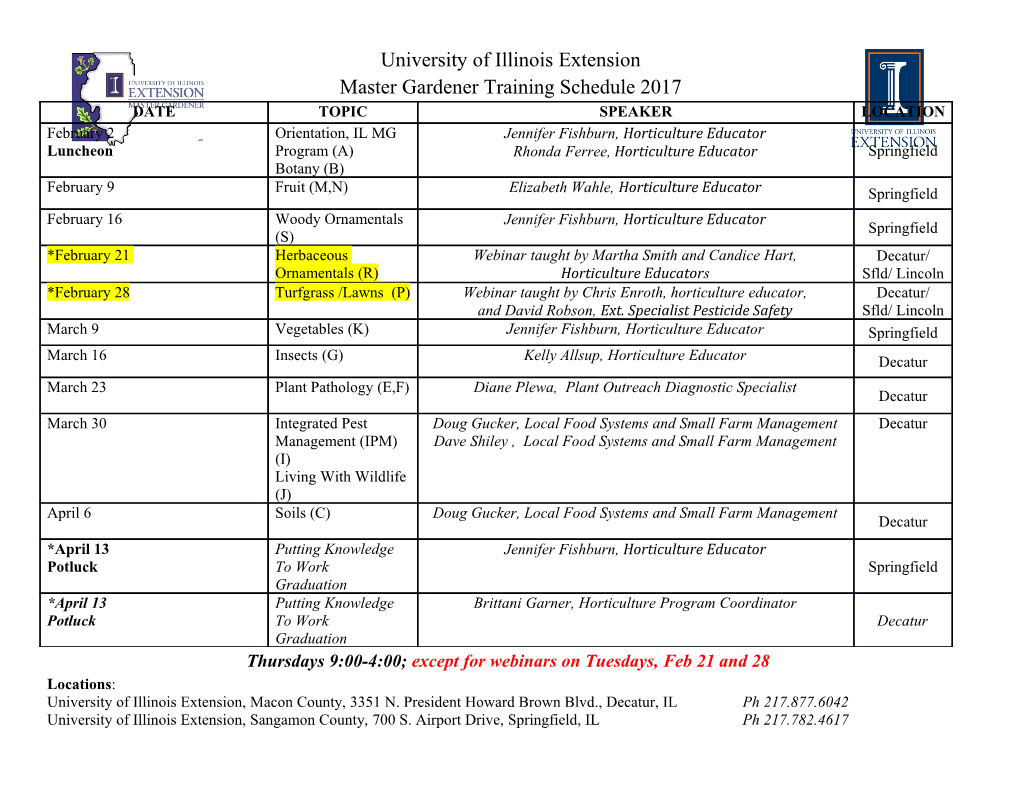
Electric Motor “Bootcamp” for NVH Engineers HBM PRODUCT PHYSICS CONFERENCE 2020, DAY 1 Ed Green, Ph.D. HBK Sound and Vibration Engineering Services Ed Green, Ph.D. • Ph.D. Purdue University - Ray W. Herrick Laboratories (1995) • Noise and Vibration Engineer in the Detroit area for the last 26 years • Principal Staff Engineer at HBK Sound and Vibration Engineering Services for last 9 years • Three years as High-Voltage Product Engineer 2 Electric Motor “Bootcamp” NVH Engineers - Background • With the transition from ICE to electric motor propulsion, NVH engineers need to learn the basics of electric motor technology • According to BloombergNEF, “By 2040, over half of new passenger vehicles sold will be electric.” (https://about.bnef.com/electric-vehicle- outlook/) This Photo by Unknown Author is licensed under CC BY-SA-NC 3 Electric Motor “Bootcamp” NVH Engineers - Outline • Physics of electric machines • Difference between Synchronous, Induction, and Reluctance motors • Control circuitry and algorithms used to power electric motors • Trade-offs of different types of traction motors and their impacts on N&V • Value of measuring current, voltage, and torque ripple along with mic and accel measurements 4 Physics The physics of most traction motors is the same = Maximize force (torque) by increasing flux density and current First Finger – Field Middle Finger – Current Thumb - Motion Fleming’s Left Hand Rule 5 Magnetic circuit Shown is the magnetic circuit for a permanent magnet motor The rotor is a magnet, and the stator is a magnetic material (iron/steel) Magnet flux lines go from the north poles to the south poles Want gap between rotor and stator to be as small as possible 6 Synchronous motor Permanent magnet synchronous motor (PMSM) is shown Conductors are in slots in the stator Force is exerted on conductors as shown earlier, but equal and opposite force is also exerted on the rotor to produce torque Alternating current is applied to the conductors (usually with multiple phases) to produce torque To produce torque, the conductors must be energized at the same rate as the rotor spins - synchronous GM Stator and Rotor 7 Induction motor Induction motor (IM) is shown Current from the stator coils induces current in the cage (rotor conductors) which produces a magnetic field in the rotor – like a transformer! Different from PMSM because rotor turns more slowly than the current stator coils are energized – slip Slip is the percent difference between rotor speed and energizing speed Invented by Nikola Tesla in 1887 Unlike a synchronous motor, the rotor speed must be slower than the excitation of the stator. Higher slip produces more current demand and more torque 8 Reluctance motor Physics of a reluctance motor is different than IM and PMSM A bar of magnetic material (laminated steel/iron) wants to align with the magnetic flux lines – like iron filings Hybrid Reluctance/PMSM have been used to increase the efficiency of latest Tesla and other vehicles Note that the polarity of magnetic excitation is not important to the direction of rotation 9 Synchronous motor/induction