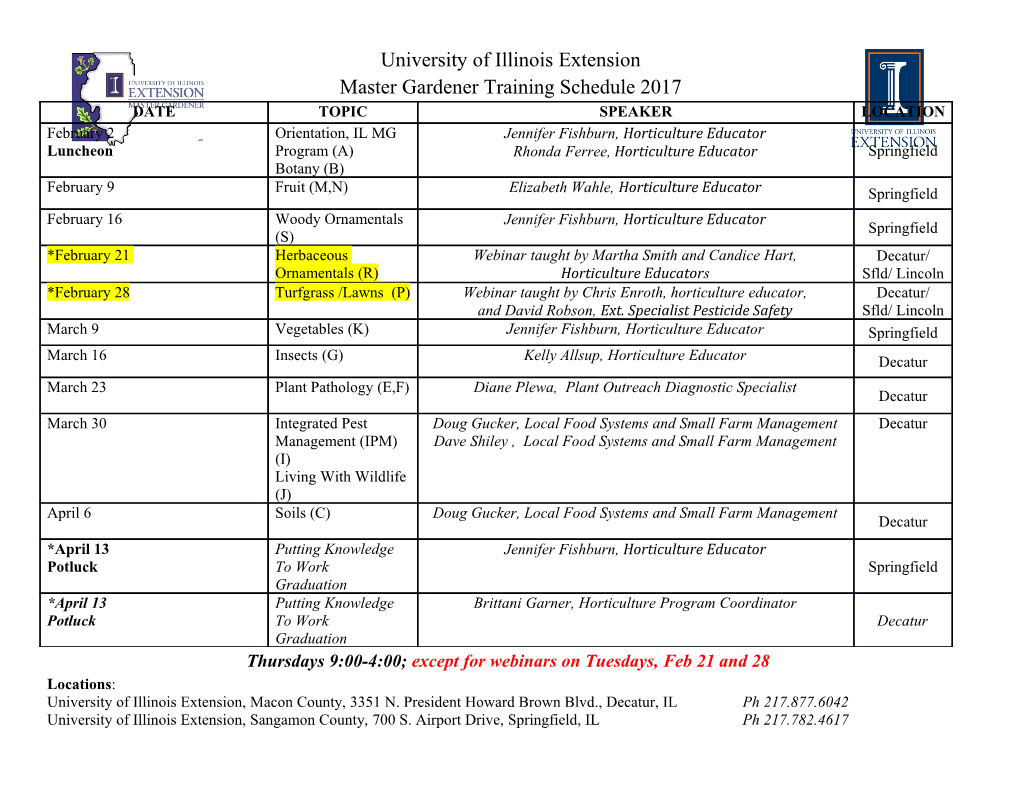
Journal of Manufacturing and Materials Processing Article Development of a Novel Tuning Approach of the Notch Filter of the Servo Feed Drive System Chung-Ching Liu 1,* , Meng-Shiun Tsai 2, Mao-Qi Hong 2 and Pu-Yang Tang 1 1 Department of Mechanical Engineering, National Chung Cheng University, Chiayi 62102, Taiwan; [email protected] 2 Department of Mechanical Engineering, National Taiwan University, Taipei 10617, Taiwan; [email protected] (M.-S.T.); [email protected] (M.-Q.H.) * Correspondence: [email protected] Received: 23 January 2020; Accepted: 2 March 2020; Published: 5 March 2020 Abstract: To alleviate the vibration effect of the feed drive system, a traditional approach is to apply notch filters to suppress vibrations in the velocity loop. The current approach is to adjust the notch filter parameters such as the center frequency, damping and depth based on observing the frequency response diagram of servo velocity closed loop. In addition, the notch filters are generally provided in the velocity loop control for the commercialized controllers such as FANUC, Siemens, etc. However, the resonance of the transmission system also appears in the position loop when the linear scale is used as the position feedback. The notch filter design without consideration of the resonance behavior of the position loop might cause degradation of performance. To overcome this problem, the paper proposes an innovative method which could automatically determine the optimal parameters of the notch filter under the consideration of resonance behavior of position loop. With the optimal parameters, it is found that both the gains of position and velocity loop controller could be increased such that the bandwidths of the position/velocity loops are higher. Based on the simulation results, the rising time is improved by 33% and the time for reaching the steady state is improved by 72% as comparing the cases of using the optimal approach and traditional approach. Keywords: notch filter; auto-tuning; feed drive system 1. Introduction High-speed machine tools are widely used in manufacturing the parts for aviation, automotive, mold, and other industrial fields. The design objectives of machine tools are to obtain high efficiency, high precision and high surface quality. However, vibrations of machine structure may be excited when the machine is under high speed and acceleration condition, and the surface quality would also be affected. To avoid the vibration effects, many factors should be considered. One of the most critical factors is how to adjust the servo control parameters. The vibrations could deteriorate the manufacturing qualities and performances [1–3]. To suppress the structural vibration of the feed drive system, many scholars have proposed different approaches. For example, motion commands are filtered before entering the servo controller [4–6]. Some scholars have also proposed strategies that adopted active damping of structural vibrations inside the control loop [7–9]. In the modern time, there are many various ways to control vibration behavior, such as neural networks [10,11], fuzzy control [12,13], and sliding mode control [14,15]. These methods can achieve higher control bandwidth by applying notch filters in the control loop. However, the design of such controllers could be difficult because higher-order plant models need to be considered in order to include the vibration modes into the dynamic model. For commercialized controllers, the control loops are designed by three main loops: current, velocity and position loops. J. Manuf. Mater. Process. 