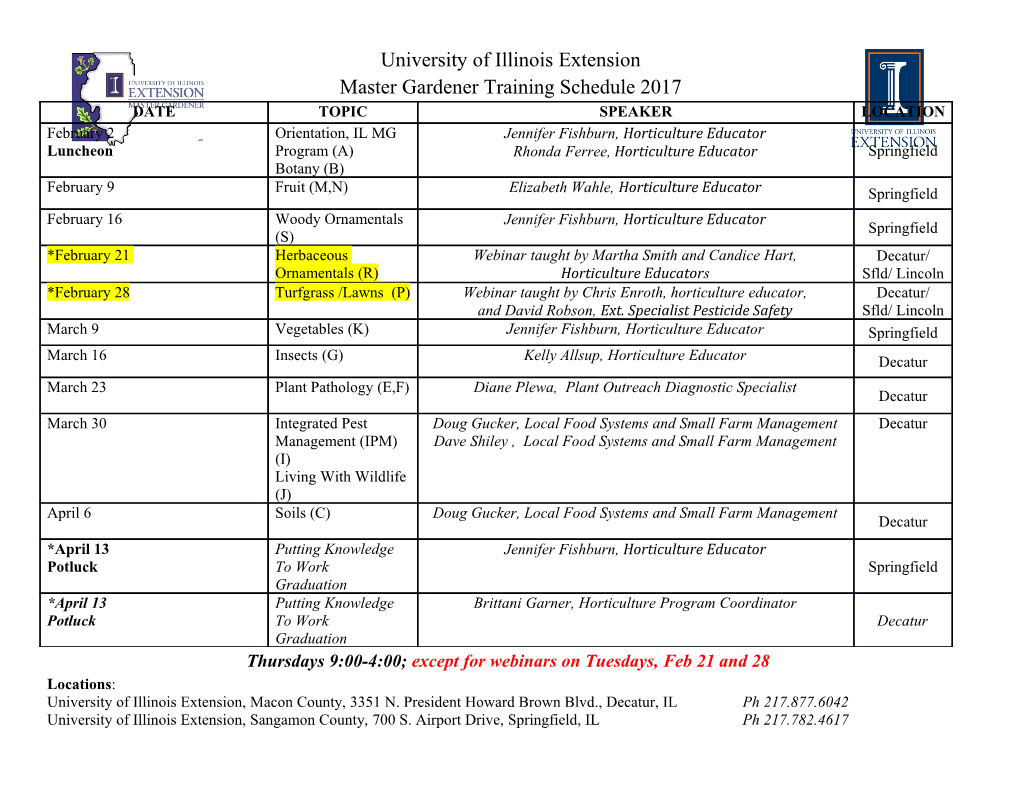
Oct 7, 1941-‘ J. ROBERTSON Ei- AL 2,257,978 EXTRACTION OF VANADIUM VALiIES FV‘ROM VANADIUM-BEARING MATERIAL Filed Feb. 25, 1940 s She'ets-Sheét 2. EFF EC 7" 01- 7'EMPERA TU/i’t' OF ?'oAsr HEADS- 20 MESH DRY Gnau/vo H0146? 90 Mm ‘ . CALC/NES QUE/VCHED 11v WATER SEC‘IONDARY Gm/vn / . a0. - " , ' . _ ' ‘ légTor/u. DI-SSOLVED 10 I 1000 1100 1200 1300 1400 1500 1600 1700 1000 IQVENTOR ?’oAsr TEMPERATUREjDEG'REES E Jahn ?abertqan ArcizibaZdAlexandenSjvrauZ?olberi'farl Dunn = _' ?rmmw?m Patented Oct. 7, 1941 22,257,978 UNITED STATES PATENT o-FFiicE EXTRACTION OF VANADIUM VALUES FROM VANADIUM-BEARING MATERIAL . John Robertson, Ricran, Peru,_'Holber't Earl Dunn, Grafton, Pa., and Archibald Alexander ‘Sproul, Rye, N. Y., assignors to Vanadium‘ Corporation of America, Bridgevill e, Pa., a corporation of Delaware Application February .23, 1940, Serial‘No. 320,458 16 Claims. (01.23-18) This invention relates to a process for recover adding transposing agents, provided that the ing vanadium values from ores and other vana roast is carried out at the proper temperature dium-bearing materials. The term vanadium and 'using the proper temperature-time cycle values is used as a. generic expression to include both for the heating and cooling operation. In the vanadium recovered whether as vanadium or respect to ‘the latter, a further, condition is that as a. compound existing in the ore or as a com the roasted ore must be cooled at a su?liciently pound synthesized from the ore. rapid rate, in order not to permit the soluble cal This application is a continuation-in-part of cium vanadate formed during the roasting to be our co-pending application, Serial No. 221,610, converted to any appreciable extent into apwater ?led July 2'7, 1938,'which application is a contin insoluble form. We have found that different uation-in-part .of our application, Serial No. vanadium ores behave diiferently in these roast’ 87,784, ?led June 27, 1936. ing and cooling operations and that ‘there exists The present invention provides a process for not only an optimumtemperature ‘and time cycle . recovering vanadium, values from ores or other during the heating or roasting stage but also a vanadium-bearing materials which is less costly critical cooling rate in the ?nal cooling stage, and in which the recovery is more nearly com which critical cooling 'rate must be exceeded, in plete than in the methods heretofore employed. order to prevent retransformation of the soluble It eliminates the use of ?uxing or transposing vanadate to an insoluble vanadate. agents during the roast-and the roast is so car We have found that when an ore containing ried out that a large proportion'of the vanadium - compounds of vanadium and calcium is roasted content is rendered water soluble, thus ‘enabling at different temperatures, a series of calcium the use of ‘a water quench in place of an acid or vanadates are formed, some of which are water alkaline leach. The water quench is, however, insoluble'and others of which are water soluble. followed by an acid leach to extract further por Thus, at a roasting temperature between about tions of vanadium. 