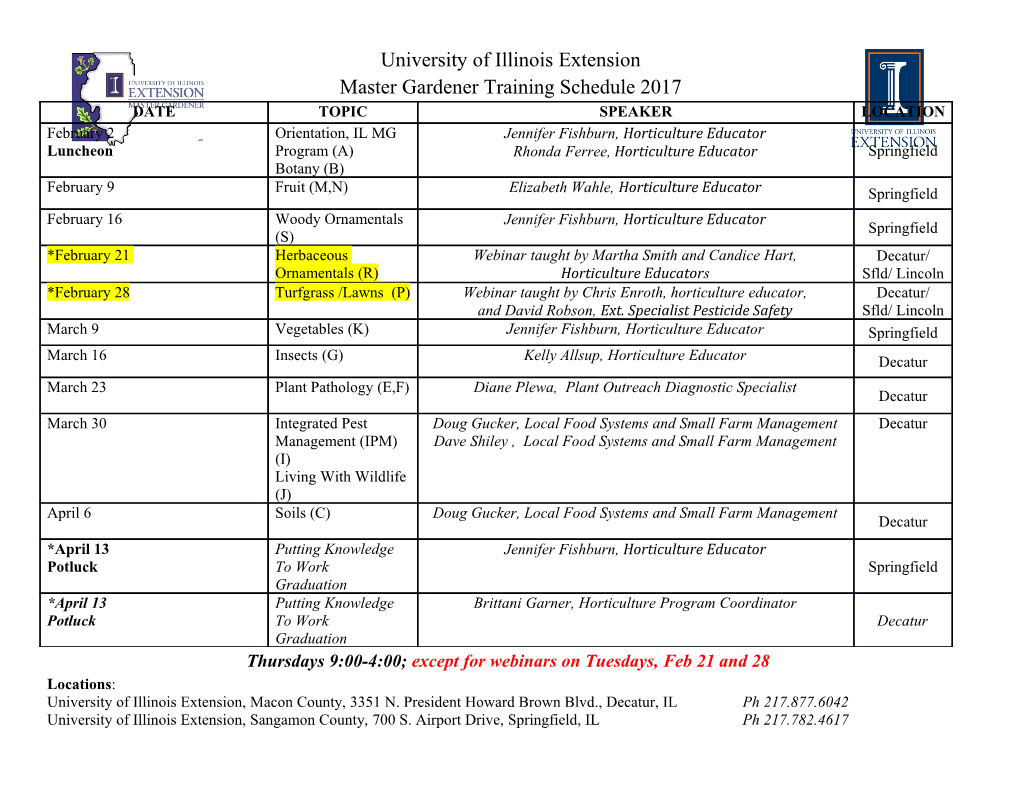
WOOD TURNING Layered Turning Manual Raymond Molinari Translated from French by Robert Mari (Nice – France 2016) 1 2 Layered Turning Manual Contents 1 Whetting your appetite 5 2 Choice and wedding of the woods. Aesthetic research 14 3 Sketch drawing of the planned piece. How to choose the kinds of layers 1 A drawing is unavoidable 17 2 Tiered sketch drawing 19 3 Truncated cone shape (“trunconic”) sketch drawing 28 4 Pyramidal sketch drawing 39 5 Mixing of several kinds of layers in the same piece 47 4 Machining the basis units, the segments 1 Equipment and common points 50 2 Circular segment with band saw or scroll saw 64 3 Trapezoidal segment with circular table saw 66 4 Trapezoidal segment with miter saw 76 5 Pyramidal segment 81 6 Specific segments and « triangulettes » 89 7 Composite segment 5 Machining rings from discs. 1 How assembly the discs in order to cut them 107 2 Cutting rings with band saw 113 3 Cutting rings on the lathe. The « Troncoline » 121 4 Cutting rings with a scroll saw 140 5 Cutting trunconic grouped merlons. Cutting mixed discs 142 6 Assembling elements and layers 1 Gluing and clamping 148 2 Ring sprung from isolated segments or from blocks sprung from discs 149 3 First lathe mounting 156 4 Full or mixed layer 161 5 The open layer. The « guillotine » 167 7 Machining of the piece and its completion 1 Inner profiling or « hollowing» 179 2 Outside profiling of the wholly assembled piece 184 3 Sanding and finishing 188 8 Examples of realizations 1 And now let’s go ! 196 2 « L’Ecossaise (Scottish) » 197 3 « Les Deux Amar » (Two « amar ») 201 4 « Riemann » 205 5 « Méandros » 211 6 « Tête Bêche » ( Head to foot ) 215 7 « Quintette » (Quintet) 219 8 « Extra » and « Intro » vases 221 9 Appendix 1 Explanations about some words and abbreviations 226 2 Bibliography. Internet 227 3 4 1. Whetting your appetite According to the dictionary, to layer means arrange in layers. You can tell, it does not get us very far. But yes, yes! We shall put together the layers (climb the stairs step by step, without getting breathless I hope). Which wood turner did not dream to make a high vase with a narrow neck? Yes, but a big piece of a pretty wood with no cracks, is uncommon. Yes, but deeply hollowing gets very hard. It’s breaking your back. You can find really clever (and expensive) accessories to succeed in that, but the purists are reluctant to use them. And the purists are numerous. Who has never craved, imagining bowls or vases, for assembling different woods, worrying about aesthetics? How can you be deprived of the pleasure to decorate a piece with gaps, while harmonizing rare (and expensive) woods? And how to spare beautiful and rare woods while making great pieces? THE SOLUTION: layered turning, you understood! From my first steps in wood turning, I hoped to make an open work piece, and I made it, inventing a method combining piling segments and positioning them thanks to a jig (which I later named « marguerite »). After a break of several years, I got a craving at the same time as I discovered out of English books (see chapter 9), wonderful items made in accordance with the technique of the layered turning, the principle of which is easy to define. It consists in piling layers of wood, gluing and turning them gradually or eventually at the end of the gluing. I came to find that the instructions in the above books were Incomplete. I felt the need to go ahead in theoretical studies, and then imagine and create techniques of machining and assembling different elements which compose an item. I am not pretending to teach you how to make beautiful layered items Through this manual, I should want simply to share with you my experiments and avoid you needless tests and make easier your work.. You may criticize my solutions, make them better, and... find other ones! We cannot test everything in a while. As for me, I followed my way successively from open working of circular segments to trunconic ones, then trapezoidal, and at last to pyramid shaped. It is your choice to go for the process that suits you the most. 5 Photos and figures are of my own, excepted the ones of Barnabé Ferré (BF), Claude Gaury (CG), François Delay (FD), Gérard Bidou (GB), Michel Havard (MH). All of them members of the Association « Autour du Bois ». I thank them heartedly. Gérard Bidou the first, for their friendly participation. Which methods do you have in regards to layered turning? The first one, rustic, not sparing with wood, consists in stacking slices, cut from a planed plank, slices drilled or not, matching or not different woods, and hollowing through or not these slices with a big bit on a column drill before sticking them, to make easier the centring when sticking, and then grinding. (Photography’s 1.1 & 1.2). I will not linger. Photo 1.1 Photo 1.2 You can see underneath the flat view of such a slice. Nothing’s simpler. 