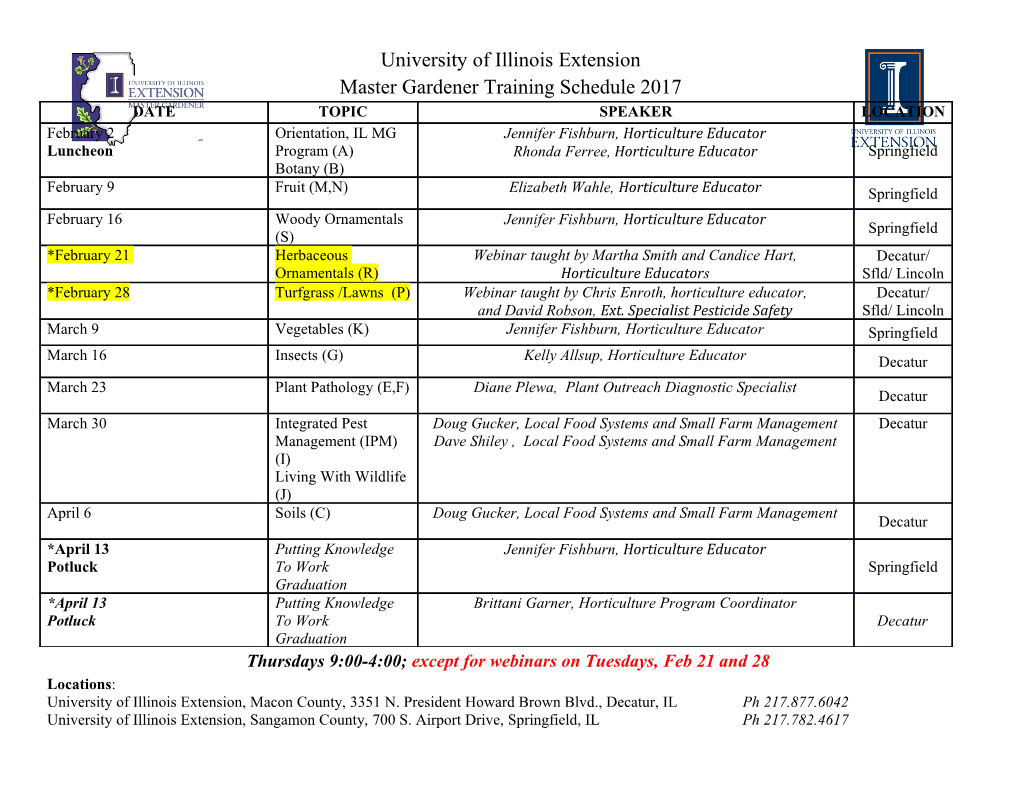
Chapter 5 Pollutant Range associated with Techniques that can be used to Comments the use of BAT reach these levels Dust 1 - 5 mg/Nm3 Fabric filter, wet EP. High performance fabric (A wet EP may be applicable to filters can achieve low gases from slag granulation or wet levels of heavy metals. gas quenching.) The concentration of heavy metals is linked to the concentration of dust and content of the metals in the dust. SO2 < 50 - 200 mg/Nm³ Wet alkaline scrubber. Alkali semi-dry scrubber and fabric filter 3 NOx < 100 mg/Nm Low NOx burner. Higher values are < 100 - 300 mg/Nm3 Oxy -fuel burner. associated with oxygen enrichment to reduce energy use. In these cases gas volume and mass emission is reduced. CO and metal Not emitted Wet scrubber To cool and clean the vapour gases of an ISF prior to use as a fuel. Total organic < 5 - 15 mg/Nm3 Afterburner. Pre-treatment of carbon as C < 5 - 50 mg/Nm3 Optimised combustion. secondary material to remove organic coatings if necessary. Dioxins < 0.1 - 0.5 ng High efficiency dust removal TEQ/Nm3 system (i.e. fabric filter), afterburner followed by quenching. Other techniques are available (e.g. adsorption on activated carbon, carbon/lime injection). Note. Collected emissions only. Associated emissions are given as daily averages based on continuous monitoring during the operating period. In cases where continuous monitoring is not practicable the value will be the average over the sampling period. For the abatement system used, the characteristics of the gas and dust will be taken into account in the design of the system and the correct operating temperature used. For SO2 or total carbon removal, the variation in raw gas concentration during batch processes may affect the performance of the abatement system. Table 2.1: Emissions to air from materials pre-treatment, secondary smelting, thermal refining, melting, slag fuming and Waelz kiln operation The metal content of the dust varies widely between processes. In addition for similar furnaces there are significant variations due to the use of varying raw materials. It is therefore not accurate to detail specific achievable concentrations for all metals emitted to air in this document. Some metals have toxic comp ounds that may be emitted from the processes and so need to be reduced to meet specific local, regional or long-range air quality standards. It is considered that low concentrations of heavy metals are associated with the use of high performance, modern abatement systems such as a membrane fabric filter provided the operating temperature is correct and the characteristics of the gas and dust are taken into account in the design. The issue is site specific but the following table gives some indication of the effects on the content of metals in dust that will be encountered locally. Component Zinc FB Zinc ISF process Lead direct Secondary Lead Roaster refining smelting lead refining processes processes Pb% 0.2 – 2 0.15 – 0.86 10 – 15 30 – 50 20 - 55 14 – 83 Zn% 50 – 60 52 – 76 20 – 50 3 – 5 0.01 - 10 3 – 28 Sb% n.a n.a n.a – 0.1 - 40 n.a Cd% 0.2 0.02 – 0.7 0.5 3 – 5 0.01 – 10 n.a 400 Chapter 5 As% 0.004 0.01 - 0.1 n.a 5 - 10 0.01 - 3 n.a n.a - Means not available Table 2.2: Metal content of some dusts from various lead and zinc production processes [tm 25, DFIU 1996] 1.1.3 Wastewater This is a site-specific issue, existing treatment systems are reported to be to a high standard. The use of sulphide precipitation or combined hydroxide/sulphide precipitation is particularly relevant to metals in this section [tm 171, Steil/Hahre 1999]. All wastewater will be treated to remove metals, solids and oils/tars. Absorbed acid gases (e.g. sulphur dioxide, HCl) and should be reused or neutralised if necessary. The techniques listed in section 2.9 are the techniques to consider. In a number of installations cooling water and treated wastewater including rainwater is reused or recycled within the processes. For primary and secondary production of the metals in this group, the total emissions to water are based on: · The slag treatment or granulating system. · The waste gas treatment system. · The leaching and chemical purification system. · The electro-winning process. · The wastewater treatment system: · Surface drainage. The following table gives associated emissions to water after effluent treatment. The data given may not be transposable to all installations. Main components [mg/l] Pb As Hg Cd Zn Process water <0.1 <0.05 <0.01 <0.05 <0.2 Note: The associated emissions to water are based on a qualified random sample or a 24-hour composite sample. The extent of wastewater treatment depends on the source and the metals contained in the wastewater. Table 2.3: Summary of associated emissions to water for some processes Process residues The use or recycling of slags, slimes and filter dusts is considered to be part of the