2020, 4, 21; doi:10.3390/jmmp4010021 www.mdpi.com/journal/jmmp J. Manuf. Mater. Process. 2020, 4, x FOR PEER REVIEW 2 of 11 commercialized controllers, the control loops are designed by three main loops: current, velocity and J. Manuf. Mater. Process. 2020, 4, 21 2 of 11 position loops. The commercial controllers generally apply the notch filters in velocity loop to alleviate the vibration signal near the resonance frequency [16] such that the bandwidth of the control Theloop commercial could be increased. controllers However, generally the apply traditional the notch method filters of in adjusting velocity loopthe notch to alleviate filter only the vibrationconsiders signalthe resonance near the resonancebehavior frequencyof the velocity [16] such loop. that The the resonance bandwidth behaviors of the control of the loop components could be increased. located However,outside the the velocity traditional loop methodhave not of been adjusting considered. the notch The filterresearch only of considers how to design the resonance the notch behavior filter by ofconsidering the velocity both loop. the Thevelocity resonance and position behaviors loop of dynamics the components is still an located open issue. outside In this the paper, velocity a novel loop haveapproach not been which considered. could determine The research the optimal of how parameters to design the of notchthe notch filter filter by considering is proposed. both In thethe velocityapproach, and the position vibration loop effects dynamics in velocity is still anand open position issue. loops In this are paper, considered a novel, approachand the parameters which could of determinenotch filters the could optimal automatically parameters ofbe the adjusted. notch filter The is paper proposed. is arranged In the approach, as follows. the In vibration Section e2,ffects the indynamics velocity andof the position feed system loops areand considered, the traditional and theapproach parameters are introduced. of notch filters Then, could the automaticallynovel optimal beapproach adjusted. is proposed The paper in isSection arranged 3. The as Bode follows. plots In velocity Section and2, the position dynamics loop of of the using feed traditional system and and theoptimal traditional approaches approach are arecompared introduced. in Section Then, 4. the The novel servo optimal performances approach using is proposed the traditional in Section and3. Theoptimal Bode approaches plots velocity for and the position step input loop and of usingthe trajectory traditional are and compared. optimal approaches Finally, Section are compared 5 gives the in Sectionconclusion.4. The servo performances using the traditional and optimal approaches for the step input and the trajectory are compared. Finally, Section5 gives the conclusion. 2. The Dynamic Model of the Feed Drive System 2. The Dynamic Model of the Feed Drive System In this section, the dynamic model of the feed drive system is first derived. Then, the dynamic modelIn thisis simplified section, theto explain dynamic the model parameter of the tuning feed drive process. system is first derived. Then, the dynamic model is simplified to explain the parameter tuning process. 