6 Fig. 1.3 The circumference can be sawed or simply hewed. The lathe will do the remnants. The central hole, hollowed with a Forstner kind bit, makes the hollowing easier and allows the centring of the layers in regard to one another. We, have the double advantage of making an item as high as we want while using simple planks? We don’t need complicated jigs. But if you want to work at the best the advantages of the layered turning method, you must stack as little wide as possible segments. Every set of segments arranged as a crown becomes a layer. We shall write « full layer » when you can see no gap. The locution “open layer” means a succession of full spaces and empty ones. At last, a “mixed layer” is a double layer with a full layer and an open one. The word “ring” is reserved to full layer. The layers can be straight or trunconic: Straight layer section Trunconic layer section (As depicted the inside and outer sawing slopes may be different) Fig. 1.4 In the same piece we can find a composition of layers of several kinds, the choice resulting from the shape of the piece (see chapter “drawing”), from the aesthetics you look for and from the machining kind. Two kinds of machining are possible to create the layers: either by assembling segments (we could have used the word “prism” instead of “segment”) cut one by one, to use a French easily adapted to English (Diagrams hereunder A and B), or either cutting discs (diagram C) The corresponding simplified flat views are the following ones: 7 A Full layers (crowns with butt-jointed segments) Trapezoidal segments Circular segments Fig. 1.5 B. Open layers (crenels and merlons) Trapezoidal segments Circular segments Fig. 1.6 About open layers, the name of the full part is « merlon », the name of the empty part is crenel, like at the top of a fortified castle... The presence of crenels allows creativity as to the shape of the merlons, the radial sides of which are possibly not straight or radial (brought into line with the center), as showed on the diagrams (see ch. 4.6 the example of such openwork item with S shaped merlons you can see from the top of it). You can make one by one straight segments, trapezoidal or circular ones (diagram A) with small planks or battens. This often happens when putting isolated full layers into an openwork item. The crown gluing then requires a great accuracy and skill. But the layers are much easier and quick to make if one cuts them in the discs as the following ones: 8 C. Discs allowing layers cuttings (straight or trunconic) C 1 Triangles made discs C 2 Small planks made discs Fig. 1.7 Please note that you can easily make isolated segments by dividing a layer from a C1 kind disc. You can easily imagine all the opportunities of the layered turning method, considering only the different machining methods and compositions of the layers, but also thanks to the wedding of wood species and open working. Yet we shall take one more step forward while combining full layers and open layers to make mixed items. In this manual, I shall not address the question of the “orange segment” or “(false) staves” assembling, despite very similar to the trapezoidal segments one. The flat sight of A kind in the figure 1.5 above is identical. The theory is the same one. But, on the other hand, the height of the layers is much higher with “orange segments”, often roughly estimated as the diameter or the height of the item. The ensuing segments cutting techniques are a little different. We work with the slant of the blade, but not with the slant of the plank regarding the blade. The thickness of the used woods also is different, more important. The « orange segments » assembling has only very often one layer of that kind. For these reasons, I quoted only this assembly which presents great possibilities as regards creation, as is showed below in the photography. Photo 1.8 (CG) Example of an « orange segment » item. Walnut and hornbeam woods. 25cm high, 28 cm diameter. 9 In order to sharpen your appetite, please find here a few simple examples of layered turning achievements. Apart of the ones which are in the different following chapters, you can find many other ones, more difficult to make, more beautiful, more … everything..
Details
-
File Typepdf
-
Upload Time-
-
Content LanguagesEnglish
-
Upload UserAnonymous/Not logged-in
-
File Pages228 Page
-
File Size-