processes. The iron precipitation method used (Goethite or Jarosite) depends on local conditions and the composition of the concentrate. The effective washing and precipitation of the leachable metals as sulphides before disposal should be considered. The solubility of the residue should be monitored using a standard leachate test. Disposal should meet the requirements set out in the directive on landfill. The production processes in this sector have been developed by the industry to maximise the re-use of the majority of process residues from the production units or to produce residues in form that enables them to be used in other non-ferrous metal production processes. An overview of the potential end uses for residues is given earlier in this chapter and some specimen quantities are also given for specific installations. The quantity of residues produced is strongly dependent on the raw materials in particular the iron content of primary materials, the content of other non-ferrous metals in primary and secondary materials and the presence of other contaminants such as organic materials. The emissions to land are therefore very site and material specific and depend on the factors discussed earlier. It is therefore not possible to produce a realistic, typical table of quantities that are associated with the use of BAT without detailing the raw material specification. The principles of BAT include waste prevention and minimisation and the 401 Chapter 5 re-use of residues whenever practical. The production of arsine and stibine from the action of water or water vapour on some residues should be taken into account. The industry is particularly effective in these practices the use and treatment options for some residues from the production of lead and zinc is given in tables 5.29 to 5.30. Costs associated with the techniques Cost data has been compiled for a variety of process variations and abatement systems. The cost data is very site specific and depends on a number of factors but the ranges given may enable some comparisons to be made. The data is provided in an appendix to this note so that costs for processes and abatement systems over the whole of the non-ferrous metal industry can be compared. 402 Chapter 5 Emerging Technologies · Zinc concentrates from some newer mines and from proposed developments, provide both opportunities and challenges to the conventional smelters. These fine ground concentrates are often characterised by low iron, elevated silica, high manganese and levels of elements such as germanium, which may cause concern. New processing technology needed to cope with these changes includes: - de-watering and materials handling of ultra-fine concentrate, novel transport systems, siliceous leach circuits, manganese removal cells and front-end smelting [tm 101, NL Zn 1998]. These concentrates are not be available to all producers and the new technology required to treat them may produce other residues that are difficult to deal with. · Environmental regulations for the disposal of the solid residues can form an incentive to change to the treatment of the iron residue by chemical fixation of the iron residue in the form of a cement (e.g. Jarofix) or other material such as the reaction of Goethite with iron slags (Gravelite). Both processes increase the amount of material produced and will only be effective if the materials are acceptable for civil engineering uses. · Leaching processes based on chloride for zinc and lead recovery are reported as being at the demonstration stage [tm 206, TGI 1999]. · The thermal treatment of jarosite and goethite has been demonstrated using the Ausmelt and Outokumpu processes [tm 41, Ausmelt 1997; tm 101, NL Zn 1998]. Zinc and other volatile metals are fumed off and recovered, the slag produced could be suitable for construction processes. The processes have not been shown to be economically viable as a general residue treatment method. · The processing of Jarosite and sewage sludge in an autoclave at 260 °C has been reported [tm 214, Vaartjes 1999]. Limited data is available and viability is not reported. The cellulose in the sewage sludge is the source of energy and the product is a molten material. Zinc, lead and silver are reported to be concentrated and sold and the stony product used for construction. · The smelting of Jarosite and Goethite has also been demonstrated, but has not been proven to be economic. · The injection of fine material via the tuyeres of a blast furnace has been successfully used and reduces the handling of dusty material and the energy involved in returning the fines to a sinter plant. · Control parameters such as temperature are used for melting furnaces and kettles and reduce the amount of zinc and lead that can be fumed from a process.
Details
-
File Typepdf
-
Upload Time-
-
Content LanguagesEnglish
-
Upload UserAnonymous/Not logged-in
-
File Pages339 Page
-
File Size-