2.1. The Derivation of the Feed Drive System 2.1. The Derivation of the Feed Drive System To describe the dynamic behavior of feed drive system, this paper utilizes the model proposed by theTo paper describe [4]. the The dynamic model includes behavior the of feeddynamics drive effects system, of this couplings, paper utilizes ball-screws, the model structure proposed base, byand the servo paper loop [4]. controls. The model The includes schematic the diagram dynamics of eaff feedects ofdrive couplings, system ball-screws,is shown in structureFigure 1a. base, The androtary servo motion loop controls.of the motor The drives schematic the platform diagram ofthrough a feed drivethe coupling system isand shown the ball in Figure-screw.1a. The The rotation rotary motionof the motor of the motorcan be drives measured the platform by the throughencoder themounted coupling on andthe themotor. ball-screw. The linear The rotationmotion of thethe motorplatform can can be measuredbe measured by theby encoderthe optical mounted linear scale on the on motor. the platform. The linear The motion feed drive of the system platform can can be besimplified measured as bya mass the optical-damper linear-spring scale (MCK) on the system platform. as shown The feed in Figure drive system1b. can be simplified as a mass-damper-spring (MCK) system as shown in Figure1b. (a) (b) FigureFigure 1.1. TheThe feedfeed drive drive system. system. ( a()a) The The schematic schematic of of the the feed feed drive drive system. system. (b )(b The) The 2 DOF 2 DOF diagram diagram of theof the feed feed drive drive system. system. InIn Figure1 1,, thethe parameters parameters could could be be defined defined as as the the following. following. isX thet is displacement the displacement of the of table, the table, is theXl isdisplacement the displacement of the ofball the-screw ball-screw,, and and is theXb displacementis the displacement of the base. of the base. and θl and are θthem are the ball-screw and motor rotation angle. Jl and Jm are the inertia of the ball-screw and motor. J.J. Manuf. Manuf. Mater. Mater. Process. Process. 20202020, ,44, ,x 21 FOR PEER REVIEW 33 of of 11 11 ball-screw and motor rotation angle. and are the inertia of the ball-screw and motor. and Mt arande theM bmassare theof table mass and of tablebase. and , base. andC t, C arel and theC dampingb are the of damping guideway, of guideway, ball-screw ball-screwand base, respectively.and base, respectively. , andK b, Kareg and the Kstiffnesst are the of sti base,ffness coupling of base, stiffness coupling and sti longitudinalffness and longitudinal stiffness of ballstiff-nessscrew, of respectively. ball-screw, respectively. The rotary Themotion rotary of motionthe ball of-screw, the ball-screw, , is transmittedθl, is transmitted to the linear to the displacement,linear displacement, , throughXl, through the converting the converting ratio, ratio, . Risl. givenRl is given as / as2 P , /where2π, where is Ptheis pitch the pitch of the of ballthe- ball-screw.screw. AfterAfter the the integration integration of of the the feed feed drive drive syste systemm and and servo servo loop loop control control system, system, the the complete complete system system cancan be be expressed expressed as asthe the block block diagram diagram shown shown in Figure in Figure 2 and2 isand named is named as the asservo the feed servo drive feed system drive.
Details
-
File Typepdf
-
Upload Time-
-
Content LanguagesEnglish
-
Upload UserAnonymous/Not logged-in
-
File Pages11 Page
-
File Size-