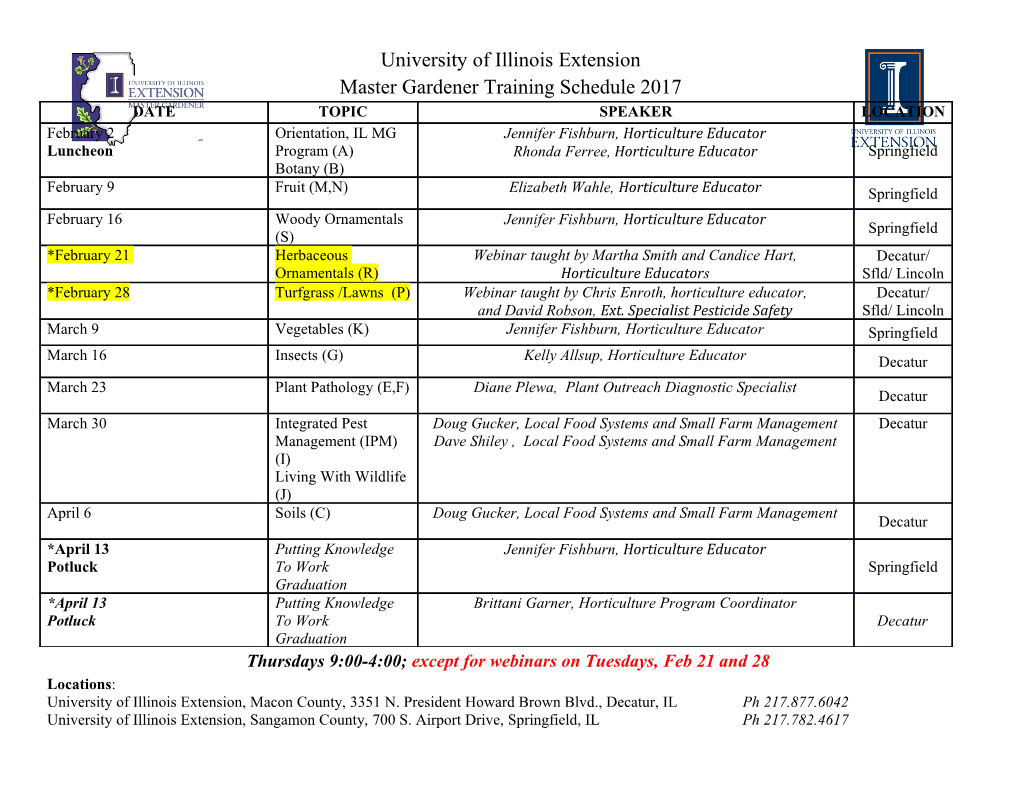
COMMUNICATION, CONFIGURATION, APPLICATION The Three Layer Concept for Plug-and-Produce Uwe E. Zimmermann, Rainer Bischoff KUKA Roboter Gmbh, Zugspitzstraße 140, 86165 Augsburg, Germany Gerhard Grunwald, Georg Plank, Detlef Reintsema German Aerospace Center (DLR), Institute of Robotics and Mechatronics, Oberpfaffenhofen, 88234 Wessling, Germany Keywords: Plug&Play, robotics, reduced set-up time, determinism, real-time communication, device description. Abstract: The Plug-And-Play is a synonym for the simple use of computer systems in office applications. This appealing idea also emerges in the branches of robotics and automation. But due to their specific technical and application driven requirements i.e. real-time, determinism, safety… a simple taking over of the technology is not sufficient. Plug-and-Produce extends the “easy to use” for applications in robotics and automation. This will lead to a dramatically reduction of set-up times of work-cells. In order to fulfil the various requirements a three layered Plug-and-Produce architecture is presented. The communication layer addresses all topics regarding the bus-system level; the configuration layer is responsible for the control and operation system level; and the application layer addresses the needs of the user and system programmer. A prototypical implementation is also presented. 1 INTRODUCTION EU funded project SMErobot™ (SMErobot, 2005) created the term „Plug and Produce“(PnProduce) to Technically, the integration of components i.e. a express these peculiarities and to delimit from the memory stick, a camera, or a disk drive into a office applications. computer system is a very complex task. Different The potential of PnProduce is very obviously: kind of knowledge is required. This includes The set-up time of robot cells is time-consuming and hardware, communication systems, operating thus an important cost factor. It take days or even systems, programming and application interfaces. weeks just to get all peripheral systems Practically, the user wishes the simple addition of communicating and working with each other, even his new device without requiring reconfiguration or though the system was planed and designed very manual installation of device drivers. “Plug-And- detailed in advance. Costs could be dramatically Play“(PnP) is the synonym for this wish. In the early reduced, if it is possible to reduce the installation 1980s the NuBus (NuBus, 1983) which was time. Especially future robotics systems will require originally developed by MIT and used by Apple much more flexibility due to frequent task and Macintosh and Texas Instruments was one of the equipment changes. It should be possible to connect earliest PnP-busses. Today the Universal Serial Bus a new, even a priori unknown device to the robot (USB) is the widest spread and probably best known controller and to use it immediately without the need PnP-bus (Axelson, 2005). of a long and error prone manual configuration. The Plug-And-Play technology was developed Besides the reduction of costs a further important for the simple use of computer systems in office factor is the “easy to use” feature. In future, more applications. Recently this appealing idea also and more robots will find their way into small and emerged in the branches of robotics and automation. medium enterprises, into the public and the health But due to their specific technical and application sector. Also service robots or assistants for driven requirements (details see in section 2) a entertainment and at home are emerging. These simple taking over of PnP is not possible. Hence the systems will be in common, that non-robotic experts 255 E. Zimmermann U., Bischoff R., Grunwald G., Plank G. and Reintsema D. (2008). COMMUNICATION, CONFIGURATION, APPLICATION - The Three Layer Concept for Plug-and-Produce. In Proceedings of the Fifth International Conference on Informatics in Control, Automation and Robotics, pages 255-262 DOI: 10.5220/0001504902550262 Copyright c SciTePress ICINCO 2008 - International Conference on Informatics in Control, Automation and Robotics will have to deal with such complex systems. 2.1.1 Device Exchange Adding of new tools, exchanging of faulty devices or upgrading the system has to be manageable A robot component i.e. a drive unit has to be without the need of an expert. exchanged or upgraded. The servicing staff powers By means of scenarios and use cases section 2 off the robot, exchanges the devices. In case of motivates the details of PnProduce and specifies the PnProduce the robot has only to be switched on inherent technical requirements. In section 3 we being operational again. The central control unit introduce the three layer concept of PnProduce and. automatically identifies the new device, reads the Some first implementation results are presented in actual device status information, configures it and section 4. integrates its functionality into the application. 