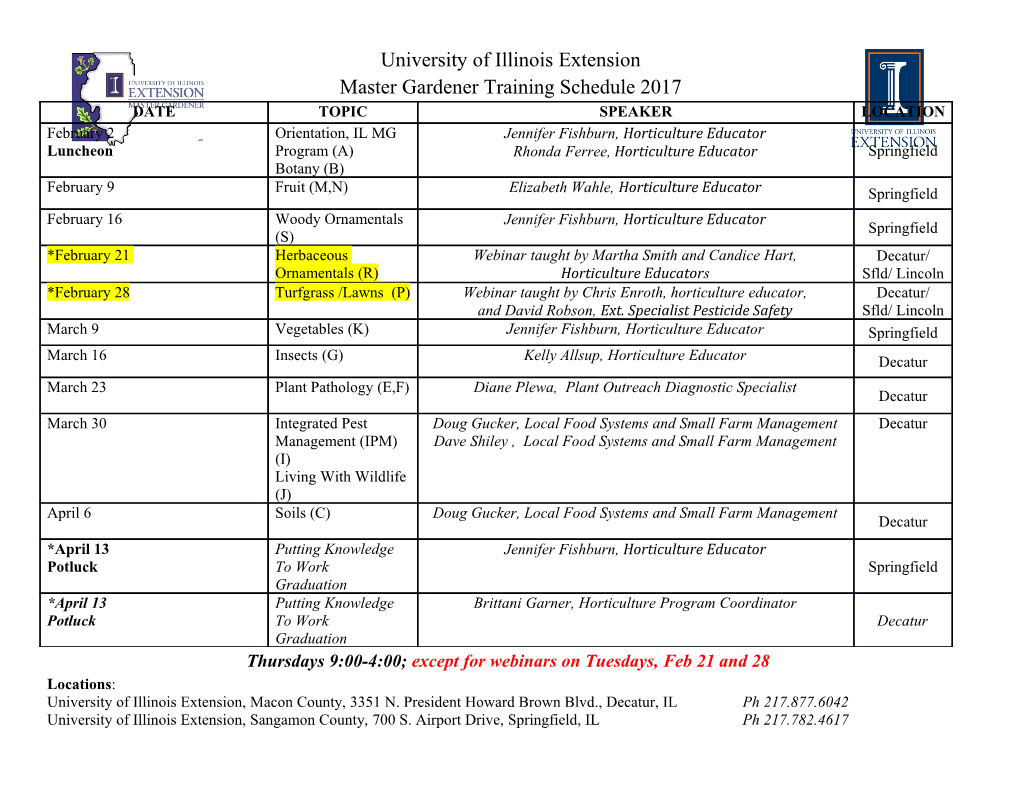
Green Process Synth 2015; 4: 307–316 Wu Zhang, Li Zhang*, Yuhai Li and Xin Li An environmental procedure to extract titanium components and metallic iron from Ti-bearing blast furnace slag DOI 10.1515/gps-2015-0031 technology for the disposal of industrial wastes has Received April 26, 2015; accepted June 29, 2015 attracted much attention. Typically, the efficient utiliza- tion of blast furnace slag is of great significance to the clean production smelting process and the global environ- Abstract: An environmental procedure to extract tita- ment; it can not only provide an outlet for the wastes but nium components and metallic iron from Ti-bearing blast can also reduce environmental pollution. furnace slag is accomplished via three steps, which are Ti-bearing blast furnace slag is a typical refractory high-temperature modification, gravity separation and industrial solid waste; it is generated during the blast hydrometallurgy method. The behaviors of metallic iron furnace smelting process of vanadium and titanium during the high-temperature modification process are magnetite. There are about 25% TiO2 and more than 5% studied. The feasibility of separating rutile from the matrix metallic iron in the slag due to the particularity of ferrous phase are investigated; based on the feasibility analysis minerals used during the melting process. A lot of slag results, the gravity separation experiment is carried out accumulates every year, polluting not only the environ- in order to improve the TiO2 content in the slag. The leach- ment but also waste resources. An environmental technol- ing behaviors and kinetics of non-titanium components in ogy to extract the titanium components and metallic iron the concentrate of gravity separation are investigated. The from the slag is necessary. Many methods are applied to activation energy of the leaching process is 62.868 kJ/mol, extract the titanium from Ti-bearing blast furnace slag, and circulatory leaching and preparation of synthetic such as acid leaching, fused salt chlorination, high-tem- rutile experiments are implemented. Finally, an environ- perature modification (HTM), preparing alloy process, etc. mental technological route is proposed for comprehensive [4–8]. However, the slag has not been utilized effectively utilization of Ti-bearing blast furnace slag. until now due to the various problems, such as water pol- lution and air pollution. Keywords: environmental procedure; iron; rutile; Based on the previous studies, the extracting Ti-bearing blast furnace slag. process in this work involves three steps: the first step is adjusting the chemical composition of the slag in order to transform the titanium component into the rutile phase; the second step is creating appropriate physi- 1 Introduction cal and chemical conditions to make the rutile crystals grown up. The above two steps could be called HTM Global concern about environmental problems is increas- process. The last step is separating the rutile and iron ing, such as solid waste pollution and air pollution. from the cooled slag by gravity separation and hydro- High-volume waste materials resulting from large-scale metallurgy method. Compared with other methods to industrial productions have long been considered to be a extract titanium from the slag, the HTM process can burden, due to the high costs of their associated post-treat- proceed without being heated