1000° F. and l200° F. the water insoluble calcium In the accompanying drawings: ortho-vanadate is formed. Therefore, if such Fig. 1 is a ?ow sheet illustrating the preferred roasting temperatures are employed, it is neces manner of carrying out the process; sary to ‘employ a transposihg agent such as so Fig. 2 is a chart illustrating the solubility se-V dium chloride, sodium-sulphate or sodium car-" cured by quenching at the roasting temperature; bonate'in the roast, in order to Tender the'roast and water soluble. ' Fig. 3 is arsimilar chart illustrating the solu 'It is well -recogni'ze'd'by those skilled in the bilities when the ore is allowed to ?rst cool in art of “extracting metals from ores that within air before quenching. a given type the Iche‘micalcomposition, particu The most common method of recovering vana 35 larly with respect to major vconstituents (the dium value from its ores consists essentially of metals that it is desired to extract) may be roasting the ore with a suitable fluxing or trans substantially uniform from lot to lot. Yet the‘ posing agent or agents which convert the vana minor constituents (principally gangue mate dium content into soluble form. Such transpos rials) may vary widely without appearing. to al ing agents may be salt or soda ash, or both, ‘or ter the general characteristics of the ore; never other suitable material. The roasted ore is there thele‘ss, there is often apparent failure of a par after leached with water. The vanadium-bear ticular procedure to extract theabove mentioned ing liquor is ?ltered off and the vanadium con major constituentsuntil.some disturbingv feature tent is precipitated from this liquor by the addi-~ which may be a differenceprincipally of physical tion of the required amount of sulphuric acid. character has been vbrought ‘under control. In The cost of the transposing agent addedto the line with this generally accepted phenomena, we roast constitutes a large item of expense which is have found in studying vanadium ores that in the eliminated in our process. Furthermore, in our formation during roasting of the maximum process the amount of acid required is consider amount of soluble calcium vanadate the optimum ably reduced. temperature-time cycle varies somewhat with the We have found that normally water insoluble particular type‘of ore and the particular lot v‘of vanadium compounds in ores or other material any type being treated. There is, therefore, a which contain vanadium and compounds of cal necessary range ofgoperating conditions required cium or other alkaline earthmetals may be to satisfactorily ‘carry out our process with the rendered water soluble Without the necessity of '55 various ores to which it is applicable, in order to 2,257,978 . ._ .. _ _ , 2. - - . secure maximum extraction. In every case, how tals are believed to be calcium deuterotetra ever, the treatment involved is a roasting to con vanadate. vert vanadium present in the ore into soluble cal— If the roast is carried out at too low a tem cium or alkaline earth metal vanadate and then perature, or at too high a temperature, and is by cooling more quickly than the afore-mentioned immediately quenched in water, the water solu critical rate to effectively preserve the water sol ble calcium vanadate is not formed. If a roast uble vanadate and prevent its transformation ing temperature above 2000° F. is employed on into the insoluble calcium vanadate stable at the ore previously described, and the roasted room temperature that would