2.1.2 (Automatic) Tool Change 2 PLUG AND PRODUCE Especially for versatile robot assistants frequent tool REQUIREMENTS changes are a common requirement. A device driven approach is just a subversion of the previous use PnProduce concepts for industrial applications case, where a new tool (e.g. driller) is plugged to the especially robotics can adapt existing PnP concepts robot and the associated tool service (e.g. “drill”) is from IT. But there are some special issues that have available for the user. to be covered and which are not solved by available In a service driven approach the user first selects solutions. By means of use cases some features of the service (e.g. “drill”) and then the tool that could PnProduce are discussed and also the specific perform the task is automatically selected by the robot system itself. This means that an automatic technical requirements. tool changer system has to be set up. 2.1.3 Start Up of a New System/Application In general an application can be characterized by the potential functionality of the connected components and devices. When powering on the functionalities of the devices are communicated with the central controller or a programmer. Bus, devices and robot controller are already configured for the immediate use. The application itself can be described by the detailed device configurations needed for running the task. This could be done manually or (semi- automatic). 2.1.4 Start Up of an Existing System/Application An application as described above may be stored in a file. When switching on the system the controller gets all status information from the devices which are connected via the real-time bus. These data can Figure 1: Scenarios for PnProduce. be compared with the stored description of the planned application. The controller can verify 2.1 Use Cases whether all devices are connected and properly configured. If not appropriate feedback to the user Figure 1 shows a generic setup of a work cell with can be given. multiple, different robots, tools, grippers, hands, sensors, and controllers. They are connected via 2.2 Deterministic and Real-time real-time bus systems i.e. EtherCAT, Sercos …. Communication Also the single components inside a robot should be connected via PnProduce. The communication in robotics and automation must guarantee some features to facilitate a proper and 256 COMMUNICATION, CONFIGURATION, APPLICATION - The Three Layer Concept for Plug-and-Produce safe operation of the system. One of the most Service Oriented Architecture (SOA) approaches. important features are real-time and determinism. As Most existing robot languages are command based there are multiple specifications on the term real- and therefore PnProduce concepts could be time, we will use in the context of PnProduce: “The integrated seamlessly. timing constraints of the system must be guaranteed Events are used for the asynchronous transfer of to be met. Guaranteeing timing behaviour requires small data sets to inform the control system or the that the communication is predictable”. The term devices on their actual status. They may also be used deterministic tightens the requirement in real-time for setting parameters of the attached devices and/or communication. It is not sufficient to guarantee the software. data within a time frame. The data have to be The parameters may be classified in static and delivered at a precise time. dynamic parameters. The latter may be set during system start-up or in case of configuration purposes. 2.3 Static and Dynamic Parameters But they cannot or should not be changed during run-time. Thus there is no need to include these parameters in the process data sets. In general, static In the past, the application programmer parameters are device specific. Dynamic parameters differentiates cyclic and acyclic communication. dynamically lead to more flexible systems. For Cyclic data are i.e. the sensor values from a force example, if a gripper with an adjustable gripping torque sensor or the nominal and real value of the force is used, the force parameter can be set once robot joints. These data types are also called (configuration data) before the application starts or “process images” (CAN, 2007), that are a complete can be changed depending on what kind of object or partial local data base. The application or the has to be gripped (process data). devices operate only on this local data, whereas the Commands and events are still called acyclic bus system is responsible to keep the distributed data even it is communicated in a cyclic manner on the consistent. The advantage is that communication and bus level. The process images as well as the data application are highly decoupled. Another important exchange between the local data bases has to be factor is the deterministic exchange of data as the configured, which is a complex task and leads to bus load is constant and could be analyzed a priori. high demands for a PnProduce system. This is especially true if the data exchange should be robot controller (master) dynamically changed.
Details
-
File Typepdf
-
Upload Time-
-
Content LanguagesEnglish
-
Upload UserAnonymous/Not logged-in
-
File Pages8 Page
-
File Size-