motor tradeoffs Induction Motor Synchronous Motor Switched Reluctance Motor Cost Low Higher Low Starting Torque Low Better Poor Low Speed Torque Better Good Good Power Density Good Better Good Efficiency Very Good Better Very Good Torque Degradation None Slight over Time None Control Easy Not as Easy Not as Easy Longevity/Durability Excellent Excellent Excellent NVH Good Better Fair Induction Motor Synchronous Motor Switched Reluctance Motor Used as Hybrid SM/SR for GM EV-1 Tesla Model 3 2WD newer Teslas Tesla Roadster Tesla Model 3 4WD (rear) Tesla Model S Tesla Model Y 4WD (rear) Tesla Model X Nissan Leaf Tesla Model 3 4WD (front) Chevrolet Volt Tesla Model Y 4WD (front) Chevrolet Bolt AC Propulsion Toyota Prius Mahindra e2o Rivian Audi e-Tron Hyundai Kona Electric Ford Focus EV 10 Porsche Mission E Jaguar i-Pace Motor inverter/controller Electric vehicle batteries are DC devices, and traction motors are AC devices A high-current, high-voltage inverter is necessary to convert the DC battery voltage into AC motor supply voltage It would be ideal for the inverter to produce a sine wave output, but solid-state-transistor devices in the inverter prefer to be in an “on” or “off” state to manage heat generation - transistors want to produce square waves! Two strategies to produce approx. sine wave current are pulse width modulation (PWM) and multi-level step 11 Inverter voltage influence on mechanical torque Torque has frequency component Voltage – • AC excitation Current – Pulse Width Modulation Multi-Level Step Torque – • Slotting effects Control type effects torque • PWM excitation on the left • 6 step excitation on the right These effects will result in N&V at the machine and down stream Voltage, current, and torque for a control change in a 3 phase machine highlighting the dependence of torque on excitation 12 Slide from “eDrive NVH HBM eDrive Testing” webinar, Oct 2019, Mitch Marks Pulse width modulation Diagram shows PWM voltage and resulting current in a coil Voltage ‘duty cycle’ is varied to modulate current waveform (pseudo- sine-wave) Wider pulses for higher current 1 = − � PWM Circuitry with IGBT Transistors 13 Multi-level step Plot shows multi-level step control Control can switch from PWM at low load to multi-level at high load V Time Multi-Level Circuitry with IGBT Transistors 14 Mitch Marks slide Noise and vibration – basic mechanisms Consider the simple synchronous motor. The rotor is a powerful magnet, the stator is iron, and they are separated by as small of a gap as possible Thus, huge radial forces (Maxwell forces) are exerted on the stator, and these forces move as the rotor moves In general, these radial forces are much larger than the tangential forces that produce motor torque and increase as load increases The fundamental excitation frequency is: p is number of poles ( ) = 60 N is the rpm 15 Noise and vibration – basic mechanisms – cont. In addition there are harmonics and subharmonics that arise from normal operation and also quality issues Induction motors have induced poles which move at the speed of rotor, but there are also alternating forces at the frequency that is applied to