during the actual indus- ment, storage and disposal [1–3]. The environment-friendly trial production process; thus, it does not require addi- tional energy. The energy that is required during the HTM process could be provided by high-temperature *Corresponding author: Li Zhang, School of Materials and slag that is discharged from the furnace. Moreover, the Metallurgy, Northeastern University, Shenyang, Liaoning 110819, experimental results of the HTM process showed that P. R. China, e-mail: [email protected] Wu Zhang, Yuhai Li and Xin Li: School of Materials Science and metallic iron would settle down to the bottom of the cru- Engineering, Shenyang Ligong University, Shenyang, Liaoning cible, and thus the metallic iron can be separated easily 110168, P. R. China after the HTM process. The rutile crystals are separated 308 W. Zhang et al.: Titanium and iron extracting from slag from the slag by gravity separation and hydrometal- therefore fully characterized by scanning severa1 areas during SEM- lurgy methods; the water used in the extracting process EDX analysis. Titanium enrichment ratio is a primary indicator for HTM pro- is recycled by circulatory process. No emission of waste cess. We use the volume fraction of rutile in the modified slag to water and pollution are expected during the production measure the titanium enrichment degree; the overall uncertainties process in this work. are ±0.3%. We convert the crystal size of rutile into equivalent cir- cle to describe the size of rutile crystals, and the overall uncertainty is ±0.7%. Line intercept method is applied to determine the average grain size and volume fraction of rutile crystals; the sample homo- geneity, magnification and numbers of measured fields are readily 2 Materials and methods sources of error during the measurement. 2.1 Materials 2.2.2 Titanium component separation process: The titanium The slag used in this work is obtained from the Panzhihua Iron and component separation process proceeds via two stages in this Steel Company, and the chemical composition is listed in Table 1. work; the first is gravity separation process, and the second As shown in Table 1, the raw slag mainly consists of TiO2, CaO, SiO2, is leaching of non-titanium components. The equipment of Al2O3 and MgO, and other oxides such as Fe2O3, which are inevitably gravity separation process is shaking table (model: 6-s, Hubei included in the slag, account for the remaining small proportion. Mining Machinery Factory, Hubei province, China), the vibration Prior to the heating experiment, the raw slag is ground and frequency and the shaking stroke are 360 per minute and 12 mm, screened by a 74-μm mesh to facilitate melting. Analytical grade respectively. oxides are mixed with the slag in order to make the titanium com- The materials used in leaching process are gravity separation ponents transform into rutile phase. All commercially available concentrates. Leaching experiments are carried out in a 1000-ml- chemical agents for experiments are without further purification. All capacity glass reactor fitted with multisockets, with the sockets being the reagents used in this work were produced by Shenyang reagents fitted with quick-fit glass adaptors and a condenser to prevent evapo- factory in Liaoning province, China. ration losses. The reactor is heated in a water bath with provision to control the bath temperature to maintain the reactor temperature within ±1 K. The leaching