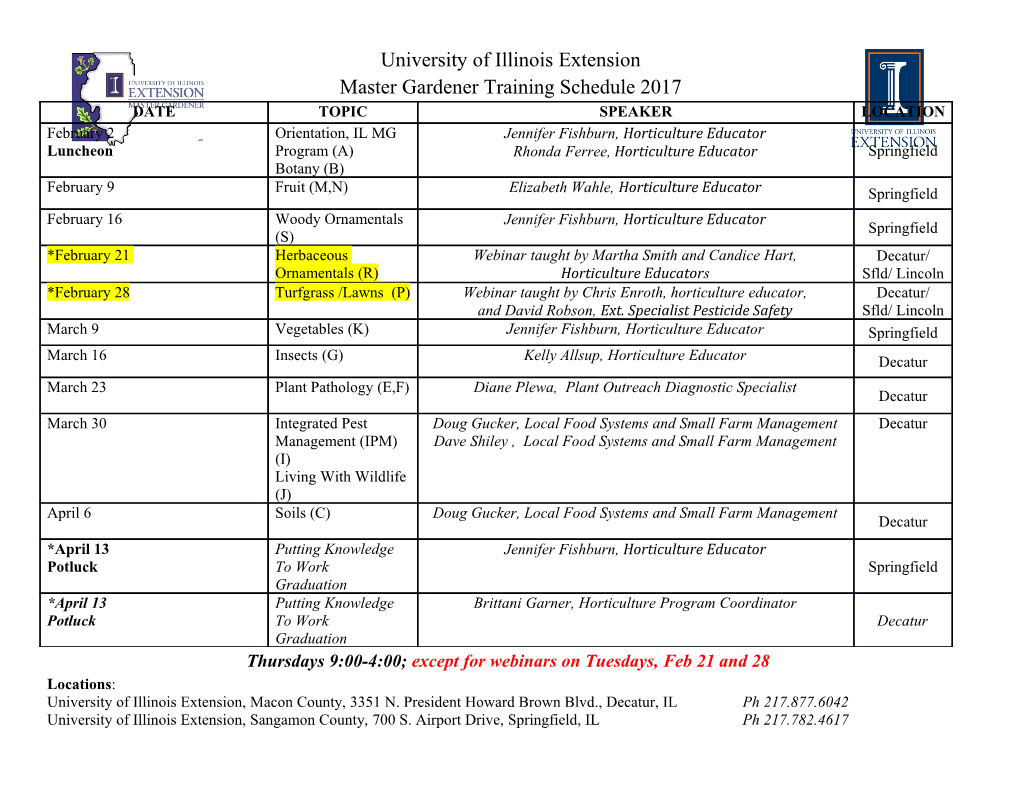
CHAPTER Inspecting and Servicing the Cylinder Block Assembly 8 Upon completion and review of this chapter, you should be able to: ❒ Perform a complete visual inspection of the ❒ Inspect piston pins and determine cylinder block and determine needed condition. repairs. ❒ Perform a complete inspection of the ❒ Properly measure the cylinder block for connecting rods, including big-end bore, bore warpage, deck warpage, and cylinder small-end bore, bends, and twists. bore wear. ❒ Recondition cylinder bores. ❒ Inspect main and rod bearings and perform ❒ Recondition connecting rods, including accurate failure analysis. replacing rod bolts, straightening, resizing ❒ Perform a thorough visual inspection of the the big-end bore, replacing pin bushings, crankshaft and determine needed repairs. and beaming. ❒ Accurately measure crankshaft warpage. ❒ Correctly install press-fit and full floating ❒ Measure the journals, seal diameters, piston pins. flange, and vibration dampener mating ❒ Properly install piston rings, including surface of the crankshaft for wear and measuring and correcting end gap, determine needed repairs. clearance checking, and proper staggering ❒ Visually inspect and measure pistons and of end gaps. determine needed repairs. With the engine block disassembled, it should be thoroughly cleaned and inspected. Before Basic Tools cleaning the block, remove the core and gallery plugs. After the block is cleaned, coat it with a Basic mechanic’s tool water-repellant solution. This is important in the cylinder and journal bores to prevent the for- set mation of surface rust. This chapter discusses the process of inspecting the block casting, main bearing bores, Service manual camshaft bores, cylinder bores, piston assemblies, and crankshaft. Keep a record of the needed parts and machining procedures required before reassembling the engine. Also, this chapter cov- ers the procedures for reconditioning the components of the cylinder block assembly. Inspecting the Cylinder Block Begin block inspection by first giving it a thorough visual inspection. Inspect the bores and jour- Classroom Manual nals for wear patterns and the entire casting for cracks. Also, use this time to clean and inspect all Chapter 8, page 177 oil passages. Some of these passages can be quite small and easily plugged (Figure 8-1). Use a small bore brush or a piece of wire to clean all oil passages. If the block passes visual inspection, it must be checked for deck warpage, cylinder wall Special Tools wear, crankshaft saddle alignment, camshaft bore wear, and lifter bore wear. Precision straightedge Feeler gauges Checking for Deck Warpage Visually inspect the deck for scoring, corrosion, cracks, and nicks. If a scratch in the deck is deep The deck is the top enough to catch your fingernail as you run it across the surface, the deck needs to be resurfaced. of the engine block Measure deck warpage using a precision straightedge and feeler gauge. To obtain correct where the cylinder results, the deck must be completely clean. Check for warpage across the four edges and across head is attached. 355 Surfaces to be measured Figure 8-1 Make sure all oil passages are thoroughly Figure 8-2 Measure the deck in several directions to cleaned. determine the amount of warpage. (Courtesy of Amer- ican Honda Motor Co., Inc.) the center in three directions (Figure 8-2). The amount of warpage is determined by the thickest feeler gauge that will fit between the deck and the straightedge (Figure 8-3). Compare the results with specifications. The deck can be resurfaced if the cylinder block dimensions will still be within specifications after machining (Figure 8-4). Even if the deck is within specifications, it is a good practice to put a new surface finish on the deck so the gasket will seal properly. This can be done by using a light cut on the milling machine or using a special disc to clean the deck. Precision straightedge Deck height Block Crankshaft centerline Figure 8-3 Measuring deck warpage. (Courtesy of Figure 8-4 The deck may be resurfaced if the overall American Honda Motor Co., Inc.) block height will still be within specifications. 