the motor – two sets of frequencies 16 Noise and vibration – basic mechanisms – cont. The stator is approximately a cylindrical shell that has natural frequencies Breathing Mode These are excited by the radial forces Degree of excitation depends on participation factor (spatial and temporal matching of force and mode First Cylindrical Bending Mode shape) Generally requires software (such as EOMYS Manatee) to determine the level of excitation Second Cylindrical Bending Mode Best designs preferentially excite higher modes, have more poles, have many slots, and are multi-phase Skewing and pole shaping to smooth excitation from on to off – analogous to Third Cylindrical Bending Mode, etc. using helical gears rather than spur gears 17 Noise and vibration – basic mechanisms – cont. Our engineering partner, EOMYS, provides an in-depth webinar series on NVH https://eomys.com/e-nvh/webinaires/?lang=en EOMYS Manatee Software can be used to evaluate: • Current amplitude unbalance • Demagnetization • Stator ovality • Pole misplacement • Parallel static eccentricity • Parallel dynamic eccentricity M.S. Islam, R. Islam, and T. Sebastian, “Noise and Vibration Characteristics of Permanent- Magnetic Synchronous Motors Using Electromagnetic and Structural Analysis”, IEE Transactions on Industry Applications, Vol. 50, No. 5, Sept./Oct. 2014 is a very good reference on basic noise mechanisms 18 Noise and vibration – basic mechanisms – cont. The PWM also produces high frequency noise which can be efficiently radiated by the stator or invertor housing Simultaneous acquisition of N&V signals and high voltage motor excitation signals is useful to understanding response HBM Genesis system has capability • High frequency • High voltage • High current • CCLD (ICP) inputs for accels and mics 19 Noise and vibration – basic mechanisms – cont. Torque ripple also produces N&V input Voltage – Current – to the vehicle through the mounts and Pulse Width Modulation Multi-Level Step suspension Torque – Influenced by motor design and control strategy Important to note that actual control does not always match intention Voltage, current, and torque for a control change in a 3 phase machine highlighting the dependence of torque on excitation 20 Mitch Marks slide Electric powertrain and NVH testing Time domain and FFT display in Perception DuT Voltage ALL Current synchronously and Post process analysis in continuously AND BKconnect Acceleration recorded with eDrive 21 P U B L I C Summary Traction motors are IM, PMSM, and new PMSM/SRM hybrids Many tradeoffs between IM, PMSM, and SRM! Controllers do not produce sine-wave excitation - PWM and multi-level step are common control strategies Control produces dynamic torque fluctuations and high-frequency noise and vibration EM forces produce strong radial forces that excite the stator at a frequency of the number of poles times the motor speed 22 Thank You Ford Mach-E en.wikipedia.org www.hbkworld.com | © HBK – Hottinger, Brüel & Kjær | All rights reserved P U B L I C.
Details
-
File Typepdf
-
Upload Time-
-
Content LanguagesEnglish
-
Upload UserAnonymous/Not logged-in
-
File Pages23 Page
-
File Size-