processes consist of two steps: (1) alkali 2.2 Experimental procedure leaching, process in which silicon and aluminum components could be removed; and (2) diluted hydrochloric acid (0.88% wt) leach- ing, process in which magnesium and iron components could be 2.2.1 High-temperature modification and samples analysis removed. process: The experiments of HTM process are carried out in a vertical furnace and the temperature controller is Shimaden FP93 (the temperature measurement accuracy is ±3 K). The working thermocouple is B type and calibrated against a standard thermocouple. 3 Results and discussion The modified slag samples are analyzed by X-ray diffraction [XRD, using a Philip X pert machine (PANalytical company, Almelo, Holland) with Cu Kα radiation]. Phases in the XRD patterns are 3.1 Phase transaction of titanium before analyzed by X pert high score plus software (PANalytical company, and after high-temperature modification Almelo, Holland) equipped with JCPDS PDF 4 database. A patch of modified slag is chipped and polished on a buffing process machine, and then metallographic microscope (201A-D, Shanghai optical instrument factory, Shanghai, China) and scanning electron Figure 1 shows the SEM images for the raw slag and microscope with the model of 201A-D and SSX-550 (Shanghai optical modified slag. As shown in Figure 1, combining with the instrument factory, Shanghai, China) are used to observe the micro- previous work [5, 7–9], there are five phases in the raw morphology of the modified slag. slag, which are perovskite, Ti-rich diopside, titanaugite, Scanning electron microscopy combined with energy-dispersive spinel and metallic iron, while there are only two phases X-ray (SEM-EDX, Shimadzu Corporation, Kyoto, Japan) analysis ena- bled the characterization of phases that are present in small con- in the modified slag; one is rutile phase, and the other centration and may not be analyzed by XRD analysis. The slags are is called matrix phase in this work. Table 2 shows the energy dispersive spectrometer (EDS) analysis results of the modified slag. Table 1: Chemical composition of raw Ti-bearing blast furnace slag As shown in Figure 1 and Table 2, most of the titanium (mass fraction, %). components in the slag are enriched in the rutile phase. Moreover, the grain size of the titanium-containing phase CaO MgO TiO2 Al2O3 SiO2 Fe2O3 Others had grown obviously, which is quite conducive to the sep- 27.07 8.04 21.36 14.13 25.20 3.4 0.8 aration process. W. Zhang et al.: Titanium and iron extracting from slag 309 AB 50 µm 50 µm Figure 1: Back scattering microscopic morphology of the modified slag: (A) before modification; and (B) after modification. Table 2: EDS results of Figure 1B. Area Element Weight % White O 34.862 Ti 65.138 Gray O 44.469 Mg 2.759 Al 8.061 Si 24.795 Ca 15.277 Ti 1.168 Fe 3.471 3.2 The behavior of metallic iron in high- temperature modification process Figure 2: Photo of modified slag and iron. During the vanadium-titanium magnetite blast furnace 2 2 r11(-ρρ2 ) smelting process, metal droplets are brought into the slag Vg=× × (1) 9 η due to high viscosity of the liquid slag; this part of metal 2 droplets is wrapped in the slag, and it is one of the most where V is the average settling velocity of iron (m/s); r1 is serious causes of metal loss [4].
Details
-
File Typepdf
-
Upload Time-
-
Content LanguagesEnglish
-
Upload UserAnonymous/Not logged-in
-
File Pages10 Page
-
File Size-