356 If the deck is warped, it is important to determine how much material the manufacturer will allow to be removed. If more material will have to be removed than the manufacturer allows, the block will have to be replaced or a thicker head gasket will have to be used (if available). Removing more material than allowed may result in piston-to-valve contact. In addition, removing stock from the deck surfaces may affect intake manifold bolt alignment. V-type engines require both decks to be machined the same amount to keep the compression ratio equal on both sides. Inspecting and Measuring Cylinder Wall Wear Special Tools After visually inspecting the cylinder bores, use a dial bore gauge, an inside micrometer, or a tele- Dial bore gauge scoping gauge to measure the bore diameter. First, check to see if the cylinders have been bored Micrometer to an oversize on a previous rebuild. Oversize pistons usually have a stamped number on the Telescoping gauge piston head to indicate the size. If the piston has no numbers, bore oversize can be checked by measuring the cylinder diameter near the bottom of the bore. Since this is a nonwear area, if the bore is larger than original specifications, the cylinder has been oversized. This information is important when ordering new pistons and rings. Common piston oversizes are 0.020, 0.030, 0.040, and 0.060 inch. Metric oversizes are in 0.50 mm increments. Piston movement in the cylinder bore produces uneven wear throughout the cylinder. The cylinder wears the most at 90 degrees to the piston pin and in the area of upper ring contact at top dead center (TDC). This is because the top of the cylinder receives less lubrication while being subjected to the greatest amount of pressure. Wear decreases toward the bottom of the cylinder, resulting in taper. Taper in the cylinder bore causes the piston ring gaps to change as the piston travels in the Taper is the bore. Out-of-round wear is caused by the thrust forces exerted by the piston. Another cause of difference in out-of-round wear is gasoline washing away the oil film from the cylinder walls during cold diameter at different engine operation or other high-fuel conditions. locations in a bore or Normally, the most cylinder wear occurs at the top of the ring travel area. Pressure on the on a journal. top ring is at a peak and lubrication at a minimum when the piston is at the top of its stroke. A ridge of unworn material will remain above the upper limit of ring travel. Below the ring travel area, wear is negligible because only the piston skirt contacts the cylinder wall. A properly reconditioned cylinder must have the correct diameter, have no taper or out-of- roundness, and the surface finish must be such that the piston rings will seat to form a seal that will control oil and minimize blowby. Taper is the difference in diameter between the bottom of the cylinder bore and the top of the bore just below the ridge (Figure 8-5). Subtracting the smaller diameter from the larger one Cylinder bore taper A C Cylinder walls Figure 8-5 To check for taper, measure the cylinder diameter at A and C. The difference between the two readings is the amount of taper. 357 gives the cylinder taper. Some taper is permissible, but normally not more than 0.006 in. (0.1524 mm). If the taper is less than that, reboring the cylinder is not necessary. Cylinder out-of-roundness is the difference between the cylinder’s diameter when mea- Out-of-roundness sured parallel with the crank and then perpendicular to the crank (Figure 8-6). Out-of-roundness is the difference is measured at the top of the cylinder just below the ridge. Typically, the maximum allowable between the out-of-roundness is 0.0015 in. (0.0381 mm). Normally, a cylinder bore is checked for out-of- cylinder’s diameter roundness with a dial bore gauge (Figure 8-7); however, a telescoping gauge can also be used. when measured parallel with the CAUTION: If the cylinder is bored to accept an oversize piston, oversize rings crank and then I are required. perpendicular to the crank. SERVICE TIP: A simple method to check taper without any special measuring tools is to use a feeler gauge and an old piston ring. Square the ring just below the ring ridge, and measure the ring butt gap with a feeler gauge. Compare this measurement to the gap measurement at the bottom of the bore. The amount of taper is the difference between the two readings divided by three. Special Tools Checking Main Bearing Bore Alignment Precision straightedge Over the life of the engine, the main bearing bores can become misaligned (Figure 8-8). The Arbor main bearings will usually compensate for this by wearing unevenly; however, if new main bear- ings are installed into an engine with the bores misaligned, the crankshaft will have increased resistance to turning. If excessive misalignment is not corrected, the new main bearings will fail prematurely. Upon inspection of the old main bearings, it may be possible to determine if the bores are misaligned. A warped crankcase will result in bearing wear on one side of the insert. Cylinder block Cylinder bore Figure 8-6 To check for cylinder out-of-roundness, Figure 8-7 The easiest way to measure cylinder bores measure the bore in different locations. is with a dial bore gauge. (Courtesy of L. S. Starrett Co.) 358 Centerline of warped crankcase True centerline of crankcase Figure 8-8 The crankcase can warp, causing saddle misalignment.
Details
-
File Typepdf
-
Upload Time-
-
Content LanguagesEnglish
-
Upload UserAnonymous/Not logged-in
-
File Pages58 Page
-
File Size-