to Volume ratio metal or alloy coating. Now since the material is coated from The surface to the volume ratio is quite large in case of atom to atom or molecule to molecule, this process has highly nanoparticles .That is if 1cm of cube is broken in cubes of pure and high performance coatings as compared to 10nm edge than surface area is increased by 106 times. While electroplating. PVD coating process is a clean and environment in crystalline particles smaller than 10nm, the amount of atoms friendly process, as it does not releases any harmful gases or at the surface becomes more significant. The size of the particle toxins as compared to conventional coating process. is inversely proportional to the surface volume ratio. In 10nm particle 10% of atoms participate in surface atoms while in PVD process is widely used in solar industry as well as in 1nm particle more than half of atoms are surface atoms. surgical implants, as it gives highest purity coatings. Coatings produced by PVD are high wear and tear resistant and have B. Change in surface structure good hardness. Science these coatings reduce friction they find Each atom in volume of nanoparticles is surrounded by wide application in high performance moving parts like a specific number of atoms called coordination number. Thus automobile and tool industry. PVD coatings are resistant to decrease in coordination number of surface atom leads to corrosion, scratches and crapes, the have high finish and they weaker cohesive energy which could lead to reduction in do not fade. They find various application in decorative items, melting temperature. household fixtures, watches and tinting of glass. C. Electronic property In PVD process the material to be deposited is kept Valance electrons occupy the energy bands in crystalline inside a high vacuum chamber with pressure approximately 10 solids. The occupancy, width and separation of these bands to 2 mbar. The material is vaporized to form plasma of atoms IJISRT18MY53 www.ijisrt.com 255 Volume 3, Issue 5, May – 2018 International Journal of Innovative Science and Research Technology ISSN No:-2456-2165 or molecules and deposited on a substrate. There can wide particles appear bulky whereas Nanoparticles always look range of substrates depending upon the coating material. The clear. The Process involves the evolution of networks through substrate is heated and cleaned thoroughly before clamping in the formation of colloidal suspension abbreviated as “sol” and deposition chamber. The pressure and temperature are then gelatin to form a network in continuous liquid phase adjusted depending upon coating material and substrate. The abbreviated as “gel”. Thus called Sol-gel formation. It occurs process usually takes place between 150 to 500 Deg C. in four stages. These processes can be applied to various kinds of Hydrolysis ceramic, polymers, alloys and composites etc. Condensation Growth of particles Agglomeration of particles D. Thermal Spray Thermal spray coating is usually used in industries. In This method the coating material is heated and melted into tiny droplets which are sprayed on coating surface with high velocity. The coating material is fed usually in powder or wire form. Thermal sprayed coatings can be applied to metal substrates, and some plastic substrates. Thermal sprayed coatings instantly enhance and improve the performance of the component. This process is known by many names including Plasma Spray, HVOF, Arc Spray, Flame Spray, and Metalizing. The coating material in the process can be tungsten carbides, stainless steels ceramics, (chrome oxide, aluminum B. Chemical Vapour Deposition and Chemical Vapour oxide, zirconia, titanium) nickel- chrome carbides, pure metals Condensation: (aluminum, zinc, copper). [16] In CVD process, the vaporized precursor is absorbed on a substance which is maintained at a high temperature. The Electric wire arc thermal spraying works on the same adsorbed molecules react with other molecules or get principles as wire arc welding. The coating material which is in decompose to produce crystals. There are three main steps in wire form is electrically charged to create an arc. Then the CVD process. molten droplets of metal wire are sprayed onto the substrate using high velocity air stream. Reactants are transported on growth surface by a boundary layer. Arc spray coatings are cheap and applied on metals like Chemical reactions take place on growth surface. pure aluminum, zinc, copper, and metal alloys such as stainless By products formed by the gas-phase reaction have to be steel. Arc spray also allows adjusting the coating texture from removed from the surface. 200 micro inches to 800 micro inches. [16] The plasma spray process uses inert gases which are fed past an electrode in the CVC technique involves pyrolysis of vapor form of "plasma" state. When these gases exit the nozzle of the gun metal organic precursors in a reduced pressure environment. A they return to their normal state, releasing huge amount of heat. metal organic precursor is introduced in the hot zone of the A powdered coating material is injected into the plasma reactor. The reactor allows synthesis of nanoparticles of two "flame" and injected on the substrate. phases or doped nanoparticles by supplying two precursors at the front end of reactor and coated nanoparticles by supplying a Ceramic Coatings are applied using plasma spray because second precursor in a second stage of reactor. of their high melting temperatures. (Often above 3500 F). Several types of ceramic coatings can be applied using plasma spray. [16] C. Sol-gel Technique Other than the techniques mentioned above, the sol-gel processing technique is also extensively used. Colloidal particles are much larger than normal molecules or nanoparticles. Although, upon mixing with liquid colloid IJISRT18MY53 www.ijisrt.com 256 Volume 3, Issue 5, May – 2018 International Journal of Innovative Science and Research Technology ISSN No:-2456-2165 topology of plated sample. By stirring we can increase the transfer/diffusion rate of metal ions from bulk solution to the electrode surface. [15] F. Electro Spark Deposition Electro spark Deposition (ESD) is a micro-bonding process that has the capacity of depositing wear and corrosion resistance coating to repair, improve and extend the service life of the component and tools. During the process, short duration of electrical pulses ranging from a few microseconds to milliseconds
Details
-
File Typepdf
-
Upload Time-
-
Content LanguagesEnglish
-
Upload UserAnonymous/Not logged-in
-
File Pages5 Page
-
File Size-