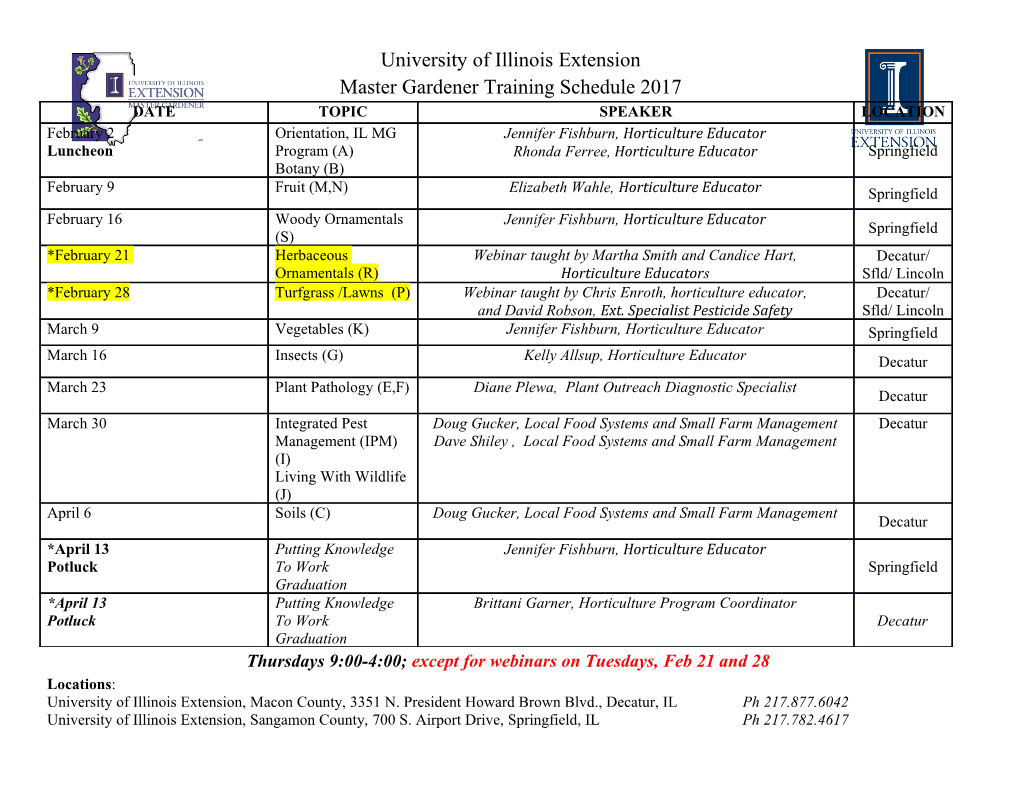
Statistical Process Control Lab by Jenna Hartmann Submitted to Dr. C. G. Willson ChE 253M Department of Chemical Engineering The University of Texas at Austin Fall 2007 Statistical Process Control Abstract 2 Contents Introduction 4 Methods 4 Results 6 Conclusions and Recommendations 15 Appendices Appendix A 17 Appendix B 19 Appendix C 21 References 22 List of Tables Table 1: Process Capability Index Values 14 List of Figures Figure 1: Process Flow Diagram 4 Figure 2: Pure Dye Pre-Mixer X-bar Chart, Estimation Method 6 Figure 3: Pure Dye Pre-Mixer R Chart 7 Figure 4: Pure Dye Post-Mixer X-bar Chart, Estimation Method 7 Figure 5: Pure Dye Post-Mixer R Chart 8 Figure 6: Mix Stream Pre-Mixer X-bar Chart, Estimation Method 9 Figure 7: Mix Stream Pre-Mixer R Chart 9 Figure 8: Pre-Mixer Distribution Histogram 10 Figure 9: Mix Stream Pre-Mixer X-bar Chart, Standard 11 Deviation Method Figure 10: Mix Stream Post-Mixer X-bar Chart, Estimation Method 12 Figure 11: Mix Stream Post-Mixer R Chart 12 Figure 12: Post-Mixer Distribution Histogram 13 Figure 13: Modified (plotted without outliers) Post-Mixer Histogram 13 Figure 14: Mix Stream Post-Mixer X-bar Chart, Standard 14 Deviation Method Figure 15: Pre- and Post-Mixer Raw Concentration Data 15 3 Statistical Process Control Introduction The purpose of this lab was to determine whether a continuous mixing process was “in control” by analyzing control charts and quantifying the benefits of an in-line mixer in the process. Statistical process control is a frequently used analytical tool for quality improvement programs. In this lab, the quality of the product stream (green dye and water solution) was analyzed using control charts (X-bar for the operating process level and R for variability) which were created by (1) an estimation method in JMP and (2) a standard deviation method. The resulting control charts were then compared to make quality control suggestions for the operating system. Methods The experimental apparatus for the Statistical Process Control lab is shown below in Figure 1. The apparatus consists of a large 20L container that holds the 0.2 wt% dye solution. Connected to this container is the recycle pump that mixes the solution to a uniform concentration. A peristaltic pump is also connected to the outlet of the container. This pump generates the continuous flow rate of dye solution to the rest of the apparatus. The water used for the dye and water mixture enters from the top left of the apparatus (as shown in Fig 1) at a junction before entering the first spectrometer. The mixed solution travels past the pre-mixer spectrometer before entering the in-line mixer. After the mixer, there is a second (post-mixer) spectrometer. The mixed solution then enters into a large graduated cylinder before exiting the system to the drain (Mullet, 2007). Figure 1: Process Flow Diagram The two detectors in this lab are spectrophotometers, or spectrometers for short, but they have slightly different path lengths (the length that the detecting light passes through the fluid). The first spectrometer has a path length of 0.56 cm, and the second spectrometer has a path length of 0.54 cm. Each of the two detectors uses the same tungsten halogen lamp as a light 4 source. The light is directed from the lamp to the detectors by means of a fiber optic cable. Once the light reaches the spectrometer, it enters the flow cell and is emitted through the flowing fluid to a detector on the other side. The spectrometer measures the intensity of light passing through the fluid. The negative logarithm of the ratio of the intensity of the light that exits the flow cell versus the intensity of light of some reference is the absorbance (shown as Equation 1). I A = − log (1) I O As the weight percent of the solution changes, the absorbance changes. A larger weight percent of dye means a larger absorbent peak due to the presence of more dye, and hence the less light that is able to pass through it. The absorbance is only a function of the amount of dye in the solution because it was “zeroed out” by taking measurements with a stream of pure water. The measurements taken with the pure water stream are then used as the reference intensity for absorbance calculations. The relationship between the amount of absorbance and the concentration is known as Beer’s Law, shown in Equation 2 below: A = εcl (2) where c is the concentration, l is the path length of the flow cell, A is the absorbance, and ε is the extinction coefficient. Beer’s Law shows that a larger concentration is directly proportional to a larger absorbance (Mullet, 2007). Before the dye solution could be mixed with the tap water, a calibration curve needed to be created using a series of settings for the rotameter. The rotameter flow rate was measured at settings of 26%, 36%, and 51% of the maximum flow rate. The flow rate of the peristaltic pump was also measured by use of a bucket and stopwatch method. Dye solution was sent through the system without mixing with tap water, and the absorbance was taken before and after the in-line mixer. Then, dye solution and tap water were mixed, and the absorbance was measured before and after the in-line mixer. All the intensity data collected by the computer were then used to calculate the absorbance, and hence concentration, by Beer’s Law. Finally, control charts were created using the estimation and standard deviation methods. Random fluctuations in a process are always present, so processes are studied to determine if non-random variations exist. Non-random variations mean that the process can be modified to obtain statistically better data because the problems are from “assignable causes.” Control charts are an excellent way to interpret the data to determine what types of fluctuations are present. When looking at a control chart, the process is said to be “in control” if the data is varying only by random fluctuations. The term “in control” only corresponds to the statistical data, not the specifications needed on the product. A system is said to be out of control when there are both random and non-random variations. The capability index incorporates specified quality limits and predicts the product quality that can be expected from a process (Mullet, 2007). 5 Results The experimental results confirmed that the in-line mixer provided benefits for the process, but not enough to be considered for further use (e.g. in a factory). The mixed stream’s pre-mixer concentration data followed a random but non-normal distribution, and the post-mixer data followed a normal but non-random distribution. For a system to truly be in control, the data must be both normal and random (Mullet, 2007). Since neither the pre- nor post-mixer data met both of these requirements, the system was determined to be out of control. The mixer reduced the variability of the process (R bar = 0.017 pre-mixer and R bar = 0.00069 post-mixer), but the post-mixer x-bar chart shows trends in the data and an out of control system. The mixer proved capable of producing a ± 0.002% product in the pure dye stream (Cp pre-mixer = 2.28 and Cp post-mixer = 1.82) but not in the mix stream (water and dye) experimental runs (Cp = 0.092 and 1.13 pre- and post-mixer, respectively). First, the experimenters calibrated the spectrometer by taking a dark reference measurement using a stream of pure dye. Figures 2 and 3 display the pre-mixer X-bar and R charts for the pure dye stream. Figure 2 exhibits the non-random behavior of the system prior to entering the mixer. The control chart shows that the dye concentration varies around the lower control limit at first, then follows an upward trend, and finally maintains steady fluctuations around the upper control limit. This trend may have resulted because the experimenters did not allow the process to reach steady state before taking data readings. Figure 3 shows that the concentration of the dye before the mixer maintained a wide range of variability. The process did not vary to a state of being out of control, but the R chart shows that the pre-mixer conditions result in a wide range of resultant product, in this case, a wide range of dye concentration. 0.1705 0.1703 0.1701 UCL=0.170113 0.1699 Avg=0.16987 0.1697 LCL=0.169627 0.1695 0.1693 DYE Pre-MixerDYE Concentration (wt%) 16 32 48 64 80 96 112 Sample Figure 2: Pure Dye Pre-Mixer X-bar Chart, Estimation Method 6 0.0011 0.0009 UCL=0.000889 0.0007 0.0005 Avg=0.000421 0.0003 0.0001 LCL=0 -0.0001 DYE Pre-MixerDYE Concentration (wt%) 16 32 48 64 80 96 112 Sample Figure 3: Pure Dye Pre-Mixer R Chart Figures 4 and 5 present the control charts for the post-mixer results of the pure dye stream. Again, Figure 4 shows the same upward trend in the X-bar chart as in the pre-mixer X- bar chart but to a lesser degree. In the case of the post-mixer, the process appears to operate under more control, with the exception of one outlying point. However, although the post-mixer results show the benefits of the mixer, the concentration still varies over a wide range of values, as shown by the R chart in Figure 5.
Details
-
File Typepdf
-
Upload Time-
-
Content LanguagesEnglish
-
Upload UserAnonymous/Not logged-in
-
File Pages22 Page
-
File Size-