result from slow ore is then immediately quenched in water and cooling. The soluble calcium vanadate is there 10 the quench liquor is concentrated so as to form after extracted with water and any remaining va crystals, we obtain green crystals which analyze: nadium is extracted by acid leaching, thus re Percent sulting as heretofore noted in a considerable V205 _________________________________ __ 59.30 saving in acid consumption, Water cooling ap CaO _________________________________ __ 17.69 pears to be more rapid for all ores than this 15 H2O (Loss on ignition) ________________ __ 23.35 critical cooling rate and hence two operations may be combined by quenching in water as here which correspond to the formula after described. 7 The initial stage of the roasting operation pref erably is carried out at some temperature above 20 CaVzOaAI-IzO 12000 F. This temperature is generally between and are practically insoluble in water, requiring 1400° F. and 1800° F., preferably about 1600° F., 35% or stronger sulphuric acid to dissolve them. but may go up as high as 20000 F. or‘ even higher, Upon reroasting the crystals at 1600° F. and if the maximum temperature and time cycle are quenching, they readily dissolve in water. not su?icient to cause appreciable sintering of 2.3 The process according to the present inven the material. Subsequent to the initial heating, the temperature may be lowered slowly or rapidly tion, may be carried out as follows: The ore crushed or comminuted to the desired ?neness, to some temperature not below about 1000” F. say 20 mesh, is roasted in a suitable furnace at before the rapid cooling at a rate greater than the the desired temperature, usually between about above noted critical cooling rate needs to be car 30 ried out. The temperature-time cycle produc 1400° F. and 1700" F., depending upon the type of ore or other material which is being treated.’ tive of maximum water extraction or maximum The roasted ore while being maintained at or total extraction by leaching in water and sub sequent leaching in acid will vary with different near the temperature of the roast is quenched ores and the process envisages the adjustment 3:3 in water. The quenched ore is then ground to of this temperature-time cycle in accordance with the desired degree of ?neness with the water. The ground material is ?ltered yielding a ?ltrate the needs of each case. containing a large proportion of the vanadium As an example, a characteristic ore treated in accordance with the present invention had the originally contained in the ore, hereafter called following composition: 40 “quench liquor,” and a residue hereafter called Percent “quench residue.” A leach of the quench resi due is then made with a dilute sulphuric acid V ____________________________________ __ 3.54 solution, say a 4% solution, and the leached ma CaO _________________________________ __ 15.53 terial is ?ltered yielding a ?ltrate hereafter S03 __________________________________ __ 25.91 - called “acid liquor” containing an additional A1203 ________________________________ __ 11.18 proportion of the vanadium contained in the SiOz _________________________________ __ 24.44 ore, and a ?nal residue or tailing.
Details
-
File Typepdf
-
Upload Time-
-
Content LanguagesEnglish
-
Upload UserAnonymous/Not logged-in
-
File Pages10 Page
-
File Size-